As engineers write tighter and tighter specifications for grouting, so equipment manufacturers must develop solutions which can help contractors meet those specifications, and prove that they have met them Atlas Copco's new mobile grouting system, Unigrout Smart A, has been designed to do just that: it can mix, pump, monitor, log and control flow and pressure precisely. The control system allows on site mixing of a range of grouts as required by the project.
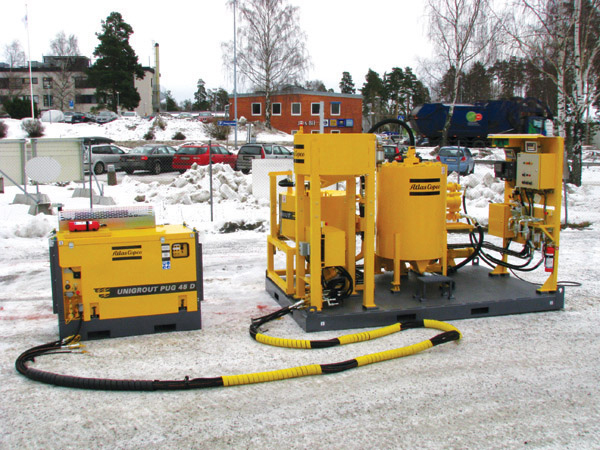
A sophisticated grouting solution is available from Atlas Copco
As engineers write tighter and tighter specifications for grouting, so equipment manufacturers must develop solutions which can help contractors meet those specifications, and prove that they have met them
The control system allows on site mixing of a range of grouts as required by the project.
The quantities of water and cement are weightbatched and delivered to the coilloidal mixer, a type of mixer which uses a high velocity blade to shear or separate grout particles, breaking surface tension and enabling complete contact between the particles and the water. From there it moves to an agitator until it is called for by the pump.
The Unigrout Smart A has a dual-pump system. As well as its established Pumpac piston pump which controls pressure and flow independently it also has the facility to operate with a progressive cavity pump, a type of pump specified by US federal regulations for grouting.
The computerised recording system samples and stores flow, volume, pressure and pumping time from up to four lines at once. The information can then be transferred to a PC for reporting purposes.