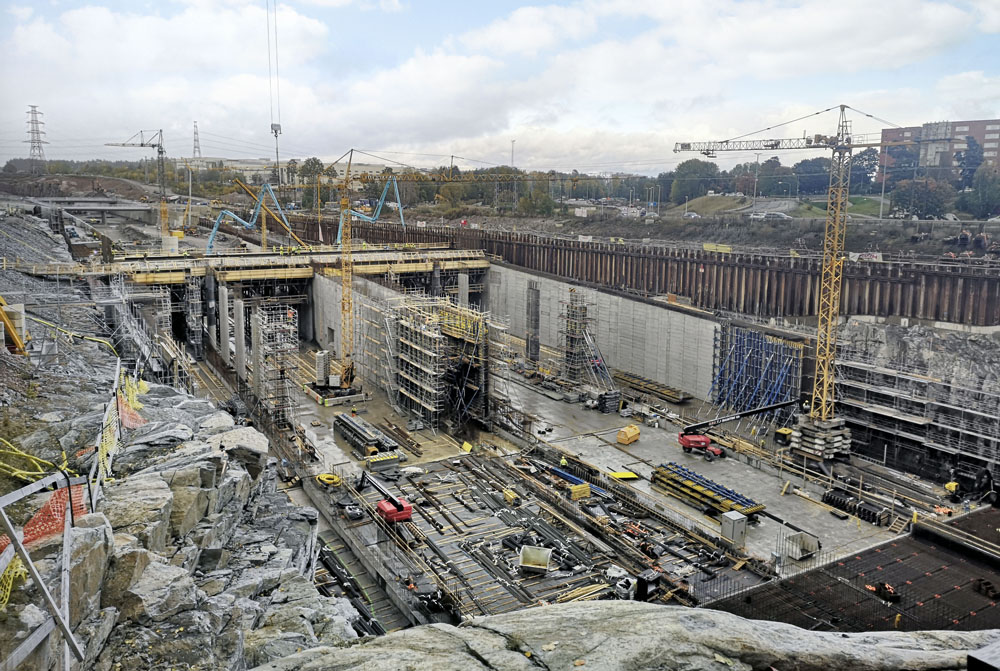
The Swedish capital Stockholm – with a fifth of the Scandinavian country’s population - has the fastest urban growth rate in Europe. The city region’s 14 islands are home to more than 2.1 million inhabitants. By 2030, Stockholm’s population is expected to grow to around 2.5 million.
For sustainable urban development, well-functioning] and safe infrastructure is essential. Local public transport has been improved, thanks in part to a new commuter railway beneath Stockholm’s central districts. The 7.4km Stockholm City Line, or Citybanan, is an electrified double-track commuter route with two stations which entered service in mid-2017.
Although the Citybanan represents an important step towards better public transport, it is not sufficient in itself to combat increasing vehicular traffic in the city. Stockholm only has only one major thoroughfare, Essingeleden, which was opened in 1967 after the country switched over to right-hand side driving. Essingeleden became the first six-lane motorway in Sweden. It was designed for 80,000 vehicles per day but 50 years on around 160,000 vehicles use it on a typical working day.
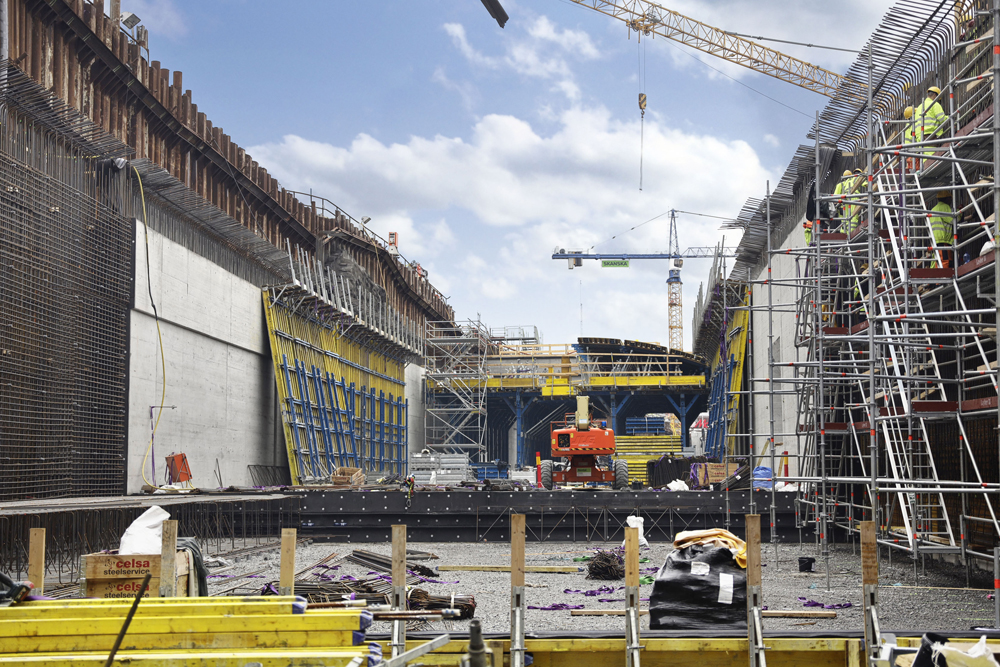
During the 1990s, Essingeleden was repainted from six lanes to eight lanes to ease congestion. Since January 2016, motorists using Essingeleden have been subject to a congestion charge. Nonetheless, traffic on the Essingelden remains extremely vulnerable to disruption by road accidents. To address this situation, a 21km motorway bypass is being constructed to link the south of the city – Skärholmen - with the north - Häggvik. This new road, the E4 Bypass Stockholm, will divert traffic away from the city centre towards the west.
The E4 Bypass - in Swedish, E4 Förbifart Stockholm - is one of Sweden’s largest infrastructure projects. When finished in 2030 it will run between the Kungens Kurva (King’s Curve) interchange in the south of Stockholm and the Häggvik interchange north of Stockholm.
Of the project’s 21km, fully 18km will run through tunnels, making the bypass one of the world’s longest urban road tunnels and slightly shorter than Tokyo’s Yamate Tunnel that runs for just over 18km. As part of the project, six interchanges will be built to connect the tunnel system to the existing roads along the tunnel’s route.
It will consist of twin tunnels with its deepest point 70m below sea level and beneath Lake Mälaren. Both tunnels will have three lanes, increasing to four at the six new interchanges along the route. During construction work, around 22 million tonnes of rock is being excavated.
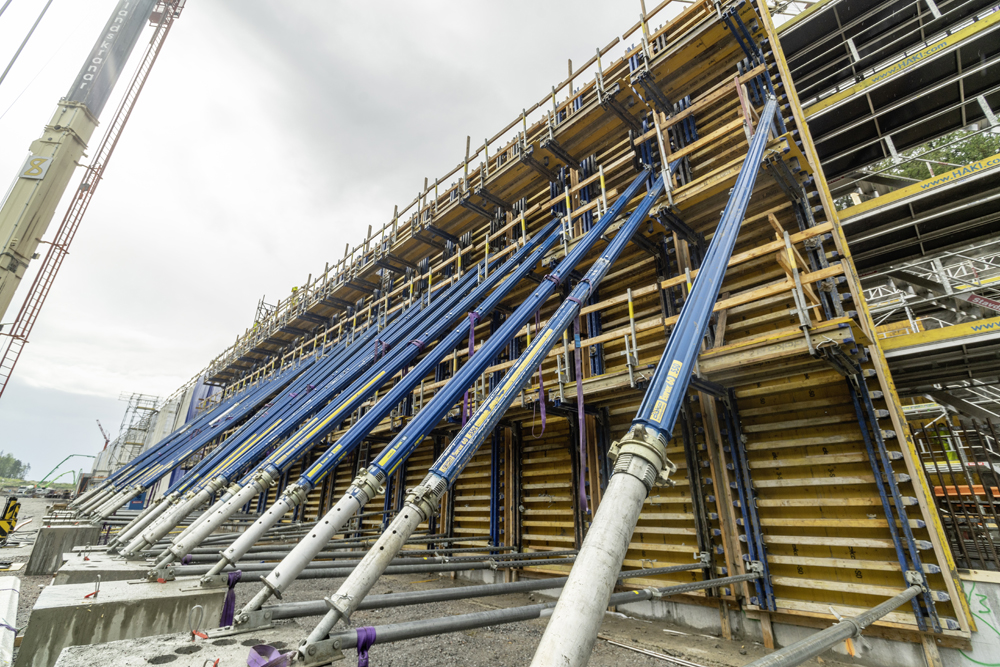
Förbifart Stockholm has been a long time coming, and will be even longer, due to politics, increasing costs and earlier worksite safety issues.
