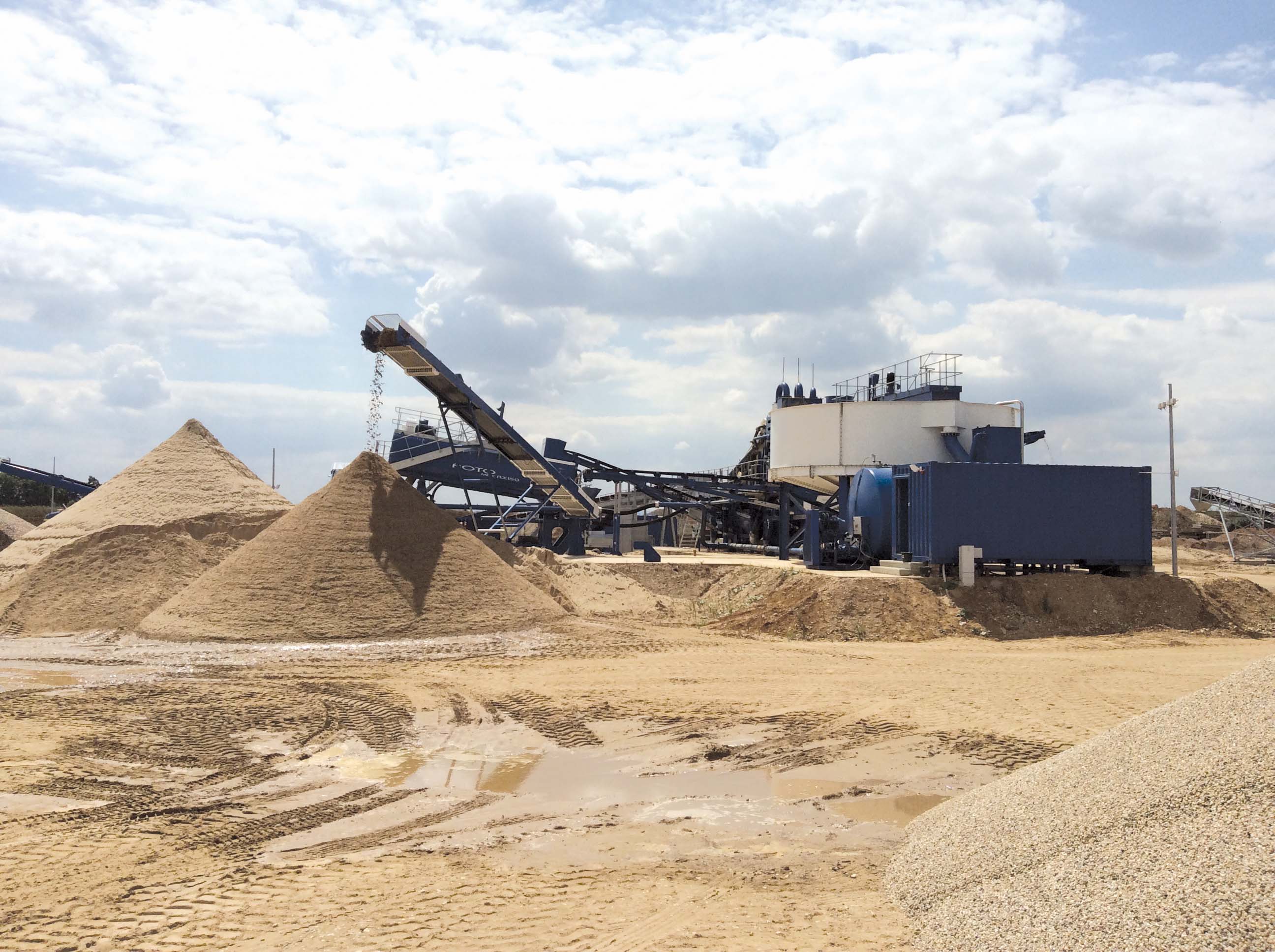
A wide array of crushing, screening and materials handling technologies have been introduced in recent months - Mike Woof writes
The manufacturers of crushing and screening products have been developing an array of new systems to optimise production. The recent Hillhead show in the UK was the launch point for a number of these new products, although firms from all over the world have also been developing new designs. Productivity and wear life are two performance factors seeing major benefits from innovation, while downtime costs are being reduced.
Key features include a novel laminate side-wall design on the ProGrade P2-75/R screen, which is said to be stronger and lighter screen and requires less power. Galvanised as standard, the lattice design screen has a reduced mass and is said to ensure more energy is transferred to the material for more efficient screening. The ProGrade P2-75/R screen is said to be an integral part of the CDE range, featured on the R2500, M2500 and M4500. All FEA results are verified with onsite physical testing procedures. Physical tests have also been carried out on the R2500 within the dedicated ProGrade screen testing facility at CDE.
