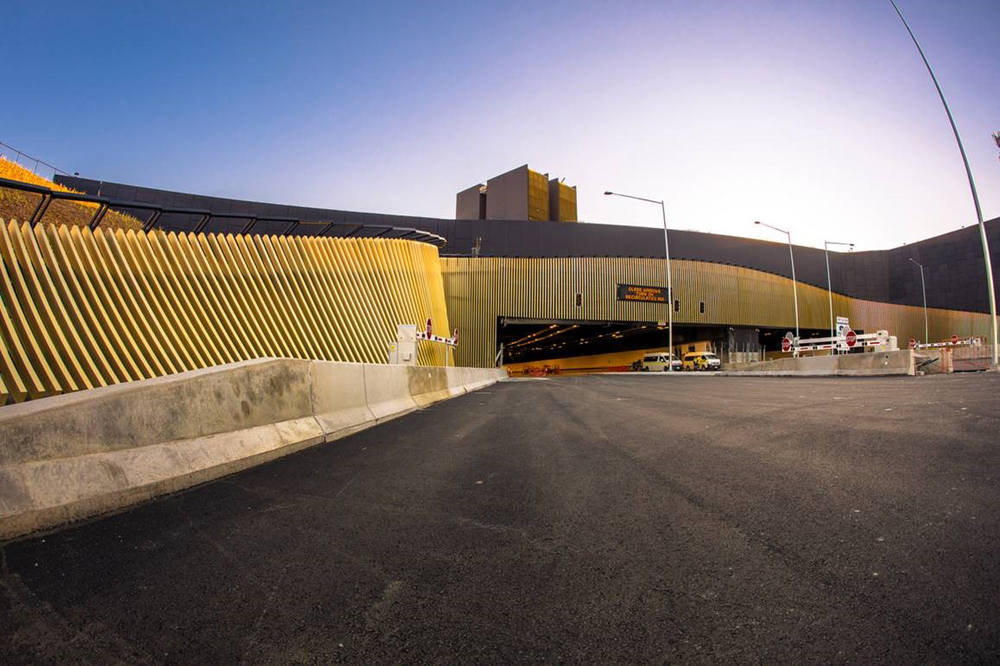
WestConnex is an ambitious 33km mostly underground motorway scheme, partially completed and partially under construction, in Sydney, New South Wales, Australia. The project, costing nearly A$17 billion, is being built in three main stages. It includes construction of around 26km of tunnels between the suburbs of Homebush and Kingsgrove, passing underneath Inner West suburbs including Haberfield and St Peters.
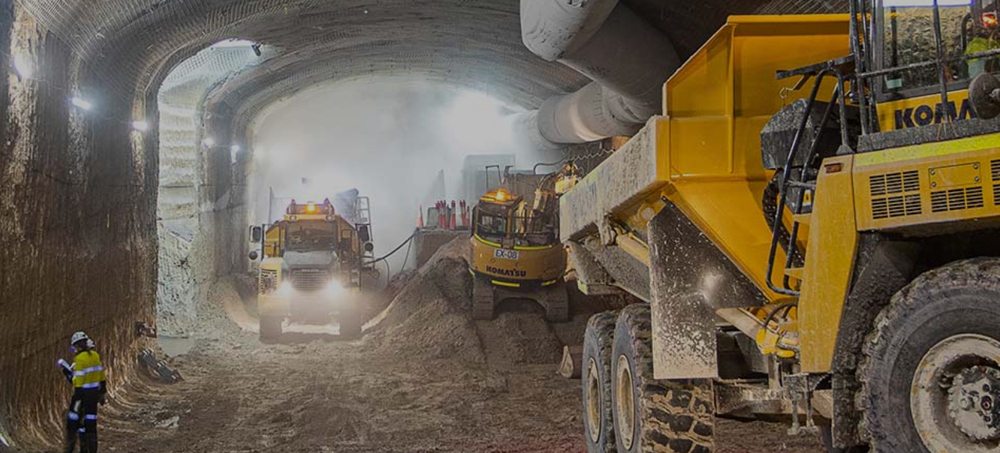
The Rozelle Interchange is part of - and at the heart of - stage three work that will link western and inner southern suburbs with the heart of the city. The $3.9 billion interchange is being built by the John Holland and CPB Contractors Joint Venture and managed by Transport for New South Wales, an agency of the New South Wales Department of Transport.
Work at Rozelle includes constructing around 22km of tunnels, including roadways, ventilation, access tunnels and cross passages – all constructed through Sydney sandstone. The project is within a 1km x 2km surface area from Blackwattle Bay to the Iron Cove Bridge. Roadways make up around 15km of the tunnels and underground works. The remainder consists of service tunnels, cross passages, emergency access tunnels, underground substations and HVAC systems - heating, ventilation and air conditioning.
Komatsu equipment is being used extensively to help construct the complex Rozelle interchange. Nearly 60 pieces of Komatsu equipment – including dump trucks, excavators and wheeled loaders – are working as deep as 65m beneath the inner Sydney suburbs of Rozelle and Lilyfield.
The overall project
Construction for the WestConnex project began in July 2016 and the first of the overall project’s tunnels, the M4 East, opened to traffic in July 2019. The second of the tunnels, the M8 Motorway – formerly called the M5 - opened this past July. The rest of the tunnels now being constructed in stage three, in what is called the most difficult of the project’s three phases, are expected to open to traffic in 2023.
Most of the project’s sections are open. The King Georges Road Interchange Upgrade opened in December 2016. King Georges Road is a major 12km arterial road running through the local government areas of Georges River Council and City of Canterbury-Bankstown.
In July 2017, the widened M4 motorway opened for traffic. The 50km partially tolled M4 runs parallel - and at times below ground - to the Great Western Highway and Parramatta Road.
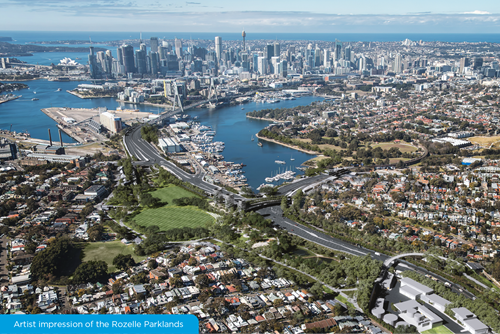
Then in July 2019, a tolled 5.5km eastern tunnel extension of the M4 from the suburb of Homebush to that of Haberfield was completed. Known as the M4 East or New M4 Tunnels section, it included around 7.5km of surface roads and was the second stage of the WestConnex project.
In July this year, the tolled M8 Motorway in a twin almost-9km tunnel under Sydney was opened. It links the M5 Motorway at Kingsgrove to St Peters Interchange. It consists predominantly of tunnels, including tunnel connections to the future M4–M5 Link and the future M6 Motorway. There is the capacity to add a third lane if required.
The M8 doubles capacity of the M5 East Tunnels and will save motorists around 30 minutes travel from south-west Sydney to the southern central business district. It will eventually connect to the M4-M5 Link (stage 3A), Sydney Gateway to the airport and the M6 to southern Sydney. A distance-based toll applies to the M8 and the M5 East.
M4-M5 Link
What lies ahead is the last stage, stage 3 – Rozelle interchange and the twin 7.5km M4-M5 Link tunnels, the most difficult and critical work of the entire WestConnex project. Up to nearly 60 Komatsu machines have been working underground. Some preliminary construction started in 2018 but work started in earnest late this year and will continue to 2023. It involves what are called the M4–M5 Link Main Tunnels, Rozelle Interchange and the Iron Cove Link. In effect, this stage is a project within a project.
The M4-M5 Link Tunnels will run between the New M4 at Haberfield and the M8 at St Peters, and incorporate stub tunnels to the Rozelle Interchange. The contractor on this stage, being managed by WestConnex /Transurban, is the Acciona Samsung Bouygues Joint Venture (ASBJV).
The Rozelle Interchange and Iron Cove Link will provide an underground motorway interchange to City West Link. It will also provide an underground bypass of Victoria Road between the Iron Cove Bridge and the ANZAC Bridge, with links to a proposed Western Harbour Tunnel. The contractor on this stage is John Holland and CPB Contractors Joint Venture. This stage is being managed by Transport for NSW.
