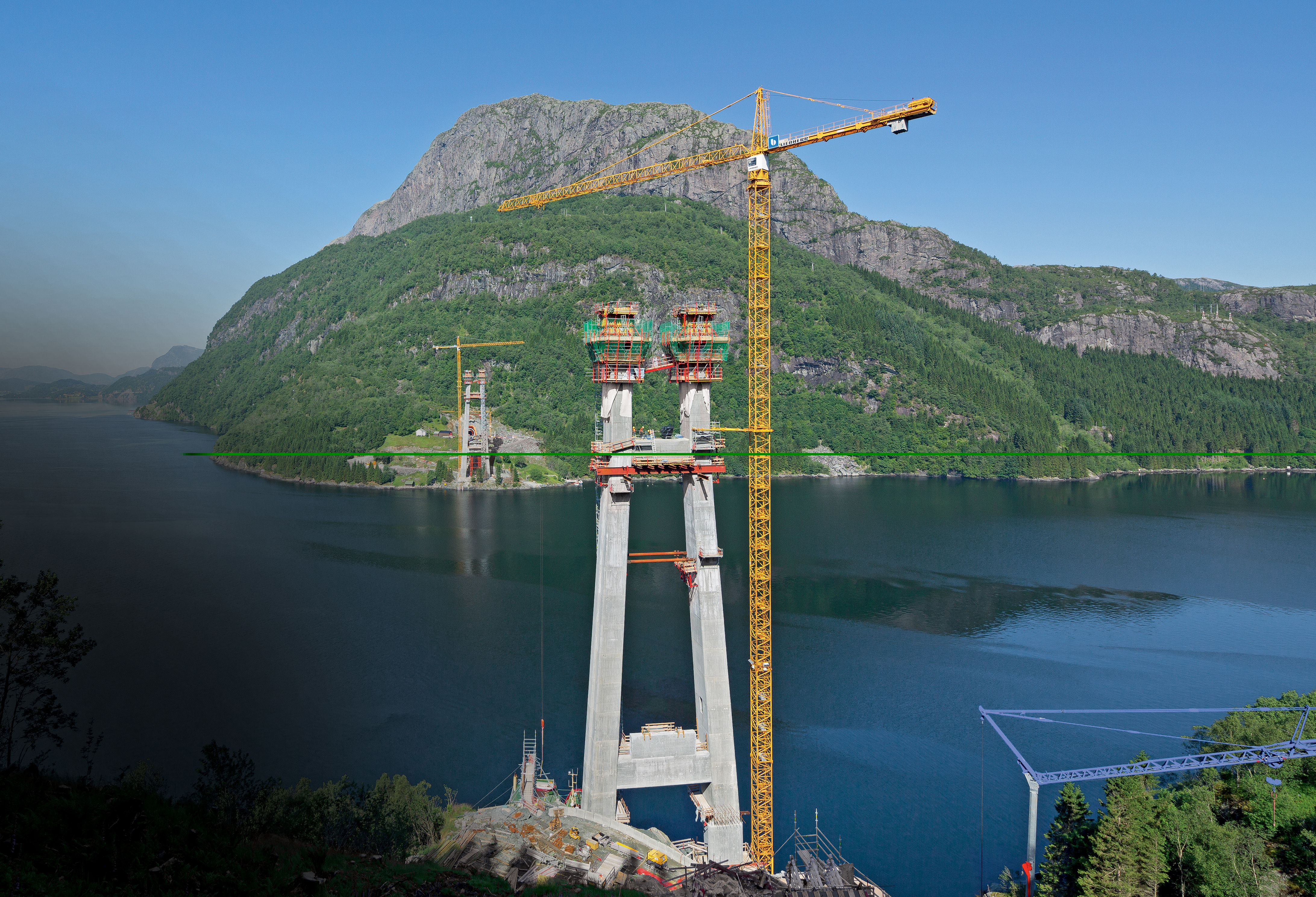
The latest formwork solutions are enabling some tough bridge-building projects to be delivered in South America and Europe, while the world’s largest construction equipment show is seeing the merits of other cutting-edge formwork. Guy Woodford reports
Taking a road and rail link across one of South America’s largest rivers, together with its swamps and floodplain, calls for a new crossing of superlative dimensions.Two 135.5m pylons for the third bridge across the Orinoco River in Venezuela are taking shape through the use of a formwork solution and automatic climbing technology from Austrian firm
The Venezuelan government is investing in this showcase bridge project at Caicara del Orinoco. The bridge will have an overall length of 11.125km on completion, which is scheduled for 2015. The main bridge is 2.28km long, and the roadway is 55m above the water level of the Orinoco. The two identical diamond-shaped pylons of the 360m main span will be the centrepiece of this high-capacity road and rail link. Doka is providing both the North and South Pylon formwork solutions. The globally renowned company is represented in Latin America by subsidiaries in Brazil, Chile, Mexico, Panama and Peru.
