North of the Austrian capital Vienna, one of the region's biggest transport infrastructure projects for decades is currently under construction, the A5 Nordautobahn. This will give the Greater Vienna region its first-ever high-capacity link to the Czech motorway and arterial road network, greatly easing congestion on the old main road. In the first phase of construction, 22.7km of motorway are to be built. Work on the second section, all the way through to the Czech border, is to start in 2010. The A5 Norda
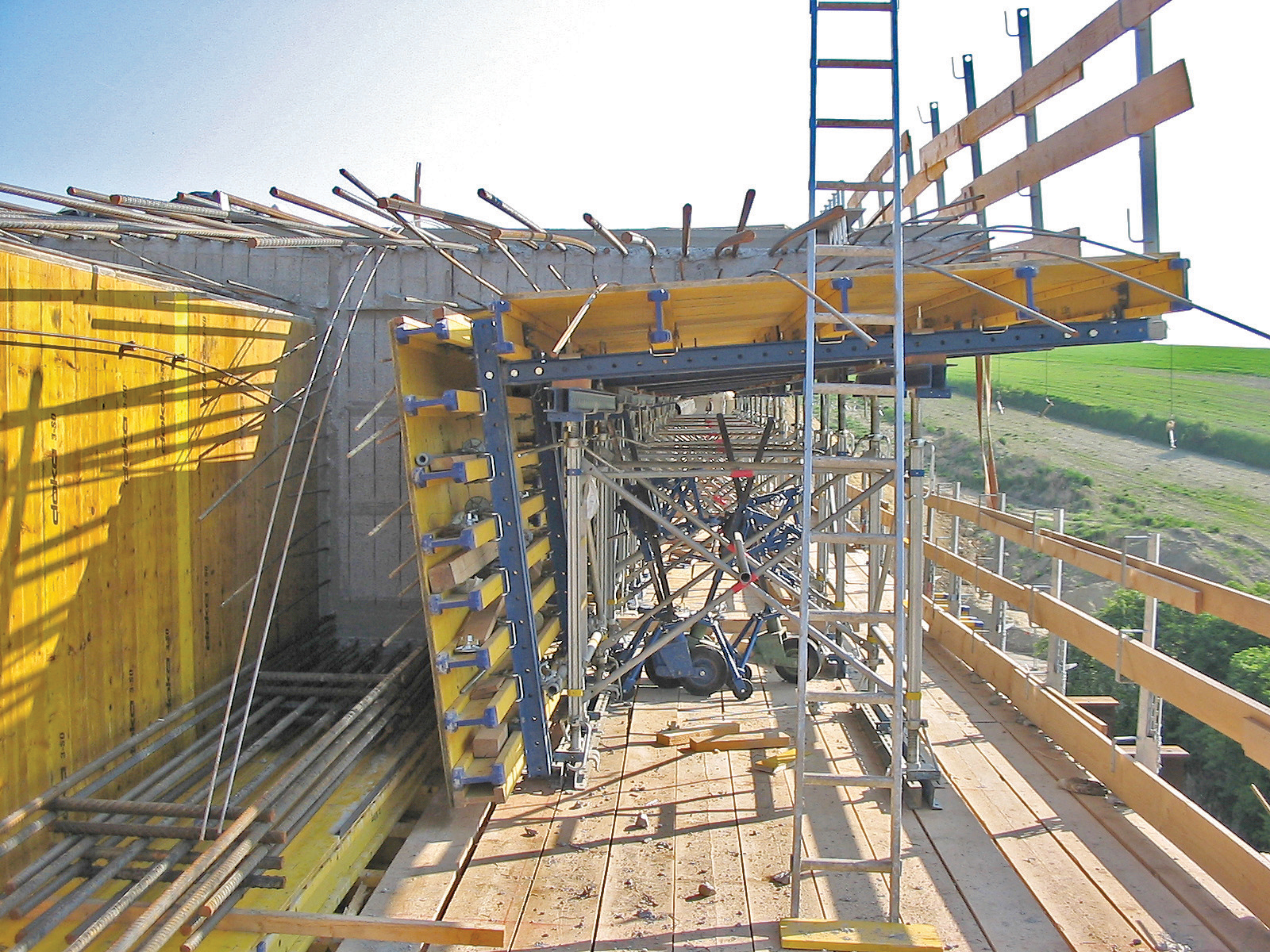
The ALPINE site crew is using an adaptable construction made of Doka Top 50 large-area formwork and Staxo 100 load-bearing towers to form the carriageway slab, main beams and cantilever arms
North of the Austrian capital Vienna, one of the region's biggest transport infrastructure projects for decades is currently under construction, the A5 Nordautobahn.
This will give the Greater Vienna region its first-ever high-capacity link to the Czech motorway and arterial road network, greatly easing congestion on the old main road. In the first phase of construction, 22.7km of motorway are to be built. Work on the second section, all the way through to the Czech border, is to start in 2010.
The A5 Nordautobahn is the first Austrian roadbuilding project to be financed using the alternative financing technique of a public-private partnership (PPP). The Bonaventura consortium, made up of981 Hochtief PPP Solutions, 1332 Alpine Bau and the French infrastructure specialists 2643 Egis, has a 30-year concession to finance, build and operate the Nordautobahn.
The works are being carried out by a joint venture of HOCHTIEF Construction and ALPINE Bau, and the total investment for the project is E933 million. The southern section of the Nordautobahn will be opened to traffic by 2010.
