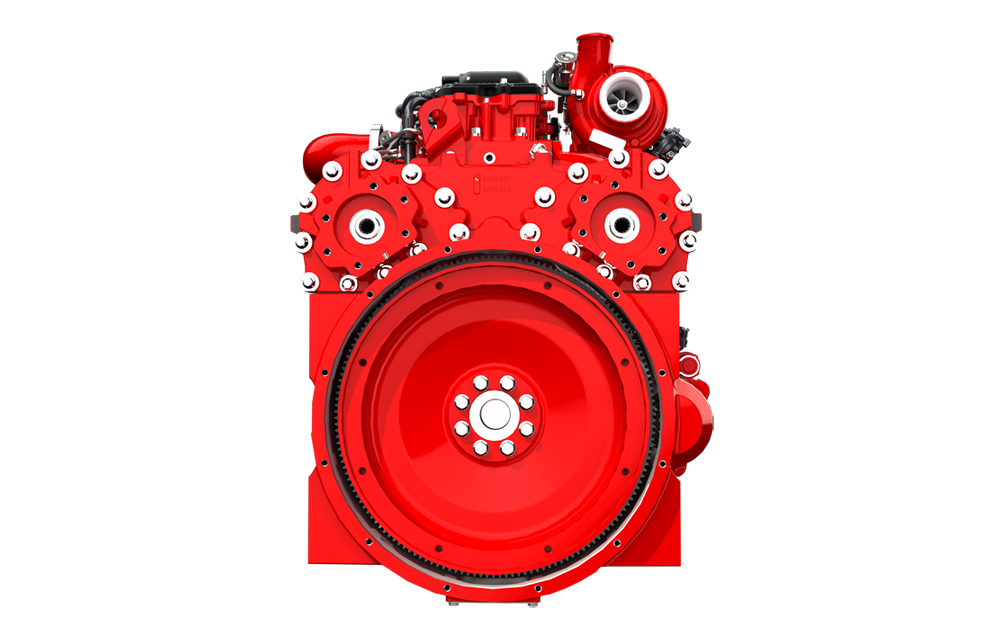
Cummins’ power units are available from 75 – 503kW (100 – 675hp) delivered as a complete and ready-made package. The units include an engine, exhaust aftertreatment system, radiator and cooling system, plus auxiliaries such as mounting feet, hoses and an air cleaner. More than 60% of the content is pre-approved, making the machine integration process simpler and quicker.
In a bid to increase the flexibility and capability of the power units, Cummins is integrating new single and dual rear-engine power take-offs (REPTO). These complement standard PTO capability used for items such as hydraulic pumps, but Cummins is also making them available on base engines without the need for a pack.
As an example, fitted with the dual REPTO, the L9 will have a total drive capability of 560 Nm. This will make the engine capable of driving additional pumping capability through SAE B 2 and 4 bolt mounts. Integrated into the flywheel housing, the dual REPTO is compact and has a minimal impact on engine packaging. The added weight is approximately 100kg.
Examples of installations to date include the L9 Power Units powering Anaconda’s new J12 and I12 crushing machines. The B6.7 version is available with Bandit in their Intimidator® 20XP tree chipper plus NLB Corp’s water jetting systems.
Jeremy Harsin - Cummins Off-Highway Marketing Director said: “Our Performance Series Power Units offer a flexible drop-in solution for manufacturers. The high-power density of our engines enables them to deliver high machine capability for hard-working applications such as crushing, screening and pumping.
“For equipment manufacturers, they have the ability to efficiently drive more from the engine without the need for additional aftermarket systems. This would support the driving of hydraulic pumps for all sorts of machine functions from steering systems to fans, etc. It will reduce installation costs and complexity for a more integrated solution.”
Sponsored content produced in association with Cummins