When project contractors
With certain minor differences, the two 135.5m tall pylons are said by Doka to be largely the same. They incline at an 18° angle below the cross-beam, and at 13° above it. The most difficult aspects to deal with in the planning work were the changes in the cross-section, the catwalk between the legs of each pylon, and incorporating an extra suspended platform to provide access to the passenger hoist.
With significant changes in cross-section between the foundations and the cross-beam, and a continued upward taper until the point where the pylon legs meet, the structure geometry is said to demand a great deal of adaptability from the formwork systems. Automatic climbing formwork SKE100 and the versatile Large-area formwork Top 50 system are said by Doka to meet these requirements without needing time-consuming adaptation work. The load capacity of 10tonnes per bracket allows work to proceed simultaneously on several levels. An extra work-deck level has been provided above the pouring platform, for mounting the reinforcing cages. This allows the forming and reinforcing operations to run in parallel.
Meanwhile, a protection screen has been deployed to ensure workplace safety. The working platform and Level +1 are enclosed with trapezoidal sheeting, and all other levels safeguarded by standard handrails. A catwalk is the main route for site traffic between the legs of each pylon. It is attached to the automatic climbers and is raised along with them up to the next section. An extra – third – telescopic suspended platform provides access to the passenger hoist.
After a near five-month planning stage, work on pre-assembling the SKE100 units began. Doka took over the forming operations on the South Pylon from the 17th casting step onward; on the North Pylon, Doka automatic climbing technology was used right from the outset. Two sets of Automatic climbing formwork SKE100 with 54 units in total, a catwalk and Large-area formwork Top 50 are in use here. Doka says it supplied all the systems for on-site pre-assembly and installation. In the crucial assembly phase, both project manager Markus Kamleithner and international formwork instructors were on the site. They gave professional introductory training to the site crew and made sure that the formwork systems were properly assembled, installed and handled. A formwork instructor has been on-site ever since, to assist the project team with his technical expertise.
After seven cycles on one pylon and eight on the other, the Doka automatic climbers had climbed to heights of 65.7 and 33.8m respectively by the beginning of 2013. Odebrecht, which has worked closely with Doka on projects in Brazil and other countries, is said to be very satisfied with its choice of self-climbing solution.
RMD Kwikform has channelled its formwork and falsework expertise into tackling a tough assignment near Alsesund, western Norway. A perilous waterfall that flows into a vast fjord was causing a road that clings to steep mountainside to become regularly impassable in the winter, due to ice and avalanche risk. A complex bridge structure was needed to divert the road away from the waterfall area. Norwegian construction company, Nordang, approached HEAB Bygstallningar AB in association with Teknikk AS, customers of
Now, standing around 350m above the fjord, the recently completed Ljoen Bridge is set to prevent future road access issues.
Engineers at RMD Kwikform were approached through its customer, HEAB, and tasked with designing a bridge falsework support system that would function safely and effectively in a difficult working environment, utilising a range of equipment to overcome unique challenges. These included the steep mountainside with loose and unstable rock, and the need to span over the fast flowing waterfall.
The design solution for the bridge falsework support system utilised a full range of RMD Kwikform equipment, including Megashor heavy duty shoring, R700 girders, Superslim soldiers and specially fabricated items.