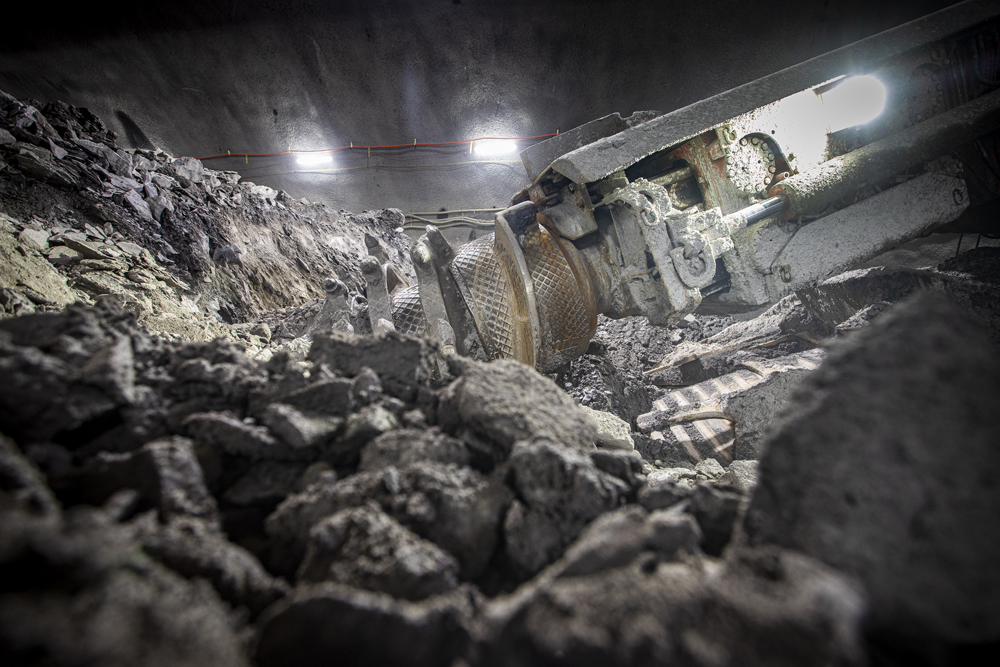
The interchange is located at the site of the old Rozelle Rail Yards. By building the interchange mostly underground, the project will deliver new active transport options in Rozelle and up to 10 hectares of new open space. The New South Wales state agency Transport for New South Wales is setting up the Rozelle Parklands Working Group to help determine the future use of the 10 hectare parklands and open space created by the project.
The Rozelle Interchange project has prepared an Urban Design and Landscape Plan in consultation with Inner West Council, the community and affected landowners and businesses. The plan will determine items such as landscaping, tunnel portals, tunnels, service buildings, bridges, retaining walls, pedestrian and cyclist access, lighting and wayfinding, heritage, monitoring and maintenance.
The future Rozelle Parklands will have a wetlands with a boardwalk, picnic and barbecue areas, play equipment, pedestrian and cyclist paths and green fields for leisure activities. There will also be two sports fields and four multipurpose courts within the Rozelle Parklands precinct.
Some of the ventilation buildings that originally were intended to be built on the surface have been moved underground. This means there will be extra ventilation tunnels in the Iron Cove area.
Ventilation is paramount
The M4 East – part of stage 1 - extends the existing M4 from Homebush to Haberfield via underground twin 5.5km tunnels with three lanes in each direction.
The tunnels are among the widest in the southern hemisphere and are flatter and higher than other tunnels in Sydney, meaning a smoother journey with less stop-start driving, relieving surface congestion and fewer vehicle emissions.
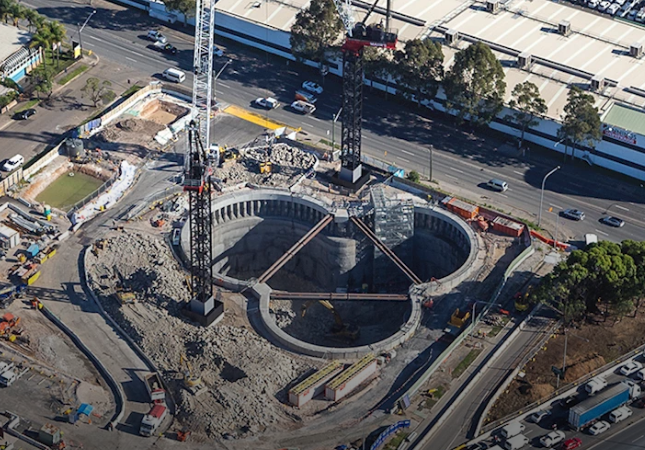
Ventilation for the tunnels in stage one is a longitudinal system with air drawn in the entry portals by moving traffic. Ventilation outlets at the western and eastern ends of the tunnel draw fresh air from outside the portal. This fresh air is combined with tunnel air before being emitted via the outlet where it is further diluted and dispersed. Monitoring stations, modelling and compliance testing make sure air quality is maintained. Monitoring results are publicly available and independently audited.
