A quarry in the US has managed to boost production by around 30%, thanks to the acquisition of new equipment. Replacing the old crusher at the Lafarge Pitt River Quarry has made a massive increase in production capacity, helped by improvements to the existing crushing circuit.
ELRUS Aggregate Systems provided advice on optimizing throughput, with the facility further improved with the addition of a new CH660 cone crusher from Sandvik Construction.
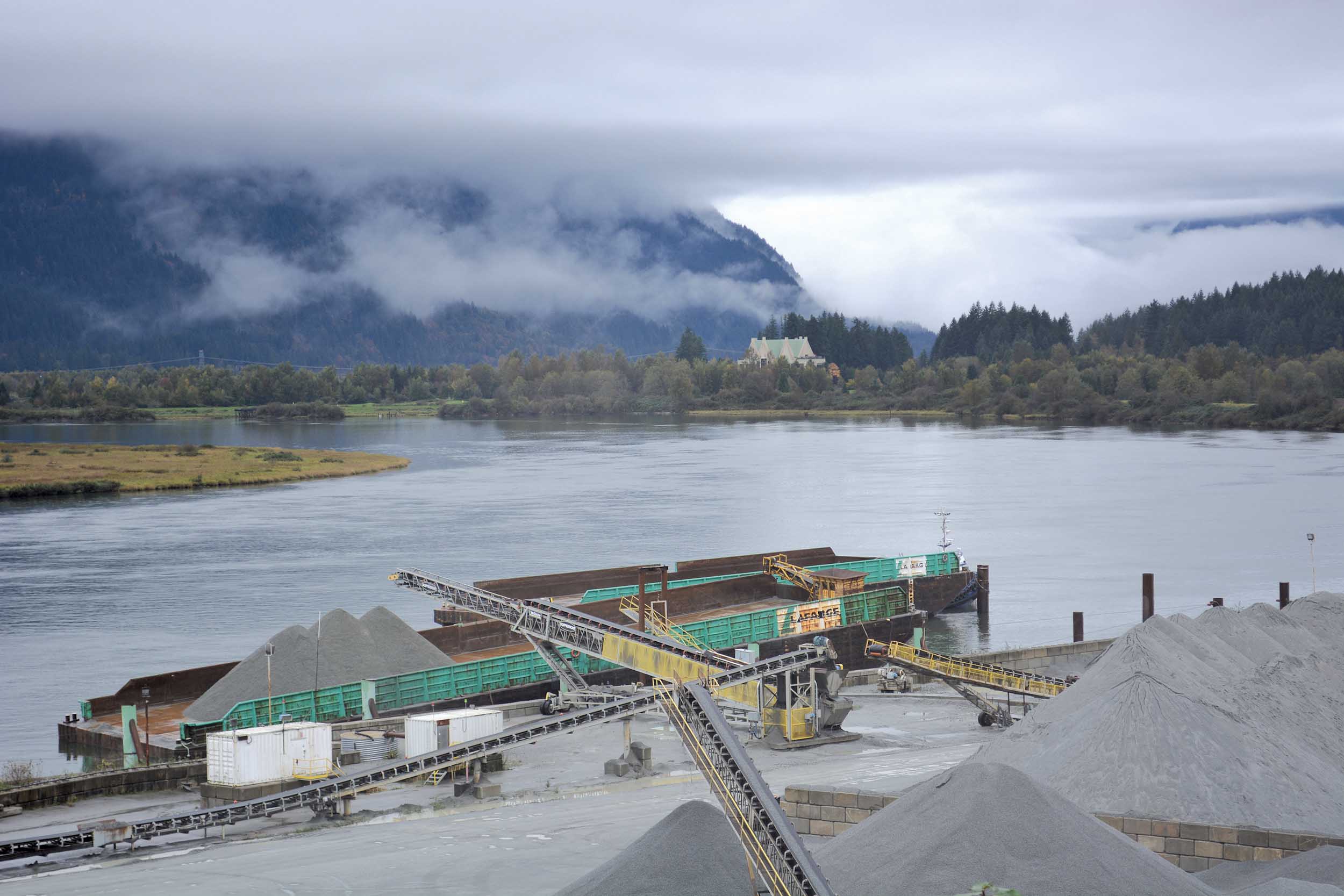
With a realigned crushing circuit, output efficiency has also been increased at the Pitt River facility, which produces 1.5-2 million tonnes/year of material that is then shipped out by barge
A quarry in the US has managed to boost production by around 30%, thanks to the acquisition of new equipment. Replacing the old crusher at the Lafarge Pitt River Quarry has made a massive increase in production capacity, helped by improvements to the existing crushing circuit.
