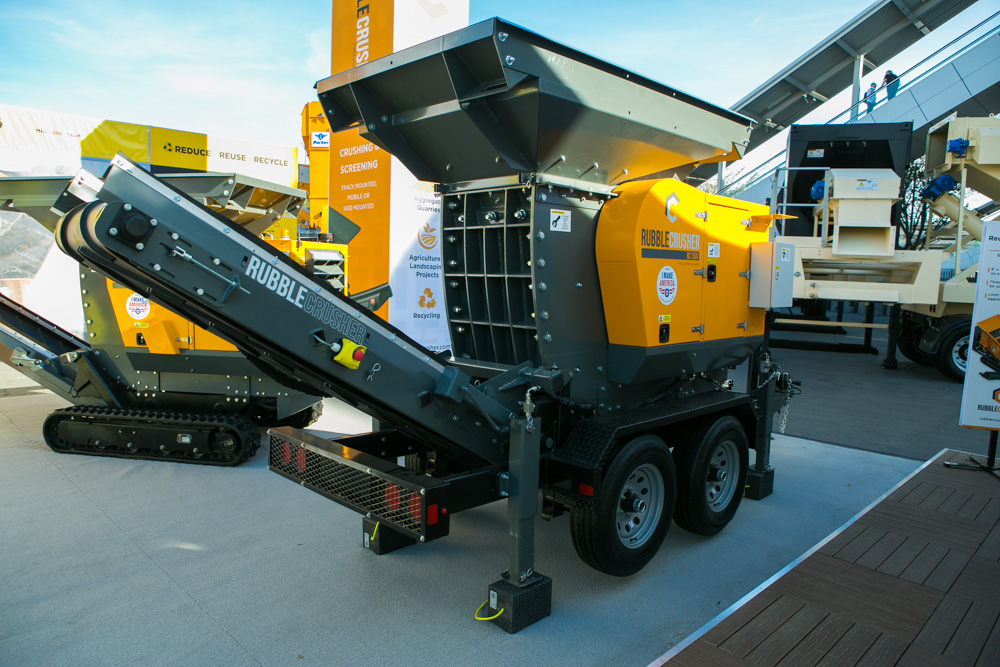
According to McLanahan, RubbleCrusher was founded with a focus on supporting the “zero waste” approach to the construction and demolition recycling industry. The machines, which are made in Leicestershire, England, are aimed at “small-to-medium-sized crushing and recycling projects that help contribute to a circular economy.”
Bought in June of last year, RubbleCrusher is one of McLanahan’s family of companies, which also includes Eagle Iron Works, Anaconda, and its latest acquisition, Diefenbach (an Italian filtration, water and tailings management firm).
Liam Holland, RubbleCrusher’s business line director, says the firm, formerly a brand owned and operated by CMB International, is excited about its commercial opportunities in the US, where it is in the process of expanding its dealer network.
“RubbleCrusher is an answer to the increasing pressure that governments around the world are putting on construction companies to target zero waste on their sites,” he says. Its compact crushers can be mounted on wheels, tracks or a skid, and pulled behind a truck.
“We see that it is not just the large-scale projects that need to reduce the amount of waste on-site, many small-to-medium-sized projects need a solution too. That was the inspiration behind the creation of RubbleCrusher.”
RubbleCrusher’s pull-behind portable crusher, RC150V, was, says Holland, developed for small-to-medium-sized recycling projects where the cost and size of larger, traditional machinery would have made recycling impossible.
The RC150V can be hauled by any full-size pick-up truck, simplifying set-up at any operation. The RC150V unit weighs just under 3.54 tonnes and enables to operator to recycle C&D waste materials for use on-site, without having to pay to remove materials or bring in new aggregate for jobs.
The RC150T offers the same features as the RC150V but is mounted on tracks, making mobility on-site possible by remote control. These tracks also allow it to be moved across roads, pavements, and driveways without causing surface damage.
Both units feature a hydraulically driven jaw that gives users the option to run the crusher forwards or backwards. The reverse function allows for clearing any blockages as well as processing sticky asphalt material. The machines are equipped with a 40-litre fuel tank that allows for a minimum of eight hours of crushing time. The RC150V and RC150T can both process up to 300 tonnes of material per day, depending on feed material and output setting.
“RubbleCrusher plants can be used across various sectors, such as demolition, construction, and landscape gardening. They remove the need to take construction and demolition waste away from site and eliminate the cost of buying in aggregates for the sites where they work,” says Holland. “These simple, easy-to-use machines can be operated by one person, transported by a 4x4 pick-up, and set up to crush within minutes.”
Booth: McLanahan C31372, RubbleCrusher S5276