The Megashor tower solution was designed to take the considerable concrete loads from the bridge deck into the existing pier pile cap bases, so no additional foundations were needed for the falsework system, saving time and costs. Two Megashor towers, ten and 4m high respectively, were founded on the small footprint of the bridge pier pile caps. Raking Megashor members splayed out from specially fabricated nodes on the Megashor towers to support the ends of the header beams.
Due to the flexibility of the Megashor and R700 system, the customer was able to rent existing materials, reducing the overall cost of the project while combining this equipment with their own stock of header beams. This was said to prove particularly useful as standard Megashor rocking heads could be used to connect to the header beams provided by the customer.
Mats Nilsson, of HEAB, says: “When Nordang explained the construction project to us and detailed the difficulties that would be encountered while working in this terrain, we approached our colleagues at RMD Kwikform for support.
“The solution they devised utilised the capabilities of the Megashor system, while recognising the need to keep construction costs as low as possible. With this in mind, RMD Kwikform’s engineers helped us develop a design that would allow the customer to integrate material they already had possession of into the bridge.”
Between the two header beams at the top of the Megashor towers, a system of Superslim plan bracing was used to transfer the considerable wind forces acting on the bridge falsework into the concrete bridge piers. This solution enabled the partly completed bridge structure to resist the strong winds present in this exposed construction environment, horizontally stabilising the Megashor towers without need for additional temporary bracing members. With vertical loading of approximately 700tonnes in each Megashor tower, maintaining structural integrity and stability was very important.
“Due to the unique construction environment and terrain, it was important to pre-assemble as much equipment as possible in our site compound area before transporting these modules to the bridge site. The expertise of the RMD Kwikform engineers was essential for this process,” says Petter Nyberg from Nordang, project manager at the Norway project. “They [RMD Kwikform] were also able to help us cut construction costs by providing an arrangement of Superslim soldiers for the bridge soffit profile, which dramatically reduced the quantity of timber formwork that would normally be needed for this kind of project.”
R700 girders were delivered as flat packed truss panels to the site compound area, a short distance from the bridge site. Each girder assembly comprised two rows of truss panels, connected together with shear pins, and braced together with the R700 bracing system. The 8.8tonne pre-assembled girder modules where then transported to the bridge site and crane lifted into position on top of the Megashor tower header beams.
In Scandinavia, says RMD Kwikform, an abundance of timber means that it is a material often used for formwork frames on bridge deck soffits. However, when it came to the Ljoen Bridge deck soffit design, because the crossfall was complex, the RMD Kwikform team came up with an alternative solution to reduce costs and maintain a high level of precision.
”The crossfall of the deck continuously changed along the bridge, meaning that every soffit formwork frame placed on top of the R700 trusses had to have slightly different dimensions to give the right profile for the deck,” says Adam Fixter, senior project engineer at RMD Kwikform. “The need for precision demanded a frame solution using Superslim Soldiers and specially fabricated struts. The specially fabricated struts varied in length slightly for each soffit frame.”
Fixter says the soffit frames were pre-assembled in the site compound area, with the specially fabricated struts delivered in bundles unique to each Superslim frame. He adds: “Each Superslim frame could then be quickly pre-assembled using pins and R-clips while lying flat, with the specially fabricated struts precisely dictating the geometry. Each Superslim frame was then labelled and transported to the bridge site and easily integrated into the structure.”
The final challenge related to how to recover the formwork and falsework equipment after the concrete had set. The Superslim soffit frames were designed to be easily spilt, and modules of soffit formwork slid out from under the completed bridge deck and lifted clear. The R700 girder modules could then be slid along the extended header beams on top of the Megashor towers. Specially designed shoes between the R700 girders and header beams ensured that the trusses could not fall off the header beams during the sliding operation. Once clear of the completed bridge deck, the R700 girders could be lifted off the header beams and stored on top of the deck ready for transport back to the assembly area.