ELRUS Aggregate Systems provided advice on optimizing throughput, with the facility further improved with the addition of a new CH660 cone crusher from2403 Sandvik Construction.
The Pitt River facility is a key unit and for3180 Lafarge in North America and is located some 50km west of Vancouver. That places it within the Vancouver metro area, which is a big market for the quarry. Situated near the banks of the Pitt River, it ships out 1.5-2 million tonnes of aggregate/year, loading either river barges or trucks with the prized product. Reserves at the quarry are expected to last for the next half century.
In 2013 operations at the granite quarry were running smoothly, churning out 900tonnes/hour of high-quality aggregate used in asphalt and concrete applications. When a main frame cracked on the existing cone crusher, the firm looked at options to replace the quaternary unit, which was too old to warrant repair. Among the offered solutions was one provided by ELRUS Aggregate Systems, the Sandvik Construction dealer for western Canada, which had supplied the quarry’s secondary crushing unit, a Sandvik S6800.
ELRUS believed a common platform unit to the S6800, the Sandvik CH660 stationary cone crusher, would be a good fit for the crushing system. After studying several flow sheets, the firm also proposed rearranging the line-up of machines to take advantage of the CH660’s finer product. The company suggested relocating the tertiary crusher to replace the damaged cone crusher and the CH660 then to carry out the third-stage crushing, offering a predicted increase in output of at least 10-15%.
The CH660 went on line as a tertiary crusher, and the benefits have exceeded expectations with the quarry experiencing a 30% increase in aggregate output, reaching 1,200tonnes/hour. Another advantage for Lafarge Pitt River Quarry is better maintenance scheduling. Because of increased production rates, the quarry can afford regular planned maintenance interruptions, which also avoid costlier overtime repair work.
Systematically maintaining the machinery has other positive implications for the company as now the maintenance occurs regularly, budgeting for it is regular, too, with the cost being spread throughout the year rather than coming in surges at sometimes inconvenient times.
The CH660 also benefits from more efficient power transfer to the crushing chamber, deriving from Sandvik’s Hydroset technology coupled with the ASRi automation system that maintains optimum reduction despite wear.
ELRUS Aggregate Systems provided advice on optimizing throughput, with the facility further improved with the addition of a new CH660 cone crusher from
The Pitt River facility is a key unit and for
In 2013 operations at the granite quarry were running smoothly, churning out 900tonnes/hour of high-quality aggregate used in asphalt and concrete applications. When a main frame cracked on the existing cone crusher, the firm looked at options to replace the quaternary unit, which was too old to warrant repair. Among the offered solutions was one provided by ELRUS Aggregate Systems, the Sandvik Construction dealer for western Canada, which had supplied the quarry’s secondary crushing unit, a Sandvik S6800.
ELRUS believed a common platform unit to the S6800, the Sandvik CH660 stationary cone crusher, would be a good fit for the crushing system. After studying several flow sheets, the firm also proposed rearranging the line-up of machines to take advantage of the CH660’s finer product. The company suggested relocating the tertiary crusher to replace the damaged cone crusher and the CH660 then to carry out the third-stage crushing, offering a predicted increase in output of at least 10-15%.
The CH660 went on line as a tertiary crusher, and the benefits have exceeded expectations with the quarry experiencing a 30% increase in aggregate output, reaching 1,200tonnes/hour. Another advantage for Lafarge Pitt River Quarry is better maintenance scheduling. Because of increased production rates, the quarry can afford regular planned maintenance interruptions, which also avoid costlier overtime repair work.
Systematically maintaining the machinery has other positive implications for the company as now the maintenance occurs regularly, budgeting for it is regular, too, with the cost being spread throughout the year rather than coming in surges at sometimes inconvenient times.
The CH660 also benefits from more efficient power transfer to the crushing chamber, deriving from Sandvik’s Hydroset technology coupled with the ASRi automation system that maintains optimum reduction despite wear.