David Williams is director of Kijlstra UK, one of the leading European manufacturers and suppliers of drainage solutions. The Group has a turnover in excess of €150 million and sites in numerous locations throughout Western Europe. Ever since Sir John Egan kick-started the Rethinking Construction movement more than a decade ago, designers, contractors and suppliers have been trying to find ways of improving site safety, cutting waste and generally improving efficiency in the construction process. “There has
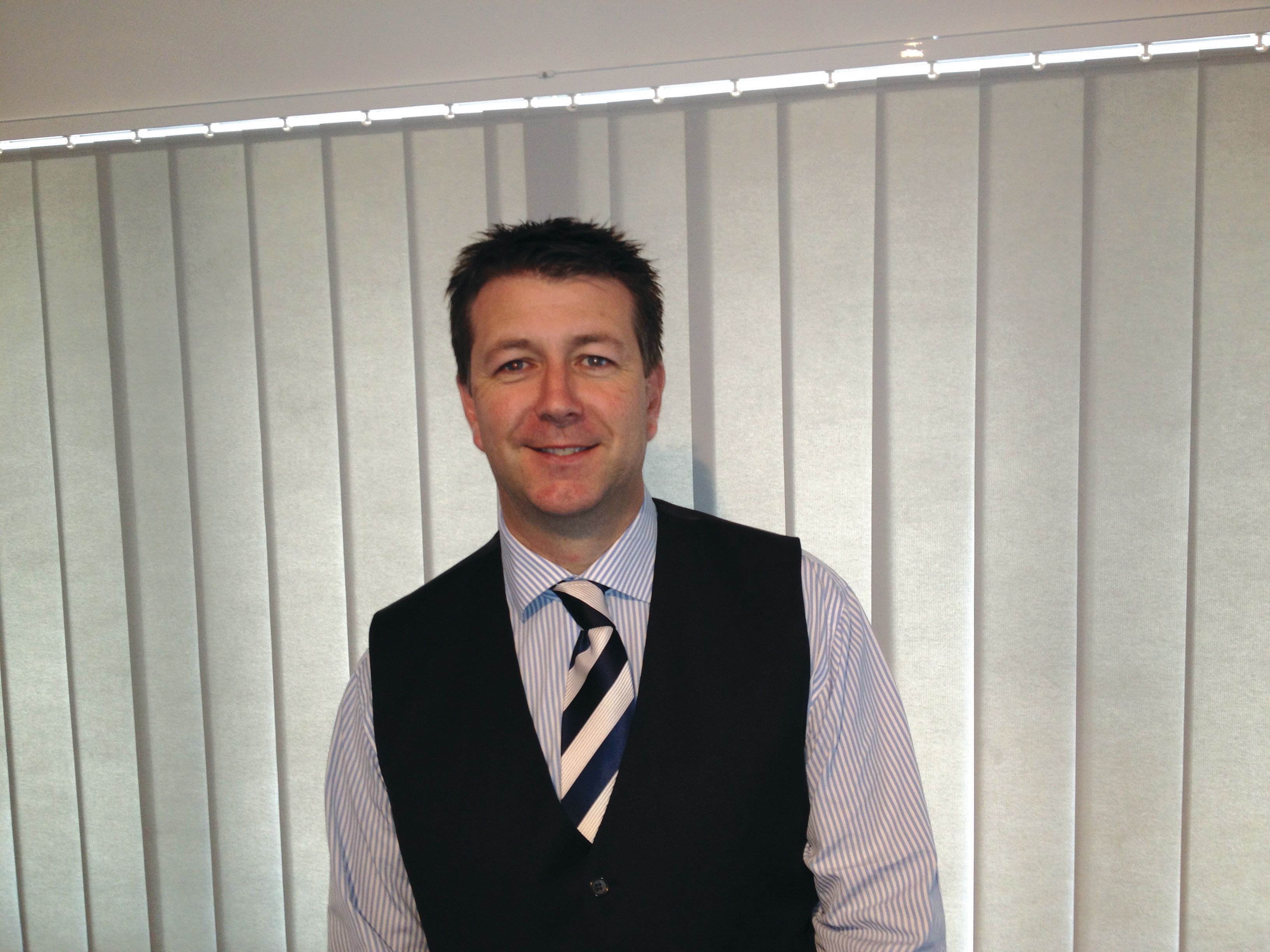
“ As the Industry Standards Group report acknowledges, there is already evidence of a change in behaviour and process” - David Williams Director of Kijlstra UK
David Williams is director of Kijlstra UK, one of the leading European manufacturers and suppliers of drainage solutions. The Group has a turnover in excess of €150 million and sites in numerous locations throughout Western Europe.
Ever since Sir John Egan kick-started the Rethinking Construction movement more than a decade ago, designers, contractors and suppliers have been trying to find ways of improving site safety, cutting waste and generally improving efficiency in the construction process.“There has been a lot of progress since then, but there remain some corners of the industry where old habits die hard and the status quo prevails.
“For example in the highways sector, it is still common for basic components such as manholes and headwalls to be designed from scratch and built on site using in-situ concrete and brickwork.
“While these bespoke structures will perform well in service, they are very much at odds with modern construction methods. Standardised components, from crash barriers to concrete kerbs, have long been commonplace in road construction, but only now are we seeing the wider adoption of factory-made standard products in road drainage systems.
“Earlier this year, the Industry Standards Group, led by
“The report memorably cited an asphalt supplier that has to produce 270 different mixes to meet various Local Authority clients’ interpretations of a handful of high level standards.
“Publication of the report is welcome and timely, and can only encourage the trend towards more off-site manufacturing and standardisation of components.
“A bespoke design might be tailored to the application, but before it gets installed it must first gain approval from the client and perhaps several other interested parties. In the case of road projects, these are likely to include the
“By contrast, standard products designed according to established criteria and with known performance characteristics can be rubber-stamped with confidence.
And when made under factory conditions, they take a lot of expensive and potentially dangerous work off-site and deliver consistent results.
“
“As the Industry Standards Group report acknowledges, there is already evidence of a change in behaviour and process. Already this year Kijlstra has seen a massive change in attitude amongst clients. Water companies and their contractors are increasingly driven by cost and time pressures and are conscious that they must find ways of doing the same job as before, only safer, quicker and cheaper.
“Increasingly, the concept of standardised components is a self-sell. There are clear cost benefits to being able to choose from a range of standard items rather than create a bespoke design from scratch. And with increasing pressure to find sustainable solutions, the low-waste, low environmental impact benefits of standardised and prefabricated methods are increasingly attractive to clients, their contractors and consultants.”