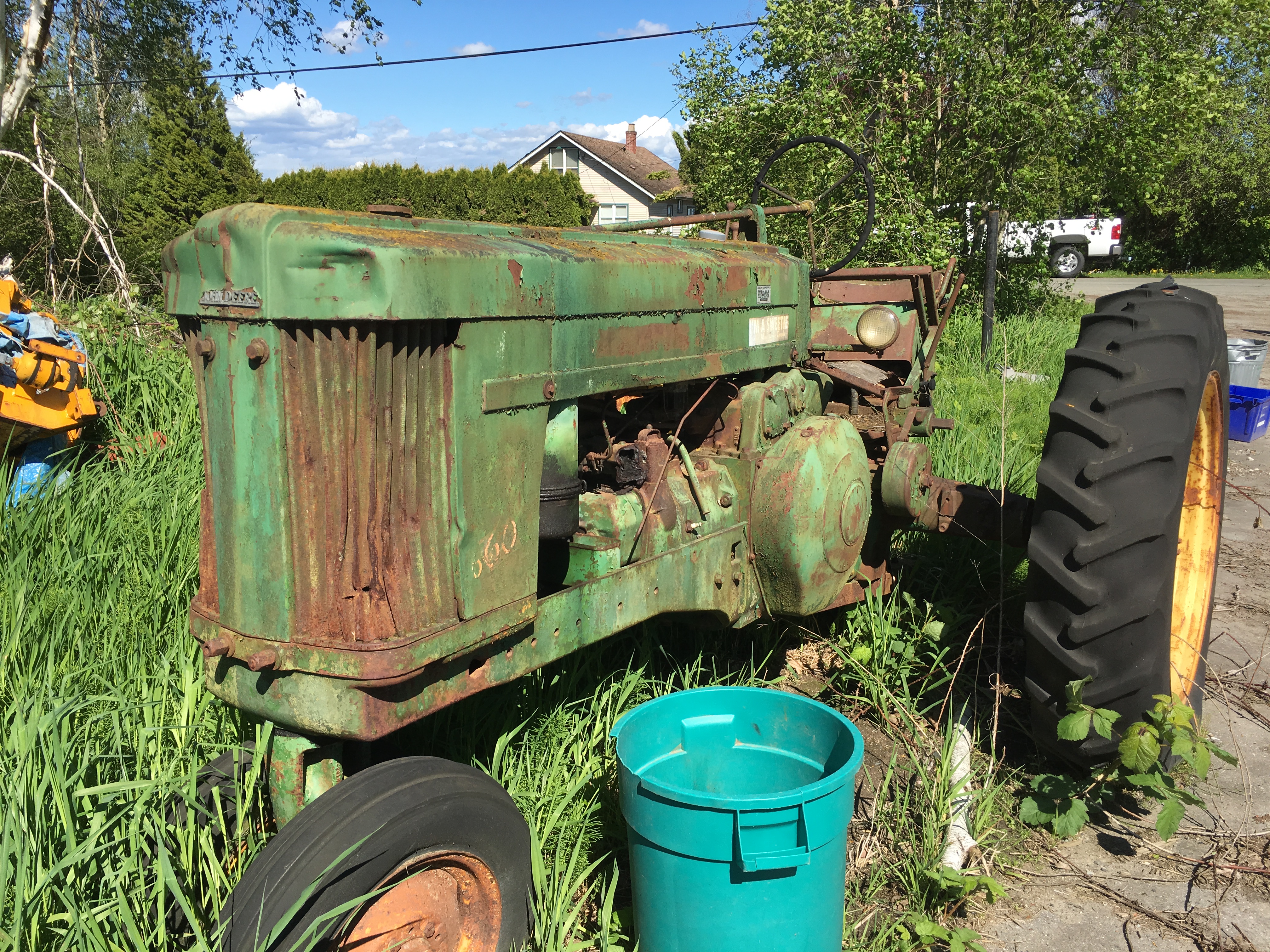
Environmental issues were close to the heart of many presentations at this year’s event at the Reed Exhibition Messe in the Austrian capital from April 16-19. This included decarbonisation – such as making engines more environmentally friendly – and the challenge of digitalisation to create a more efficient transport system.
By improving pavement performance, there will be fewer interventions for repairs as well as complete rebuilding of highways. This translates into fewer emissions by road building equipment, no matter how eco-friendly the engines are.
One aspect of improving pavement performance is the addition of glass fibre, as proposed by Christiane Weise of the Technical University of Dresden, Germany. The investigations considered the cracking and rutting performance of asphalt and how this could be improved with the addition of the fibre.
The team tested a variety of combinations of different length of cut glass fibre, from zero - as a control sample - up to 9.8mm. The results showed that 4mm fibres constituting 0.5% of the total mass of the asphalt material gave the best performance in terms of stiffness, fatigue and rutting of an asphalt base course mix.
The asphalt base control sample containing no glass fibre and 25% recycled asphalt allowed a reduction of 2.5cm in the road’s base layer.
Adding 4mm glass fibre and 25% recycled asphalt improved the reduction in the base layer only slightly, to 3cm. However, a mix of 4mm fibre and 40% recycled asphalt allowed the asphalt base layer to be reduced by 4.5cm. This could potentially reduce costs by reducing the amount of required base layer material.
Increasing the length of the glass fibres to 9.8mm produced the lowest stiffness value and gave no better rutting performance than the control sample with no glass fibre at all. However, Weise said that more work was required to understand this relationship. It was possible that the longer fibres were balling together and not mixing evenly throughout the asphalt. Additionally, all the fibres were dosed by weight, leading to a small total amount of the 9.8mm material.
Another additive that came under the spotlight was rubber-modified bitumen, also done by a team from the Technical University of Dresden - Juliane Kraft, Anita Blasl and Frohmut Wellner. The additive came in the guise of discarded tyres. This conserves non-renewable resources and finds a home for old tyres which otherwise would be dumped in landfill.
The experiment used rubber crumbs of varying sizes – 0.4mm (small), 0.8mm (medium) and 1mm (large) – and in varying amounts (10%, 15% and 20%) in the overall bitumen material.
Their research determined that bitumen modified with 15% of the smallest rubber articles provided the best resistance to fatigue. Meanwhile, bitumen modified with 20% of the largest rubber particles created the greatest resistance against rutting.
X-head: Less noise
Luc Goubert of the Belgian Road Research Centre put forward a method of using roadway structures to reduce traffic noise.
Traditionally, tall screens are used to shield nearby buildings from excessive road noise. Instead, the centre claims that narrow slit in the ground running parallel to the roadway noticeably reduces traffic noise.
It works because noise propagation from roadways occurs close to the surface. The slit, known as a roadside resonator, captures some of the sound waves. The waves bounce around inside the resonator and then escape upwards and out at an angle. This creates a so-called shadow zone several metres high above the ground. The sound waves travel upwards and outwards to pass over the roofs of nearby buildings, out of earshot of occupants and residents. Placing transverse elements within the slit reduces noise by 4db, according the research.
The centre’s next step was to construct a low barrier, 45cm high, parallel to the roadway. Slits are placed within the top of it. Noise measurements taken of a car passing this barrier at speeds between 75-85kph revealed a 9db reduction around 12m from the road – equivalent to the effect given by a conventional 5m-high screen.
Noise from a truck travelling between 50-80kph was reduced by 6db. This smaller reduction is due to a combination of a truck producing more low-frequency noise. Also, its engine is mounted higher than it would be in a passenger car.
Transport Research Arena – TRA 2018
%$Linker: