A modular mobile jaw crusher is being offered by a new manufacturer to the market. Based in Britain, Crushers UK has designed its track-mounted, single toggle jaw Hercules 1830 machine to be easy to transport and make ready for use. The machine features a crusher opening measuring 800x500mm and can produce stone sizes from 25-100mm, with a maximum throughput of 100tonnes/hour.
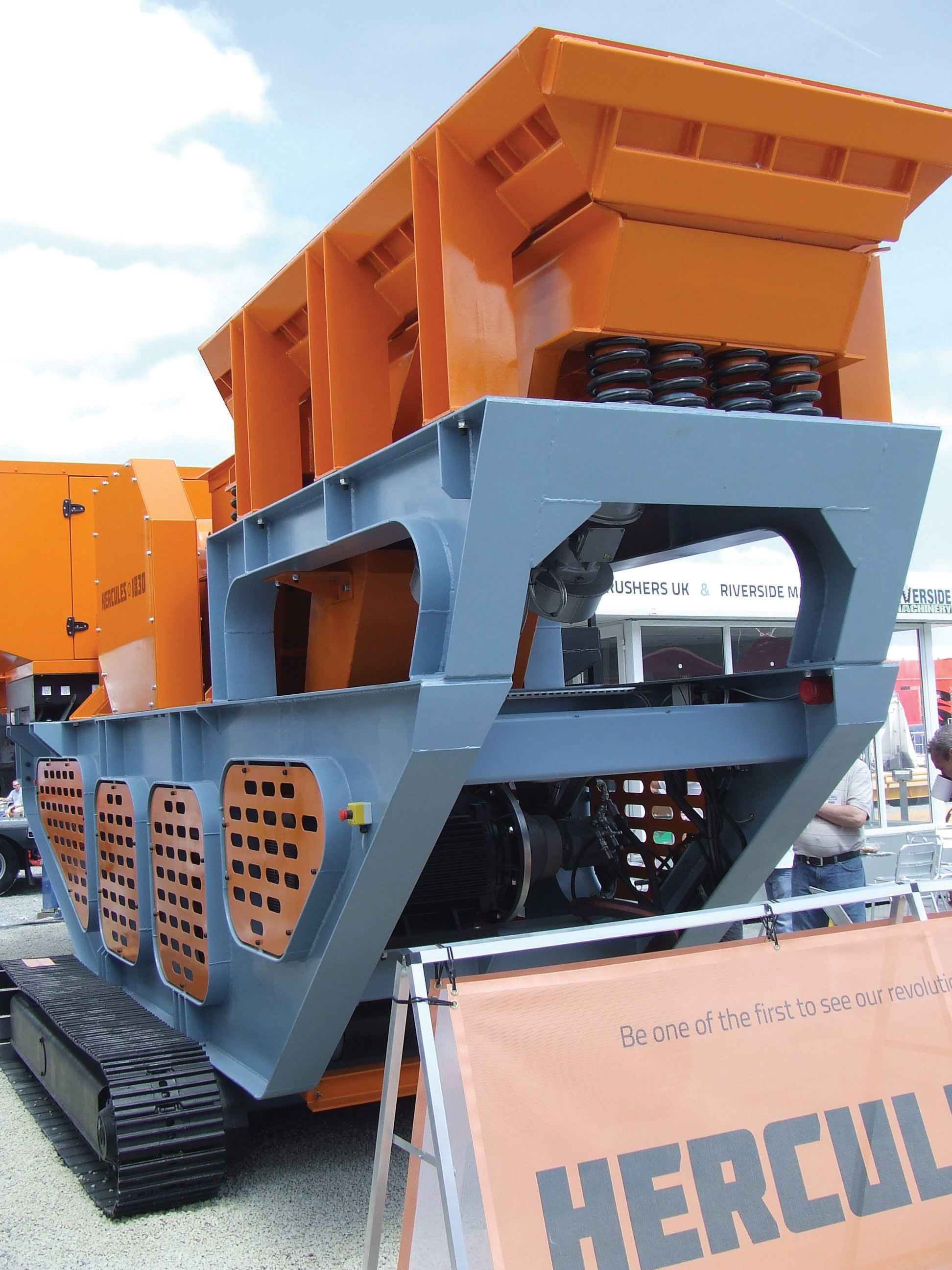
Highly mobile, the modular Hercules 1830 jaw crusher from Crushers UK offers ease of transport combined with high performance
A modular mobile jaw crusher is being offered by a new manufacturer to the market. Based in Britain, 2359 Crushers UK has designed its track-mounted, single toggle jaw Hercules 1830 machine to be easy to transport and make ready for use. The machine features a crusher opening measuring 800x500mm and can produce stone sizes from 25-100mm, with a maximum throughput of 100tonnes/hour. Power comes from a 257 John Deere diesel rated at 91kW and which meets the current European emissions requirements, although drive to the various components is all electric rather than hydraulic.
The firm's director, Greg Shipley, explained that the electric drive concept is simpler, easier to maintain and more compact. Although Crushers UK is new to the industry as a manufacturer the firm has been involved in supplying crusher components to the sector and has plenty of experience. It is because of this depth of experience that Shipley was able to design the Hercules 1830, starting from his own rough sketches on a chalkboard. Similarly, the components selected, such as the Eriez magnetic separation unit and generator from Advanced Diesels, are all proven units from well recognised suppliers. The jaw configuration, with its upward movement, has been designed for an optimum trade-off between maximum breaking efficiency as well as minimum wear life. Weighing in at 20tonnes the Hercules 1830 features an 800mm wide conveyor with electric drive and can discharge material at up to 2.4m high. The modular layout brings benefits and Shipley said, "You can unbolt the tracks and have it as a static machine."
A small portable control unit allows remote operation for safety and this has a simple switch to change between crushing and travel modes. Meanwhile the grizzly is located so as to ensure fines will drop out before reaching the crusher. The machine has been designed so that it can be manufactured in batches from a small production facility and Shipley said, "It's all modular and built from standard materials and standard plate sizes. If we do get sufficient orders we do have a facility lined up."
The firm's director, Greg Shipley, explained that the electric drive concept is simpler, easier to maintain and more compact. Although Crushers UK is new to the industry as a manufacturer the firm has been involved in supplying crusher components to the sector and has plenty of experience. It is because of this depth of experience that Shipley was able to design the Hercules 1830, starting from his own rough sketches on a chalkboard. Similarly, the components selected, such as the Eriez magnetic separation unit and generator from Advanced Diesels, are all proven units from well recognised suppliers. The jaw configuration, with its upward movement, has been designed for an optimum trade-off between maximum breaking efficiency as well as minimum wear life. Weighing in at 20tonnes the Hercules 1830 features an 800mm wide conveyor with electric drive and can discharge material at up to 2.4m high. The modular layout brings benefits and Shipley said, "You can unbolt the tracks and have it as a static machine."
A small portable control unit allows remote operation for safety and this has a simple switch to change between crushing and travel modes. Meanwhile the grizzly is located so as to ensure fines will drop out before reaching the crusher. The machine has been designed so that it can be manufactured in batches from a small production facility and Shipley said, "It's all modular and built from standard materials and standard plate sizes. If we do get sufficient orders we do have a facility lined up."