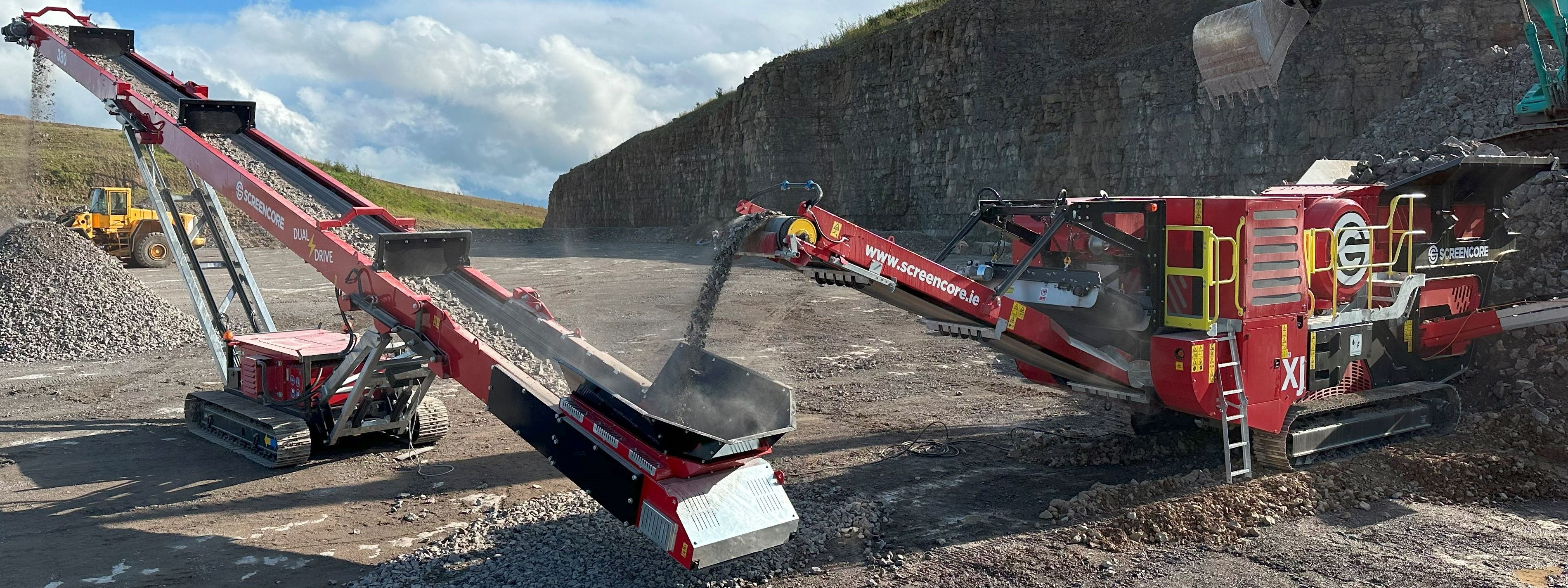
The use of apps for more productive screening operations and the dual use of diesel and electric power have helped boost quarry efficiencies, according to Kleeman, Major and Screenscore.
Kleeman reports that its intuitive SPECTIVE mobile app operating concept contributes significantly to efficient operability of its crushing machines. The material discharge and, therefore, associated material stockpiles can now be better monitored and organised thanks to the “stockpile monitoring” function.
Meanwhile, Kleeman says that SPECTIVE CONNECT now also makes work easier for the wheel loader operator whose tasks include clearing stockpiles.
Stockpile monitoring allows SPECTIVE CONNECT to display the current status of material stockpiles at all times. Users can define from what stockpile height they wish to be informed; for example, at 90 percent of the total height.
Stockpile monitoring is particularly helpful on extensive terrain and with larger machine trains. Not all material stockpiles are always in the excavator operator's field of vision. Wheel loader operators often have other tasks as well.
SPECTIVE CONNECT sends a push notification to enable operators to go to the full material stockpile at the right time to clear it, enabling them to concentrate on their other jobs. This saves unnecessary trips, prevents switch-off when the stockpile is full and increases productivity.
The system, says Kleeman, also learns for the future. All data on the material stockpiles is recorded and used to build up an algorithm that calculates the time remaining until the stockpile is full. The stockpile monitoring function then allows processes on the work site to be optimised and prevents downtimes.
Electric crushing
To further boost crushing efficiency, Kleeman says that its electric crushing and screening plant lineup raises the environmental credentials of its owners and operators by omitting CO2 emissions on site. Kleeman acknowledges that initial investment costs are higher, but says that the higher costs are quickly amortised due to savings on diesel fuel.
A sample calculation for the German market shows that this is possible after around six years, according to Kleeman. If the system can be supplied with energy via the customer's own photovoltaic system, Kleeman says that return on investment can be as low four years.
