Using ground penetrating radar to determine reason for serious pavement settling in Kentucky-Tennessee tunnel
Just a few years after the opening of the Cumberland Gap Tunnel, highway officials noticed moderate to severe settling of the continuously reinforced concrete pavement. The mountain tunnel provides an important link between Kentucky and Tennessee along US25E and the problem looked serious, with many voids discovered beneath the pavement surface.
To investigate the problems, the Kentucky Transpor
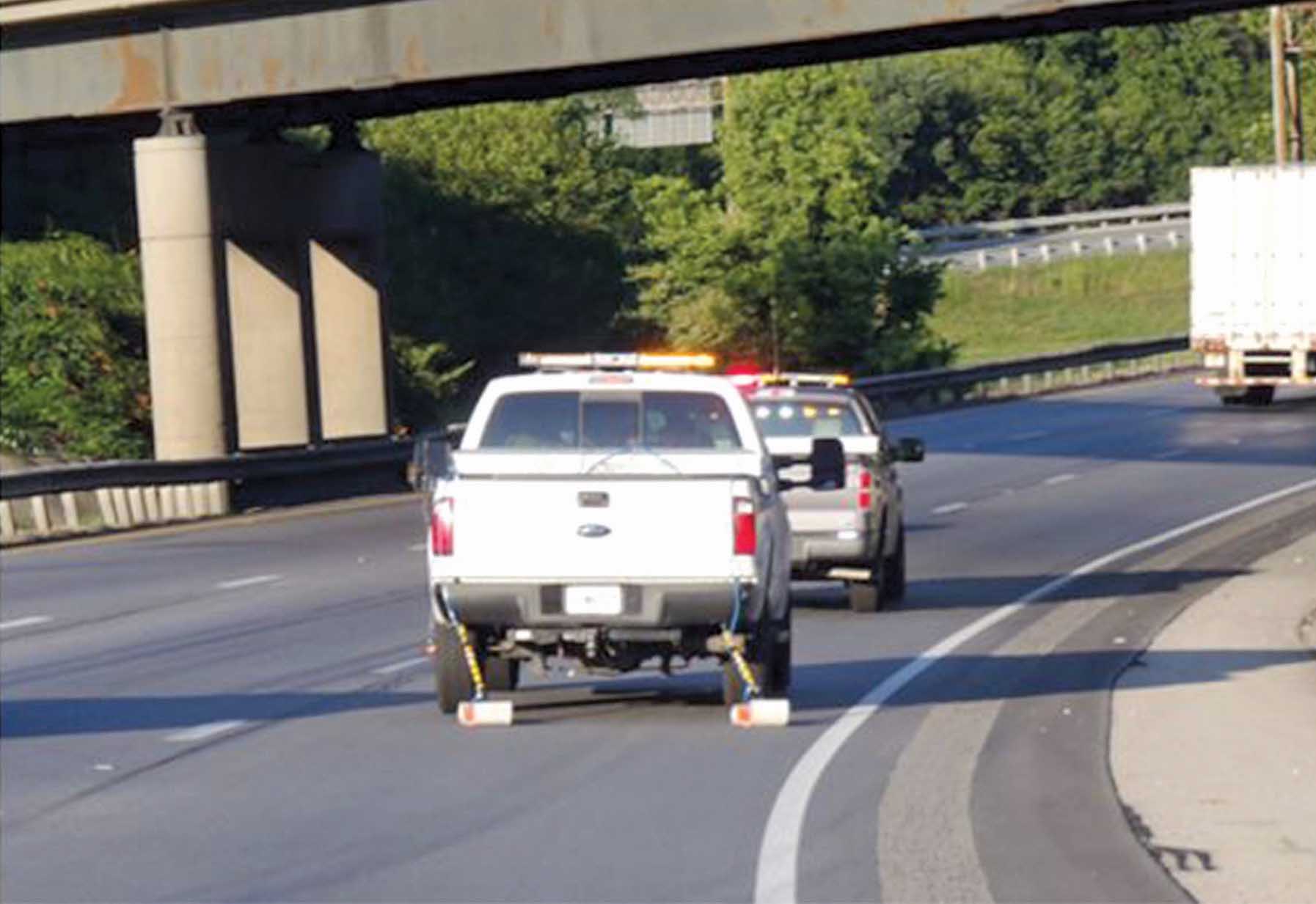
GPR equipment was towed behind a vehicle for fast analysis
Using ground penetrating radar to determine reason for serious pavement settling in Kentucky-Tennessee tunnel
Just a few years after the opening of the Cumberland Gap Tunnel, highway officials noticed moderate to severe settling of the continuously reinforced concrete pavement. The mountain tunnel provides an important link between Kentucky and Tennessee along US25E and the problem looked serious, with many voids discovered beneath the pavement surface.
