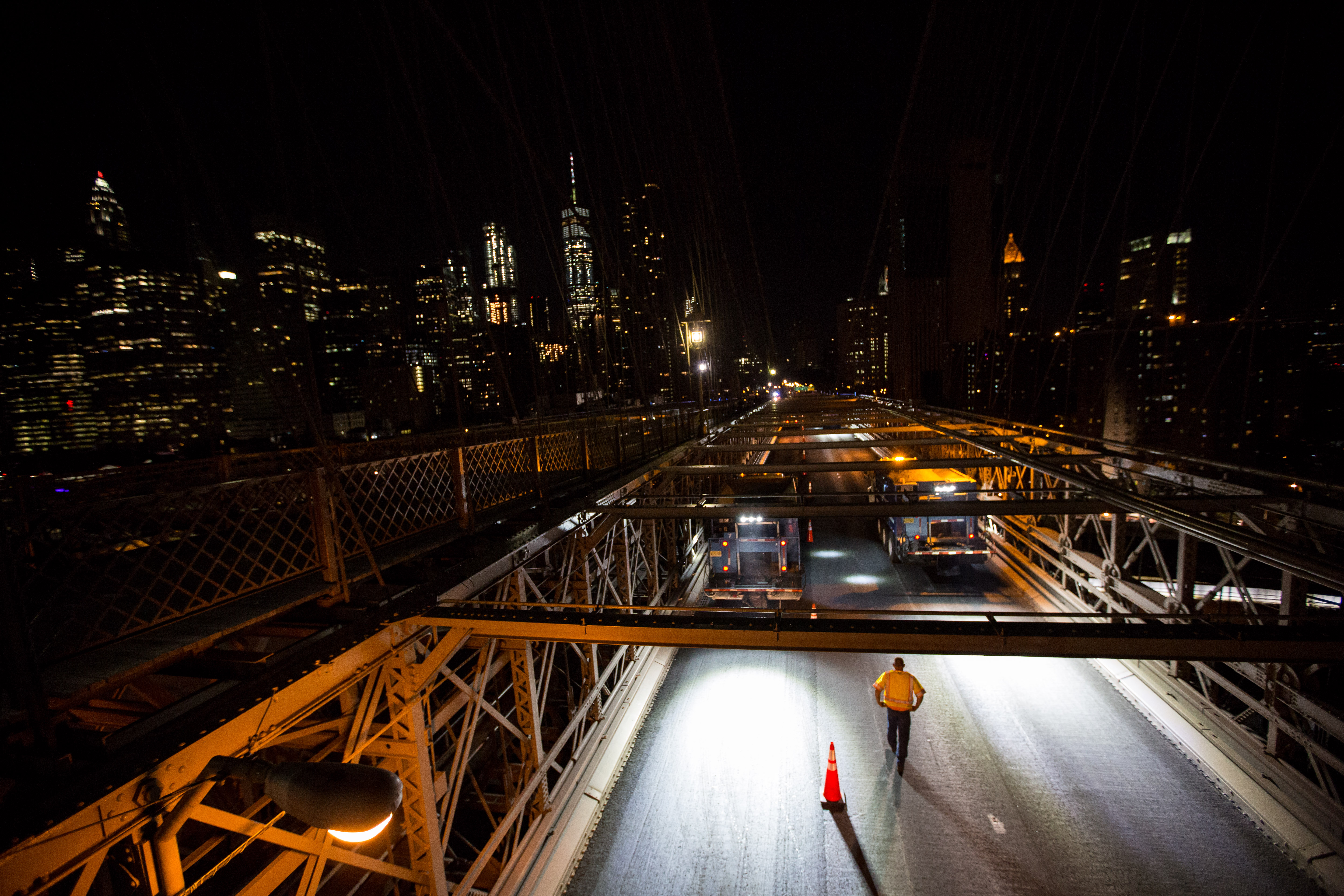
It was the third time in Ken Messina’s career that he would provide micro surfacing for the iconic Brooklyn Bridge, built in 1883. Messina, as president of New Jersey-based Asphalt Paving Systems (APS), knew only too well the challenges that lay ahead.
And there were many.
There would be only a brief window of opportunity for paving, with lane closures starting at 10pm and ending at 5am. The cool, humid atmosphere would affect scheduling. There would have to be a tricky Type 3 mix and double micro surfacing lifts of 28 pounds (15.2kg/m²) each. The opportunity for complications was far greater than with a typical micro surfacing job.
