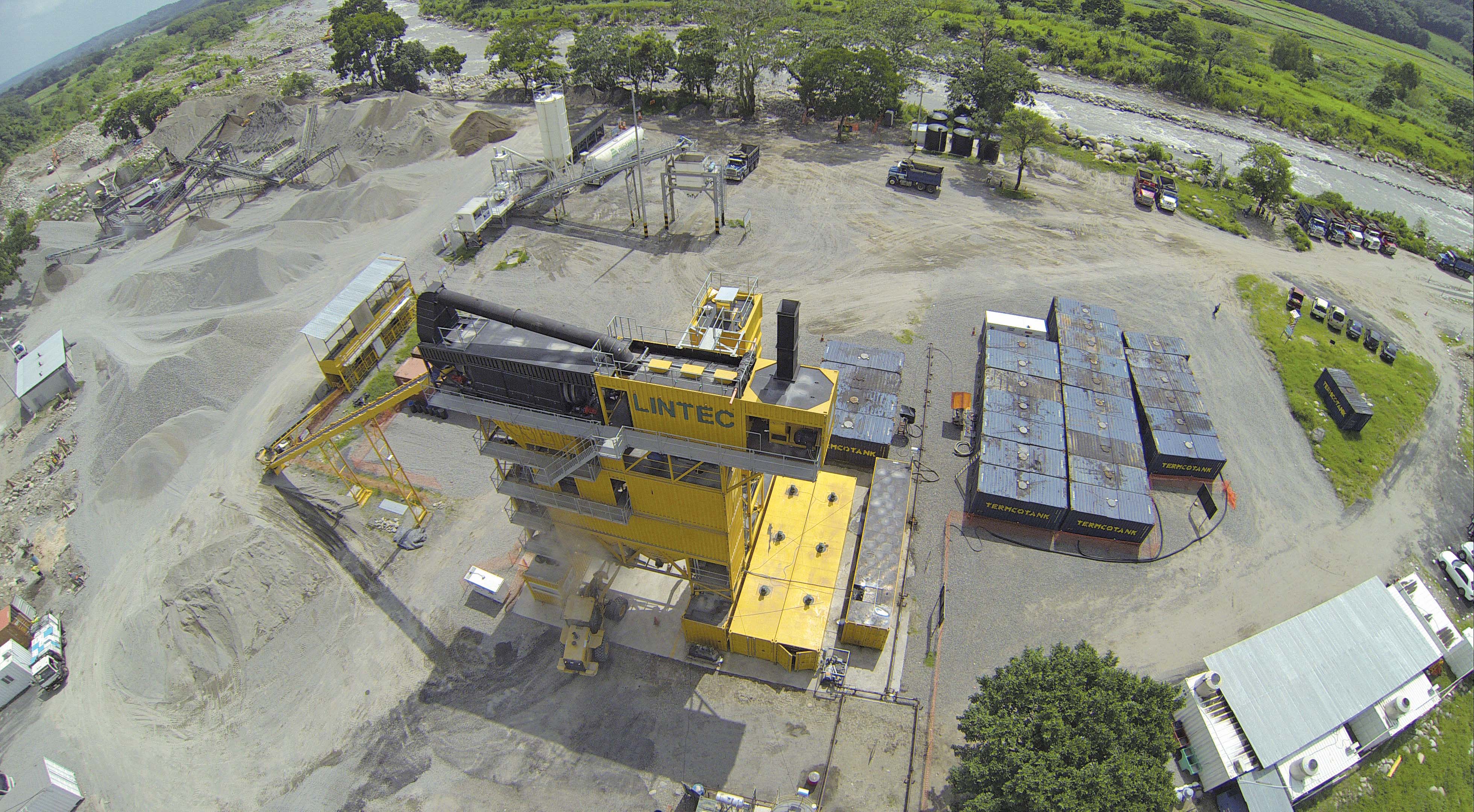
A new up to 180tonnes/hour
The new UltiMAP 2000 model which started work last year in the Lagos suburb of Imota is the result of Lagos State Public Works (LSPW) emphasising their need of a highly flexible plant allowing high quantity usage of RAP [Recycled Asphalt Pavement], in order to break with a countrywide tradition of failing to recycle existing asphalt pavement. To meet this request, Marini’s technical team firstly decided on a plan whereby the client would pre-treat the RAP in order to control the quality of old bitumen and the size of recovered aggregates (the highest quality of the final product has always been a priority in the technical discussion) and then use a bespoke Marini UltiMAP 2000 plant solution with one line to the dryer (recycling ring) offering up to 35% recycling.
