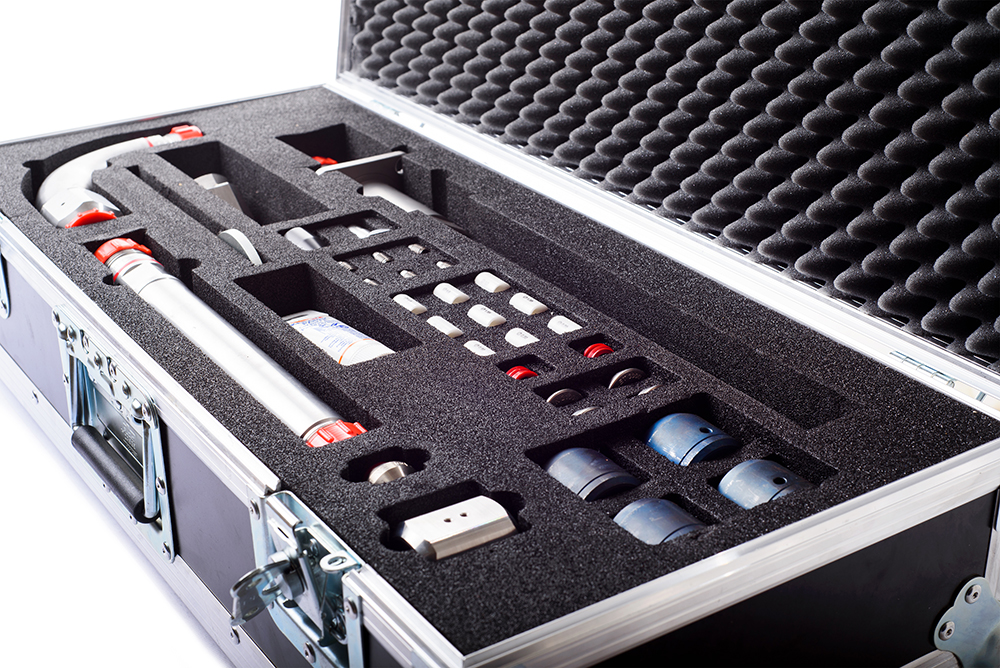
This latter feature means that contractors can now reduce the number of components on hand and reduce downtime previously needed to exchange parts.
The modular system can be assembled in a number of configurations for any application. Standardised ends allow components to attach in any direction. For example, if the nozzle needs to enter a narrow space it can be mounted in a 90° elbow.
It also features a variety of longevity and performance improvements. The Super Lance is now standard on Aqua Cutter robots and can be retrofitted to older models.
Aqua Cutter hydrodemolition robots use the Super Lance to direct high-pressure water at a surface, for removing deteriorated concrete or to remove concrete to a pre-determined depth without risk of microfracturing or damage to the underlying rebar.
The system also includes uniform threads and seals and multiple fittings for different hoses, making the attachment compatible with any aqua cutter on the market. The uniform threads also mean less need for adaptors, which can lead to a risk of leaks if used.
Aquajet improved performance in the Super Lance by manufacturing it with a 13mm bore-through hole and no change in diameter, helping water enter the nozzle without turbulence and not lose power. The Super Lance also includes several improvements. It is lined with ceramic, reducing wear on the lance as it protrudes through the protective rubber below the hydrodemolition robot’s hood. It is also thinner, meaning less wear on the rubber. Aquajet billet machined all pressure parts and added a longer lasting wear cap.
The Super Lance is equipped with Aquajet’s unique ceramic nozzle specifically designed for demanding hydrodemolition applications. The highly-efficient nozzles last 300-350 hours, depending on the water quality.
The Super Lance is available to be ordered as a kit containing the main system components for equipment retrofits.