Advances in bridge monitoring technology should help ensure structural safety Highly productive, Fugro Aperio's ground penetrating radar system offers accurate scanning of bridge condition Bridge engineers can now benefit from a new technology designed to pinpoint shallow targets, such as masonry fixings, reinforcement bars or delamination between thin layers. This uses the latest high resolution ground penetrating radar (GPR) antenna and has been developed by Cambridge-based Fugro Aperio in the UK. Operati
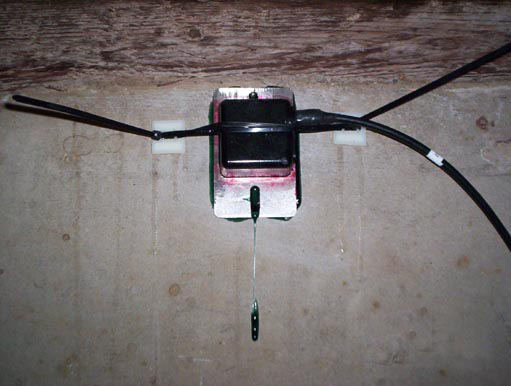
The Soundprint acoustic testing system is now being widely used to examine bridge cable integrity
RSS2929 Fugro Aperio in the UK.
Operating at a higher frequency than comparable instruments, 2,600MHz in comparison to the 1,500MHz range of most competing systems, the new system offers major gains in non-destructive testing technologies. This new system is able to pinpoint detail, such as multiple layers of reinforcement in walls and cracks in floors. According to Fugro Aperio, the technology offers powerful new capabilities in asset surveying for a range of highways applications, including assessment of post-tensioned bridges, bridge and tunnel decks, tunnel walls and pavements. As well as recording thickness to a depth of around 1m, the system can detect voids within and behind concrete, as well as delamination in concrete and asphalt. It also provides precise mapping of reinforcement and other embedded features, such as post-tensioning ducts and cables.
The package is highly portable as it is compact, rugged and is also suited for use where access would be difficult for conventional investigation methods. The system can be mounted on a trailer or vehicle to scan larger areas such as bridge decks, and for pavement evaluation and can survey 3-5 linear km of data/day. As well as concrete, this GPR capability is also effective on masonry, for the evaluation of brick arches, for instance, to determine thickness or to map ring separation and moisture.
Meanwhile Pure Technologies has developed the SoundPrint Technology, an acoustic monitoring system that is designed to detect the fracture of high-tensile steel wires such as those found in post-tensioned bridges and structures. The system uses surface-mounted acoustic sensors to detect the energy released by the fracture of a wire and locate the position of the break. The package is non-destructive, provides continuous monitoring to the structure and can make huge savings for bridge owners in unnecessary repairs and premature decommissioning.
When a high-tensile steel wire fractures, potential energy is released, causing the surrounding concrete to vibrate. This is detected by an array of piezoelectric sensors fitted to the structure and signals are then carried to a data acquisition system (DAQ) through a SoundPrint Smart Junction (SSJ) box. When signals reach the DAQ they are amplified and run through a series of filters and pre-processors, rejecting construction noise and traffic. Data passing through these primary filters is sent to a data processing centre through the Internet and software analyses the information to determine the time and location of a wire break. All this retrieved data can be viewed through a website.
The system can identify issues such as corrosion of steel tendons in post-tensioned bridges as this can cause them to fracture, compromising the strength and integrity of a structure. Conventional monitoring methods are time-consuming, expensive and may cause traffic delays. An alternative is the use of SoundPrint monitoring, which can be applied to structures where further deterioration can be tolerated.
Demand for the system has increased in the UK in recent years and, as authorised distributors of the system, the Transport Research Laboratory (777 TRL) is involved in the installation, commissioning and monitoring of the system on several structures. Recent installations include; Bowdon View Bridge on the M56 motorway at Junction 7 and the Thorley Lane Bridge on the M56 at Junction 5, near Manchester Airport.
RSS
Advances in bridge monitoring technology should help ensure structural safety
Bridge engineers can now benefit from a new technology designed to pinpoint shallow targets, such as masonry fixings, reinforcement bars or delamination between thin layers. This uses the latest high resolution ground penetrating radar (GPR) antenna and has been developed by Cambridge-basedOperating at a higher frequency than comparable instruments, 2,600MHz in comparison to the 1,500MHz range of most competing systems, the new system offers major gains in non-destructive testing technologies. This new system is able to pinpoint detail, such as multiple layers of reinforcement in walls and cracks in floors. According to Fugro Aperio, the technology offers powerful new capabilities in asset surveying for a range of highways applications, including assessment of post-tensioned bridges, bridge and tunnel decks, tunnel walls and pavements. As well as recording thickness to a depth of around 1m, the system can detect voids within and behind concrete, as well as delamination in concrete and asphalt. It also provides precise mapping of reinforcement and other embedded features, such as post-tensioning ducts and cables.
The package is highly portable as it is compact, rugged and is also suited for use where access would be difficult for conventional investigation methods. The system can be mounted on a trailer or vehicle to scan larger areas such as bridge decks, and for pavement evaluation and can survey 3-5 linear km of data/day. As well as concrete, this GPR capability is also effective on masonry, for the evaluation of brick arches, for instance, to determine thickness or to map ring separation and moisture.
Meanwhile Pure Technologies has developed the SoundPrint Technology, an acoustic monitoring system that is designed to detect the fracture of high-tensile steel wires such as those found in post-tensioned bridges and structures. The system uses surface-mounted acoustic sensors to detect the energy released by the fracture of a wire and locate the position of the break. The package is non-destructive, provides continuous monitoring to the structure and can make huge savings for bridge owners in unnecessary repairs and premature decommissioning.
When a high-tensile steel wire fractures, potential energy is released, causing the surrounding concrete to vibrate. This is detected by an array of piezoelectric sensors fitted to the structure and signals are then carried to a data acquisition system (DAQ) through a SoundPrint Smart Junction (SSJ) box. When signals reach the DAQ they are amplified and run through a series of filters and pre-processors, rejecting construction noise and traffic. Data passing through these primary filters is sent to a data processing centre through the Internet and software analyses the information to determine the time and location of a wire break. All this retrieved data can be viewed through a website.
The system can identify issues such as corrosion of steel tendons in post-tensioned bridges as this can cause them to fracture, compromising the strength and integrity of a structure. Conventional monitoring methods are time-consuming, expensive and may cause traffic delays. An alternative is the use of SoundPrint monitoring, which can be applied to structures where further deterioration can be tolerated.
Demand for the system has increased in the UK in recent years and, as authorised distributors of the system, the Transport Research Laboratory (
RSS