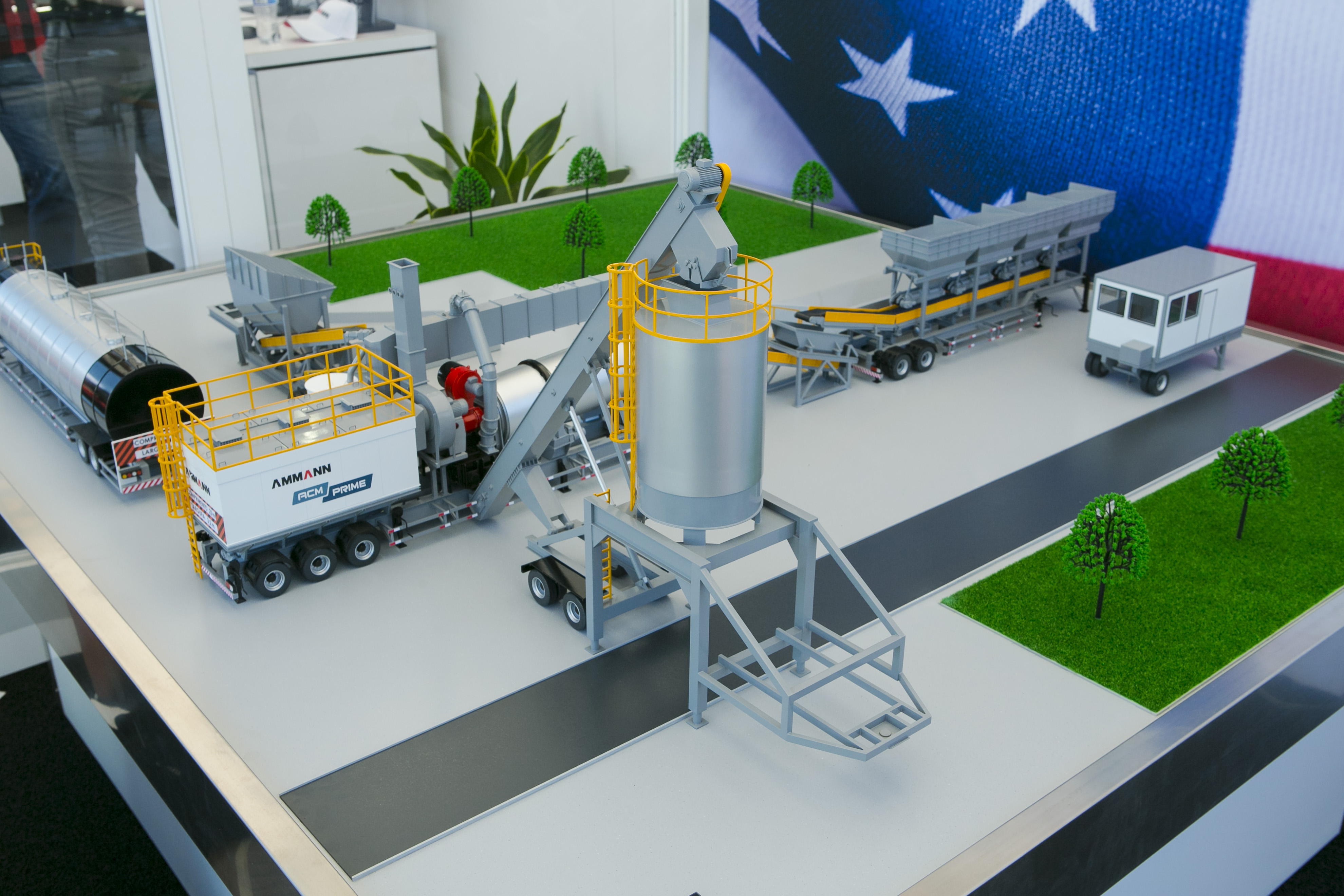
Asphalt plant manufacturers have delivered better technology to reduce emissions over the last decade. Among the improvements are advanced baghouse filters, improved combustion processes and alternative fuel sources.
And now, emissions reductions are being fought on a new front: during the loading process. Ammann is a leader in the industry with its Ammann blue smoke treatment (BST) technology.
The BST system captures vapours that would previously have escaped during loading. With BST, the trapped fumes undergo a filtration process to remove oily particles with the remaining gas streams being sent to the burners.
“BST is a win for plant owners on all counts,” said Mathias Halter, Ammann’s director of Sales for Europe, the Middle East and Africa. “It’s the answer the industry has been looking for.”
Blue smoke emissions have been around since the advent of asphalt-mixing plants. The smoke released during loading resulted from the high temperatures required in the production process. The temperatures were a necessity so little could be done to stop the smoke.
New regulations are requiring that steps be taken to mitigate blue smoke fumes. This is a challenge for those in the industry, but Ammann says it has found an answer with BST.
The BST system captures the fumes and redirects them to a multi-stage filtration system. The filters remove the oily particles during multiple filtration stages, ensuring high efficiency and allowing the remaining gases to be re-used in the combustion process. The condensed oil that accumulates in the filtration system can be recycled. The BST system also allows a steady flow rate at the chimney, a key factor in controlling NOx and CO emissions.
According to Ammann, BST is a cost-effective solution. It does not require the use of complex and costly confinement methods, and the filtration system is efficient and inexpensive to operate. The BST system delivers environmental benefits right across the asphalt production operation. Diffuse emissions are removed, for the benefit of those working at the plant and anyone in the immediate vicinity of the facility.
This new innovative technology by Ammann is already in use with the expected results in several Ammann Plants
“This is a significant development on the sustainability front,” said Marzio Ferrini, product marketing manager at Ammann. “Blue smoke is a challenge the industry has faced for years and Ammann has found an answer.”
In addition, Ammann has been developing an innovative continuous asphalt plant specifically to meet the needs of the North American market. The plant is designed to deliver capacities in the 270-360tonne/hour range, which forms the majority of US demand and the firm says that this new model will be ready for delivery to customers by the start of the 2024 paving season.
Ammann’s business development manager Carlo Machado said, “We decided to move asphalt plants to the US and will be manufacturing here. We are working on developing the supply chain.”
At the same time, the firm is also offering its versatile ACM Prime Asphalt-Mixing Plant for the North American market. This plant is said to offer the benefits of a high-capacity machine but in a fully mobile package.
Ease of transport is achieved as the plant fits on two, two-axle trailers and remains on them upon arrival and during operation. To relocate the plant, the trailers can be hitched onto trucks and moved to a new site. This continuous plant is 100% mobile. Accessories such as tanks, RAP feeders, self-erecting storage silos and the control house are also on wheels. With previous models, some of these elements were stationary.
John Elliott has been hired as president, North American Asphalt Plants for Ammann and explained, “The US is a continuous asphalt plant market. Ammann has got a lot of sophisticated technology applicable. are building a team to capitalise on it.”
Elliott said that the new, large-capacity continuous plant will benefit from Ammann’s sophisticated technology and will feature a counterflow drum mixer with a 50% recycling capability.
Meanwhile, the cost of the compact ACM Prime Asphalt-Mixing Plant is less than a conventional stationary plant, making it easier for small businesses to enter the market. The firm says that the plant can be ready to work quickly as it arrives assembled, with plug-in components to speed set-up. Production capacity is 161tonnes/hour and mixing times are adjustable, based on the recipe and desired output. The plant can utilise RAP, produce warm mix, and incorporate filler, fibres and other additives.