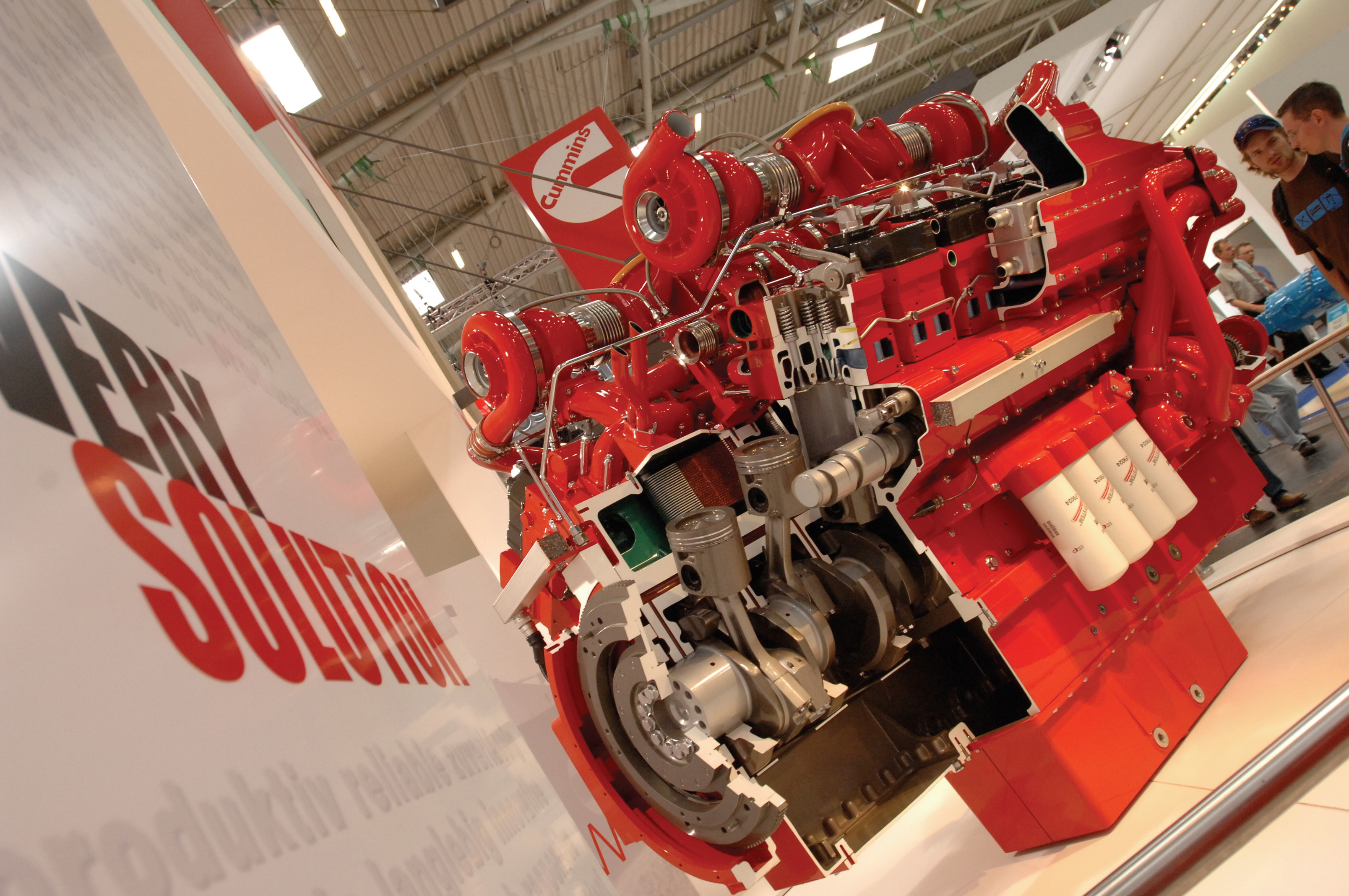
With the Stage IIIA/Tier 3 emissions legislation now in play, engine manufacturers have provided the market with an array of solutions to meet requirements in Europe as well as North America. These current engines are considerably cleaner and quieter in operation than before and the manufacturers have to be praised for achieving the tough requirements set out by legislators in Europe and the US.
The latest generation diesel engines on the market produce far less particulate emissions or NOx at the tailpipe than would have been envisaged in the past. These engines are similar in exterior size to the units they have replaced, as well as offering improved power and torque and in many instances, better fuel consumption. When the legislation was first announced some years ago, engine manufacturers scratched their heads as to how the targets would be achieved and some even said it would not be practical.
Different firms have taken different routes to achieve the low emissions targets but all of the companies have employed sophisticated, high pressure common rail fuel systems in one form or another. Improved combustion is also being used in all the newest engines, with companies employing features such as cross-flow head design, four valves/head and sophisticated engine management technology.
Looking ahead, manufacturers are already planning how to tackle the much tougher Stage IIIB/Tier 4 emissions requirements, without loss of engine performance or drastic increases in fuel consumption. These will be rolled in gradually from 2011, depending on engine power output. The plan is to further reduce particulate and NOx emissions from these next generation diesels and this is presenting a major challenge to the manufacturers.
The challenges are substantial.
Most of the firms are keeping quiet about the technologies they plan to use.
The firm already knows the technology it will use to meet stringent US EPA Tier 4 Interim and European Stage IIIB emission standards for off-highway machines in the 130-560kW powerband taking effect in 2011. It is worth noting that the other firms will take similar routes, although they will of course develop their own in-house solutions.
Caterpillar, New Holland/Iveco and Volvo will also be able to make extensive use of proven engine technology developed for the on highway sector in reducing the emissions from diesels used for off highway equipment. And as Komatsu has an extensive joint venture partnership with Cummins, it will see similar benefits.
The core technology Cummins intends to use combines particulate filters and EGR systems. Engine improvements will also include the use of special variable geometry turbochargers advanced electronic controls and high pressure common rail fuel systems.
To minimise both development costs within Cummins and maintenance costs for the user, common Tier 4/Stage IIIB technology will be used on engines from the mid-range QSB to the heavy-duty QSX engines. The improved product range will maintain or increase power outputs in comparison with the current Tier 3/Stage IIIB engines. Fuel efficiency will be improved by up to 5%.
Cummins believes it can achieve Tier 4/Stage IIIB emissions requirements by developing a package of engine combustion solutions to work with the aftertreatment filter. This will reduce particulate matter emissions levels by 90% and the use of cooled EGR enables the required 45% reduction in NOx to be achieved.
The EGR subsystem has proven to be effective when working with the Cummins VG Turbo technology, which is said to deliver good engine response with optimised boost at given exhaust gas recirculation rates.
Using this technology means that original equipment manufacturers will be able to specify a Tier 4 compliant power system from Cummins, from the air intake filter system to exhaust aftertreatment. As with the current diesels, a sophisticated electronic control module will govern the engine as well as the aftertreatment stages. This last feature is something that will be common to all of the engine manufacturers, although of course they will employ their own in-house solutions.