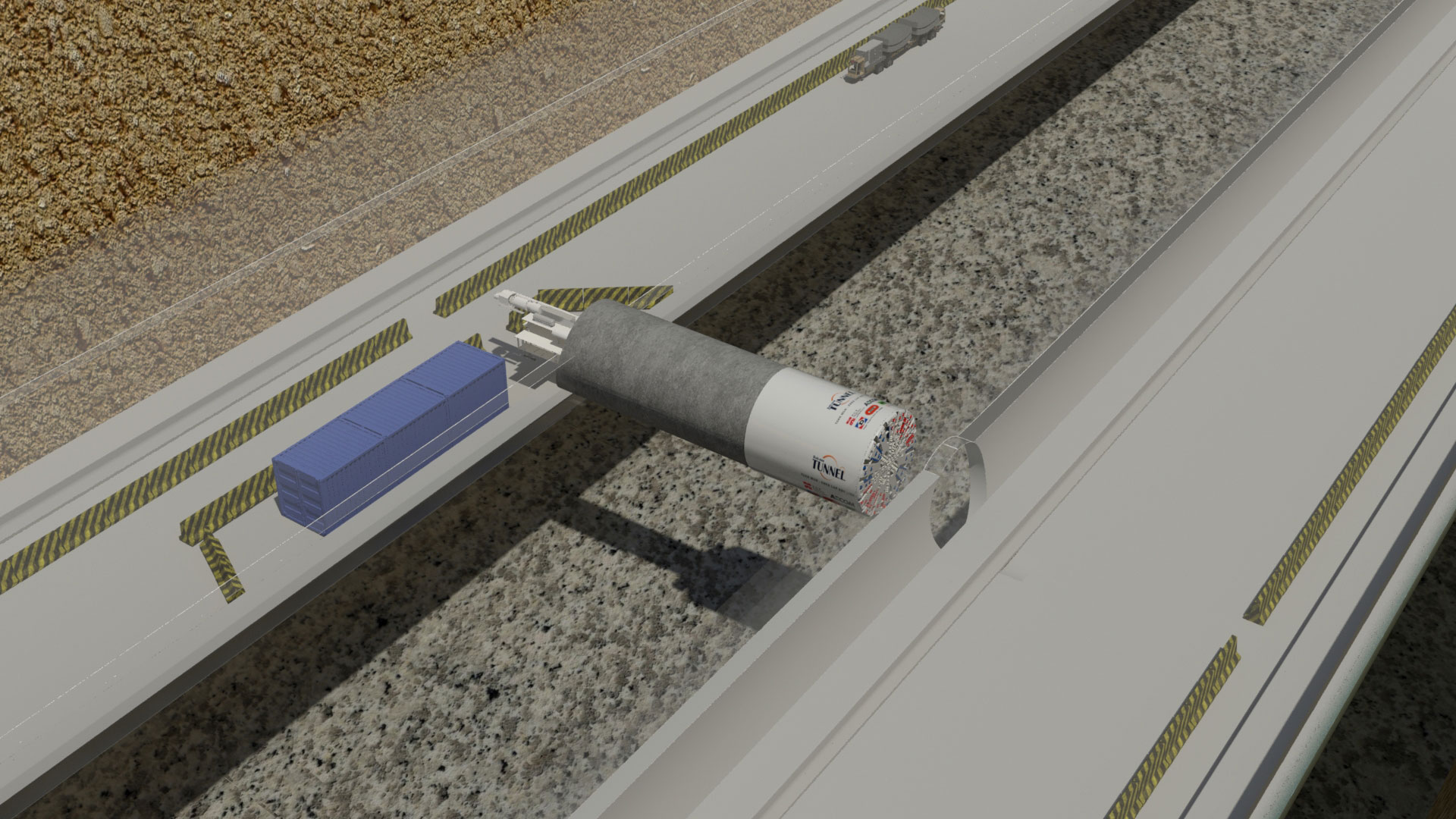
It is not only the scale of the Tuen Mun to Chek Lap Kok tunnel that impressed delegates but the number of novel technologies that Dragages Hong Kong, a Bouygues Construction subsidiary, is employing on this project.
The 4.6 km tunnel running 60m below sea level is part of a strategic new route linking Hong Kong’s airport on Lantau Island and the New Territories. Dragage’s contract includes reclamation of 16.5-hectares at the tunnel’s north end to accommodate the north portal and a ventilation building. Work started in 2013 on the nearly US$2.4 project and is due to run until 2018.
After initial larger sections of tunnel were completed, the Herrenknecht-made TBM was converted to a 14m-diameter machine to dig the southbound tunnel while another
Dragages is using its Mobydic system that employs sensors in the disc cutters to take measurements such as speed of rotation and temperature of the discs. As well as indicating disc wear, the information provides insight into the type of rock through which the TBM is churning.
Another Bouygues remote technology, Snake, uses an exploration arm equipped with a high-pressure jet to clean the tools making them ready for inspection and possible replacement. Perhaps the most impressive for delegates was the use of the Telemac, a heavy robotic arm to change cutter tools.
Human intervention is also required to change tools. Because tunnel pressures are high due to the water above it and the fractured rock - up to 6 bar - specialist tunnelling divers must do the work. They remain in pressurised containers on the surface and are shipped to the cutter head in pressurised shuttles. This avoids divers having to go through several compression and decompression cycles during a shift if needed. Apart from saving time, is also lowers health risks associated with the cycles.
Equally as challenging technically is construction of 56 cross-tunnel passages for which Dragages and Herrenknecht devised special 3.85m-diameter mini-TBMs, or pipe-jacking machines. When combined with launch frames, they can cope with the high pressures. To date the contractor has constructed six cross passages using this method.