New and highly regarded existing formwork systems have been used in major recent transport-related construction projects across the globe. Guy Woodford looks at some of their applications
The multi-million dollar Mississippi River Bridge project in the United State is creating a vital new gateway between Illinois and Missouri.
Central to the project is the realignment and reconstruction of Interstate 70 and a new landmark bridge, featuring two pylons projecting vertically from the Mississippi river bed w
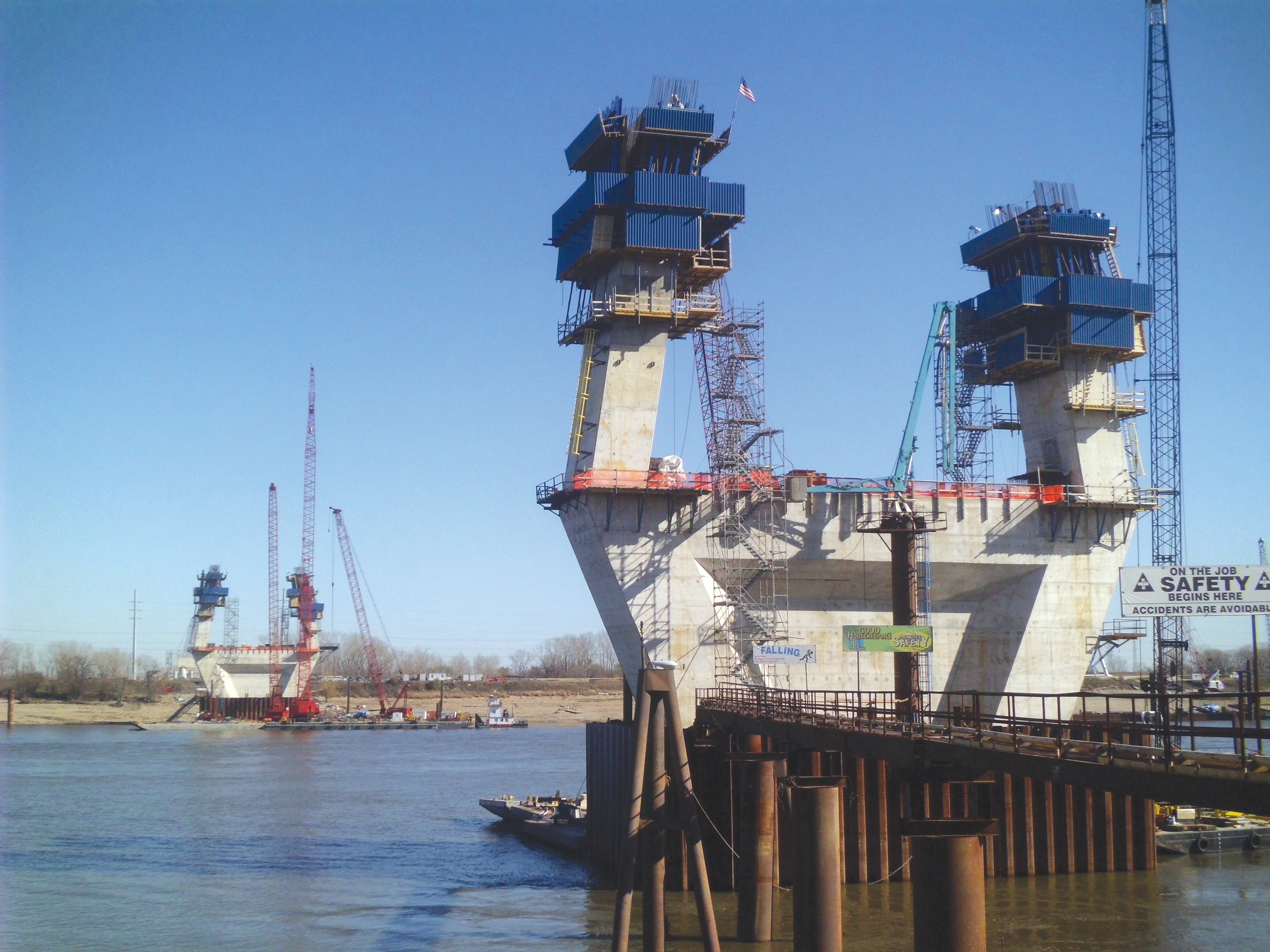
The Mississippi River Bridge is a cable stay bridge construction with two pylons and the tower elevates to 123m above the footing. Photo: Doka
New and highly regarded existing formwork systems have been used in major recent transport-related construction projects across the globe. Guy Woodford looks at some of their applications
The multi-million dollar Mississippi River Bridge project in the United State is creating a vital new gateway between Illinois and Missouri.Central to the project is the realignment and reconstruction of Interstate 70 and a new landmark bridge, featuring two pylons projecting vertically from the Mississippi river bed with 6metre deep footings.
General contractors
“The New Mississippi River Bridge will be a 1,500 foot cable-stayed bridge across the Mississippi River between the
“It will have two lanes in each direction, but will be wide enough to be restriped for three lanes in each direction if traffic volumes warrant and additional funding is secured. There will also be new road approaches on the Illinois and Missouri sides to get traffic to the bridge.”
The Doka D22 dam formwork used on part of the new bridge build comprised seven lifts with gangs fabricated by Doka for nearly every lift. The formwork provided a working platform with what was said to be ample space for labourers to work from, as well as an area to stage equipment. The D22 forms were suspended on climbing shoes that encompass the entire perimeter of both pylons.
Twenty-two lifts utilising automatic climbing systems SKE 100 and SKE 50 were used for all four tower legs. According to Doka, using the automatic climbing systems allows for faster overall completion time as raising the formwork can be done in all weather and wind conditions (up to 40 mph) and enables gangs to lift independent of a tower crane.
To provide an area to pour footings, MTA had to install a coffer dam and pump the Mississippi River water out of it. MTA used Doka’s girder forms to form 26.8metres x 16.8metres x 6.1metres deep footings. All standard girder forms are the same depth, which are said by Doka to greatly reduce or eliminate shimming form joints. The company’s steel girder forms are modular, and can be ganged and picked in large sections. With capabilities to form concrete and support concrete loads on structures such as beams or bridge pier caps, the steel girder form is said to be able to span large distances without any additional support or shoring. The girders for the footings provided MTA with a heavy duty gang system that was said to be easily installed, requiring a minimal number of forms.
Doka’s heavy duty spindle struts and custom channels were said to have given maximum security when hanging forms from the pylon face. There were areas located at the eyebrow where the concrete face projected out at a 35° angle. At lifts five to seven of the lower pylon eyebrow, separate Top 50 gangs had to be assembled for all three lifts at the haunch area.
Two engineers were involved in designing customised support brackets for single sided walls. Doka worked closely with MTA to ensure the brackets did not conflict with the form design.
Both tower legs were converted from a tie to a tieless solution, with Doka designing and installing W16’s walers vertically along the back of the Top 50 gangs. SKE 100 and SKE 50 automatic climbing systems were incorporated for the tower legs, along with Framax Xlife forms for the interior core of all four legs, and Top 50 gangs for the exterior leg face.
To connect gang forms together, MTA used customised steel brackets and splice plates. In addition, a bespoke aluminium pouring platform was incorporated that MTA installed above +1 platform. The +1 platform was said to provide a secure, lightweight surface and allowed labourers to work safely and easily well above gangs while pouring concrete into each wall cell.
A custom protection screen was used on the outside face of Doka’s SKE climbing system as a method to cocoon working platforms, keeping workers safe and comfortable during the harsh weather in the winter months of the bridge lower pylon works. Doka’s SKE climbing systems are said to have offered MTA a method to easily climb all four legs safely, efficiently and independent from using a tower crane, therefore saving the contractor valuable time and money.
According to Doka, the flexibility of its climbing and formwork systems allowed them to easily adapt to bridge geometry and MTA’s requirements.
“The pylon structure presented many challenges for Doka from the foundation monolith, to the solid substructure with a concrete overhand for the roadway as well as the leaning hollow shaft superstructure,” said Monnot.
“Doka USA was the formwork provider with the range of products required for this project.”
Doka’s formwork expertise has also been in demand in the East as well as the West.
Vladivostok in eastern Russia is hosting a summit meeting of the Asia-Pacific Economic Forum (APEC) in September 2012. As a result the region’s infrastructure is being updated, with projects including a four-lane motorway bridge recently built to link a proposed hotel complex and other facilities on Russkiy Island to the mainland. The bridge’s A-shaped suspension tower height of 320metres (20metres taller than the Eiffel Tower’s steel construction) and free span of 1,104 are both new world records.
Responsible for on-time completion of the mainland tower, construction firm Mostovik chose to use a Doka formwork. The decision was said to be taken due to the wealth of experience that Doka had amassed on infrastructure projects across the world over the last 50 years, particularly in building the 306-metre A-shaped suspension towers of Sutong Bridge in eastern China.
On the Vladivostok project, however, the frequent stormy weather and bitter cold in winter months added to more traditional structure geometry challenges faced in formwork planning.
Doka planned a self-climbing formwork solution with 650 m² of made-to-measure Top 50 beam formwork. According to the company their “finely jointed” and “highly adaptable” SKE50 automatic climbing formwork was ideal for inside the tower legs, where space was limited, and SKE100 with its high load-carrying capability was used on the outside walls. At 10tonnes lifting capacity per bracket, it was said by Doka to be perfect for craneless lifting of the beam formwork assemblies and seven different platform levels.
The climbing falsework was anchored to the structure at all times, so craneless, safe lifting of formwork and platforms could proceed in all weathers. Doka said the CIP concrete had to set for four days in the closed formwork before stripping out could commence. To ensure high-quality concrete placement even at extremely low temperatures, the firm enclosed all seven platform levels inside a robust scaffolding tarpaulin and built a roof consisting of seven sections. The workplace was fully enclosed inside this structure and could be heated in winter. When temperatures rose, and when reinforcing bars had to be manoeuvred into position, the individual sections of the roof slid one above the other on rollers.
To ensure smooth progress in all forming tasks, two Doka site foremen and an engineer were said by Mostovik to be on-site at all times, providing round-the-clock advice and assistance for the site crew.
Another impressive road bridge currently under construction is the Waldschloesschen Bridge in the Waldschloesschen area of Elbe Valley in Dresden, eastern Germany.
The road bridge will connect the eastern and southern districts of the city with areas in the north. Peri has planned and is supplying the formwork for the superstructure of the steel composite bridge, and is said to have won over the construction site team with an easy-to-use and, above all, cost-effective solution.
The Waldschloesschen Bridge has a total length of around 635 m. Two steel arches with a span of 148metres sit 26metres above the Elbe and carry the central part of the bridge. The foreshore bridges account for a large part of the structure’s length with V-shaped double piers in place to support the superstructure.
The standard cross-section of the bridge in the arched area has an overall width of around 28metres. A 14-metre wide carriageway has been constructed between the two steel arches consisting of four lanes whilst 4.45metre wide pedestrian and cycle lanes cantilever outwards on both sides of the bridge respectively.
The customised formwork solution for the superstructure was developed by
In order to minimise deformations, a total of 21 casting segments were planned for the carriageway slab and cantilevers. In spite of the geometric changes found in the bridge construction, forming was carried out with only two standard raised formwork units. The length of the units were planned so that that they could be combined in a number of ways for the construction of the sections. The raised formwork units mounted on-site by the
Through the multiple usage of the raised formwork units and the utilisation of the VARIOKIT engineering construction kit, it is said by Peri to be possible to move from one concreting section to the next without the need of any modification work. In addition, the units were said to be relatively light, easy to handle and can be moved quickly and without complications. Such a high degree of material utilisation and easy application were said to have made the formwork solution extremely cost-effective.
The name ‘Waldschloesschen Bridge’ is not only given to the bridge structure, but also refers to a 4.5km long traffic route which leads up to and joins the steel composite construction. The height of the bridge was deliberately planned to be as low as possible in order to ensure an unimpeded view between the Pavillon landmark on the Bautzner Straße and the city centre of Dresden. The bridge will be open to traffic at the end of 2012.
The approach tunnel to the Waldschloesschen Bridge also has a formwork solution based on rentable VARIOKIT system components. Peri says the limited space available meant that a single-sided formwork solution was required for the twin-tube main tunnel, as well as the single-tube secondary tunnel with an arched rectangular cross-section. Walls and slab were constructed in one pour. Horizontal bracing with HD 200 heavy-duty props served to transfer loads during concreting.
“Peri provided us with the most logical approach for the superstructure formwork, specifically tailored to the given bridge geometry,” says Michael Wothe, of Dresden-based Sächsische Bau, who is project manager of the Waldschloesschen Bridge build.
“Already during the tendering phase, the formwork proposals were very detailed. For us, the VARIOKIT raised formwork construction provides the best possible option to suit the local conditions. In addition, it can be adapted to the individual circumstances without any problems whatsoever."
In German neighbouring France, Peri was this month due to unveil its new safety system for building shells at
The PROKIT EP 110 is 1.10m high, quickly mounted temporary protection for open slab edges on building shells. The innovative product prevents site personnel or objects and materials falling off edges, stairs and other areas up to inclination angles of 10%.
Fully compliant with EN 13374 Class A, the PROKIT EP 110 has minimised system parts to ensure swift and easy application: a 2.6m long mesh barrier, one post and assembly feet for slabs or walls. Through the overlapping variations of the mesh barrier, every edge length can be secured while a 1.3metre long side mesh barrier is also available for length compensations. Peri says the small number of system components not only simplifies the assembly process, but also material needs and logistics.
Depending on site specifics, mounting takes place on the slab, laterally on the slab or wall, or on the stair stringer.
If no mounting parts are permitted in the slab and drilling is not allowed, the PROKIT Uniclamp PUC can be used. The clamp is attached by means of a jack nut to the slab or parapet. Subsequently, the self-securing posts are inserted and supplemented by the protective barrier.
A distinctive yellow or red coloured powder coating on the side mesh barrier is said by Peri to guarantee a long service life for the PROKIT EP 110. It also makes the safety barriers more visible from distance, advertising the danger area.
Peri’s new UP MDS shoring is also being made available to all markets outside France after being showcased at Intermat.
The shoring tower is equipped with working platforms hanging from the handrails, providing a high level of security during the erection and dismantling phases, and a significantly reduced exposure to musculoskeletal disorders (MSDs).
The working platform sets an automatic working position 1m below the handrail and follows the top of the tower. The system improves productivity by optimising weight (total weight of the platform is divided by 2, with the heaviest item weighing 16kg) by systemising the erection and the dismantling operations, and by reducing unnecessary movements, bad postures and, as a result, the risk of MSDs.
The optimisation of safety and ergonomics are, according to
Despite the tough global economic climate, Stéphanie Derouet, management assistant at Peri, said that company product sales had gone up since 2010.
“Poland is a booming market and Ukraine is also good, partly because of the need to build new facilities for Euro 2012,” said Derouet.
“We also provide the tunnel formwork for the Panama Canal works. It’s the biggest contact Peri has. Work is being done to make the Canal bigger to allow bigger boats access.”