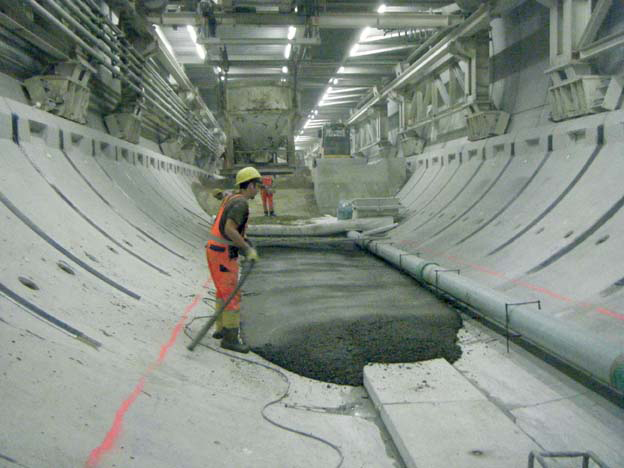
New safety regulations and high traffic volumes require new tunnel construction all across Europe. Mike Woof reports
Anew highway tunnel now being built in Austria will boost traffic volumes and safety standards on a key European route. The existing Pfänder Tunnel lies close to Austria's borders with Germany and Switzerland and carries a heavy traffic volume, so a new parallel tunnel is under construction to help spread this load, increasing capacity as well as safety.Stringent tunnel safety standards have now been introduced across Europe as a result of several horrific disasters. In one particular tunnel incident, high fatalities were the result of vehicles burning following crashes, with those trapped by wrecked vehicles unable to escape. The shocking disaster triggered a public outcry over tunnel safety and the authorities have responded by pushing through this new legislation and providing some or all of the funding for the improvements (some links will be tolled, which will provide long-term financing). The new rules have strict requirements covering key factors such as traffic volumes, safety barriers, emergency areas and ventilation and enforcing these across Europe is triggering a string of major projects.
Austria, Switzerland, Germany, France and Italy have a large number of highway tunnels in and around the Alpine Region and this is where much of the work is being undertaken.
The first Pfänder Tunnel, a service link, was built between 1974 and 1976 with the main tunnel then being driven between 1977 and 1980. The new tunnel will lie to the west of the existing link and will be some 6.5km long, although with the necessary cuttings at either end, the contractor is working over a project some 7.5km long in all. This is a major construction project and the basic cost for the new tunnel is €128 million, with the total project costing around €191 million. There is other excavation work at the project too, aside from the main tube being driven at present. Safety standards require cross connections between the main tunnels every 500m and there are recesses slotted into the side of tunnel to provide a safe area for vehicle users in the event of breakdowns, while there are also ventilation tunnels being driven. According to Michael Höllrigl construction manager from the contracting partners ALPINE and Beton- und Monierbau Gesellschaft, "Construction on the Western tube started in October 2007. It's due to open to traffic in 2012 and this will be followed by renovation of the Eastern tube."
By 2013 the upgrade work to the existing tunnel will be complete and both will then be open to traffic.
Safety is not the only reason for this tunnel project though. Steady increases in vehicle numbers have made it clear that the existing link will not be sufficient to meet future demand. In 2005, the existing tunnel carried 23,000 vehicles/day and this rose to 26,000/day in 2007. The forecast for 2020 is that 46,200 vehicles/day will want to use the link and as the existing tunnel has a safe capacity of 35,000 vehicles/day, it is clear that the new link is vital to meet future transport needs for the area.
A tunnel boring machine (TBM) was selected to drive the main tunnel following the experience of the difficult conditions encountered when constructing the first link. One of the problems is that there is a high water content in the ground, so effective drainage is important. The tunnel is being lined with some 19,500 concrete segments that are 2m wide precast and weigh 60tonnes apiece, while the tunnel also features multiple sealing layers to prevent water ingress. Because the working area is compact, the precast lining sections have to be manufactured elsewhere and are carried 100km by truck to an on-site storage area with sufficient capacity for five days. The safety standards require a cross connection between the two tunnels every 500m while there are also recesses slotted into the side of tunnel to provide a safe area for vehicle users in the event of a breakdown.
Tunnel drive
The Herrenknecht S474 TBM being used on this project was originally constructed in 2006 and was used on a tunnelling project in France initially, driving two 3km tubes in parallel for a new highway link. Prior to being used on the Pfänder project, the machine was rebuilt and reworked over the space of a year and is effectively a new machine, according to ASFiNAG. This electric drive TBM has a 16x160kW drive rating and features 24 drive rams that push against a 2.4m pressure ring. It delivers a 67,500kN driving force, weighs in at 2,000tonnes and has a total installed power of 4,800kW.
Most of the weight is at the front of the 210m long machine, with the 11.92m diameter cutting shield alone weighing 200tonnes. The shield has 72 disc type cutters as well as six clearer apertures to let spoil fall away from the face and into the clearer tube for removal by the conveyor system, with around 7,500tonnes/day of material being cut from the face. Höllrigl said, "The cutters perform a rolling action over the face and this is how you get the material out. The cutter shield turns at 4rpm; it's the fastest we can go and we'd overheat the cutters if we went any quicker."
At Pfänder the TBM advances 25m/day, with the boring work carried out in two 10-hour shifts by a 14 strong crew, while the remaining four- hour shift is used for machine maintenance and the work is carried out five days/week. Operating the TBM is a tricky process with a single person in control who monitors a bank of video display screens and steers the machine as required to keep it accurately on track.
The rock conditions include varying types of sandstone, with some hard and abrasive areas containing high silica content. The most difficult areas are where there is swellable material, which can expand up to 25% in size on contact with water. These conditions were expected, and the design accounts for these.
By September, the TBM will have finished its portion of the project and the roadway can then be paved and the mechanical and electrical installation work can commence.
Crosstown traffic
A new Liebherr R924 machine is one of a number of Liebherr excavators being used for excavating the cross sections. The machine is specially equipped for tunnelling with a blade and two extra guides for each of the tracks. Power comes from a 130kW Liebherr diesel and the machine is equipped with a particle filter to reduce emissions in tunnels. A key feature for the application is the specially designed boom, which rotates 45º in two directions to achieve the best digging position in the tunnel.
The R924 is not the only special machine modified by Liebherr for this application and the firm has also supplied a new wheel loader and a new tracked loader in the special tunnelling configuration.
Alexander Katrycz is in charge of marketing at Liebhher's Telfs facility in Austria where the crawler loaders are built. He explained that the ventilation tunnels for the project posed problems for existing machines as these go over the top of the main tunnel. The tunnels climb 31m in height over a fairly short distance and are too steep for a wheeled loader to operate so the joint venture partners spoke with Liebherr to find an alternative. The solution was to modify a crawler loader for the task according to Katrycz. This 15tonne LR634 model has a particulate filter for its four cylinder diesel to reduce emissions, extra protection for the rear bumper and a cut down cab to work in the restricted headroom application. Katrycz said, "This machine has a very low noise output, especially when compared with the older machines."
In addition a Liebherr L566 2 plus 2 loader is being used at the site and this also features a particulate filter for the exhaust system, as well as extra protection for the z-bar rams and heavy-duty reinforcement for the rear bumper. Other Liebherr machines onsite include some smaller (and older) R900 excavators and an assortment of older wheeled loaders. In addition, three underground trucks are used to haul material outside while there are also a number of Atlas Copco tunnelling jumbos that are being used where required for additional side cuts.