Turkish firm E-MAK has a reputation for delivering innovative solutions to the industry, with its presence at the bauma exhibition in Munich providing further proof. The firm’s two latest bitumen storage developments could cut costs for plant operators substantially. The new Bi SAS 300 system from E-MAK is intended to cut the cost of bitumen storage by lowering heating bills. According to E-MAK’s chairman, S Nezir Gencer, the operators of most asphalt plants tend to focus on how much fuel the burners used t
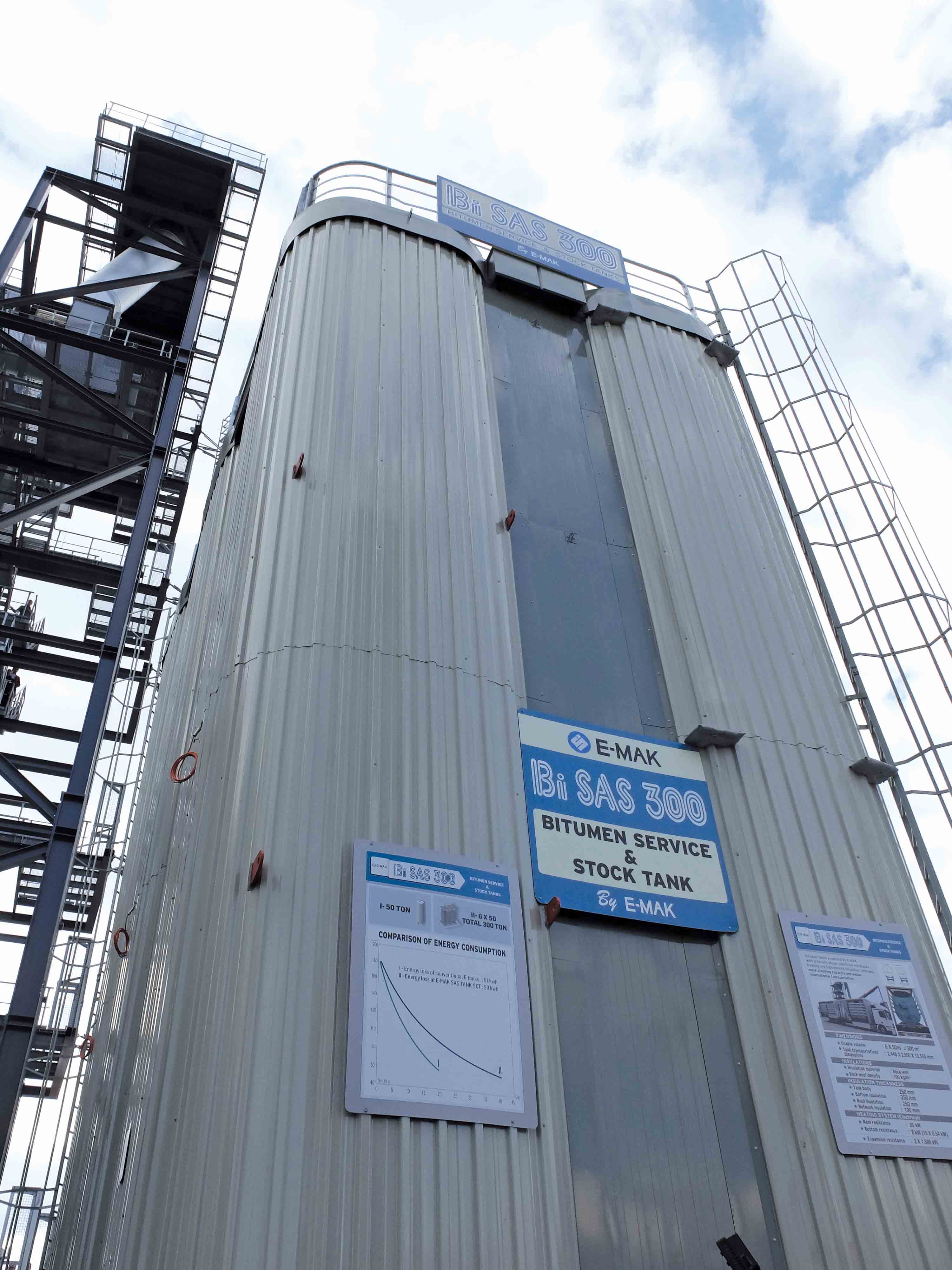
The Bi SAS 300 system developed by E-MAK can reduce heat losses from bitumen storage tanks
Turkish firm E-MAK continues with its innovations with new developments in bitumen storage - Mike Woof writes
Turkish firm208 E-MAK has a reputation for delivering innovative solutions to the industry, with its presence at the bauma exhibition in Munich providing further proof. The firm’s two latest bitumen storage developments could cut costs for plant operators substantially. The new Bi SAS 300 system from E-MAK is intended to cut the cost of bitumen storage by lowering heating bills. According to E-MAK’s chairman, S Nezir Gencer, the operators of most asphalt plants tend to focus on how much fuel the burners used to heat the asphalt. Employing efficient burners can help optimise performance and lower overall fuel consumption. But with regard to the plant’s entire fuel consumption, Gencer points out that it is also important to consider the fuel used to heat the bitumen storage system. It is worth noting that the bitumen tanks have to be heated constantly, even when the rest of the plant is not in operation.