Other important points evaluated during the negotiations between Marini’s Nigerian dealer, HMD, and LSPW were the possibility to control, in the best possible way, the metering processes (for single components), the ability to frequently change the formula in production, and the possibility of producing small quantities of asphalt. There was also said to be a focus on maximum plant efficiency, the production of special products (possibility to use coloured additives and fibres), and the environment and working conditions.
LSPW requested a special bitumen supply facility, and the UltiMAP 2000 plant at Imota has a total bitumen storage capacity of 300tonnes, granted by six vertical tanks. The operator can easily change the type of bitumen during the HMA (hot mix asphalt) production and can also order the bitumen from the supplier who will deliver within an agreed timeframe. These peripherals are said by Marini to be common to all asphalt plant supply deals, but the request was for new design tanks with low thermal bridges as they have to consider production process optimisation, the environment and, of course, the most economical mode of production in terms of efficient use of raw materials.
Marini says it is confident that more contractors will now follow LSPW’s example and implement road maintenance programs that respect the environment, while also reducing equipment fuel consumption and emissions, and maximising the quality of the final product.
The customer, Zagrebake Ceste, based in Zagreb, tasked the German asphalt plant manufacturer with producing a plant that should set new standards for Croatia in performance and technical maturity, while, at the same time, needing to be completed and operational in just a few months.
The plant devised by Benninghoven has a parallel drum for processing up to 80% hot recycling and a filler/water mixer with a capacity of 20tonnes/hour to reduce the formation of dust while loading the filler. All drives over 15kW are equipped with a soft starter, thus allowing for energy-efficient plant operation. The use of frequency converters offers further potential savings and optimises the precise control of the drives. Additionally, all the plant’s motors run in the energy efficiency class ie2.
With an 800mm wide conveyor belt, the stone is fed in into the new plant’s drying drum in order to be heated and dried by burning environmentally friendly natural gas. The Benninghoven filter technology Pure Air ensures, thanks to the highest ecological standards, that emissions are reduced to an absolute minimum. Additionally, splitter silencers were installed to reduce noise emissions.
The new plant’s screening machine with six screening decks is said to provide perfect separation of the different grain sizes and distributes the material to the subsequent storage in the various hot mineral silos with a total capacity of 80tonnes.
The precise dosage given by the Benninghoven weigh hopper system is said to ensure high accuracy and provides the foundation for the claimed excellent recipe of the final product.
The Zagrebake Ceste plant’s in-built Benninghoven BLS 3000 control system enables the operator to take control of the entire asphalt plant with just a few mouse clicks. With the BLS 3000, all parameters of the production can be evaluated individually in order to achieve perfect transparency of the cost. The breakdown and the possibilities for exploitation of the control system’s database was said to be an important, if not the most important, criteria in Zagrebake Ceste’s decision to purchase the asphalt plant.
Delivery of the new plant was further complicated as the project timescale fell during a period of time when Croatia was not part of the
Two 120tonnes/hour
Odebrecht are said to have been attracted to the modular concept of the Lintec plants, which enables easy, safe and economical transport of the containerised plant components as well as a quick assembly of the plant at the jobsite. They also have previous experience of successfully deploying Lintec plants on other significant road projects in Central and South America.
Experienced Lintec engineers accompany the set-up and training period on-site and are always available for service assignments as well as for support in case the plants should be required for a different project at a different destination.
Both Lintec asphalt mixing plants being used on the Centro Americana 2 Highway are equipped with integrated hot storage silo, external filler silo, light oil tank and bitumen tanks with agitators amongst other components according to the specific requirements of this project.
Odebrecht is involved in recovery and duplication work on 140km of the overall 300km long Centro Americana 2 Highway (CA-2), which traverses the southern part of the Guatemalan territory from the border with El Salvador to Mexico. The road plays a crucial role in the country’s logistics, since it said by government stats to transport the equivalent of 65% of Guatemala’s GDP (Gross Domestic Product) in the form of products for export and domestic consumption. The US$384 million CA-2 Highway contract is one of the largest investments made until now by the Guatemalan government.
The completion of the CA-2 Highway project creates some major challenges for the team due to the contractual term and climate and geography conditions. The rainy periods in the region, for example, which extend from May to October, have rainfall rates between 4,000 and 5,000mms/year. Even under these conditions, the work must be completed by June 2016. In order to overcome these difficulties, the project has been organised along three stretches extending approximately 45km each with 18 simultaneous work fronts engaged in earth levelling, bridge construction and paving activities.
The asphalt concrete used for the paving is being produced at the two industrial centres installed along the banks of the Nahualate and Ocosito rivers. They are installed at strategic sites to facilitate logistics and support the production of the paving teams. The field teams are also working to build eight bridges. By 2016, 76 bridges should be completed. The San Francisco Bridge – the first to be delivered in April 2014 – represented a milestone in the advancement of the CA-2 construction work.
One Brazilian example is at Transcarioca in Rio de Janeiro during what was one of the main mobility works in the city ahead of the 2014 World Cup and 2016 Olympic Games. The avenue is being extended by 39km, cutting across Rio, connecting Barra da Tijuca to Ilha do Governador. Ciber’s UACF 17 P2 Advanced line plant is creating asphalt for the project’s paving teams based on a German technique called SMA (Stone Mix Asphalt), a special type of asphalt mix that results in a pavement with a much higher useful life and greater superficial roughness than those achieved through traditional techniques. This is said to result in a better cost/benefit relationship and higher safety for users.
Still in the Rio de Janeiro area, Ciber plants are also operating at Arco Metropolitano, a road that that is being constructed in the area surrounding metropolitan Rio to provide an alternative route for the intense vehicle traffic crossing the city in order to reach other regional cities and towns. As part of the rigid road construction requirements are key environmental protection guidelines. The filtering system of the one Ciber UACF 17 P1 and one UACF 15 P1 Advanced Line plants being deployed allows for pollution emissions significantly below local regulations. The new Arco Metropolitano route will connect Rio to the cities of Itaboraí, Guapimirim, Magé, Duque de Caxias, Nova Iguaçu, Japeri, Seropédica and Itaguaí.
Present in all countries in Latin America, Australia and South East Asia, Ciber’s UACF 17 P2 plant has also recently been deployed in Cairo, Egypt. According to Cristiano Lameira, the local sales manager for Ciber Road Equipment, 2,000tonnes/asphalt was produced in just two working days by Ciber’s customer.
In Mexico, the Ciber asphalt plant model UACF 19 P2 has been recently installed in order to produce asphalt to pave a road that will significantly reduce the distance, and, as such, people’s driving time, between the cities of Mérida and Playa Del Carmen.
The Advanced Line plants’ increased aggregates’ drying time meant it was possible to completely dry the region’s high water apportion limestone origin material during the Mexican road paving project. The slow and gradual drying of aggregates in the plant is said to have allowed for a great adhesiveness to bitumen.
According to Rafael Zuchetto, Ciber’s Latin America sales manager, the UACF 19 P2 is a very productive machine with great adaptation to different climate conditions. "It is the Ciber plant with the highest productivity. The reason is that it is fully mobile and easily transported from one site to another. It was chosen because of its versatility and robustness, delivering high production in the contrasting climates of different Mexican regions.”