With 15 bridge structures, the 3.3km stretch of motorway between Gaweinstal and Schrick is technically the most challenging contract section of the route between the interchange at Eibesbrunn (also currently under construction) and the junction at Schrick. This section of motorway is projected to cost a total of around E225 million.
To build the technically demanding viaducts A5.11 and A5.12, the joint venture is relying on203 Doka formwork technology.
The 154m long superstructures are all designed as identical, statically separated beam-and-slab constructions, and are each being executed in five casting steps using tableforms that have been specially adapted to the geometry of the structure.
"Fast, safe vertical access to the bridge superstructures, at a height of 14m off the ground, is provided by a Staxo stair tower," says Doka.
The twin superstructures of the two motorway bridges rest on two rows of piers, each consisting of five piers of up to 14m in height. These piers were 'climbed' using Doka wall formwork FF 20, in two casting steps.
In order to keep within the tight construction schedule, the 15m wide carriageway slabs and the massively dimensioned (2.4m high and 80cm wide) main beams are being cast in one single pour. For this application, Doka's formwork experts at its Vienna branch faced custom tables with Large-area formwork Top 50 and mounted them on heavy-duty Staxo 100 load-bearing towers. This construction includes a forming box for the space between the main beams.
"The formwork for the main beams is joined to the timber beam formwork for the carriageway slab, so it can be retracted in one piece with this when the time comes to strip the formwork. This helps us by giving us short stripping and repositioning times, and speedier forming operations overall", explains ALPINE supervisor Marcello Gebhardt.
The formwork elements for the 2.7m long cantilever arms are also joined to the formwork for the main beams, and so can be quickly pulled back from the concrete. The entire Doka formwork construction is mounted on field-built, site-provided falsework. Following completion of the first carriageway, this falsework is moved across on travelling units ready for use on the second superstructure, saving a great deal of time. To permit the custom tables to be repositioned by crane, site management, headed by Marcello Gebhardt, joined with Doka's Vienna branch to develop a modified crane fork that is perfectly tailored to the geometry of the custom tables.
After the final casting step, the formwork boxes and the cantilever arm formwork are moved out using a telescoping stacker truck and a specially designed fork. This innovative solution makes it possible to do without the gaps that would otherwise be needed in the carriageway slab for lifting out the formwork by crane. The forming operations are right on time and within budget, and are on track for completion by the end of this year.
This will give the Greater Vienna region its first-ever high-capacity link to the Czech motorway and arterial road network, greatly easing congestion on the old main road. In the first phase of construction, 22.7km of motorway are to be built. Work on the second section, all the way through to the Czech border, is to start in 2010.
The A5 Nordautobahn is the first Austrian roadbuilding project to be financed using the alternative financing technique of a public-private partnership (PPP). The Bonaventura consortium, made up of
The works are being carried out by a joint venture of HOCHTIEF Construction and ALPINE Bau, and the total investment for the project is E933 million. The southern section of the Nordautobahn will be opened to traffic by 2010.
With 15 bridge structures, the 3.3km stretch of motorway between Gaweinstal and Schrick is technically the most challenging contract section of the route between the interchange at Eibesbrunn (also currently under construction) and the junction at Schrick. This section of motorway is projected to cost a total of around E225 million.
To build the technically demanding viaducts A5.11 and A5.12, the joint venture is relying on
The 154m long superstructures are all designed as identical, statically separated beam-and-slab constructions, and are each being executed in five casting steps using tableforms that have been specially adapted to the geometry of the structure.
"Fast, safe vertical access to the bridge superstructures, at a height of 14m off the ground, is provided by a Staxo stair tower," says Doka.
The twin superstructures of the two motorway bridges rest on two rows of piers, each consisting of five piers of up to 14m in height. These piers were 'climbed' using Doka wall formwork FF 20, in two casting steps.
In order to keep within the tight construction schedule, the 15m wide carriageway slabs and the massively dimensioned (2.4m high and 80cm wide) main beams are being cast in one single pour. For this application, Doka's formwork experts at its Vienna branch faced custom tables with Large-area formwork Top 50 and mounted them on heavy-duty Staxo 100 load-bearing towers. This construction includes a forming box for the space between the main beams.
"The formwork for the main beams is joined to the timber beam formwork for the carriageway slab, so it can be retracted in one piece with this when the time comes to strip the formwork. This helps us by giving us short stripping and repositioning times, and speedier forming operations overall", explains ALPINE supervisor Marcello Gebhardt.
The formwork elements for the 2.7m long cantilever arms are also joined to the formwork for the main beams, and so can be quickly pulled back from the concrete. The entire Doka formwork construction is mounted on field-built, site-provided falsework. Following completion of the first carriageway, this falsework is moved across on travelling units ready for use on the second superstructure, saving a great deal of time. To permit the custom tables to be repositioned by crane, site management, headed by Marcello Gebhardt, joined with Doka's Vienna branch to develop a modified crane fork that is perfectly tailored to the geometry of the custom tables.
After the final casting step, the formwork boxes and the cantilever arm formwork are moved out using a telescoping stacker truck and a specially designed fork. This innovative solution makes it possible to do without the gaps that would otherwise be needed in the carriageway slab for lifting out the formwork by crane. The forming operations are right on time and within budget, and are on track for completion by the end of this year.