Meanwhile, air quality monitoring stations are installed all along the WestConnex Project corridor to collect data in local surface areas. These stations help WestConnex keep track of what the air quality was prior to project approval, prior to project operation and after opening to ensure there has been no measurable impact on local air quality and to assess any changes.
A key enabler for good air quality for the overall project is the Parramatta Road Ventilation Facility. The PRVF provides tunnel ventilation for the M4 project (stage one) and will for the future M4-M5 link (stage three now under construction). Arcadis was appointed to provide civil design services for the WestConnex M4 project in a joint venture with AECOM.
Due to the location of the PRVF within a densely-populated community, solutions were needed to reduce construction noise. To achieve this, the shape for the shaft includes three intersecting circular shafts each around 30m in diameter so they could fit on the constrained site at the intersection of Parramatta Road and Wattle Street. Also, most of the PRVF building was constructed below ground to minimise operational noise.
The PRVF was excavated to approximately 45m below existing ground level. The building itself was constructed from the base of the excavation with the top of the PRVF building approximately 27m above ground level.
To enable excavation of the PRVF shaft, Arcadis and AECOM designed the excavation retention system at the top of the shaft. This required 122 piles around the perimeter of the shaft.
To assist construction and enable the footprint of the shaft to remain as open as possible during excavation, the pile capping beams were propped by three temporary steel props spanning more than 28m. These props were replaced by permanent reinforcement concrete props once the PRVF building structure was built back to ground level.
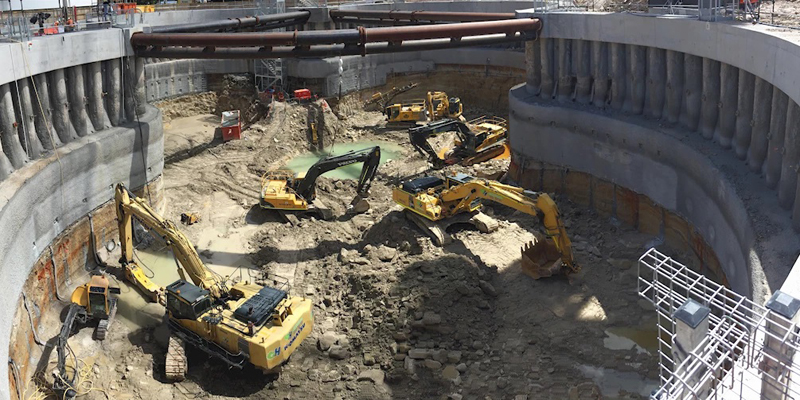
Formwork for the Parramatta Road Ventilation Facility was provided by RMD Australia. The PRVF building houses large fans that connect to twin tunnels at Haberfield. The building has three basement levels around 60m below ground and a few split levels above ground. The suspended slabs and beams vary in depth from 300mm to 1,700mm. Around 500tonnes of shoring was spread across three shafts, a setup that remained onsite well into 2018. RMD’s 74kN Rapidshor shoring system was combined with its Aluminium Beams (primary bearers), called Alform Beam and Albeam, which enabled RMD designers to increase the efficiency of the shoring system further. RMD was able to provide a complete package, ultimately reducing the number of components which saved the client time and money, while maintaining safety.
As well as the design of the excavation retention system for the PRVF, Arcadis and AECOM delivered geometric and road engineering designs, pavement design, flood assessment and drainage design, traffic engineering services, lighting design, utilities coordination and structural design of the bridges, retaining walls, cut and cover tunnels and buildings.
M8 air quality monitoring
The M8 motorway, part of stage 2 of the three-stage project, opened in June this year. The 9km twin-tube underground tunnel runs from the end of the M5 Motorway at Kingsgrove to St Peters Interchange in Sydney’s south region. A network of ACOEM air quality monitoring systems is providing environmental management.
Under stringent government regulations, all underground motorway tunnels require the inclusion, operation and maintenance of three specific air quality monitoring functions: sensors inside the tunnel, ventilation outlets and ambient locations around the tunnel.
The WestConnex M8 is the first tunnel project in Australia that incorporates ACOEM air quality monitoring hardware for all three regulatory components. In-tunnel air quality sensors are supplied by Tunnel Sensors. Ecotech has supplied ambient and ventilation outlet monitoring stations. Both companies are members of the AECOM group.
In addition, Ecotech has also been contracted to provide ongoing maintenance and data validation for air quality monitoring on behalf of WestConnex | Transurban which is responsible for owning and operating the asset during its concession.
