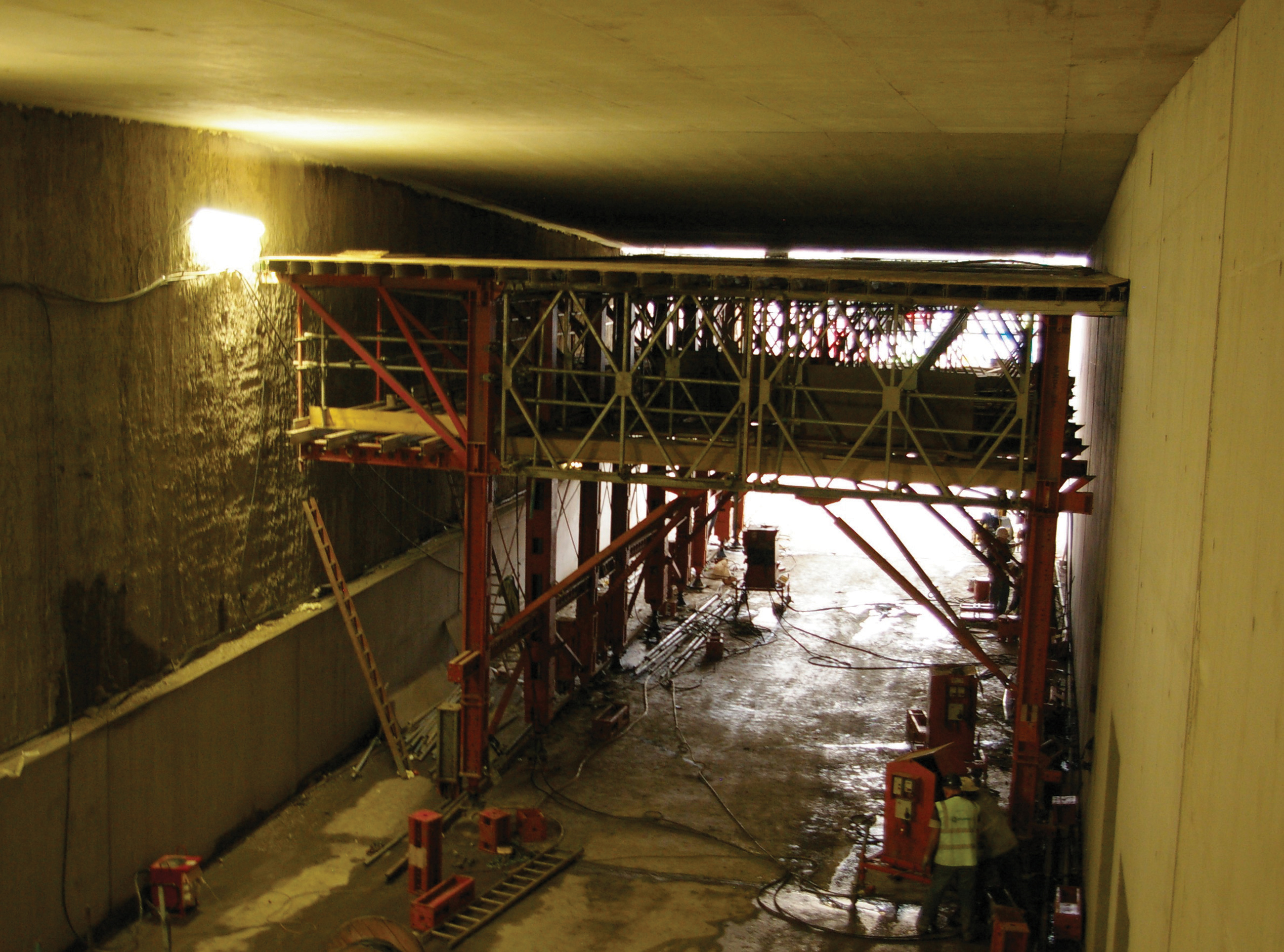
While tunnels are often more expensive than bridges, they can offer environmentally attractive options for transport schemes. Patrick Smith reports
Tunnels offer environmentally attractive options for a range of transport infrastructure schemes, but in many cases high construction costs may restrict their use. For example, at water crossings a tunnel is generally more costly to build than a bridge although where navigational considerations may limit the use of high bridges or drawbridge spans, a tunnel may be the only option.Bridges also often need a larger footprint on each shore than tunnels, and in many city centre areas, particularly where there are environmental concerns or where there are expensive properties such as Manhattan, London, Paris and Hong Kong), tunnels offer an alternative solution.
The 'Big Dig' project in Boston, USA, replaced unsightly elevated roadways with a tunnel system to increase traffic capacity, hide traffic and reclaim land thus reuniting the city with its waterfront.
In Paris, a 4.5km section of double-deck tunnel (nicknamed Duplex) on the A86 between Rueil-Malmaison and Vaucresson-A13 completed a portion of Paris' second ring road. Vehicles run in opposite directions on each level, while trucks have a separate tunnel.
Engineered by Cofiroute, the tunnel reduces a previous 45 minute journey to ten minutes, and by reducing the surface traffic by 15%, it has a very significant contribution to the reduction of greenhouse gases emissions.
The tunnel's state-of-the-art safety and security systems include equipment from
"An impressive traffic management centre was erected in Rueil to collect all data from the numerous control and safety sub-systems inside the tunnel, particularly video cameras and the Citilog Automatic Incident Detection system. On the video wall a tunnel schematics shows the traffic in real-time as well as incidents and anomalies. The faintest alarm is looked at and operators can remotely activate security systems as well as launch emergency vehicles based at both ends of the tunnel," says Citilog.
