Taking a road and rail link across one of the biggest rivers in South America, together with its swamps and flood plain, calls for a new crossing of superlative dimensions. Two 135.5m pylons for the third bridge across the Orinoco River in Venezuela are taking shape with the Venezuelan government investing in the showcase project at Caicara del Orinoco. The bridge will have an overall length of 11.125km on completion, which is scheduled for 2015. The main bridge is 2.28km long, and the roadway is 55m above
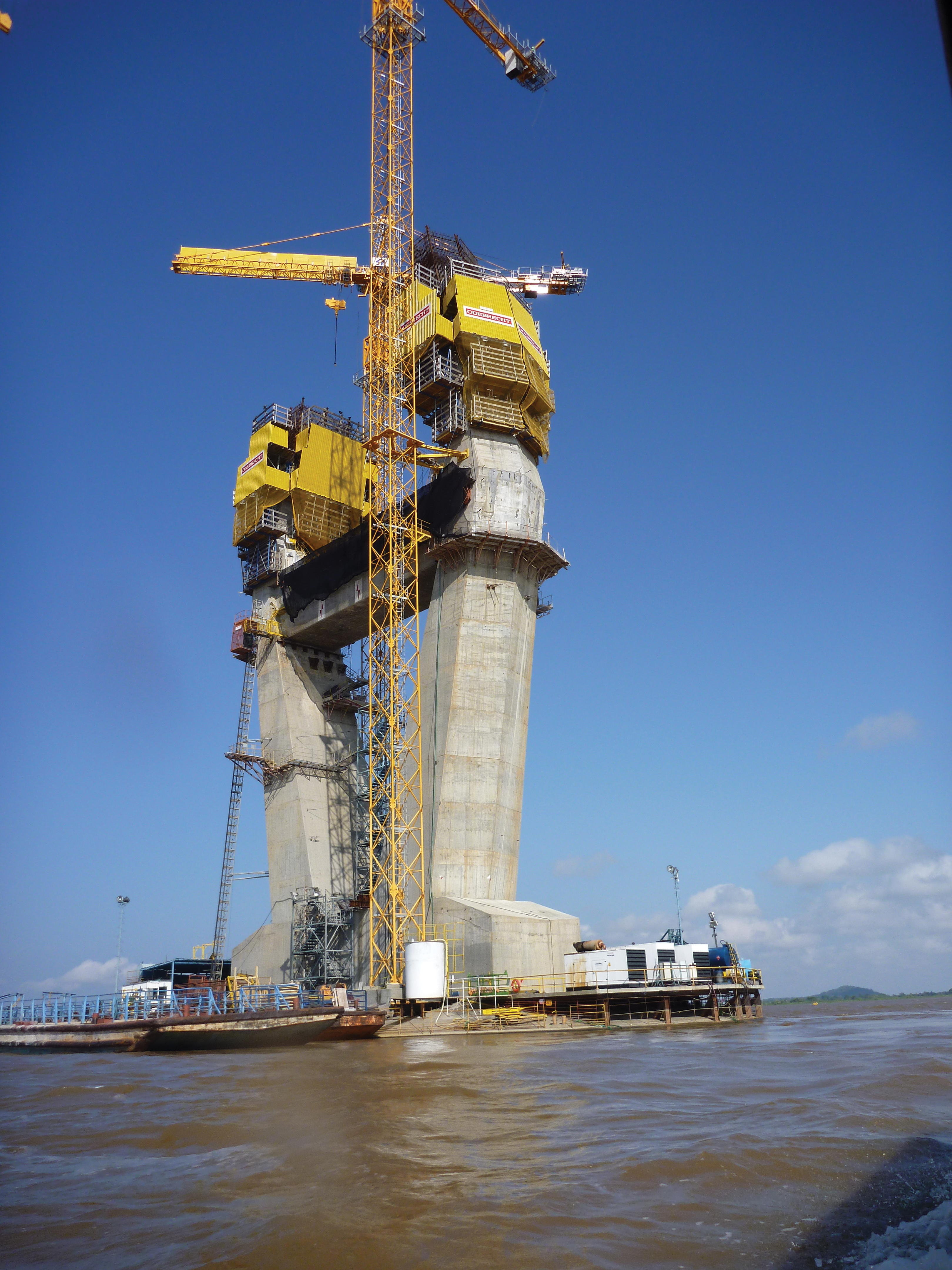
Formwork from Doka meets the requirements regarding changes in the cross-section (Picture: Doka)
Taking a road and rail link across one of the biggest rivers in South America, together with its swamps and flood plain, calls for a new crossing of superlative dimensions
Two 135.5m pylons for the third bridge across the Orinoco River in Venezuela are taking shape with the Venezuelan government investing in the showcase project at Caicara del Orinoco.The bridge will have an overall length of 11.125km on completion, which is scheduled for 2015. The main bridge is 2.28km long, and the roadway is 55m above the water level of the Orinoco.