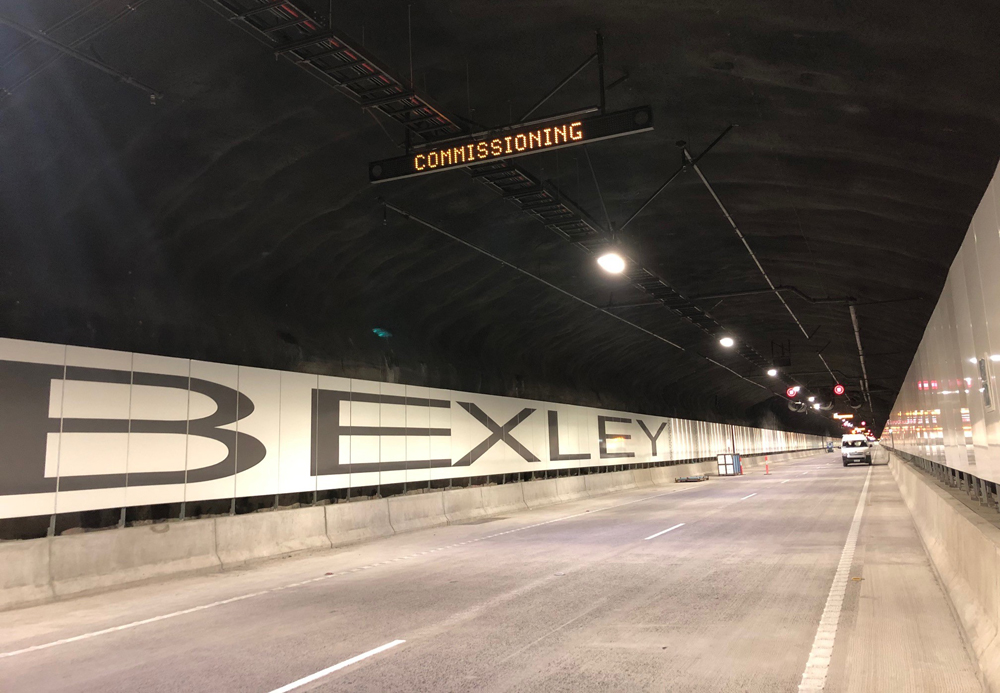
ACOEM has supported the tunnel delivery contractor, CPB Contractors Dragados Samsung Joint Venture since the project’s inception in 2014. Michael Preston, strategic business development manager with ACOEM, has noted that by using equipment from AECOM companies, there has been a “seamless solution for all aspects of air quality monitoring from initial planning, through construction phase and testing all the way to operations and maintenance contracts”.
Tunnel sensors, formed in 2005 as a subsidiary of Dynoptic Systems, is based in the UK. It designs and manufactures a range of air pollution monitoring equipment specifically for tunnels in the areas of visibility and dust, toxic gas emissions, air speed and direction as well as tunnel luminance and illuminance. Tunnel Sensors became part of ACOEM in 2019.
Ecotech, based in Melbourne, was set up 40 years ago to provide environmental monitoring for air, water, gas, noise, vibration, blast, meteorology, fine particulate and dust. It operates in more than 80 countries and became part of the AECOM group in 2017.
Last year Ecotech was commissioned to undertake continuous emissions monitoring and data reporting for the M4 East tunnel ventilation facilities, part of the stage 1 construction that was completed in July 2019. The M4 East tunnel ventilation facilities consist of two stacks, the Underwood Road Ventilation Facility (URVF1 and URVF2) and the Parramatta Road Ventilation Facility.
Komatsu goes underground
Komatsu has supplied 58 machines to the joint venture between September last year and August this year for stage 3 work, including the underground M4-M5 Link and the Rozelle Interchange. They are now removing a total of 2.65 million m3 of material from the site over the three-year construction period, ending in 2023.
The M4-M5 Link Tunnels run between the M4 at Haberfield and the M8 at St Peters and work includes stub tunnels to the Rozelle Interchange. The contractor for this work is an Acciona Samsung Bouygues Joint Venture (ASBJV) along with management by WestConnex | Transurban.
The contractor on the Rozelle Interchange and Iron Cove Link is John Holland and CPB Contractors Joint Venture, with management by Transport for NSW.
As well as the Komatsu equipment on the Rozelle site, the project has shotcrete rigs, rock bolters and face drills. Up to 22 roadheaders are carrying out the primary tunnel excavation. These machines - also called boom-type roadheaders or simply header machines - consist of a boom-mounted cutting head, a loading device usually involving a conveyor and a crawler travelling track to move the entire machine forward into the rock face to allow for continual cutting.
Komatsu’s site support includes what is called a pop-up workshop and parts store where three qualified Komatsu diesel technicians are on call 24 hours a day. Also, there is always one HM300-2 articulated dump truck on standby.
John Bostock, project plant manager for the Rozelle Interchange Project, says there were a number of reasons why Komatsu was chosen as the primary earthmoving equipment supplier for the project. “To start with, their service, support and equipment package was pretty good.”
But there was also Komatsu’s knowledge gained from working on other Sydney tunnelling projects, he notes. Komatsu equipment has been extensively used on the WestConnex 1b project (Homebush to Haberfield), WestConnex 3a (Haberfield to St Peters) and NorthConnex (Wahroonga to West Pennant Hills).
“The performance of the equipment since we started here in September last year has proven to be pretty good; there were a couple of issues with accumulators, which they replaced, but overall reliability and availability have been very good, in line with what we expected.”
Bostock and his plant management team recognise that skilled and careful operators are critical to successful equipment operations. To facilitate this the team has put additional effort into ensuring that operators look after their equipment and – importantly - are recognised for doing so.
“Tunnelling is a very harsh environment and we’re running a 24-hour-per-day operation,” he explains. “If you add up the number of plant items onsite, it’s around 130 to 140, plus forklifts, underground vehicles and so on. We need to be able to crew up to 22 roadheaders working three shifts. It’s also a challenge to get really good operators and it’s important to find people who want to look after the gear.”
To achieve this, Bostock’s team is running a Take Pride in your Plant campaign. Posters are up throughout the site reminding operators of the importance of caring for their equipment and working safely.
“We want the cabins to be pleasant places in which to work, not filled up with dried mud and dust. So we ask the operators to clean their cabins at the end of their shift. And with COVID-19, in the pre-starts we communicate to operators the importance of wiping down their cabins, steering wheels and controls as an additional measure to sanitise the machines,” he says.
If a machine is scratched, even incidentally or there is very minor damage, Bostock says he wants to know about it, no matter how minor the incident. If it gets reported, then actions can be taken to mitigate a similar incident in future.
To encourage operators to report such incidents, Bostock’s team has implemented a plant award following a random inspection of four pieces of equipment per team. “We mark against various criteria, including safety, cleanliness, if the machines are in good order and so on.”
It is recognition for the extra effort the operators and teams put into their work. “The reward is a monthly barbecue for the winning site team and a trophy to keep at reception until the next inspection. For us, the benefits are safety, cost control, fleet efficiency and taking pride in their work and their fleet. And we are seeing some great results,” he says.
KOMTRAX, Komatsu’s remote machine monitoring technology, has proven to be an essential part of managing the Komatsu fleet at Rozelle. An in-tunnel WIFI system connects each machine to a surface transmitter and from there to the company’s remote monitoring satellites.
Bostock has also been applying feedback from KOMTRAX to ensure optimum operation of machines. “It allows us to intervene to eliminate poor operating habits. By having all of this information available to us quickly, we can talk to operators about any incorrect operating procedures,” he says.
“This added technology from Komatsu is a good tool in helping us reach our goals of the safe and correct operation of equipment at all times and ensuring maintenance is kept up to date.”
The WIFI also includes a tracking system giving the location of each piece of equipment, vehicle and person. The project team always knows the location of each machine and person in relation to each other.
Bostock is also using this tracking system to optimise the use of equipment onsite – particularly the movement of trucks which is a complex process across the three tunnelling sites.
“We have quite an advantage here in that all three tunnel access points are located on the one site, which allows us to maximise the use of our fleet across the tunnels,” he says.
“The rule of thumb is that you need two trucks per roadheader. So if you have 22 roadheaders in operation at any one time, you’d need 44 trucks. But we know our utilisation factor is about 60%, which means we need only 28 trucks onsite full time. So we’re running it here like an Uber operation. The trucks are all on call and using our tracking technology we put them where they’re needed, when they’re needed.”
The bulk of the Komatsu equipment onsite – all but 11 machines – are fitted with ultra-low emission Komatsu Tier 4 Final engines which contribute to significantly cleaner air quality underground.
Emissions testing is carried out on all the underground equipment every month to check for compliance and safety. In the past, with Tier 1, 2 and 3 engines, catalytic converters have had to be added to meet requirements for underground use. “But what we are finding with these Tier 4 engines, the emissions are much lower, conditions are much cleaner,” says Bostock. “In fact, the emissions levels are significantly better than putting a catalytic converter on a Tier 3 machine.”