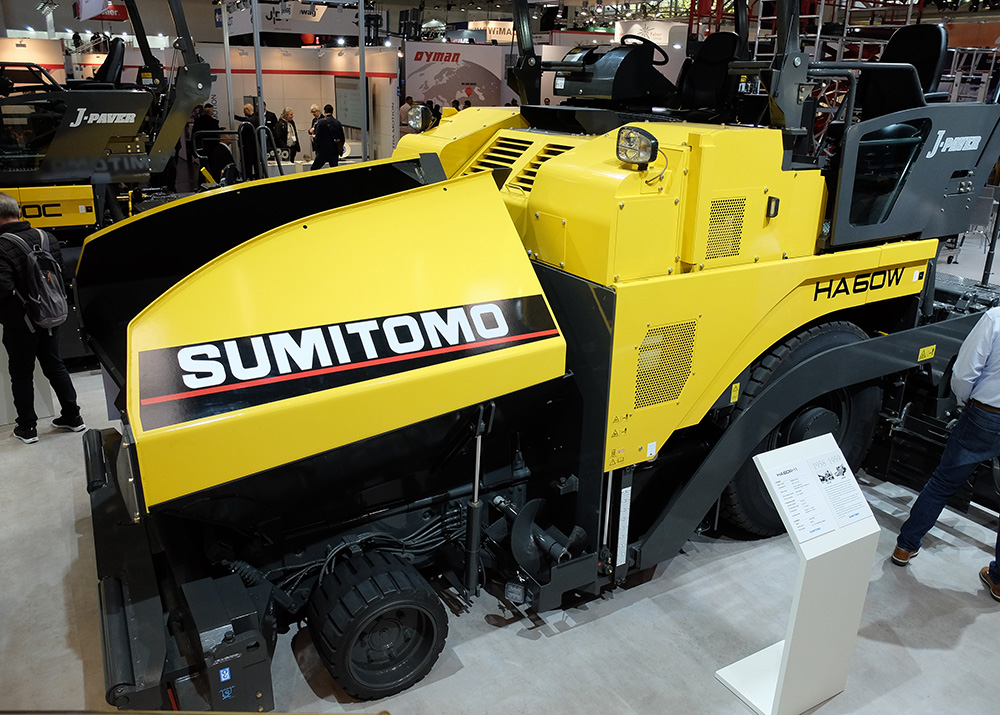
According to the firm, the machines are easy and comfortable to operate. Improved features include low noise and exhaust emissions as well as ease of maintenance. High performance and low running costs are also key features with both variants competing in the 16tonne class.
Power for the HA60 machines comes from a Yanmar diesel rated at 110kW, an increase from the 92kW of the Isuzu engine in the previous generation machines, giving extra power for paving tight curves with a full screed. The machines also benefit from sophisticated technology developed by Sumitomo, ensuring high work efficiency and low fuel consumption, while meeting the Stage V emissions standards due to the use of a selective catalytic reduction (SCR) system.
The improved heating system now features flat-type heating plates. “We modified the design of the heating elements to increase efficiency,” said a spokesperson for the firm. "Before, we used a round-type, but now we use a flat-type heating element and you get more contact with the ground.” Heating times are also said to be around 50% quicker than before due to the new elements. In addition, the heating generator has been changed from a belt drive to a direct motor drive, eliminating the need for daily belt adjustments.
Sumitomo’s innovative STV compaction system (strike-off, tamper, vibration) is said to ensure a high-quality, smooth surface. An automatic tamper speed setting function is now available on the DASH 11 generation machines. The machine retains the proven novel screed design, which features overlapping hydraulic cylinders and allows wider extension than other machines in its size class. However, the firm says that the rigidity of the screed has been increased to make it stiffer and further boost paving quality. Both the wheeled and tracked variants offer screed widths from 2.3-6m using the hydraulic extension, although bolt on extensions can be used if a wider setting is required.
The wheeled model now has a slightly shorter hopper than before, which helps manoeuvrability in tight locations. This feature also allows the machine to be loaded on a truck along with a small twin drum roller for eases of transport, increasing its appeal for use in urban road repairs from small contractors. Hopper capacity for the wheeled machine is only slightly reduced at 12tonnes, compared with 13tonnes for the tracked model.
Crew comfort levels have been improved and the new FRP canopy is raised and lowered hydraulically, while there are also side windshields to provide operator protection in bad weather, as well as LED lighting for night working. Site safety is improved due to the installation of a field view monitor (FVM) package that allows the operator to see around the machine. A new differential lock option helps to ensure traction when working on soft ground while the brake steer system that was an option on the previous wheeled model is now a standard feature.