Ammann is showing its versatile UniBatch asphalt mixing plant at bauma China 2014. The equipment has been developed in response to market demand and a key feature is its high mobility. The firm says that this helps reduce overall emissions as well as operating and transport costs, when compared with conventional systems. The highly sophisticated asphalt mixing plant is able to meet targets for reduced emissions, as well as being a highly versatile and adaptable unit.
The firm says that the machine has been
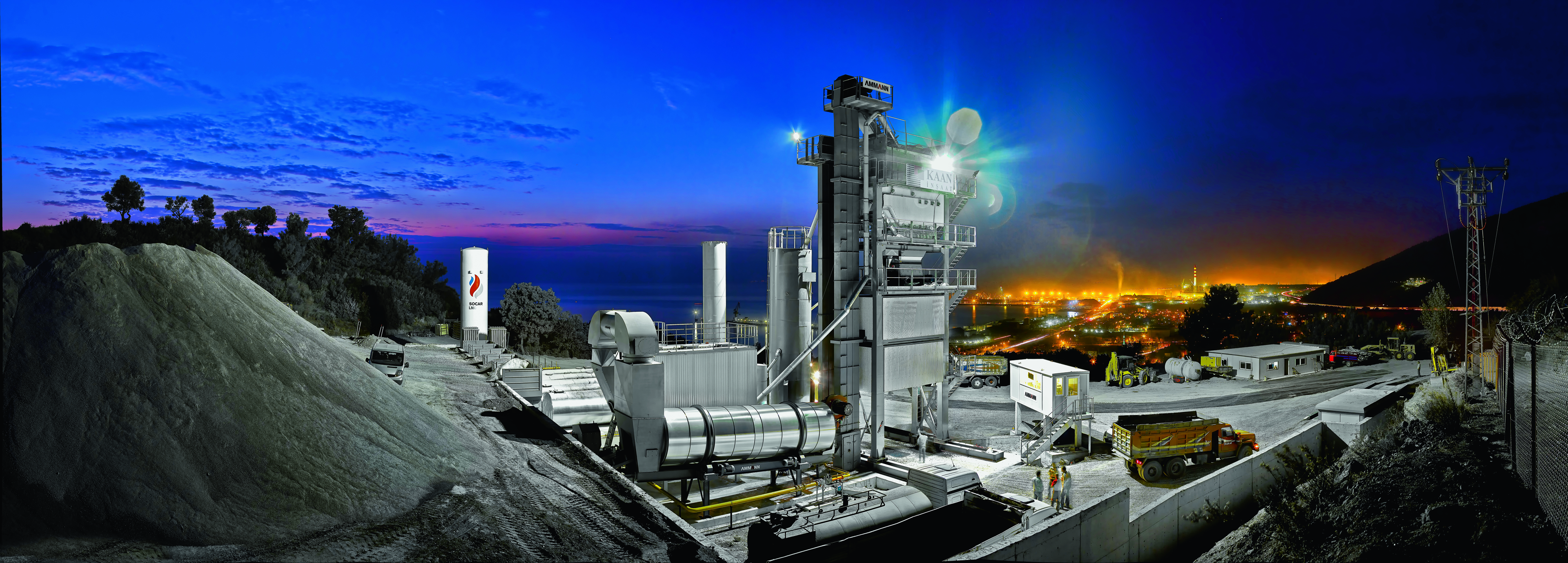
The UniBatch model range incorporates flexibility, extendibility and a larger selection of variants.
The firm says that the machine has been called the UniBatch as this highlights that it is built to standard specifications. The firm’s process of machine standardisation is based around a modular design concept that comprises a series of module elements. These elements are produced in small batches and are then assembled to meet incoming orders. This production method allows the efficient use of raw materials and results in a reduction of both costs and tooling times.
This new generation of plants was developed and designed by a team of German, Swiss and Italian engineers. Extensive experience acquired over many years is said to ensure that the UniBatch range meets the demands of every market. While the materials required for asphalt production are similar the world over, they may have different properties depending on the region. The local practices and processes relating to asphalt production also differ but as Ammann is an international manufacturer, the company can adapt its plants to suit local customer needs for every region.
The modular design is said to be crucial, with the plant’s basic components consisting of the three towers T1, T2 and T3. These offer production outputs of 80-180tonnes/ hour, 210-260tonnes/hour and 300-340tonnes/hour respectively. The units are also are complemented by various combinations of dryers, filters, hot aggregate silos and mixed mineral storage silos for dozens of potential configurations to meet the demands of the firm’s customers. Hot aggregate silos of 25–114tonnes are offered and featuring four, five or six chambers depending on the configuration, while the plant has the Ammann as1 control system.
The three main configurations are based on modules that also share many parts in common despite differences in design. The firm says that this strategy help to reduce costs and optimise delivery times. Various other concepts have also helped boost the efficiency of core components, while making the plants more compact and cost effective. In addition to using fewer raw materials and reducing plant emissions during operation, the optimised dimensions of the plant also helps cut transportation needs when moving the equipment from site to site.