The two identical diamond-shaped pylons of the 360m main span will be the centrepiece of this high-capacity link.
The formwork solution for both the north and south pylon comes from
When the contractors
According to Doka, by this time it had become clear that the local crane-jumped formwork originally fielded here was not suitable for the task.
Following initial discussions with Odebrecht, Doka developed a solution based on the crane-independent automatic climbing formwork SKE100. “The formwork solution presented by Doka convinced the client in terms of safety and cost-efficiency, as well as speedy construction progress,” says Markus Kamleithner and Nikolaus Eder, the Doka project managers.
The 135.5m tall pylons are basically identical, but with certain minor design differences. They incline at an 18° angle below the cross-beam, and at 13° above it.
Doka says that the most difficult aspects to deal with in the planning work were the changes in the cross-section, the catwalk between the legs of each pylon, and incorporating an extra suspended platform to provide access to the passenger hoist.
With significant changes in cross-section between the foundations and the cross-beam, and a continued upward taper until the point where the pylon legs meet, the structure geometry demands a great deal of adaptability from the formwork systems.
“Automatic climbing formwork SKE100 and the versatile Large-area formwork Top 50 system meet these requirements without needing time-consuming adaptation work,” says Doka.
The load capacity of 10tonne per bracket allows work to proceed simultaneously on several levels. An extra work deck level has been provided above the pouring platform for mounting the reinforcing cages. This allows the forming and reinforcing operations to run in parallel.
A protection screen has been deployed to ensure workplace safety. The working platform and Level +1 are enclosed with trapezoidal sheeting, and all other levels safeguarded by standard handrails.
A catwalk is the main route for site traffic between the legs of each pylon. It is attached to the automatic climbers and is raised along with them up to the next section. A third telescopic suspended platform provides access to the passenger hoist.
After an approximately five-month planning stage, work on pre-assembling the SKE100 units began in September 2011. Doka took over the forming operations on the south pylon from the 17th casting step onward, while on the north pylon the company’s automatic climbing technology was used from the outset.
Two sets of automatic climbing formwork SKE100 with 54 units in total, a catwalk and Large-area formwork Top 50 are in use.
Doka supplied all the systems for on-site pre-assembly and installation. In the crucial assembly phase, both project manager Markus Kamleithner and international formwork instructors were on the site, giving professional introductory training to the site crew and making sure that the formwork systems were properly assembled, installed and handled.
A formwork instructor has been on-site ever since, to assist the project team with his technical expertise.
After seven cycles on one pylon and eight on the other, the Doka automatic climbers had climbed to heights of 65.7m and 33.8m respectively by the start of 2013. The Odebrecht company has worked closely with Doka on projects in Brazil and other countries.
“Doka convinced us with a well thought-out formwork solution. Both the all-in package and the level of detail in the offer documents were truly impressive. The help the Doka formwork experts gave us with on-site assembly laid down an important basis for the project to progress smoothly,” says Vicente Rodrígues.