Ciber’s iNova asphalt plant line is also in demand in Latin America. Authorities in the Venezuelan city of Guacara recently invested in an UACF iNova 1200 P1 plant. Located in the state of Carabobo, Guacara officials are said to have chosen an iNova line plant due to their singular technology and maximum mobility. Ciber says the equipment stands out due to its four dosing silos and other key features such as its pick-up system for monitoring the belts' speed and the transmission of dosing data through digital signal. This is said to ensure the project’s correct ratio between aggregates and the perfect percentage of PAC (Pre-Placed Aggregates Concrete). Like the Advanced Line plants, the iNova’s longer drying times allow for even more poriferous aggregates to be dried. With the iNova plants, there is also the possibility of inserting RAP (Reclaimed Asphalt Pavement) in the so called recycling ring. Additionally, the iNova line has a pug-mill type external mixer with a novel system for using dry mix (previous aggregates mix). The use of dry mix, says Ciber, was only previously possible in batch plants.
Luciano Sackis, Ciber’s product support co-ordinator, who was at the Venezuelan UACF iNova 1200 P1 plant delivery ceremony, says Ciber place great emphasis on the quality of its plant installations.
Reducing emission values and costs plays an ever greater role in the construction of asphalt mixing plants.
The reasons that led to the development and marketing of the EasyBatch 140 model are based on the success of the EasyBatch 90. However, Ammann says a growing number of its customers wanted a highly road-mobile batch plant with higher production rates for different reasons. Firstly, in some countries it is easier to obtain approval for the installation and operation of a road-mobile plant than for a stationary plant. Secondly, preparing the construction site is much cheaper, as no foundations are required in contrast to a conventional plant. Furthermore, installation does not require any cranes, which can be hard to access depending on the region. However, the key argument is the ability to quickly transfer asphalt production from one location to another without having to compromise on the hourly production output.
The EasyBatch 140 consists of two trailers: trailer ‘A’ contains the cold feed bin, dryer and filter, while trailer ‘B’ houses the aggregate elevator, screen, hot aggregate silo, buckets and mixer. The core components, such as the burner and mixer, are standard Ammann products, while the dryer and filter were developed specifically for the road-mobile plant.
The first plants have already been sold and others are in production. EasyBatch 140 plants went to Saudi Arabia, Turkey, Libya and Canada. The geographical features of the countries purchasing the first plants are said by Ammann to provide an indication of just how versatile the machine is when used in differing regions of the globe, and also its huge potential.The demands placed on Ammann’s new UniBatch plants, whose main purpose is the fulfilment of “standard specifications”, are said to be completely different. The principle of standardisation is based on the production of specific module elements in small series that are then assembled in accordance with incoming orders. This production method is said to allow for the efficient use of raw materials and results in a reduction of both costs and tooling times.
The UniBatch plant’s basic components consist of the three towers - T1, T2 and T3 - with a production output of 80-180tonnes/hour, 210-260tonnes/hour and 300-340tonnes/hour. They are complemented by various combinations of dryers, filters, hot aggregate silos and mixed mineral storage silos for dozens of potential configurations to meet the demands of our customers in the best way possible.
The three main configurations are based on modules that have many parts in common despite differences in design to reduce costs and optimise delivery times. The development and implementation of the UniBatch range is accompanied by various other projects aimed at increasing the efficiency of core components. The plant will, says Ammann, be even more compact and cost-effective as a result. The firm notes that until recently, dryers of the type 2390, for example, were installed in plants with an output of 210tonnes/hour. Today, they are installed in plants with an output of 260tonnes/hour, resulting in a claimed increase in output of around 25%.
The contribution this makes towards protecting the environment is said by Ammann to be substantial: in addition to fewer raw materials and reduced plant emissions during operation, the optimised dimensions of the ever more compact plant also results in fewer transport journeys. This means fewer vehicles are needed for delivery and the environment benefits as a consequence.
Finally, Ammann states that rationalised production processes enable better quality control. This is said to guarantee that all plants – regardless of where they are manufactured – always have the same outstanding quality.
UniBatch 260 asphalt mixing plants have recently been shipped to Azerbaijan, Iraq and Turkey; and an additional UniBatch 210P went to Russia. All plants are said to be operating successfully.