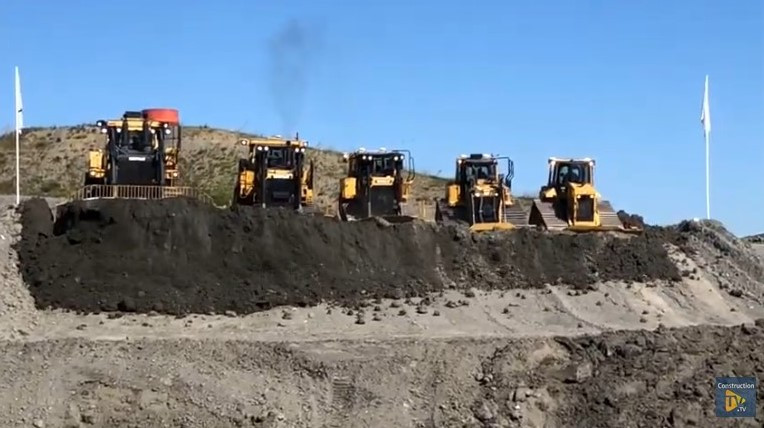
Early February sunshine baths many of
The gathering was to present the best and the brightest of Caterpillar’s machines ahead of the triennial
The Center covers 105 hectares outside Malaga, just off an industrial and commercial estate that rises gently into the hills. Presentations took place in the 220-seat auditorium and demonstrations were held in front of tiered seating a short walk across the campus-like setting. Also at the facility is the S•O•S Services/Fluid Analysis Laboratory which provides preventive maintenance services to customers and dealers throughout Europe, Africa, Middle Eastern and CIS territories – former Soviet Union countries.
Various product managers and directors presented their line-ups in the auditorium, including A.J. Lee - Alexis James – who is in charge of cold planers. The PM300 small planer line-up - PM310, PM312, PM313 – is his baby (see box). Not his newest baby, though. That accolade belongs to a small child back in the US who was born only three weeks before the Malaga event.
Lee holds a civil engineering degree from Michigan Technological University founded in 1885. Michigan Tech is a “small regional school with a big engineering reputation”, he says. Lee has been 14 years with Caterpillar and has for some time been helping revamp the milling division. This means bringing to market new products with the latest machine control and artificial intelligence usually found only on larger machines. It also means getting the right people in place to help customers.
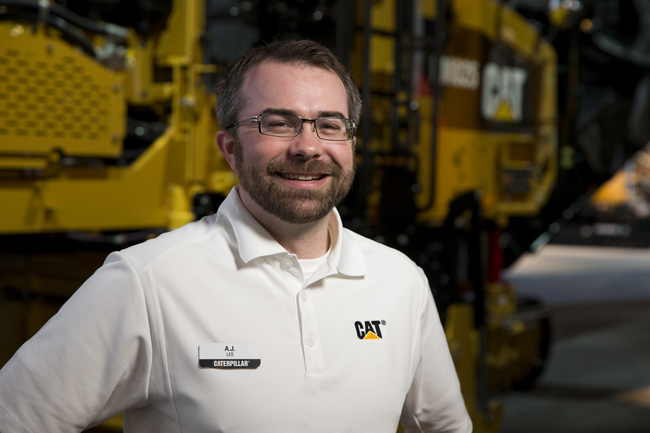
Strategic plan
It was around 2010 when Caterpillar went to work on its planing line-up with a strategic plan for the division to rise higher in the market. It was a strategy that needed to happen, explains Lee. It started with a lot of customer input into what makes a good machine. “As we have re-invented ourselves [milling division] we have taken on a half dozen or so milling specialists who ran their own companies for 20 or 25 years,” he says.
“Their job is to go out, understand the customers’ jobsites and teach people to operate the machines most efficiently. We’re very, very customer focused. We don’t have the legacy [within Caterpillar] of, say, the Dozer D6 people in a division which has been around for 75 or 100 years. We’re going to give as much as we can to help our customers be successful,” explains Lee.
“In 2014 we really kick-started the programme after a lot of research and market analysis. We brought in customers from around the world, including Australia, Taiwan, Europe, North and South America. It was a global approach to benchmark what is out there and what customers are looking for.”
The result of this work is Caterpillar’s newest 300 series as well as the larger 600 and 800 series. But it isn’t stopping there, he says. “Probably one of our biggest projects is a full-lane-width machine for North America. The common cutter size would be a 3.8m and the machine would have the weight and power to go with that.”
Lee believes that a lot of Caterpillar’s competitors have taken a small machine and simply beefed up the horsepower to make it an attractive weight-to-power ratio. But if you don’t balance horsepower and vehicle weight, you won’t make the best use of the engine.
“We have three rotor speeds – low, medium, high – that correspond to the engine RPM. And there are practical applications such as torque loads that allows you to dial back to get more appropriate engine RPM. In essence, we are trying to use as many features as possible to make the job as efficient as possible. This is because a contractor may have only one night to get onto the site, say around five city blocks long.”
