Driveline technology continues to develop rapidly, with many manufacturers at this year’s Conexpo exhibition showing Tier 4 Final emissions solutions, along with a host of fuel saving transmissions and hydraulic systems, all aiming to reduce operating costs for the customer. However, while there was certainly a hybrid presence at the show, things haven’t perhaps moved forward as fast as many had expected.
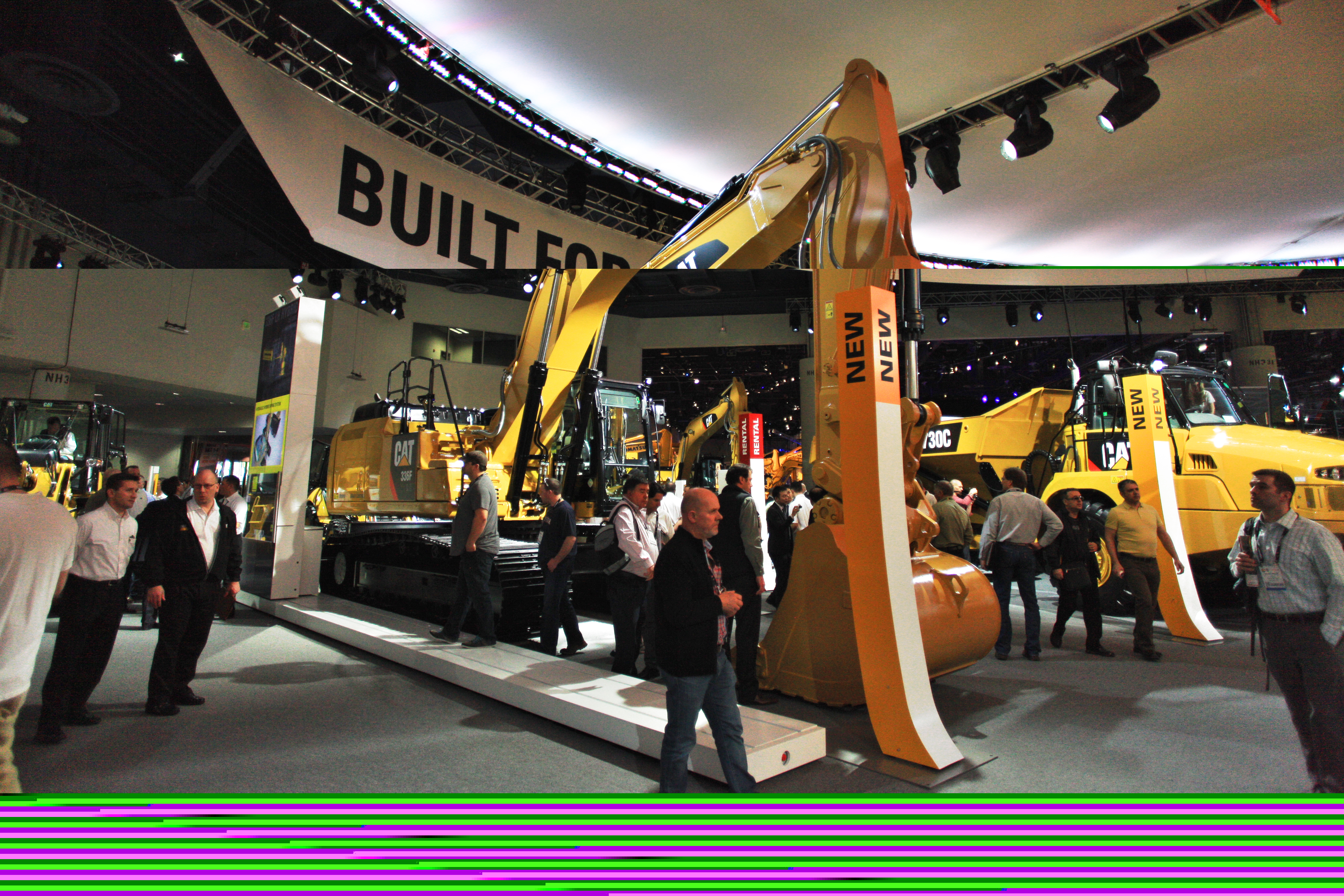
Cat’s 336 hybrid excavator now benefits from a Tier 4 Final engine
Driveline technology continues to develop rapidly, with many manufacturers at this year’s Conexpo exhibition showing Tier 4 Final emissions solutions, along with a host of fuel saving transmissions and hydraulic systems, all aiming to reduce operating costs for the customer.
However, while there was certainly a hybrid presence at the show, things haven’t perhaps moved forward as fast as many had expected.
Given the speed of progress in the automotive market and the almost constant launch of series and parallel hybrids, full electric vehicles and other technologies, construction equipment risks being left behind if the industry doesn’t continue to constantly push a wide range of driveline options. Many of the hybrid machines that we have seen in the past, such as2300 Komatsu’s HB215 and 178 Caterpillar’s similarly sized 336E hybrid excavator, are still attracting attention on the stands, though they have this year become the HB215-2 and the 336F Hybrid.
However the majority of the updates to these machines involve the move to Tier 4 engines, rather than changes to the actual hybrid technology. It’s a similar story with236 Hyundai’s R220-LC Hi-Poss excavator, which uses a hydraulic hybrid system rather than an electrical storage system. All of these companies base this technology on a single machine at present. Given the fuel saving and efficiency benefits of hybrid drive, spreading it across a range of machines would benefit more customers.
That has been the case at257 John Deere Construction, where the success of the 644K Hybrid wheeled loader has led to the introduction of a hybrid version of the larger 944K. That said, rather oddly, the 644K Hybrid continues with a Tier 4 Interim engine at present, while Deere’s other wheeled loaders have made the move to Tier 4 Final.
Component suppliers are keen to make the most of any move to hybridisation.1575 Ricardo is continuing to develop its TorqStor high-speed flywheel energy storage system. This combines a modular high-efficiency carbon fibre flywheel, with a magnetic coupling and gearing system, to provide a range of energy storage capacities for different machine applications. This year Ricardo is delivering a 200kJ capacity Torq Stor unit to a number of OEMs for evaluation, which it hopes will lead to actual take-up and machine production.
“While Ricardo has technical and integration experience of a wide range of energy storage systems, from super capacitors and electrical hybrids to accumulator-based systems, we believe that the high speed flywheel offers a highly pragmatic and low cost approach to achieving real-world fuel savings in construction equipment,” said David Rollafson, Ricardo’s VP of innovation.
“We are now accepting orders from OEMs and Tier 1 manufacturers for pre-production units for the delivery in late spring 2014.”
2254 Dana is also developing hydraulic hybrid technology, with the Spicer PowerBoost system. This captures wasted energy from the driveline and hydraulics and recuperates that energy to help power the machine, reducing fuel consumption by a claimed 20-40%. Hydrostatic energy is captured in an accumulator and then delivered to the drivetrain when required. Dana has conducted more than 1,000 hours of testing using a 16 tonne wheeled loader and is now trialling the system in a telescopic handler.
One totally new system on show at3485 Conexpo was an electric hybrid driveline from 7214 Oerlikon. Aimed at the wheeled loader market, the hybrid package is a complete electric drive system. Oerlikon has partnered with Cummins to provide a Tier 4 engine, which drives conventional hydraulic pumps for the loader arms and an electrical motor/generator for the driveline.
The electrical power is used to drive the machine’s wheels through individual electric wheel motors, rather than conventional axles. Each motor also contains the brakes, allowing energy recuperation under retardation. The system is currently in the development stages, but it offers a fresh approach to the market and is currently being tested on a 30 tonne wheeled loader with a manufacturer in China.
This highlights perhaps the most important factor in the adoption of these technologies. Hybrid systems are designed to reduce fuel consumption and exhaust emissions, through the capture of waste energy and the reuse of that energy to assist the diesel engine. Adoption of hybrid systems can only succeed in the market when machine owners and operators feel that the fuel consumption benefit outweighs the additional purchase and operating cost, or government legislation drives that adoption.
While a number of US companies are at the forefront of technological advance, introducing hybrid technology in a country with notoriously inexpensive fuel is always going to be difficult. Countries like China however, along with many European territories where reduced emissions and high fuel prices will drive interest, will no doubt provide an increasingly receptive audience.
However, while there was certainly a hybrid presence at the show, things haven’t perhaps moved forward as fast as many had expected.
Given the speed of progress in the automotive market and the almost constant launch of series and parallel hybrids, full electric vehicles and other technologies, construction equipment risks being left behind if the industry doesn’t continue to constantly push a wide range of driveline options. Many of the hybrid machines that we have seen in the past, such as
However the majority of the updates to these machines involve the move to Tier 4 engines, rather than changes to the actual hybrid technology. It’s a similar story with
That has been the case at
Component suppliers are keen to make the most of any move to hybridisation.
“While Ricardo has technical and integration experience of a wide range of energy storage systems, from super capacitors and electrical hybrids to accumulator-based systems, we believe that the high speed flywheel offers a highly pragmatic and low cost approach to achieving real-world fuel savings in construction equipment,” said David Rollafson, Ricardo’s VP of innovation.
“We are now accepting orders from OEMs and Tier 1 manufacturers for pre-production units for the delivery in late spring 2014.”
One totally new system on show at
The electrical power is used to drive the machine’s wheels through individual electric wheel motors, rather than conventional axles. Each motor also contains the brakes, allowing energy recuperation under retardation. The system is currently in the development stages, but it offers a fresh approach to the market and is currently being tested on a 30 tonne wheeled loader with a manufacturer in China.
This highlights perhaps the most important factor in the adoption of these technologies. Hybrid systems are designed to reduce fuel consumption and exhaust emissions, through the capture of waste energy and the reuse of that energy to assist the diesel engine. Adoption of hybrid systems can only succeed in the market when machine owners and operators feel that the fuel consumption benefit outweighs the additional purchase and operating cost, or government legislation drives that adoption.
While a number of US companies are at the forefront of technological advance, introducing hybrid technology in a country with notoriously inexpensive fuel is always going to be difficult. Countries like China however, along with many European territories where reduced emissions and high fuel prices will drive interest, will no doubt provide an increasingly receptive audience.