“Our mobile plant train in the sample calculation consists of a jaw crusher MOBICAT MC 120 PRO, cone crusher MOBICONE MCO 110 PRO as a secondary crusher and a downstream screen machine MOBISCREEN MSC 953 EVO,” said Tobias Böckle, head of product management at Kleemann. “The plant train consumes an average of around 77 litres of diesel per operating hour. In the electrified version, it has an average current consumption of 302kW per operating hour. The maximum power requirement is 542kW.
“The energy requirement must first be provided by the infrastructure and is ideally met by electricity from renewable sources,” noted Böckle. “A sustainable and quickly cost-efficient solution is to use an in-house photovoltaic power supply.”
RFID technology
Major, a Canadian global manufacturer of wire screen media, has updated it app offering with the addition of the FLEX-MAT Sensor App. It includes marketing materials, expert documents and a newsroom with articles and announcements as well as RFID reader technology and the FLEX-MAT Sensor.
“Simplifying The MAJOR App allows customers to access all their screen media data in one place, saving time and virtually eliminating room for measurement errors,” said Kevin Laporte, R&D manager for Major.
The app streamlines customer and dealer processes by digitalising relevant product information. Customers and dealers can track and store screen media data such as screen dimensions and customer-defined details to simplify the ordering process through FLEX-MAT ID-Enabled.
Meanwhile, RFID technology allows customers and dealers to easily access product information through without needing an additional reading device. Simply scan the FLEX-MAT screen with The Major App to access product information. This makes the reordering process easier by minimising the need to climb onto the screen deck to measure screen. Fewer physical measurements also reduce the potential for mistakenly ordering the wrong size, which can result in producing out-of-spec products.
For screen media without ID-enabled features, the app includes an augmented measurement tool where customers and dealers can use their phone camera for approximate measurements.
The app also features the FLEX-MAT Sensor, a vibration data measurement tool where operators can fine-tune their screen machine without shutting down the equipment. Operators connect to a single sensor, which is placed on one corner of the machine at a time. The sensor is moved to each corner of the machine to get a full view of the vibrational data. Once the measurement process is complete, the data is delivered to the Major App, where it is stored locally for ease of use and viewing in areas with cellular limitations.
Once a signal is available, the information is uploaded into Major’s cloud storage, where it is viewable from a web browser. By providing accessible, real-time data immediately following a vibration analysis, the Major App supports quick and easy maintenance for maximum production.
The app also includes an efficiency calculator, open area calculator and a warehouse function that compiles a list of screen media in storage along with their specifications. These features help operations closely monitor production as well as inventory for improved efficiency.
The free app is available for Apple and Android phones.
Dual power
Screencore says that the latest version of its hybrid tracked jaw crusher, the hybrid XJ Dual-Power, is more fuel-efficient and more accurate than its predecesdsors.
The hybrid XJ Dual-Power is a development of Screencore’s bestselling diesel-electric 1,000mm x 650mm jaw crusher. Features include an updated jaw-level sensor, refined electric plug-in (genset or mains), push button hydraulic CSS wedge adjustment and a bolted mainframe jaw construction.
In addition, for inner city material recycling operations, the compact crusher is equipped with an updated dust suppression system, overband magnet and an optional deflector plate.
The XJ is able to use mains electricity as power, as well as provide the power for other attached screens or stockpilers, explained Ciarán Ryan, a director of Screencore, based in Ireland. “With its low transport height and length and rapid setup time, under 10 minutes, the XJ is easily moved between sites for maximised operational flexibility. This makes it ideal for rental companies and businesses with a number of production sites.”
Recently Screencore introduced the first of a range of Dual-Drive series of stockpiling conveyors. These are manufactured with a conveyor drive that can easily switch from an electric drive motor on one side of the conveyor to a hydraulic drive motor on the opposite side. This empowers operators to choose the most suitable and readily available power source, all the while enjoying the convenience of a fully tracked mobile unit.
Through refining the operation, the Dual-Drive now enables stockpilers - and other members of the Screencore range - to be connected to the electrical outlet of the Dual-Power XJ jaw crusher. This enables the attached machine to run efficiently at virtually zero additional cost, offering a cost-effective solution for materials handling.
“The intelligent integration on our new Dual-Drive stockpilers and Dual-Power crushers, can be extended to other crushers or screens with spare electrical capacity, eliminating the need for an extra engine and significantly contributing to carbon reduction,” said Ryan. “As well as providing an environmentally focused and a flexible efficient solution for customers, it also ensures that crushing, screening and stockpiling operations are more cost effective and efficient.”
A major feature of the XJ Dual-Power is its miserly fuel consumption, which, said Ryan, even when powered by diesel is in single digits for liters per hour. This is even lower when running on electric power while powering other screens or stockpilers.
“This means that environmentally, as well as production wise, the XJ checks all the boxes including both the ‘Zero Emissions’ box with its plug-in ability, and the ‘Low Noise’ box,” said Ryan. “We believe that the XJ Dual-Power yet again raises the productivity bar substantially for mid-sized crushers.”