Bergkamp has launched the M1E self-propelled continuous slurry seal and micro surfacing paver. The machine has two main advantages over older versions, said the manufacturer: it is easier to operate and has electronic mix control and diagnostics.
“It is much simpler to operate than the old-style machine,” said Bergkamp general manager Bill Cooper. “The operator can pick it up much quicker which means that if you lose an operator you can get a new one up to speed faster.”
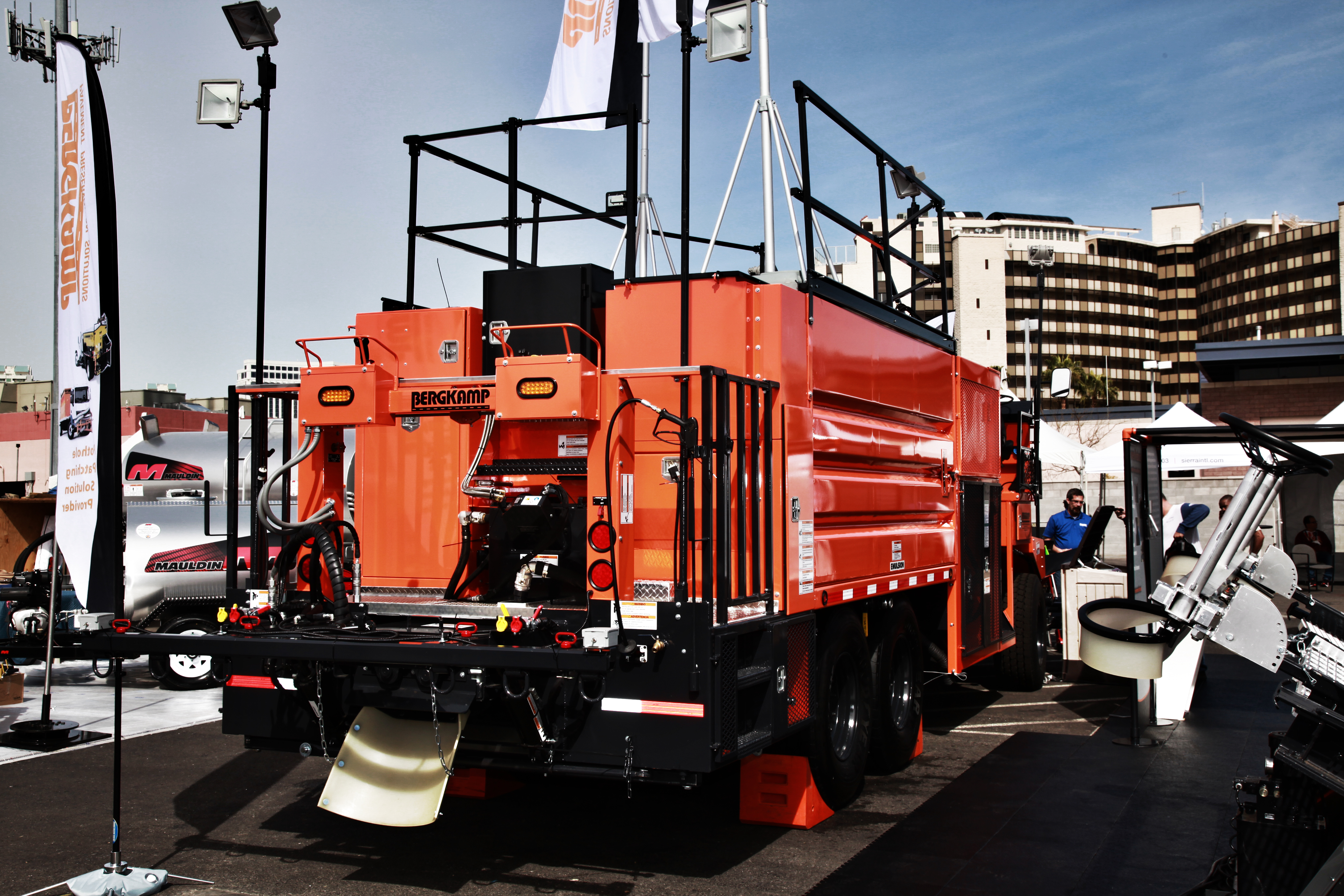
Bergkamp’s M1E is easy to operate and has self-diagnostics
“It is much simpler to operate than the old-style machine,” said Bergkamp general manager Bill Cooper. “The operator can pick it up much quicker which means that if you lose an operator you can get a new one up to speed faster.”
Aggregate, asphalt emulsion, mineral fillers, additives and water are fed into the machine and the control system then adds the correct proportions according to the mix design. A pugmill with two shafts and 36 paddles then mixes the components together. Once combined, the mix is delivered into a spreader box attached to the back of the machine.
The self-diagnosing control system picks up on problems and displays a simple error code, reducing troubleshooting and repair time, said Bergkamp. The manufacturer has replaced all major component clutches, chains and sprockets on the standard M1 with direct-drive hydraulics to work with the electronic control system.
The electronic system also makes calibration simpler and much quicker, according to Rusty Price, general manager of Intermountain Slurry Seal in Utah which owns an M1E, “This machine has cut our calibration time in half,” he said. “And with this technology’s computerised monitoring system, we know the percentage of each mix ingredient that goes onto the roadway at all times. At any time during or after the job, we can request a print out of the system to determine whether the crew is meeting the required specifications.”
The M1E reduces the number of construction joints because the supply of material is constant. Cooper said that he expects that it will used primarily for micro surfacing.
%$Linker: