Now part of the Wirtgen Group, Brazilian firm CIBER produces asphalt plants for the Latin American market and has developed a series of technological innovations for this sector. The firm is now introducing its new iNOVA 2000 plant design that it will offer for Latin America. The firm has developed the machine based on its experience of the sector, while also incorporating the latest advances in asphalt plant technology. The plant has benefited from the firm’s research into the needs of different asph
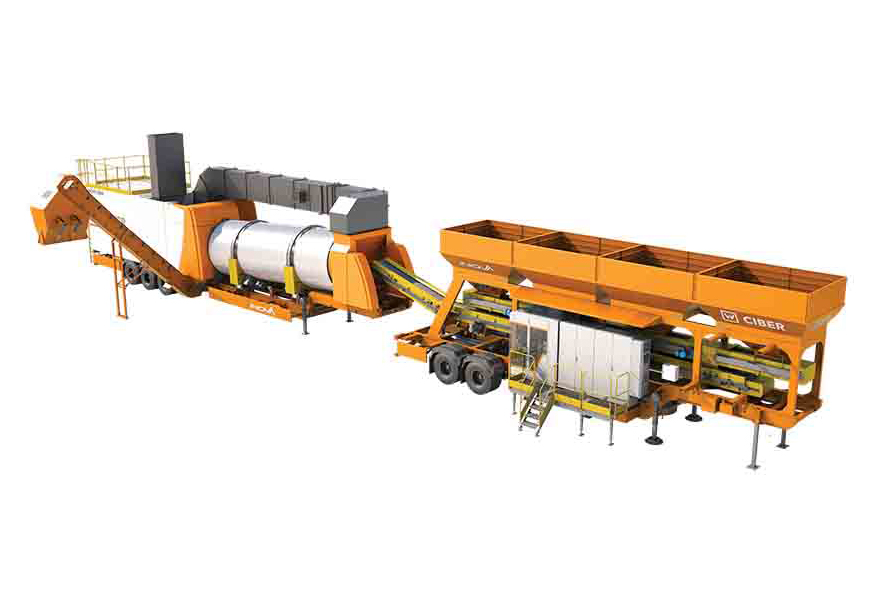
CIBER’s new iNOVA plant is said to offer versatility and productivity
Now part of the 364 Wirtgen Group, Brazilian firm 6241 CIBER produces asphalt plants for the Latin American market and has developed a series of technological innovations for this sector
The firm is now introducing its new iNOVA 2000 plant design that it will offer for Latin America. The firm has developed the machine based on its experience of the sector, while also incorporating the latest advances in asphalt plant technology.
The plant has benefited from the firm’s research into the needs of different asphalt mixes and can be adapted to suit the material feed and product specification requirements.
According to CIBER, its iNOVA 2000 plant can deliver high productivity, no matter which feed materials and mix design is being used. The new unit offers a large production capacity for a mobile unit, while also being able to deliver special mixes to tight specifications. The firm said that the plant is also highly fuel efficient, while being easy to operate and maintain.
CIBER said that the iNOVA 2000 combines the versatility of a mobile plant with high production capacity. The plant can be transported and installed in two chassis sections and can deliver an output from 100 to 200tonnes/hour. The modular design helps lower transport costs, while the use of pre-assembled components means that installation time is quicker than for comparable plants with the same production output according to CIBER. The modular design is also said to allow the plant to be adapted to suit the requirements of most construction sites, further simplifying installation.
The firm said it has optimised the design so as to minimise energy consumption when drying aggregates. Aggregate drying time control is achieved by varying the dryer drum rotating speed. This ensures an accurate drying time for each type of aggregate, lowering fuel consumption. The plant also has an automatic, close loop control governing the flow to the burners. The exhaust provides only the correct quantity of air for the burner system, reducing fuel consumption and optimising combustion. The CIBER’s Total Air burner also heats just the air required for combustion in the drum, further lowering fuel consumption.
The company claimed that the heat-exchange process between the burner and the aggregate has been optimised to deliver high mix quality, while providing maximum thermal efficiency. According to CIBER, the iNOVA 2000 delivers high efficiency whether the unit is producing conventional dense mixes or special mixes such as SMA. Another key feature of the plant is its external pug mill mixer, which has a dry mixing stage. CIBER said that this design ensures aggregate homogeneity before adding bitumen and any additives, a feature required for the production of dense mixes or SMA mixes needing cellulose fibres. A user can also vary the aggregate mixing time according to mix requirements.
The sophisticated automatic controls use industrial computers and provide the new EasyControl system, which is said to make the plant easier to operate. The system offers computerised control of production, with features including automatic variation of flame intensity to match aggregate heating needs. Maintenance needs have been reduced, with longer lasting wear components, such as mixer blades with a new geometry to reduce internal wear. Components are made from materials with a high abrasion resistance while the sleeves can be replaced quickly, lowering downtime. Sophisticated fault-diagnosis technology also speeds troubleshooting and reduces downtime.
The firm is now introducing its new iNOVA 2000 plant design that it will offer for Latin America. The firm has developed the machine based on its experience of the sector, while also incorporating the latest advances in asphalt plant technology.
The plant has benefited from the firm’s research into the needs of different asphalt mixes and can be adapted to suit the material feed and product specification requirements.
According to CIBER, its iNOVA 2000 plant can deliver high productivity, no matter which feed materials and mix design is being used. The new unit offers a large production capacity for a mobile unit, while also being able to deliver special mixes to tight specifications. The firm said that the plant is also highly fuel efficient, while being easy to operate and maintain.
CIBER said that the iNOVA 2000 combines the versatility of a mobile plant with high production capacity. The plant can be transported and installed in two chassis sections and can deliver an output from 100 to 200tonnes/hour. The modular design helps lower transport costs, while the use of pre-assembled components means that installation time is quicker than for comparable plants with the same production output according to CIBER. The modular design is also said to allow the plant to be adapted to suit the requirements of most construction sites, further simplifying installation.
The firm said it has optimised the design so as to minimise energy consumption when drying aggregates. Aggregate drying time control is achieved by varying the dryer drum rotating speed. This ensures an accurate drying time for each type of aggregate, lowering fuel consumption. The plant also has an automatic, close loop control governing the flow to the burners. The exhaust provides only the correct quantity of air for the burner system, reducing fuel consumption and optimising combustion. The CIBER’s Total Air burner also heats just the air required for combustion in the drum, further lowering fuel consumption.
The company claimed that the heat-exchange process between the burner and the aggregate has been optimised to deliver high mix quality, while providing maximum thermal efficiency. According to CIBER, the iNOVA 2000 delivers high efficiency whether the unit is producing conventional dense mixes or special mixes such as SMA. Another key feature of the plant is its external pug mill mixer, which has a dry mixing stage. CIBER said that this design ensures aggregate homogeneity before adding bitumen and any additives, a feature required for the production of dense mixes or SMA mixes needing cellulose fibres. A user can also vary the aggregate mixing time according to mix requirements.
The sophisticated automatic controls use industrial computers and provide the new EasyControl system, which is said to make the plant easier to operate. The system offers computerised control of production, with features including automatic variation of flame intensity to match aggregate heating needs. Maintenance needs have been reduced, with longer lasting wear components, such as mixer blades with a new geometry to reduce internal wear. Components are made from materials with a high abrasion resistance while the sleeves can be replaced quickly, lowering downtime. Sophisticated fault-diagnosis technology also speeds troubleshooting and reduces downtime.