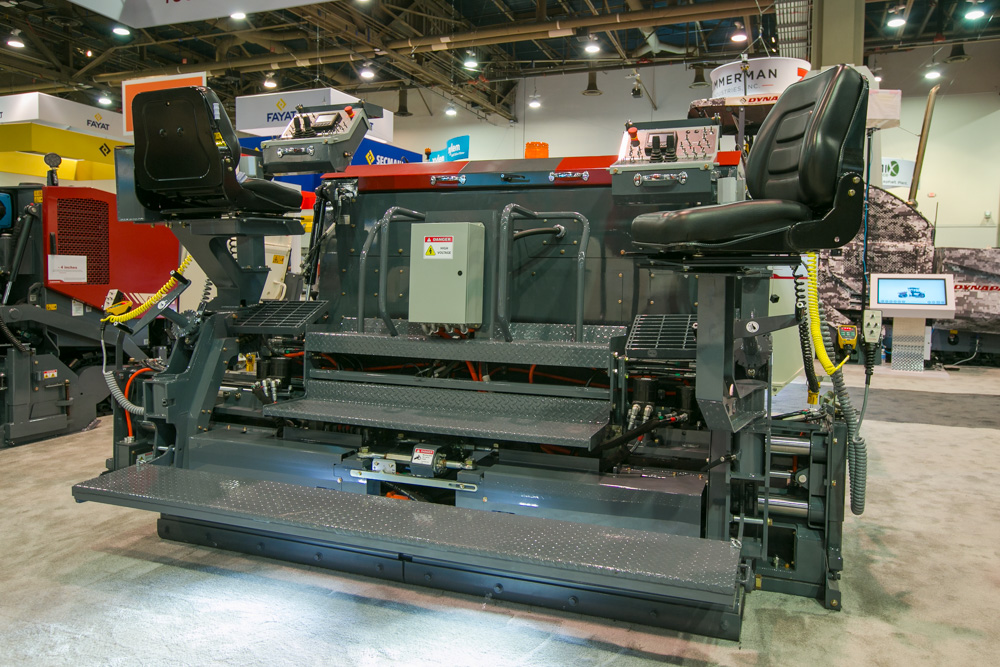
The paver is specifically for the North American market and comes with a vibrating screed. Key enhancements over its predecessor, the FC1700 C, include a fail-safe heat management system for increased efficiency and reliability. The newly designed proportional auger conveyor system controls the material flow to the screed.
Dynapac’s entire product range is built on the principle of ‘Designed to Perform and Built to Last’. With this in mind, bolted-on conveyor floor plates, segmented auger flights and screed plates mean that all the wear parts are easily replaced and can be rebuilt several times.
The company’s quad auger system includes screed-mounted augers on both main and extensions. This allows the material to feed with a smoother process whatever the pavement width, without needing a lot of manual work to get the material to wider paving widths.
The independent conveyor system, along with reversible conveyor capability, allows for ease of operation while paving and eliminates spillage onto the ground when transporting the paver between jobsites.
The proportional feed system offers precise control of the head of material in front the screed. Operators can personalise from the display the various material pile-height settings according to job requirements.
Dynapac’s D17 C is paired with the VF0816 front extension screed for high-quality paving results. Weighing in at just over 2,040kg, the VF0816 is the heaviest in its class, providing unbeatable pre-compaction, says the company.
D17 C screed heating is the next-level technology for commercial-class pavers. A newly designed, direct drive 3-phase 16kW engine-mounted generator increases the efficiency and reduces heat-up time. The heating system includes multi-zone heat monitoring for even temperatures across the entire width of the screed. The reliability of the heat control system is further enhanced by having redundancy sensors combined with smart fail-safe heat management technology.
Booth Central Hall 300931