The use of high-pressure water jets to remove old concrete on structures is becoming increasingly popular
Hydrodemolition of concrete structures by robotic equipment is becoming an increasingly used method for removing deteriorated concrete with high-pressure water techniques.
It offers the selective removal of deteriorated concrete, while retaining sound concrete below the intended level of removal, a process that will not damage rebar or cause micro-cracks in the concrete, as will mechanical methods s
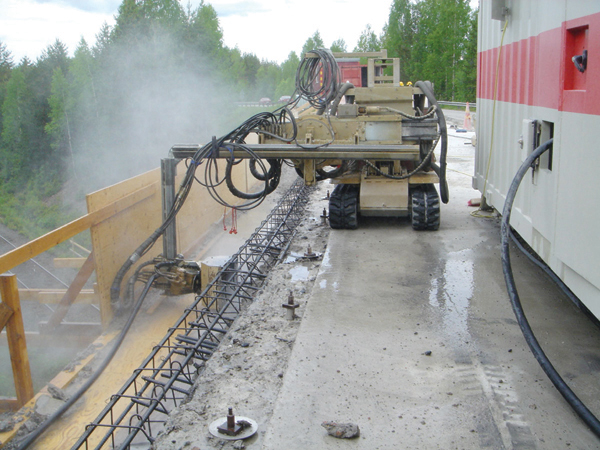
An Aquajet HVD6000 Aqua Cutter was used to prepare a section of the A22 in Vienna for new impact barriers
The use of high-pressure water jets to remove old concrete on structures is becoming increasingly popular
Hydrodemolition of concrete structures by robotic equipment is becoming an increasingly used method for removing deteriorated concrete with high-pressure water techniques.It offers the selective removal of deteriorated concrete, while retaining sound concrete below the intended level of removal, a process that will not damage rebar or cause micro-cracks in the concrete, as will mechanical methods such as jackhammers, says Swedish specialist
Over the years the hydrodemolition process and equipment has developed, and today the robotic units are capable of performing vertically, horizontally, and overhead as standard units. Attachments are available that allow removal from the underside of bridge decks, columns, and parapet beams to name a few.
Complete hydrodemolition units comprise a high-pressure pump, driving engine and control system housed in the acoustically-treated container and a hydrodemolition robot with a series of standard tools. Computerised control plays a key role in the performance quality and design of hydrodemolition equipment, allowing the machines to carry out repetitive tasks automatically.
The key element of hydrodemolition is to pressure and widen existing pores and micro-cracks in the weakened concrete structure using high-pressure water penetration. Material is removed as the build up pressure exceeds the tensile strength of the damaged or weakened concrete.
Claimed advantages to using hydrodemolition include a rough, irregular surface to provide an excellent bond for repair material; fracturing in the leftover concrete caused by mechanical removal methods are eliminated; lower strength and deteriorated concrete is selectively removed, and vibration to the surrounding structure is eliminated.
Examples of the use of hydrodemolition techniques on structures, particularly bridges, worldwide are many, and one such can be related by Austrian hydrodemolition specialist contractor Rohsler & Co. It used an Aqua Cutter HVD6000 from Swedish company Aquajet to remove more than 300m³ of concrete to expose rebar for installation of new impact barriers in the Austrian capital Vienna.
While work was being carried out to construct a 1.2km extension to the city's A22 road in a bid to solve traffic congestion, the highway authority as part of the project to upgrade the impact barriers along the existing 300m long elevated section of the A22, and hydrodemolition techniques were the specified preferred option to expose the bridge rebar.
Röhsler & Co was appointed main sub-contractor responsible for the work, opting to use its HVD6000 Aqua Cutter to cut an 80cm wide channel to a depth of 25cm to expose the rebar, removing all the concrete along the outer edge of the highway platform.
Using a high-pressure jet of water (the HVD6000 robot was coupled to a Woma pump supplying water at a pressure with 1,200 bar and a flow rate of 200 litres/min), the diesel-powered Aqua Cutter robot blasted the concrete without causing any damage to the structure or the reinforcement bars, and in a second adjacent cut, Röhsler & Co prepared a further channel
1m x 5cm to expose the top rebar without causing any damage. New rebar was then embedded into the 1m section and across to the new extended bridge edge, further reinforcing the exposed rebar.
A new 1.4-1.6m wide concrete platform was formed with a 20-30cm thickness and supported by temporary formwork scaffolding, while the new improved steel impact barrier meets with the latest EU regulations. An outer steel and fibreglass infill canopy provides an aesthetic finish and noise damping.