To investigate the problems, the Kentucky Transportation Centre (KTC) brought in a research team to establish the cause of the settlement issues, using ground penetrating radar (GPR) and hydro-geochemical water testing (HGWT). The use of the GPR equipment, manufactured by Geophysical Survey Systems, Inc. (8095 GSSI), provided information that slashed the costs for the tunnel repair project by showing precisely where repairs were necessary. The equipment now forms an integral part of the long-term inspection process that will assist in finding other distressed areas within the tunnel should they arise in the future.
The Cumberland Gap Tunnel is a twin-bore mountain tunnel in the Appalachian Mountains, which goes through the Cumberland Gap. Constructed in 1996 at a cost of US$260 million, the tunnel is located within the Cumberland Gap National Historic Park on the Kentucky-Tennessee state line. An existing narrow, winding and somewhat hazardous two-lane road goes up and over the mountain, and the state decided to build the four-lane tunnel through the park and the mountain to improve traffic safety without interfering with the scenery.
Located about around 305m below the pinnacle, the tunnel carries about 22,500 vehicles/day. About 10% of the traffic is for heavy vehicles, predominately transporting coal from mines in Kentucky to fuel a Tennessee power plant.
Not more than four years after the tunnel opened, highway officials noticed a settlement area and an odd dipping of pavement. The steel-reinforced concrete pavement had settled in various areas of both the north and southbound tunnels. And 10 years after the tunnel’s completion, approximately 687.5m2 of pavement surface had voids beneath it that ranged from 12mm-1m deep. Only the steel reinforcement was keeping the pavement from collapsing.
The state made several attempts to shore up the settled pavement areas before starting investigative repair in 2007 that attempted to tackle the most severely damaged section and get to the root of the causes of the settlement issues.
The effort was led by a team from the5193 University of Kentucky, College of Engineering, Kentucky Transportation Centre. The facility is contracted to perform the Kentucky Transportation Cabinet’s investigative research tasks for highways, roads, bridges.
The research began with an analysis of the economic impact to tunnel users if the pavement was to fail and the link had to be closed. The study showed that if they could no longer transport coal through the tunnel and had to find an alternate route, there would be about a four hour diversion. User costs for that diversion, along with costs associated with delays for people living in Kentucky but commuting to work in Tennessee, amounted to about $1.1 million/day.
Based on the high level of economic impact, the state made the decision to find a permanent fix for the problem. But first it was necessary to locate the voids and determine why the concrete pavement had settled in various areas throughout the tunnel. In order to do this, the research team performed GPR surveys and HGWT.
The tunnel was constructed with a 1.22-1.52m layer of crushed limestone-based material placed beneath the concrete pavement. By design, between 19-45.5 million litres of groundwater flows beneath the tunnels on any given day through the layer of crushed limestone. The HGWT testing showed that the groundwater inflow in certain areas is aggressive to calcite, so the calcium-rich limestone backfill material placed beneath the concrete pavement was dissolving and leaving the tunnel through the groundwater collection system every day. Some of the groundwater entering the tunnel was runoff from coal seams; when water runs through coal it changes chemical properties, becoming more acidic.
The testing results indicated that approximately 0.59-1.18m3 of limestone sub-base material disappeared from the tunnel every month due to calcium-deficient ground-water beneath it. “That’s about a wheelbarrow and a half of material leaving the tunnel in solution, dissolving and washing out through drainage every day,” said *Brad Rister, senior research engineer with the Kentucky Transportation Centre. This led to about 6.5-14m2 square surface feet of new void area opening up beneath the concrete pavement/month.
The team then used GPR technology developed by Geophysical Survey Systems, Inc. (GSSI) to identify the location and size of the voids or cavities. The equipment, SIR-20 and SIR-3000 control units with a 900 MHz antenna and survey wheel, was used to scan from one end of the tunnel to the other on both tunnels. Each side of the tunnel takes about 4-5 hours to scan, or about 10 hours total.
The first void found was 1.22m deep and 9m long; some of the void areas span across both lanes (9m wide) and extend from 0.3-21m in length. “The concrete pavement was essentially performing as a bridge in these void locations,” said Rister. “Structural loading calculations indicate that a concrete slab if designed as a bridge would only be able to span 6” (1.82m) before starting to fail. The only reason the pavement structure did not completely collapse is because reinforcing steel is placed inside the concrete.”