Fixter adds: “The design solution that we developed with HEAB in association with Teknikk also took into account how the materials would be removed from the bridge after the deck had been struck. This required a high level of communication and collaboration with the construction team as specially modified equipment had to be used to address this challenge. By devising a time-effective solution we were able to reduce construction time, again saving the customer money on this project.”
Among
The P300 is said by the Italian firm to be based on a 100x300cm base panel with a few simple accessories, including a quick connection block said to allow extremely rapid framework operations, and a varnished frame and surface counter-case in 18mm-thick, high resistance, multi-layered Finnish panels to guarantee a high number of uses. Spaced every 1.5m², the coupling system is based on a P300 connecting block and is designed to enable swift assembly and exact alignment of the formwork.
Also from Pilosio and used on the Bucharest overpass project were special formworks and high-capacity towers and props. The overpass has 32 piers of different heights and widths installed with special modular formworks with P300 formworks.
Dalsfjord Bridge’s two H-shaped pylons are around 100m high and the upwardly tapering cross-sections of the double piers are designed with external pilaster strips.
With the help of PERI’s ACS (Automatic Climbing System) and RCS (Rail Climbing System), contractor Bilfinger Construction’s build team was said to be able to complete 24 concreting sections in regular weekly cycles, without a crane and regardless of the weather. For this, PERI engineers combined the external ACS self-climbing system with the rail-climbed RCS positioned on the inside. The VARIO girder wall formwork as part of the climbing units supplied the required shaping. A PERI supervisor briefed site personnel during the initial assembly and operational start-up of the climbing formwork, and ensured swift construction progress from the beginning.
While the connecting bridge between the two sets of pier formwork was an integral part of the PERI formwork solution for Dalsfjord Bridge, another integral aspect was said to be the PERI UP Rosett scaffolding system. This was said to provide safe access to the respective working platform. The stair tower included alternating staircase units with 64cm-wide flights of stairs – continuously extended in accordance with construction progress up to 92m high. The stairs were anchored at regular intervals with PERI push-pull props in order to safely bridge the ever-growing gap to the inclined pylon shafts as the tower increased in height. For this, the existing anchoring points for the ACS could be used.
Dalsfjord Bridge is due to be completed in late 2013. On PERI’s role in its construction Bilfinger Construction’s Martin Schweizok, the Dalsfjord Bridge project’s manager, said: “The PERI systems are well thought-out, easy to understand and designed to meet individual requirements. There were no problems whatsoever for our construction team. As a result, we could maintain the tight construction schedule as well as meeting strict Norwegian safety requirements.”
Alsina’s formwork in demand
Leading Spanish formwork company Alsina has seen its solutions used in a number of major highway projects over the last 12 months.
In order to build a required 1,200m-long false road tunnel between Icod and El Tanque de los Vinos in Tenerife, in the Canary Islands, Alsina’s Research and Development department designed and manufactured a false tunnel cart, including new elements such as tanks, cylinders, adapted profiles HEB-160 and HEB-300, and special, customised curved metal beams.
The formwork carriage was said to leave a porch in the central bay, allowing the passage of vehicles onsite. The cart was 14m long, and placings were performed in 12m spans.
Alsina’s work on the still under construction S8 highway in Poland, stretching 550km between Wrocklaw and Bialystok, involved the provision of formwork solutions for 10 overpasses, each with a width of 6000-8000m³, four prefabricated overpasses and four animal step tunnels. These were all said by the firm to be built with ultimate efficiency using the Nikliborc solution: a shoring board based system. This solution was said to have greatly reduced costs as it allowed the lowering of the deployed multiform measures, as well as the MF braces completely. It was also said to have reduced the required vertical AR80 shoring system by up to half, without losing any of its efficiency, technology and onsite safety.
Another still to be completed highway benefiting from Alsina’s 60 years-plus formwork trading experience is another S8 route, this time in Portugal.
The firm’s AR-65 shoring system, with an onsite shoring volume of 30,000m³, plus the multiform system, was used to build three viaducts and four archway steps covering 270m of the highway.
This project was a particularly important work as it has created better access to the new hospital in Vila Franca de Xira, a town 32km north-east of Lisbon.