In 2009 the project was approved by the Swedish government and construction was expected to start in 2010, taking eight years to complete. The cost was estimated at US$3.3 billion. However, the construction didn’t begin until 2014 with tunnel excavation starting in 2016. Expected time to completion is a decade and at an elevated cost of $4.11 billion. Worksite safety issues in 2019 caused the cancellation of a contract for one part of the tunnel. The completion date has been reviewed, with its opening now looking like 2030 – and at an even higher cost of nearly $4.5 billion.
Among the many major sub-contractors is Doka which is providing formwork equipment for four of the project’s sections (see Bypass pass notes box). Doka’s products included its Framax Xlife and Framax Xlife Plus systems with accompanying large-area formwork Top 50, load-bearing tower Staxo 40 and Staxo 100, as well as its formwork traveller and the heavy-duty supporting system SL-1.
Doka’s challenges
The FSE105 Kungens Kurva - King’s Curve - section is the largest of the four contracts. The project includes a traffic area with a roundabout bridge and ramps, a 350m-long concrete trough and two 330m-long concrete tunnels. Around 300,000m³ of rock and 375,000m³ of soil are being displaced.
The North of Hjulsta section is where European Routes E4 and E18 meet and will be one of Sweden’s most important interchanges. The project section includes a 200m concrete tunnel. Doka said that its main challenge was to supply two formwork travellers that could be used to concrete the walls and ceiling simultaneously. The client also wanted to be able to move the travellers once a week. To achieve this, the travellers were fitted with hydraulic systems to complete the formwork work rapidly and logically.
A monolithic construction method was adopted for the North of Hjulsta section, by which walls and slabs are constructed together. Cement concrete is poured in a lightweight aluminium formwork system requiring reinforcement bars for needed strength. The method is fast and efficient because the walls and slabs are cast in one go.
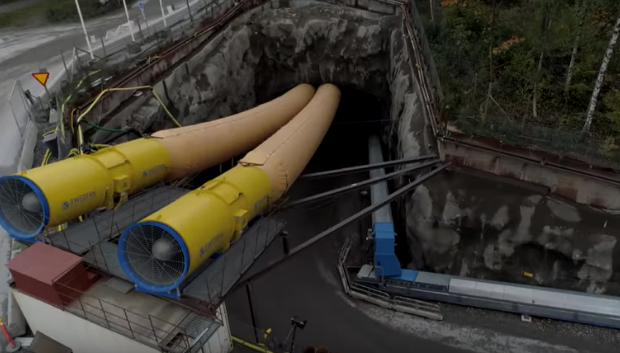
For the FSE61 Akalla section, an elliptical flyover is being built. Construction includes around 950m of motorway, major shoring measures for the excavation work, a 120m-long tunnel built using the cut-and-cover method, a 480m cutting for the tunnel entrance and a roundabout.
Construction from the city suburb Häggvik towards the flyover is progressing through a deep rock gorge alongside the Hansta Nature Reserve. Work is being carried out in a highly challenging traffic environment, where access for traffic must be guaranteed at all times. On average, over 100,000 vehicles pass the site each day.
Tough tunnelling
Driving the tunnels has proved more difficult than anticipated, according to main client Trafikverket, the Swedish road authority. The tunnels are being driven through rock of mainly good quality. Nonetheless, the rock is being injected with cement-based sealant before blasting. This technique prevents groundwater from entering the tunnel and the lowering of the groundwater level, according to the authority. Then the tunnel itself is blasted out with a traditional drill and blast method.
The tunnel is driven forward in cycles, with seven steps in each cycle. Progress is 5-15m per week.
Holes 20-25m long are drilled obliquely in a ring around the tunnel. A high-pressure mixture of cement and water is forced into the bore holes and out through any cracks in the rock. The hardened cement seals the rock.