According to Rister, the GPR equipment was able to delineate where the problems were and gave the team a way to continue to track the problem. They had originally started using the GPR technology in 2002 to conduct scans every 6 months to identify areas where new voids were appearing. Several costly but temporary fixes had been performed that involved digging a hole and backfilling it with concrete to support the structure. “GPR gave us a visual on where the problems were located,” said Rister. “It was such a large area that I don’t know what else we could have done to visually see where the problems where.”
The study determined that the best remediation strategy was to remove the existing limestone sub-base material and replace it with layers of crushed granite, separated by a geo-grid fabric, and a new 254mm reinforced concrete pavement. Granite is inert and has properties not affected by the low pH water.
Rister explained that the mountain through which the tunnel goes is a thrust fault – the bottom is limestone, then there is a layer of sandstone and then fieldstone. In Tennessee, the water runs through limestone, while the water coming in from Kentucky was running through fieldstone, so it didn’t have calcium elements. Groundwater with no calcium to neutralise the acid was what dissolved the limestone fill in the tunnel. “Being able to confirm the geologic formation gave us confidence that there were no voids that needed to be fixed on one end of the tunnel, significantly reducing repair costs.”
The initial proposal was to replace approximately 853m of pavement in each tunnel at an approximate cost of $10 million. The GPR and HGWT results, however, allowed crews to limit repairs to the isolated areas and save considerably. Completed in 2012, the project cost around $3 million. The project took 35 days, with work done 24 hours/day.
As part of the tunnel’s routine maintenance sequence, scans will be performed with the GPR every six months. The equipment is a key component of a long-term inspection process that will assist in finding other distressed areas within the tunnel if they arise in the future.
The project was selected for inclusion in the American Association of State Highway and Transportation Officials (AASHTO) 2012 High Value Research compendium, Research Impacts: Better - Cheaper - Faster. It was also featured in the1257 National Cooperative Highway Research Program (NCHRP) executive brochure Research Makes the Difference 2012.
According to Rister, whose group performs forensics work on failures of bridges, tunnels, and roads, GPR is an important tool available to obtain discernable information, providing an understanding of whether the problem is a sink hole or settling pavement, and if the cause is water trapped beneath a roadway. “Our success goes back to use of the GPR,” explained Rister. “Without it we wouldn’t have had the ability to image what’s going on beneath the surface.”
*Brad Rister is senior research engineer with the Kentucky Transportation Centre at the University of Kentucky. His current research involves using remote sensing technologies such as: Ground Penetrating Radar; LiDAR; infrared; and laser inspection to assist in identifying and solving transportation problems non-destructively.
Just a few years after the opening of the Cumberland Gap Tunnel, highway officials noticed moderate to severe settling of the continuously reinforced concrete pavement. The mountain tunnel provides an important link between Kentucky and Tennessee along US25E and the problem looked serious, with many voids discovered beneath the pavement surface.
To investigate the problems, the Kentucky Transportation Centre (KTC) brought in a research team to establish the cause of the settlement issues, using ground penetrating radar (GPR) and hydro-geochemical water testing (HGWT). The use of the GPR equipment, manufactured by Geophysical Survey Systems, Inc. (
The Cumberland Gap Tunnel is a twin-bore mountain tunnel in the Appalachian Mountains, which goes through the Cumberland Gap. Constructed in 1996 at a cost of US$260 million, the tunnel is located within the Cumberland Gap National Historic Park on the Kentucky-Tennessee state line. An existing narrow, winding and somewhat hazardous two-lane road goes up and over the mountain, and the state decided to build the four-lane tunnel through the park and the mountain to improve traffic safety without interfering with the scenery.
Located about around 305m below the pinnacle, the tunnel carries about 22,500 vehicles/day. About 10% of the traffic is for heavy vehicles, predominately transporting coal from mines in Kentucky to fuel a Tennessee power plant.
Not more than four years after the tunnel opened, highway officials noticed a settlement area and an odd dipping of pavement. The steel-reinforced concrete pavement had settled in various areas of both the north and southbound tunnels. And 10 years after the tunnel’s completion, approximately 687.5m2 of pavement surface had voids beneath it that ranged from 12mm-1m deep. Only the steel reinforcement was keeping the pavement from collapsing.
The state made several attempts to shore up the settled pavement areas before starting investigative repair in 2007 that attempted to tackle the most severely damaged section and get to the root of the causes of the settlement issues.
The effort was led by a team from the
The research began with an analysis of the economic impact to tunnel users if the pavement was to fail and the link had to be closed. The study showed that if they could no longer transport coal through the tunnel and had to find an alternate route, there would be about a four hour diversion. User costs for that diversion, along with costs associated with delays for people living in Kentucky but commuting to work in Tennessee, amounted to about $1.1 million/day.