One of the largest infrastructure projects ever to be undertaken in Queensland, Australia, The Clem Jones (Clem7) Tunnel, is now open to traffic marking a historic day for Brisbane. It links five existing major motorways and arterial roads on the north and south sides of the Brisbane River and is designed to alleviate traffic congestion in this rapidly growing city.
Here, a total of 224 intelligent cameras monitor the 6.8km tunnel, pinpointing potential hazards before they occur.
Traficon's hi-tech automatic-video incident detection (AVID) cameras monitor traffic flow in the tunnel, automatically triggering alerts for abnormal incidents so motorists can be quickly diverted in the event of a disaster. These AVID cameras (integrating VIP-T modules) are able to pinpoint accidents, pedestrians, smoke or debris warnings. Operators are then able to assess the incident, before employing safety procedures ranging from closing lanes to emergency evacuations.
The tunnel's main control room at Bowen Hills will be manned 24 hours a day by teams of two, who will monitor the more than 60,000 cars expected to pass through each day. Main control will also be able to break into the 12 major FM channels and nine AM channels to broadcast pre-recorded or live directions for motorists, warning them of situations ahead.
Hindhead Tunnel
In the UK, the Hindhead Tunnel project, the longest non-estuarial tunnel in the UK, will feature cross passages every 100m and stateof- the-art safety and communications systems including high quality lighting and ventilation, CCTV surveillance and radio-interrupt systems to convey quick appropriate information to tunnel users.The A3 trunk road is a major highway between London and Portsmouth on England's south coast. To tackle congestion and improve safety on this busy route, which carries an average of 28,400 vehicles/day, the UK
As part of an integrated single team with the Highways Agency and its consultant, Mott MacDonald is responsible for all design aspects of the tunnel and the highway, including civil, structural, geotechnical, mechanical, electrical, fire and safety systems engineering. Specialist assistance is being provided by Wessex Archaeology, landscape and ecology consultant RPS, and statutory procedures advisor Persona Associates.
The ground conditions are predominantly sandstone and the tunnel bores will be constructed using sprayed concrete lining, with a target completion date in 2011.
Balfour Beatty appointed
A spray-on waterproofing, Masterseal 345 developed by
Using some 80,000m2, Hindhead is the largest application of Masterseal 345 in the world to date, surpassing the 60,000m2 applied during the Clem Jones tunnel project.
When Balfour Beatty reached the stage where it was faced with the task of core drilling approximately 13,000 holes in the walls and floors of the tunnels, the main requirements were speed of drilling and reliability.
The holes in the tunnels' shotcrete walls needed to be 40mm diameter, 150mm deep and drilled every 750mm at an upward angle using rigs mounted on the concrete shutter units. The holes in the tunnel floor needed to be 137mm diameter and 220mm deep drilled vertically every 2m using a portable drill rig. Both sets of holes are needed to ensure total stability of the automatic concrete shutter units when forming the concrete tunnel lining sections in situ.
With just under 1.8km on each bore needing to be lined, it meant that approximately 9,500 holes at 40mm and 3,500 holes at 137mm needed to be drilled.
The technical solution was provided by Ted George,
Chosen for core drilling the walls were eight of the new Atlas Copco LCD 1500 hydraulic core drills (two per shutter) each powered by an Atlas Copco electric, 20litres/minute hydraulic power pack. Electric power packs were selected because they do not pose a problem in the tunnels with exhaust emissions.
Meanwhile,
Formwork Solution
Tasked with forming the all-important safety escape route on the North structure to the new £260 million (US$400 million) Tyne Tunnel project in north-easy England, funded jointly by concessionaire TT2 and project promoter, the Tyne and Wear Integrated Transport Authority (TWITA), specialist contractor Dunne Building & Civil Engineering used an innovative new ceilingmounted design from Having prepared for the needs of the system when the roof slabs were poured using an RMD Kwikform traveller solution, special tubes were incorporated into the roof slab above the wall position and RMD Kwikform recoverable Anchor Screws either side.
The Anchor Screws enabled sectional runway beams to be fixed into place, while the tubes allowed the concrete to be poured from above the roof slab to effect the top down wall construction. The success of the wall formwork system and its ability to allow for large escape voids to be cast in situ was crucial in delivering the project to an extremely tight programme.
Appointed by TT2's design and build contractor,
Working in the tight confines of the covered tunnel section itself, complete with its 1.2m thick concrete roof, the wall formwork system, designed by formwork and falsework specialist RMD Kwikform, had to be assembled inside the tunnel and lifted into place in a very confined space.
Ian Fryer, engineering director for RMD Kwikform UK, said: "The solution that we proposed was to mount full-size formwork panels to suit the wall on beam trolleys, which would run on steel runway beams fixed to the previously cast tunnel roof slab. It was this innovative solution that ticked all the boxes for the main contractor Bouygues Travaux Public, who specified this approach for the project."
The company's offering is a package of technologies and includes wall treatment, effective lighting, anti-smog coating and surface upgrades. SCT can provide a high visibility, acrylic varnish-type coating for the walls that is reflective and durable and makes the tunnel easier to clean as well as reducing the lighting requirement. The anti-smog treatment is based on titanium dioxide technology, is washable and reduces exhaust pollution, aided by the fitting of UVA lamps.
High performance LED lighting is said to reduce power consumption and offer extended life over previously available technologies.
An abrasion treatment for asphalt makes surface lighter and helps boost tunnel brightness while a spray-on titanium dioxide treatment further reduces smog.