Versatility and productivity are key drivers for the concrete plant sector - Mike Woof writes. The days of most construction machines being expressly designed and built for a single specific purpose have gone. These days construction equipment is largely intended to be versatile and adaptable, allowing it to be operated in a wide array of applications and duties. New concrete plants are designed too for mobility as this allows users to set up highly productive equipment quickly on basic sites, with little p
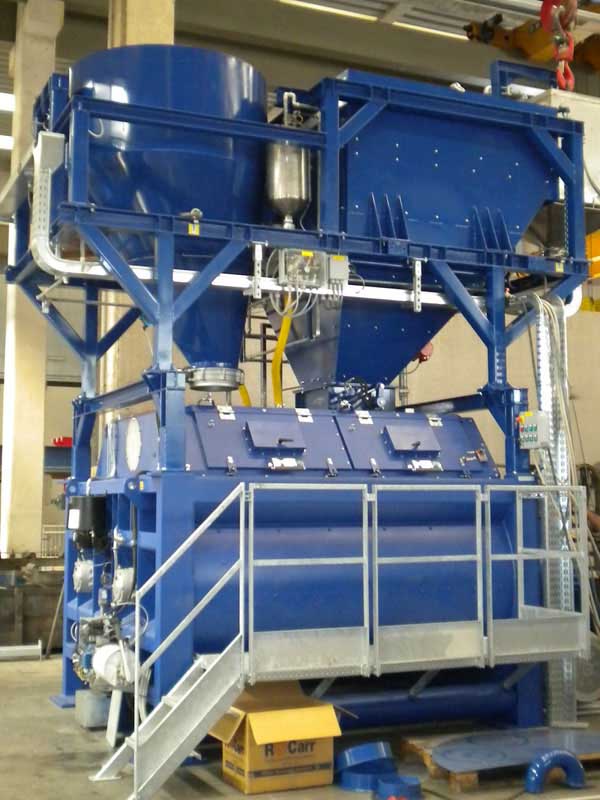
Twin-shaft mixers ensure high productivity according to MCT
Versatility and productivity are key drivers for the concrete plant sector - Mike Woof writes
The days of most construction machines being expressly designed and built for a single specific purpose have gone. These days construction equipment is largely intended to be versatile and adaptable, allowing it to be operated in a wide array of applications and duties. New concrete plants are designed too for mobility as this allows users to set up highly productive equipment quickly on basic sites, with little prior preparation being required.
The concrete plant sector has a number of key players and as in other machine categories, mobility is a recurring theme amongst newer designs. Allowing plants to be moved from site to site and commissioned faster means that users can increase uptime, while advances in control systems offer superior product quality.
Swiss firm6791 Ammann has been investing in the Elba concrete equipment division, since it acquired the business, widening the range and developing new models. Lieven van Broekhoven, executive vice president sales and marketing commented, “We have fully integrated Elba into the Ammann Group and will be offering the existing and new line of concrete plants through the Ammann channels to our customers globally. The Elba distribution channels have been integrated into the Ammann distribution channels where it made sense. Our approach with the concrete plants will be a global one. We introduced new models at bauma 2016 and will continue to develop new plants to meet the global market requirements leveraging our existing manufacturing footprints."
A key addition to the line-up is the CBS Elba Concrete Mixing Plant, which the firm says is designed to be used in small and medium-sized operations. The CBS has been developed to meet the needs of customers looking for versatile concrete plant solutions and the unit features advanced controls, with output ranging from 105-160m³/hour.
The basic unit is designed to be fitted with either the firm’s EMS single-shaft or EMDW twin-shaft mixers, allowing concrete outputs ranging from 2-3.5m³ depending on the specification. The firm says that the CBS Elba is designed to be easy and comparably inexpensive to transport from site to site and can suit either stationary or semi-mobile operation.
Also being introduced by Ammann Elba is a new range of mobile and compact concrete-mixing plants. The CBT 60 Elba Compact Concrete Mixing Plant is the first of this new range, offering an output of 58m³/hour. And when the CBT range is complete it will offer capacities from 30-130m³/hour, with the models sharing key features and a similar modular design concept.
A central feature of the new CBT 60 is its Elba EMS 1000 single-shaft mixer, while the unit also has an integrated linear batcher and can be equipped as standard with either two or four aggregate components. The firm has designed this plant for fast installation as this maximises profitability for the user. A sophisticated design allows the major components to be unfolded onsite, lowering set up time and simplifying the commissioning process. As with other mobile plants from Ammann Group, this new Elba concrete plant is designed without a need for fixed foundations, so that it can be set up on sites with a minimum of ground preparation required beforehand.
CEI Enterprises, part of the1250 Astec Group, has been continuing to develop its range of sophisticated concrete plants. The latest models are said to offer the benefits of high throughput combined with high-quality output. Sophisticated controls help deliver mix specifications to close tolerances. The plants are designed to deliver long working life and low maintenance needs, along with ease of servicing.
The new batch plant the firm is bringing to market is called the Fusion Hybrid-Process Ready Mix Plant. The name Fusion is derived from the fact that the plant uses precision aggregate blending technology from the asphalt industry, combined with conventional cement and water metering systems. By providing a more precisely-blended aggregate mix than in older generation concrete batch mixers, the voids are reduced. With fewer voids to fill with cement and water, then cement consumption is also lowered. The firm says that the Fusion plant will allow producers to make better concrete, with less cement, than with older equipment. The company is currently building a Fusion plant that it will use for demonstration purposes at its manufacturing facility in Albuquerque, New Mexico.
Turkish firm Çesan has developed its CBS range of concrete plants, which offer outputs of 60–240m3/hour. The company claims this range of plants benefits from a long working life and high performance, as well as the ability to meet an array of concrete specifications. Highly efficient in operation according to the firm, the plants are also said to offer low running costs and can cope with heavy-duty applications due to its rugged design and construction. Long life is claimed for key components and the plant is said to have durable mixer wear plates that can cope with abrasive materials, while they are also said to be easy to replace when necessary.
A key feature of the CBS range is the modular design that allows ease of transport, which reduces the cost of moving the plant from one site to another and also minimises the time needed for set up.
718 Liebherr continues to develop its concrete equipment range, with the latest Mobilmix 2.5 concrete mixing plant offering high mobility, versatility and ease of transport. At the centre of the plant is its new twin shaft mixer, which is said to offer an output that compares with a stationary mixing plant. The new Mobilmix 2.5 replaces the earlier Mobilmix 2.25 model, with a key feature being the increase in output from 100m³/hour to 110m³/hour.
As with the earlier design, the new plant is designed for fast set up although this has been further optimised and the system can now be made ready to work within two days of arriving on site. Key updates for the new and more productive version of the Mobilmix concept include shorter cleaning times and reduced wear rates for major components, as well as a lowered mixer platform.
The new design benefits from a slight slope to the discharge hopper, which the firm claims simplifies cleaning operations, while a keyless security system on the mixer access hatch also optimises access for cleaning. Better access to the mixer system is claimed while the plant now has a feed flap on its skip as well as its dust filter systems. These last features are said to provide high protection against dust around the mixer platform. The skip also now benefits from parallel running surfaces and plastic rollers that are said to help lower wear and tear, while the uses of galvanised assemblies and high quality components further boosts durability.
The main components are mounted on a platform which can be transported as a single unit on a flatbed truck, including the container housing the control system integrated into the module. During set up the base unit with the mixer system, weighing system and skip can be lifted off with a crane, unfolded and bolted in working position. The control cabin is equipped with the firm’s sophisticated Litronic-MPS microprocessor control system. Meanwhile two additional transportation units include the in-line silo and the unit with dosing valves and weighing belt. Up to 140m³ of aggregates can be stored in four or six chambers in the in-line silo. The chamber is 3.5m wide allowing feeding with a wheeled loader.
The new generation twin-shaft mixer has been completely reworked, while the electric motors, gears, hydraulics, mixer gate, central lubrication and high pressure cleaning system are placed close together for easy overview.
The Italian8015 Marcantonini Concrete Technology (MCT) Group says that its batch plants are highly sophisticated and are customised to suit the customer’s specific requirements. The plants are also configured specially to suit weather and climate where the unit will be operating. The firm says that the layout of the plant can be optimised according to the client’s needs and the constraints of the site so as to ensure that the operation will be efficient. This includes making sure that the truck traffic will not be subject to jams and that flow of raw materials through the facility is also efficient.
MCT says that it equips its latest plants with wet batch technology, fitting twin shaft mixers. This batching design is combined with MCT’s Compumat software technology, which the firm claims allows the plant to handle multiple batches simultaneously. The advanced double batch technology helps to reduce the size of the mixers and the scales, while special holding hoppers are fitted to handle the aggregates and concrete. These hoppers are mounted on load cells that measure the weights, freeing the scales and mixers for the next batch.
The 4.3m3 twin-shaft mixer plant has a high output, proving sufficient to fill an 8.6m3 capacity truck mixer in less than four minutes. The firm says that each plant comes with a broad range of features including an aggregates dosing system with valves that optimise flow control and accuracy against dosing time, as well as accurate aggregates weighing and conveying technology. Mounting the aggregates holding hopper on load cells is said to further boost dosing accuracy while the concrete holding hopper is also mounted on load cells and has a hydraulic discharge gate to free the mixer for the next batch, while optimising truck loading. In addition, control systems tackle factors such as ambient humidity to ensure consistency while emissions control systems help minimise dust and improve efficiency.
Customised solutions are available for reclaiming waste, including separation screws with trough and receivers for returning concrete as well as filter-press units and other downstream treatments.
All production data is logged in software reports, allowing concrete producers to replicate the same concrete mix if required. Meanwhile technicians at MCT’s facility in Italy constantly monitor the operating performance of customer plants.
Italian firm2595 SIMEM has broadened its product range with the introduction of the new BISON concrete plant and Rhyno mixer. The BISON is a new continuous mixing plant can be used for an array of duties such as for supplying road base material, for supplying RCC applications and for soil treatment. Both versatile and mobile, the firm claims that the BISON plant combines a large output capacity with the capability to produce material to a very high specification accuracy. Because the plant is trailer-mounted, it is highly mobile and can be moved quickly from site to site, while commissioning the site is also said to be short. As this plant offers both high output and high-quality materials, it can be used in large highway jobs or for airport runway applications also.
The firm says that the plant is versatile and can be fitted with a range of extra features as options. A trailer-mounted control cabin and service container are available, as is additional aggregates storage, a 40m3 capacity dosing trailer and a trailer-mounted cement silo with a capacity of 55m3.
Meanwhile SIMEM’s new Rhyno twin-shaft mixer is said to be around 7% more efficient with power consumption than earlier generation machines, due to its direct-drive motor and gears. The new Rhino replaces the earlier MSO mixer from the firm and incorporates SIMEM’s flower paddle design, which is said to deliver improved mixing capabilities, such as increased dispersion of cement. The Rhyno is offered in sizes from 1-9m3 capacity. Output is suitable for standard WET and SCC concrete, RCC concrete and MCC concrete and the Rhyno also has a highly efficient auto washing system, according to the firm.
The days of most construction machines being expressly designed and built for a single specific purpose have gone. These days construction equipment is largely intended to be versatile and adaptable, allowing it to be operated in a wide array of applications and duties. New concrete plants are designed too for mobility as this allows users to set up highly productive equipment quickly on basic sites, with little prior preparation being required.
The concrete plant sector has a number of key players and as in other machine categories, mobility is a recurring theme amongst newer designs. Allowing plants to be moved from site to site and commissioned faster means that users can increase uptime, while advances in control systems offer superior product quality.
Swiss firm
A key addition to the line-up is the CBS Elba Concrete Mixing Plant, which the firm says is designed to be used in small and medium-sized operations. The CBS has been developed to meet the needs of customers looking for versatile concrete plant solutions and the unit features advanced controls, with output ranging from 105-160m³/hour.
The basic unit is designed to be fitted with either the firm’s EMS single-shaft or EMDW twin-shaft mixers, allowing concrete outputs ranging from 2-3.5m³ depending on the specification. The firm says that the CBS Elba is designed to be easy and comparably inexpensive to transport from site to site and can suit either stationary or semi-mobile operation.
Also being introduced by Ammann Elba is a new range of mobile and compact concrete-mixing plants. The CBT 60 Elba Compact Concrete Mixing Plant is the first of this new range, offering an output of 58m³/hour. And when the CBT range is complete it will offer capacities from 30-130m³/hour, with the models sharing key features and a similar modular design concept.
A central feature of the new CBT 60 is its Elba EMS 1000 single-shaft mixer, while the unit also has an integrated linear batcher and can be equipped as standard with either two or four aggregate components. The firm has designed this plant for fast installation as this maximises profitability for the user. A sophisticated design allows the major components to be unfolded onsite, lowering set up time and simplifying the commissioning process. As with other mobile plants from Ammann Group, this new Elba concrete plant is designed without a need for fixed foundations, so that it can be set up on sites with a minimum of ground preparation required beforehand.
CEI Enterprises, part of the
The new batch plant the firm is bringing to market is called the Fusion Hybrid-Process Ready Mix Plant. The name Fusion is derived from the fact that the plant uses precision aggregate blending technology from the asphalt industry, combined with conventional cement and water metering systems. By providing a more precisely-blended aggregate mix than in older generation concrete batch mixers, the voids are reduced. With fewer voids to fill with cement and water, then cement consumption is also lowered. The firm says that the Fusion plant will allow producers to make better concrete, with less cement, than with older equipment. The company is currently building a Fusion plant that it will use for demonstration purposes at its manufacturing facility in Albuquerque, New Mexico.
Turkish firm Çesan has developed its CBS range of concrete plants, which offer outputs of 60–240m3/hour. The company claims this range of plants benefits from a long working life and high performance, as well as the ability to meet an array of concrete specifications. Highly efficient in operation according to the firm, the plants are also said to offer low running costs and can cope with heavy-duty applications due to its rugged design and construction. Long life is claimed for key components and the plant is said to have durable mixer wear plates that can cope with abrasive materials, while they are also said to be easy to replace when necessary.
A key feature of the CBS range is the modular design that allows ease of transport, which reduces the cost of moving the plant from one site to another and also minimises the time needed for set up.
As with the earlier design, the new plant is designed for fast set up although this has been further optimised and the system can now be made ready to work within two days of arriving on site. Key updates for the new and more productive version of the Mobilmix concept include shorter cleaning times and reduced wear rates for major components, as well as a lowered mixer platform.
The new design benefits from a slight slope to the discharge hopper, which the firm claims simplifies cleaning operations, while a keyless security system on the mixer access hatch also optimises access for cleaning. Better access to the mixer system is claimed while the plant now has a feed flap on its skip as well as its dust filter systems. These last features are said to provide high protection against dust around the mixer platform. The skip also now benefits from parallel running surfaces and plastic rollers that are said to help lower wear and tear, while the uses of galvanised assemblies and high quality components further boosts durability.
The main components are mounted on a platform which can be transported as a single unit on a flatbed truck, including the container housing the control system integrated into the module. During set up the base unit with the mixer system, weighing system and skip can be lifted off with a crane, unfolded and bolted in working position. The control cabin is equipped with the firm’s sophisticated Litronic-MPS microprocessor control system. Meanwhile two additional transportation units include the in-line silo and the unit with dosing valves and weighing belt. Up to 140m³ of aggregates can be stored in four or six chambers in the in-line silo. The chamber is 3.5m wide allowing feeding with a wheeled loader.
The new generation twin-shaft mixer has been completely reworked, while the electric motors, gears, hydraulics, mixer gate, central lubrication and high pressure cleaning system are placed close together for easy overview.
The Italian
MCT says that it equips its latest plants with wet batch technology, fitting twin shaft mixers. This batching design is combined with MCT’s Compumat software technology, which the firm claims allows the plant to handle multiple batches simultaneously. The advanced double batch technology helps to reduce the size of the mixers and the scales, while special holding hoppers are fitted to handle the aggregates and concrete. These hoppers are mounted on load cells that measure the weights, freeing the scales and mixers for the next batch.
The 4.3m3 twin-shaft mixer plant has a high output, proving sufficient to fill an 8.6m3 capacity truck mixer in less than four minutes. The firm says that each plant comes with a broad range of features including an aggregates dosing system with valves that optimise flow control and accuracy against dosing time, as well as accurate aggregates weighing and conveying technology. Mounting the aggregates holding hopper on load cells is said to further boost dosing accuracy while the concrete holding hopper is also mounted on load cells and has a hydraulic discharge gate to free the mixer for the next batch, while optimising truck loading. In addition, control systems tackle factors such as ambient humidity to ensure consistency while emissions control systems help minimise dust and improve efficiency.
Customised solutions are available for reclaiming waste, including separation screws with trough and receivers for returning concrete as well as filter-press units and other downstream treatments.
All production data is logged in software reports, allowing concrete producers to replicate the same concrete mix if required. Meanwhile technicians at MCT’s facility in Italy constantly monitor the operating performance of customer plants.
Italian firm
The firm says that the plant is versatile and can be fitted with a range of extra features as options. A trailer-mounted control cabin and service container are available, as is additional aggregates storage, a 40m3 capacity dosing trailer and a trailer-mounted cement silo with a capacity of 55m3.
Meanwhile SIMEM’s new Rhyno twin-shaft mixer is said to be around 7% more efficient with power consumption than earlier generation machines, due to its direct-drive motor and gears. The new Rhino replaces the earlier MSO mixer from the firm and incorporates SIMEM’s flower paddle design, which is said to deliver improved mixing capabilities, such as increased dispersion of cement. The Rhyno is offered in sizes from 1-9m3 capacity. Output is suitable for standard WET and SCC concrete, RCC concrete and MCC concrete and the Rhyno also has a highly efficient auto washing system, according to the firm.