Based on the high level of economic impact, the state made the decision to find a permanent fix for the problem. But first it was necessary to locate the voids and determine why the concrete pavement had settled in various areas throughout the tunnel. In order to do this, the research team performed GPR surveys and HGWT.
The tunnel was constructed with a 1.22-1.52m layer of crushed limestone-based material placed beneath the concrete pavement. By design, between 19-45.5 million litres of groundwater flows beneath the tunnels on any given day through the layer of crushed limestone. The HGWT testing showed that the groundwater inflow in certain areas is aggressive to calcite, so the calcium-rich limestone backfill material placed beneath the concrete pavement was dissolving and leaving the tunnel through the groundwater collection system every day. Some of the groundwater entering the tunnel was runoff from coal seams; when water runs through coal it changes chemical properties, becoming more acidic.
The testing results indicated that approximately 0.59-1.18m3 of limestone sub-base material disappeared from the tunnel every month due to calcium-deficient ground-water beneath it. “That’s about a wheelbarrow and a half of material leaving the tunnel in solution, dissolving and washing out through drainage every day,” said *Brad Rister, senior research engineer with the Kentucky Transportation Centre. This led to about 6.5-14m2 square surface feet of new void area opening up beneath the concrete pavement/month.
The team then used GPR technology developed by Geophysical Survey Systems, Inc. (GSSI) to identify the location and size of the voids or cavities. The equipment, SIR-20 and SIR-3000 control units with a 900 MHz antenna and survey wheel, was used to scan from one end of the tunnel to the other on both tunnels. Each side of the tunnel takes about 4-5 hours to scan, or about 10 hours total.
The first void found was 1.22m deep and 9m long; some of the void areas span across both lanes (9m wide) and extend from 0.3-21m in length. “The concrete pavement was essentially performing as a bridge in these void locations,” said Rister. “Structural loading calculations indicate that a concrete slab if designed as a bridge would only be able to span 6” (1.82m) before starting to fail. The only reason the pavement structure did not completely collapse is because reinforcing steel is placed inside the concrete.”
According to Rister, the GPR equipment was able to delineate where the problems were and gave the team a way to continue to track the problem. They had originally started using the GPR technology in 2002 to conduct scans every 6 months to identify areas where new voids were appearing. Several costly but temporary fixes had been performed that involved digging a hole and backfilling it with concrete to support the structure. “GPR gave us a visual on where the problems were located,” said Rister. “It was such a large area that I don’t know what else we could have done to visually see where the problems where.”
The study determined that the best remediation strategy was to remove the existing limestone sub-base material and replace it with layers of crushed granite, separated by a geo-grid fabric, and a new 254mm reinforced concrete pavement. Granite is inert and has properties not affected by the low pH water.
Rister explained that the mountain through which the tunnel goes is a thrust fault – the bottom is limestone, then there is a layer of sandstone and then fieldstone. In Tennessee, the water runs through limestone, while the water coming in from Kentucky was running through fieldstone, so it didn’t have calcium elements. Groundwater with no calcium to neutralise the acid was what dissolved the limestone fill in the tunnel. “Being able to confirm the geologic formation gave us confidence that there were no voids that needed to be fixed on one end of the tunnel, significantly reducing repair costs.”
The initial proposal was to replace approximately 853m of pavement in each tunnel at an approximate cost of $10 million. The GPR and HGWT results, however, allowed crews to limit repairs to the isolated areas and save considerably. Completed in 2012, the project cost around $3 million. The project took 35 days, with work done 24 hours/day.
As part of the tunnel’s routine maintenance sequence, scans will be performed with the GPR every six months. The equipment is a key component of a long-term inspection process that will assist in finding other distressed areas within the tunnel if they arise in the future.
The project was selected for inclusion in the American Association of State Highway and Transportation Officials (AASHTO) 2012 High Value Research compendium, Research Impacts: Better - Cheaper - Faster. It was also featured in the
According to Rister, whose group performs forensics work on failures of bridges, tunnels, and roads, GPR is an important tool available to obtain discernable information, providing an understanding of whether the problem is a sink hole or settling pavement, and if the cause is water trapped beneath a roadway. “Our success goes back to use of the GPR,” explained Rister. “Without it we wouldn’t have had the ability to image what’s going on beneath the surface.”
*Brad Rister is senior research engineer with the Kentucky Transportation Centre at the University of Kentucky. His current research involves using remote sensing technologies such as: Ground Penetrating Radar; LiDAR; infrared; and laser inspection to assist in identifying and solving transportation problems non-destructively.