Sandvik Construction’s compact QS331 has been designed to accept large feed sizes and achieve high production capacities. Sandvik says this boosts productivity on applications such as Type 1, crusher run or in primary gravel crushing.
For more than 30 years, the “S” type gyratory cone crusher has proven itself in stationary applications. The technology has now been incorporated into a self-contained, diesel driven track-mounted plant.
The “S” type gyratory cone accepts a feed size up to 90% larger tha
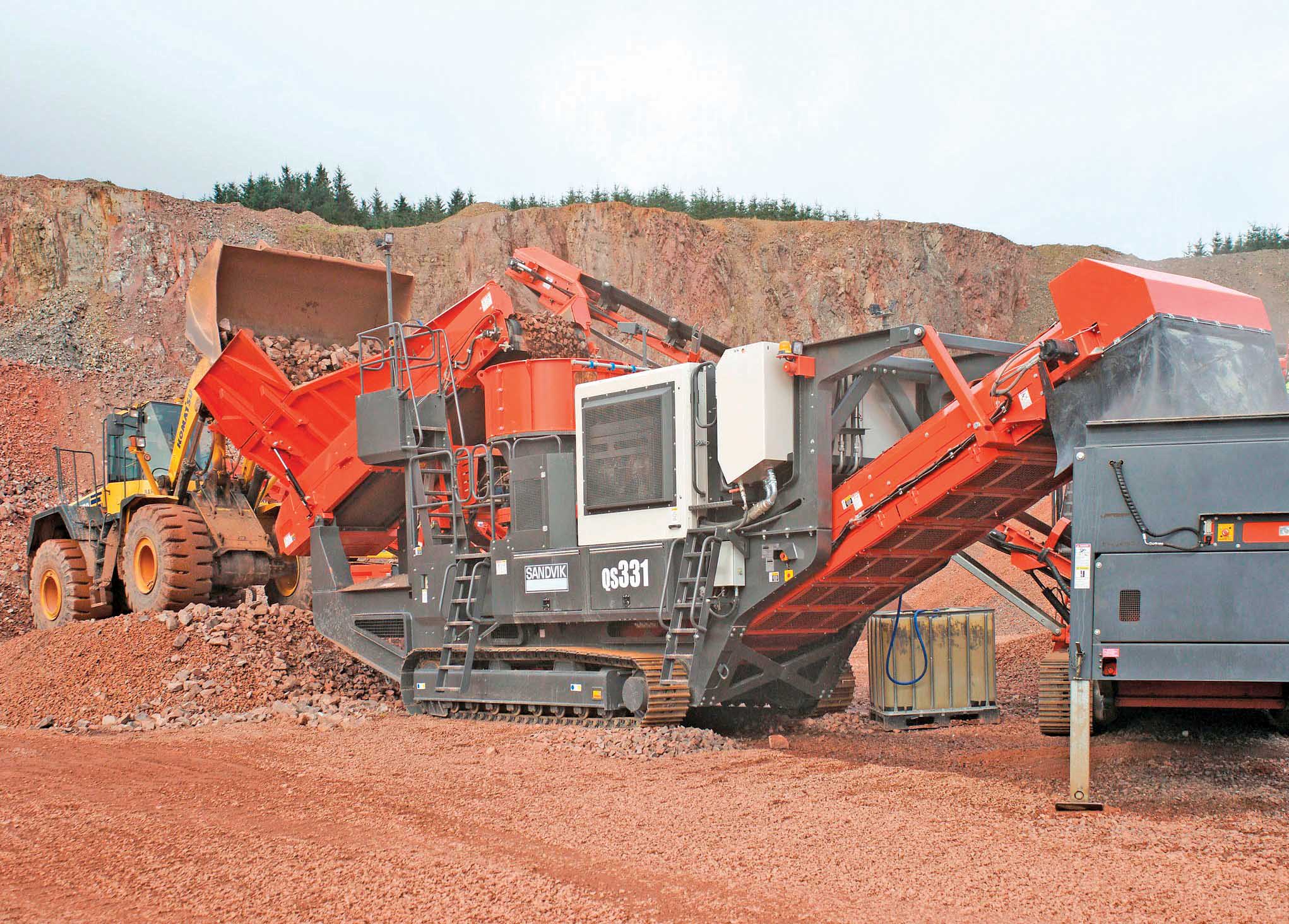
Sandvik’s new crusher offers high output
For more than 30 years, the “S” type gyratory cone crusher has proven itself in stationary applications. The technology has now been incorporated into a self-contained, diesel driven track-mounted plant.
The “S” type gyratory cone accepts a feed size up to 90% larger than standard cones to enable maximum productivity from a primary crusher. It even facilitates the use of the “S” cone as a primary crusher itself on gravel applications.
The 36tonne Mobile QS331 has a choice of three concaves and four bush settings to control the closed side settings and material gradation. Due to the large feed acceptance, jaw crusher production may be optimised by opening the CSS to reduce fuel consumption and wear. The unit is a Type 1 solution provider but is also equally suited for crusher run (6F5 material) or railway ballast/drainage stone.
Key features include an automatic level sensor above the crushing chamber to control the feed rate and minimise operator intervention for maximum production and reduction. A metal detector fitted as standard provides maximum stability and protection from tramp material. There is also a remote camera for visibility of the crushing chamber from ground level.
A Hydroset CSS regulation system optimises production and keeps track of liner wear. The heavy-duty “I” beam chassis ensures maximum durability while power comes from a CAT C9 or C9.3 diesel engine with direct drive.
A hydraulically driven cooling fan with auto reverse function can back flush dust from the radiator. An optional hanging screen is available for recirculation or stockpiling to produce two products.