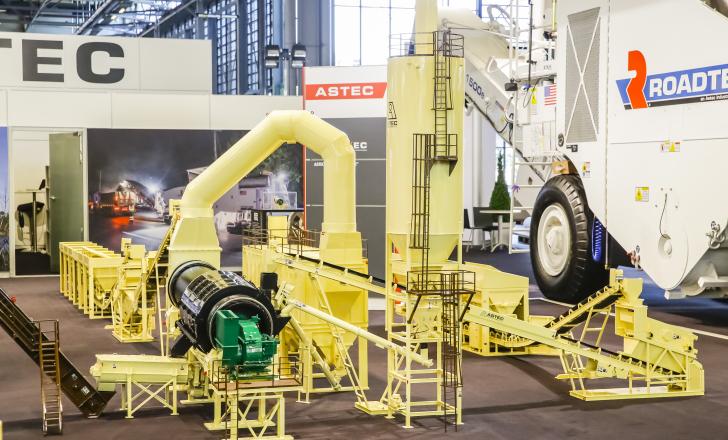
Astec’s Double-Barrel XHR plant provides more use of recycled asphalt planings (RAP) today – and helps meet emissions standards of the future.
The Double-Barrel XHR is built on previous technology, said Malcolm Swanson, President of Astec, a subsidiary of
“The biggest benefits to the plant are its flexibility and emissions,” said Malcolm Swanson, president of Astec, a subsidiary of Astec Industries Inc.
The potential emissions reductions result from Astec’s elimination of a separate dryer for RAP. Swanson said that is significant because emissions that come from those dryers are increasingly facing scrutiny. The Double-Barrel XHR does not require that separate dryer, and therefore does not have the resulting emissions.
“Separate RAP dryers likely will need more pollution controls in the future,” Swanson said. “With this plant, you don’t have those emissions.”
V flights and their efficient heating of materials are among the key factors enabling elimination of the separate RAP dryer, he said.
The flexibility, meanwhile, means plant use of RAP can range from none to 65 per cent, Swanson said.