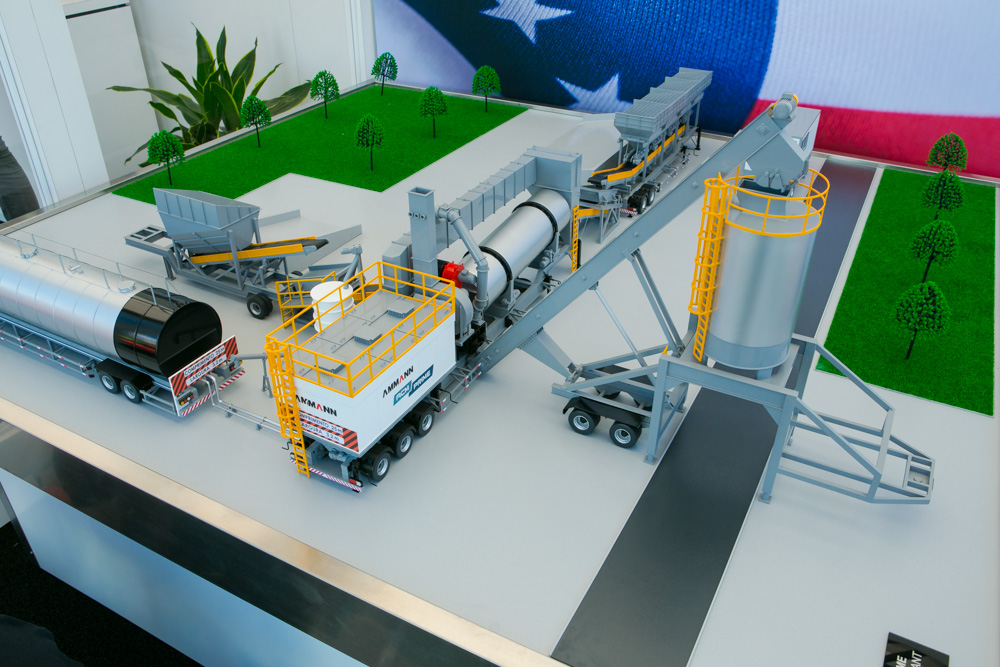
The firm is also introducing its proven ACM Prime Asphalt-Mixing Plant to North America, which is primarily built in the US and offers the benefits of a high-capacity plant in a fully mobile package.
The ACM Prime Asphalt-Mixing Plant fits on two, two-axle trailers and remains on them upon arrival and during operation. To relocate the plant, the trailers are simply attached to trucks and moved.
The new ACM Prime is a continuous plant that is 100% mobile. Accessories such as tanks, RAP feeders, self-erecting storage silos and the control house are also on wheels. With previous models, some of these elements were stationary.
Ammann’s business development manager Carlo Machado said, “We decided to move asphalt plants to the US and will be manufacturing here. We are working on developing the supply chain.”
John Elliott has been hired as president, North American Asphalt Plants for Ammann and explained, “The US is a continuous asphalt plant market. Ammann has got a lot of sophisticated technology applicable. We recognise this as an opportunity for Ammann and we are building a team to capitalise on it.”
Elliott said that the new, large-capacity plant will benefit from Ammann’s sophisticated technology and will feature a counterflow drum mixer with a 50% recycling capability.
Meanwhile, the cost of the compact ACM Prime Asphalt-Mixing Plant is less than a conventional stationary plant, making it easier for small businesses to enter the market. The firm says that the plant can be ready to work quickly. It arrives assembled, and plug-in components make set-up extremely fast.
While the ACM Prime is highly mobile, it produces high-quality mix. The plant has successfully manufactured mix for airport runways, where quality is of the utmost importance.
Production capacity is 161tonnes/hour with 5% moisture. Mixing times are adjustable, based on the recipe and desired output. The plant can utilise RAP, produce warm mix, and incorporate filler, fibres and other additives.
The Ammann as1 Control System helps improve quality while reducing material waste and energy consumption. A proven, reliable and robust fieldbus system is included.
Fuel efficiency is another benefit. Heat exchange is optimised between hot gases generated by the burner flame and aggregates. Enclosed gaskets between the dryer and chamber are well insulated. Air pressure is controlled inside the drum and burner, and dryer and burner settings are precise to minimise fuel burn.
Booth S5455