Other features, such as automatic jump and ramp-in, ramp-out, makes the operator more efficient, he says. “When the machines arrives at a manhole it is easier to negotiate that obstacle, rather than spend five minutes to manually manoeuvre the machine, clean up and get rolling again.”
Another useful feature is the Stand-by Resume system. “It is literally a pause button,” he says. “Imagine you are going along and have a good cutting speed that is balancing productivity with truck flow, your water levels are set to the right increments and the conveyor and ventilation systems are fine. Now, instead of coming to a stop between trucks, Stand-by Resume simply cycles everything down. We had this first on our PM600 when it was introduced in 2016 and now it is across all our models.”
The black art
Pavement thickness measuring remains something of black art for the planing sector. Caterpillar, like many companies, is working on systems to allow for a more accurate milling thickness. But there are issues, explains Lee.
“Sometimes a contractor is told to remove 100mm. Other times they are told to leave a smoothly profiled surface that meets a certain grade no matter what. Sometimes they are asked to do both, which is not that easy. You might be running along cutting 100mm of pavement and then you realise that you are actually cutting 25mm of gravel below the pavement surface,” he says. “When that road was built 30 years ago, paving wasn’t as accurate as it might be today.”
Even only five years ago having 3D on planers and milling was specialised, an option used by contractors who paved airport runways. “It is still specialised but the number of contractors who are asking us for 3D is skyrocketing,” he notes.
Lee believes the move to put 3D into the small 300 series milling machines is a nod towards the future, basically future-proofing that line-up. “We want it in now because we don’t want to revisit the design to the extent where we redesign the machines or have customers trying to figure out how to retrofit 3D systems.”
Also, if a contractor is running a fleet of various machines, 3D on the small 300 series means there is continuity in performance abilities. “Efficiency is not just about one machine and its performance but the performance of several machines working together. If you are milling 100% accurately then the paving part becomes a lot easier.
“We decided to bring that [3D] onto the 310 milling machine even though you would think the smaller machines do more urban work, maybe only patching jobs that are less likely to need 3D. Yes, it is a very select group of customers now doing it but, I think it will grow quite quickly not just in North America but more so in Europe than anywhere else.”
In Scandinavia there has been some interest in putting a cab on the small machines. “Probably not a practical solution just yet on the 310 size,” explains Lee. The type of urban work the 300series does means the operator is doing more up-and-down movement, as well as getting on and off the machine because it is operating in tight spaces where visibility is often restricted. “We haven’t seen a customer demand for a cab on the 300 size. The demand is becoming more common on our 600 and 800 size, the larger machines, for half-lane work, higher productivity.
Lee on teamwork
Lee believes that one aspect of having a machine control system across in small machines such as the 300 series of planers is that an operator can move seamlessly from one machine to the other if there is an operator shortage. This can help with the generally acknowledged lack of skilled operators. “This would seem an intuitive approach but has not been as common in the industry as a whole,” he says.
Hard to get crews? “It is. Like every part of the industry, we are struggling to get good labour,” he says. “Also, milling is kind of a niche area. They are doing a lot more than, say, pushing a stick on a dozer. Because it’s a niche skill, contactors are also often afraid that their skilled team workers might jump to another contractor for not even a lot of money.”
Potential recruits might still have the image of working with asphalt as one of the dirtiest construction jobs, which isn’t so, says Lee. “You go back in history and workers have their shins covered in tar and stuff. But as we have learned about the properties of asphalt and the machinery has improved, modern day paving should be a pretty clean operation.
“The best paving teams take good care of their equipment. They also don’t want to be shovelling if they can avoid it. They aren’t shovelling piles of asphalt back and forth and dealing with overloads. They are maximising the efficiency of their equipment,” he says.
Lee believes that few people understand how much cold planing is a team effort which also makes it one of the most demanding jobs in road construction.
“In an ADT, you drive, you stop, you dump. Excavator you dig and unload and even then never at the same time. People have a lot more time to think to themselves.” That’s not the case with planing, he explains.
“For example, while the machine is planing the operator on top is operating a conveyor and making sure it aligns with the back of the following truck. You are counting on that truck driver to position themselves and also to move with the planer. At the same time you are propelling the machine forward to get the exact speed for the desired cut, so you don’t overrun the pavement and reduce the quality of the cut.
“You are also trying to steer precisely to the road alignment, more difficult in a city with the road may twist and curve more than on an open highway. Even with a grade control - and they do a wonderful job – you still must keep an eye on it. As I mentioned, on CAT planers it’s a Resume Button to stop and start the machine and which keeps the same settings. It’s all happening at once,” he says.
“In Europe we are seeing a lot more of two-person teams. Either way, they have to be good at communicating back and forth. As it goes, you never hear at good crew talking because they communicate with signs. The bottom guy will look up at the top guy and they will know what to do.”
However, it is not always the top person driving who is the foreman. It all depends on the crew and contractor’s way of working. Sometimes the foreman is a ground level watching the grade. Other times the foreman isn’t even riding or working the machine, but he set it all up for operators.
“There is no right or wrong way. The best crews are those who get the highest efficiency out of themselves and from the machine.”