For handling material the new feeder stackers from McCloskey are said to be more versatile and to increase productivity. The TF80 and WF80 models can be adjusted quickly from 0°-29° and are said to be mobile and easy to transport. The units can improve materials handling and stockpiling duties and can operate flat at 0°, for lower stockpiles, while providing controlled flow of material output without blockages, bottlenecking or bridging. The wheeled version, the WF80, features a radial axle, and a pivot point that allows the hopper to remain stationary while in operation. Meanwhile the tracked TF80 is powered by a 75kW diesel and is said to offer high mobility on site as well as hydraulic folding for fast setup times. In addition to the high capacity feed hopper (up to 17.3m3), the 2014 models feature a 1.2m wide, heavy duty 24.4 long conveyer and a 1.2m wide heavy duty feeder.
Modular design helps to lower parts costs as the same components are used across the Prisec 3 HSI range. Downtime is also said to be lower than for other units. With these machines the user can now replace crushing chamber components in just 15 minutes, compared with two hours for previous generation models. Rowan Dallimore is product manager for impact crushers at the firm and explained, “We can change the crushing chamber to suit the products.”
The design of the crushing chamber is said to offer efficient reduction ratios and the machines have infinite hydraulic curtain adjustment as well as a system that prevents damage should any uncrushable materials enter the crushing circuit. The design of the rotors and hammers are said to optimise performance due to high inertia, with a self-sharpening hammer design said to deliver effective shearing of incoming material. A safety interlock prevents accidental opening of the crusher while it is operating.
The design also allows the curtains to be raised, without stopping the crusher to clear blockages.
The CI531 can handle input material up to 1m across, features a throughput range of 400-700tonnes/hour and weighs in at 27.75 tonnes while the CI532 can handle feed material up to 350mm in size, has a throughput range of 250-400tonnes/hour and weighs 29.65tonnes.
And fitted with the firm’s CS430 S Type gyratory cone crusher, the QS331 is a compact, mobile secondary cone crusher. The QS331 is said to be able to produce a high quality output and has a feed opening almost twice as big as with conventional cone crushers and can handle feed sizes of up to 360mm. A spokesperson said, “You’re getting into jaw crusher territory there. Due to the configuration of the chamber it minimises fines.”
Equipped with a hydroset CSS regulation system to optimise production and keep track of liner wear, the unit also has an automatic level sensor above the crushing chamber to control feed rate and minimise operator intervention for maximum production and reduction.
In addition, the firm has also unveiled its 5011 breaker, which is designed along similar lines to the 3288 and 4099 models. All three breakers now feature a novel operating principle that allows the units to be purpose-matched to specific applications, boosting productivity and usability.
Suitable for excavators that weigh from 43-80tonnes, the 4.75tonne 5011 breaker slots neatly into the
The flexible operating principle features a variable stroke concept. The long stroke setting has a low blow frequency for use in hard materials, such as granite and reinforced concrete foundations, while the short stroke setting offers a high blow frequency for use in softer materials, such as limestone.
Meanwhile the idle blow protector selector means that the working mode can be adjusted to provide protection against blank firing. Long working life is claimed and the breaker can be fitted with the firm’s Ramlube I or Ramlube II greasing systems for additional tool wear life and reduced maintenance.
From
The HT152R is capable of processing lump sizes up to 600mm at a rate of up to 300tonnes/hour and barrel apertures are available up to 300mm. The barrel assembly has two separate sections, which are bolted together and can produce two different product sizes as well as exiting oversized material at the end of the barrel. The barrel apertures are designed and built to suit specific requirements and will process a wide range of different materials. The heavy duty feed hopper has a capacity of 5.2m3 and can be fed from the rear or the side by an excavator or wheeled loader.
The feed material falls on to the feeder table where the reciprocating feeder action pushes the material inside the barrel at a regulated rate.
Barrel rotation speed can be adjusted to suit different feed materials as well as changing weather conditions or site location. Processed material is collected from underneath the unit while the oversize material is collected from the end of the trommel.
From
This modular product line consists of several predesigned static and semi-static crushing and screening modules.
Set-up time and ease of operation is aided by the simplicity of the modular product range. Modules are designed to fit and work together interchangeably. All Terex MPS modules bolt together on site and require minimal on-site wiring.
From sister firm
Its modular design as well as its serviceability and functionality are said to help make it it quick and easy to set-up and easy to maintain. The plant also includes a novel web frame chassis design that is easily assembled and supports the scrubbing hull, the trash dewatering screen, the two deck rinsing and sizing screen and integrated sump and pump.
The Aggresand 206 wash plant is the larger model of the AggreSand 165 model and provides greater capacity of up to 400tones/hour. It offers modular design and can increase productivity, while sharing the novel features of the AggreSand 165 wash plant. Full containerisation means ease of transportation and rapid set-up times due to the pre-wired and pre-plumbed componentry. It also has isolated spray bars and an HMI control system, giving efficient and productive performance.
Other features include rolling chutes and rolling centrifugal pumps, as well as sensors throughout the machine providing the operator with information on water pressure; cyclone feed pressure and electrical power consumption.