Fortunately, APS’s skilled workforce has extensive knowledge of
The M210 has a full-width working platform that allows operators to easily see both sides of the unit, the spreader box and the material being placed. In addition, a remote side-shift control lets the spreader box operator control the box from the ground.
The Brooklyn Bridge’s deck is a metal grid filled with concrete and then surfaced with asphalt. Because of weight restrictions, the deck requires milling and micro surfacing on average every eight years to maintain surface condition. It sees an average daily traffic count of around 150,000 vehicles which makes paving a night time occupation.
“The span we covered included three lanes in each direction and it is about 3,500 feet [1,067m] across,” Messina explains. “As the bridge was paved with a double lift, this translates to around eight lane-miles of paving over six nights.”
Prior to laying down the new surface, all the bridge lanes were manually stripped of old micro surfacing. They were then shot blasted to remove all the old asphalt creating a clean surface onto which the new micro surfacing would adhere. Any repairs required to the bridge deck then took place. “At that point, the bridge was pretty much our baby for the rest of the project,” Messina says.
Type 3 mix
With the extreme traffic count for this bridge and the fact that it is a standalone surface, the contractor APS paved with a Type 3 mix design, in lieu of Type 2. “Type 3 has a coarser aggregate with some larger stone in it. Not all of the aggregates lend themselves well to a micro surfacing with Type 3, which can create some complications with the mix designs.”
“Also, it’s the Brooklyn Bridge, so you’re over the river. You’ve got the humidity. You’ve got cooler temperatures. You’ve got the bridge moving pretty much the entire time you’re on it because traffic is still using one lane in either direction depending on where you’re working.”
For this, APS worked with the emulsion and emulsifier producer to ensure a mix that would set up quickly yet provide the required strength.
Each night of the project, starting at 10pm, the crew busied itself with two hours of prep work to cover expansion joints and drain inlets before surfacing work could begin. “That’s where the unions came in,” notes Messina. “What we do is specialised and the unions don’t necessarily have people trained in our field. Plus, this is a job where we’re using a larger than normal crew. At that time of year we don’t have people just floating around, everybody’s out there working on projects.
“But we were able to get good union labourers to help us and we taught them how to protect all of the utilities that were out there… That includes the inlets which were only 4.5m apart and the expansion joints that have to move in between. It’s all got to be protected,” says Messina.
In addition, because APS sourced its specialised aggregate from a quarry in central New Jersey, material transportation needs were high. “We were able to get operators out of the operating halls that kept the trucks loaded with material and moving to the project. Such reliable labour is key to a good project.”
Call in the M210
Messina also credits the paving equipment. No new equipment was purchased because the skilled workforce had intimate knowledge of the Bergkamp’s M210 pavers.
According to Messina, the M210 was ideal for the job for a number of reasons, not the least being the machines’ strong dependability, an immensely important factor when you have a small window of opportunity to get a lot of paving done. “We had limited time in which to close the road, complete prep work then surface, stripe and re-open the lane all in the course of a single night,” he says.
The truck-mounted M210 can carry 8m³ of aggregate in a level struck load, 2,271 litres of asphalt emulsion and the same litres of water. It features a 246-litre stainless steel additive tank. The unit is powered by an onboard 74kW Cummins diesel engine at the front of the unit in an enclosed engine compartment to reduce noise for the driver and crew. It provides flexibility to better manage legal load weight restrictions by allowing up to three tag axles, including one behind-the-drive axle. This feature increases the wheelbase and helps the M210 meet the federal bridge law.
Aggregate is delivered to the pugmill by a belt-over-chain conveyor that eliminates slippage. Steep hopper walls minimise bridging while the hopper’s polyethylene lining reduces friction. This eliminates the need for a vibrator which could loosen bolts and damage welds and components.
Asphalt emulsion is delivered to the pugmill by a positive displacement heat-jacketed gear pump. The pump is powered by a jackshaft that is common to the aggregate conveyor to provide a consistent asphalt emulsion-to-aggregate ratio. The variable-speed, dual-shaft, multi-paddle pugmill has a dual hydraulic drive to provide even mixture and coating of the aggregate.
“With the M210, we got good mix action out of the pugmill and we had really good coating on our aggregate, combined with a good mix design and a good emulsion. It was a great product at the end of the day. Also, the M210 keeps up very well with the speed of the pugmill. It put down a 28-pound application [15.2kg/m²] in one lift, which is really heavy for a micro, especially when it comes to a Type 3,” Messina says.
The Brooklyn Bridge project was completed just prior to the July 4th Independence Day celebration weekend in 2017.