Next, blasting holes are drilled using a computer-guided drilling rig and a blasting agent containing the blast charge is pumped into the holes. The charges are sequentially connected to ensure controlled and precision blasting.
Trafikverket estimates that more than 19 million tonnes of rock must be transported away from the tunnels but as much as possible is used for construction of the bypass and in other projects in the region.
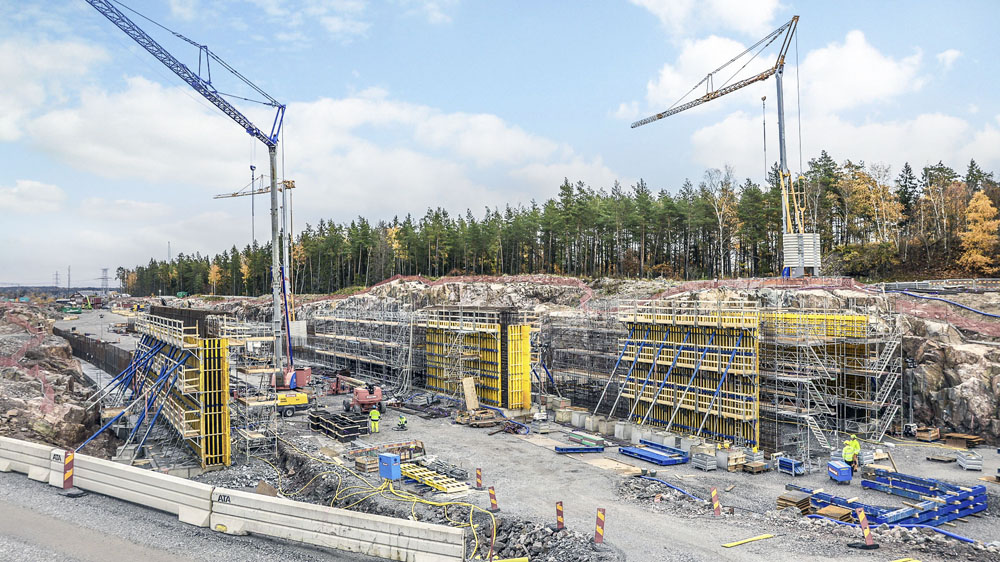
After scraping the tunnel ceiling and walls – both mechanically and manually – the tunnel is reinforced with rock bolts. The need for rock reinforcement varies along the route and depends on the quality of the rock.
A suspended ceiling made of sheeting directs water seepage along and into the tunnels main drainage system. The sheets are welded together and covered with reinforced concrete. The concrete walls and ceiling are then installed; this is what drivers will see as they pass along the tunnels.
Better with Bentley
Construction of the new bypass is taking place close to many sensitive areas, passing through natural and cultural reserve areas, as well as beneath Lake Mälaren, Sweden’s third-largest freshwater lake. Two islands on the lake are important Viking Age archaeological sites, while a third, Lovön, is the site of Drottningholm Palace – the residence of King Carl Gustav of Sweden and a UNESCO World Heritage Site.
Together with the client, Trafikverket, the AECOM-ÅF team had to find a way to excavate and transport around 19 million tonnes of rock during construction, ensuring that the impact to the surrounding environment was minimal.
The answer was to create underground crushing chambers at several locations along the route, as well as tunnels through which they could transport the rock mass. Conveyor belts would then take 50% of the rock to jetties, from where it moved through Stockholm’s waterways to temporary reception points.
Nearly 600 designers from 20 disciplines in nine countries are involved in the project, with the design of the rock tunnels alone requiring the creation of over 50,000 documents. The problem with generating such a large amount of data is that it can end up being unstructured, poorly coordinated and difficult to manage. Such inefficiency can stall and add extra costs to projects.
Designers AECOM and Swedish partner AF Consult used the project as a building information modelling (BIM) pilot. So successful was the BIM work that construction-ready 3D models are part of the tender process for the 50 contractors expected onsite.
Using Bentley MicroStation, MXROAD and InRoads, AECOM modelled evacuation routes and assessed the impact and operation of the tunnel facilities in a virtual environment. ProjectWise allowed the incorporation of metadata in all 3D designs to facilitate asset management throughout the project life cycle.
Bentley i-models enabled infrastructure information exchange, with ProjectWise as the common data environment, ensuring information mobility. Bentley Navigator provided the collaborative 3D design environment necessary to detect clashes and design issues among the 19 different disciplines’ models.
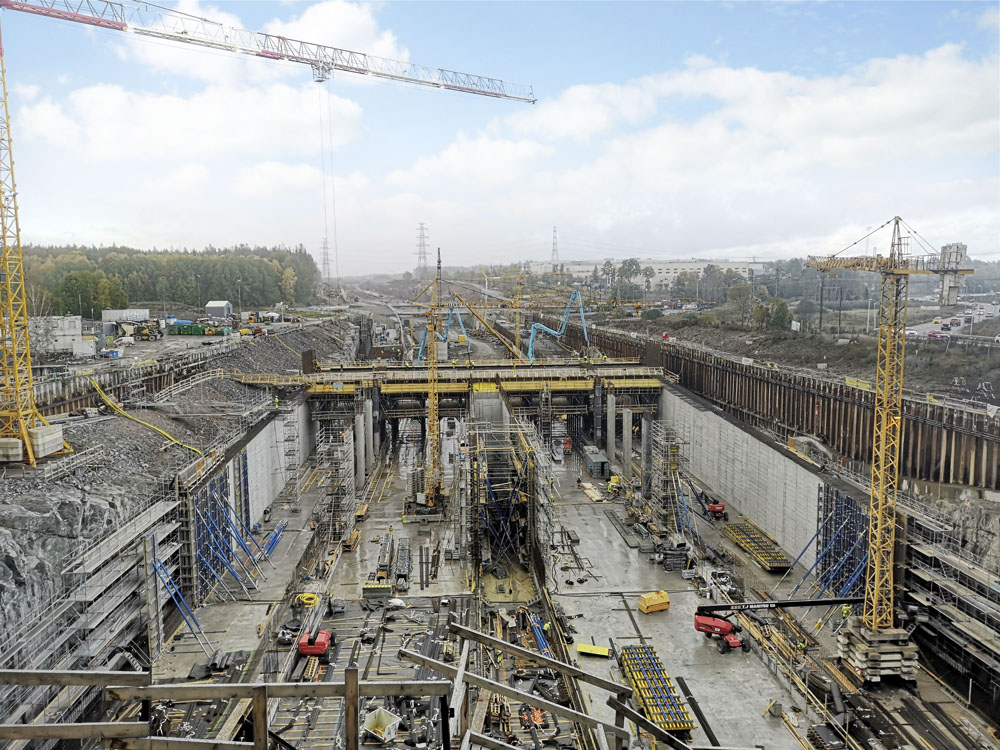
The model became the basis for scheduling, quantity and cost estimates, as well as construction-ready design documentation. The common data environment provided by ProjectWise facilitated the delivery of information to contractors during construction. Contractors accessed models for applications such as automatic machine guidance to assure quality and safety of onsite operations.
Using ProjectWise to provide a common data environment permitted rigorous optioneering during design development. The streamlined, collaborative process for review and checking design detailing produced correct, well-thought-out solutions during the early stages of the project. As a result, significant time and cost savings will be realised in the operations phase. The use of ProjectWise will carry forward through construction - expected to be completed in 2025 - and into operations, enabling better asset management and lower operating costs.
AECOM’s work using Bentley BIM software won accolades at the annual Bentley Be Inspired awards in 2015. The contractor walked off with top honours in the Innovation in Megaprojects category: E4 Stockholm Bypass FSK02 Rock Tunnels Design Contract.
Bypass pass notes
CLIENT: Trafikverket Swedish Transport Administration (STA)
CONSTRUCTION COMPANIES:
NCC, Skanska and Züblin Scandinavia
FOUR CONSTRUCTION SECTIONS:
l FSE105 Kungens Kurva
l FSE502 North of Hjulsta
l FSE61 Akalla
l FSE62 Häggvik
TOTAL MOTORWAY LENGTH: 21km
TOTAL TUNNEL LENGTH: 18km
TOTAL VOLUME OF ROCK: 22 million tonnes
CONSTRUCTION START: Autumn 2015
SCHEDULED COMPLETION: End 2030
ESTIMATED DAILY TRAFFIC BY 2035: 140,000 vehicles