The Bi SAS 300 system is intended to tackle this issue, supplying a more heat efficient concept for storing bitumen and can help lower a plant’s overall fuel bill. Sales representative Onur Recepgil said, “It’s not a matter of how to heat the bitumen but how to preserve the energy.”
According to E-MAK, around 60% of asphalt production facilities use a conventional hot oil burner heating system to maintain temperature for the bitumen storage tanks. Some of this heat is lost through the exhaust, with other major losses during the heat transfer process, as well as from the tanks themselves.
With tanks mounted conventionally, major heat losses can occur into the ground, with the mounting acting as a thermal bridge. Meanwhile losses from the tank sides can be substantial when the insulation is insufficient.
E-MAK has designed a new mounting system to address the thermal losses to the ground, isolating the tank from the ground with an aluminium and rockwool sandwich. A PLC system continuously monitors bitumen temperature in the tanks, using off-peak electric heating at night to reduce costs for the user.
The tanks themselves are mounted together inside a heavily insulated skin, so there is no wind generated, cooling air flow effect. With six tanks installed together, this provides storage for up to 300tonnes of bitumen. The concept is modular however and different numbers of tanks could be supplied as required.
The firm has proven the system at its own quarry close to Bursa. Assuming a surrounding ambient temperature of 10°C and a bitumen temperature of 180°C inside each tank, the firm says it would take 40 days for the tank temperature to drop to 60°C. According to E-MAK, the bitumen temperature with a conventional storage system would drop to 60°C within just 20 days.
The storage system also offers safety benefits as the tanks are shielded externally, so there is no chance of site personnel suffering burns. Because there are several tanks in each system users and can also store different bitumen grades separately, while agitators can also be fitted to tanks for PMB storage.
While the Bi SAS 300 system can be described as a logical development for lowering asphalt plant heating bills, then E-MAK’s other concept for bitumen storage is radical and all the more so as this is not being patented, allowing it to be implemented globally.
The idea is that bitumen storage costs can be reduced in very large tanks by reducing the amount of insulation. A conventional large bitumen installation will feature insulation all the way up the sides. However, for the E-MAK concept insulation is only required for a height of 2m from the bottom of the tank.
The heating coil is mounted centrally, raising the temperature of the bitumen in the centre of the tank to the required 120°C. But this heat energy only needs to be supplied centrally as the bitumen itself is a good heat insulator. This design allows the heat to rise so that the material can flow, however the heat distribution drops towards the external surface of the tank. And due to the insulation properties of the bitumen itself, there is no need for additional insulation for the walls of the tank.
The combination of the centrally mounted heated coil and the low thermal conductivity of the bitumen mean that comparatively low power demands are required to ensure that the material will flow from the tank when required. Overall, E-MAK believes this design could save in both tank construction costs and heating costs.
Turkish firm
The Bi SAS 300 system is intended to tackle this issue, supplying a more heat efficient concept for storing bitumen and can help lower a plant’s overall fuel bill. Sales representative Onur Recepgil said, “It’s not a matter of how to heat the bitumen but how to preserve the energy.”
According to E-MAK, around 60% of asphalt production facilities use a conventional hot oil burner heating system to maintain temperature for the bitumen storage tanks. Some of this heat is lost through the exhaust, with other major losses during the heat transfer process, as well as from the tanks themselves.
With tanks mounted conventionally, major heat losses can occur into the ground, with the mounting acting as a thermal bridge. Meanwhile losses from the tank sides can be substantial when the insulation is insufficient.
E-MAK has designed a new mounting system to address the thermal losses to the ground, isolating the tank from the ground with an aluminium and rockwool sandwich. A PLC system continuously monitors bitumen temperature in the tanks, using off-peak electric heating at night to reduce costs for the user.
The tanks themselves are mounted together inside a heavily insulated skin, so there is no wind generated, cooling air flow effect. With six tanks installed together, this provides storage for up to 300tonnes of bitumen. The concept is modular however and different numbers of tanks could be supplied as required.
The firm has proven the system at its own quarry close to Bursa. Assuming a surrounding ambient temperature of 10°C and a bitumen temperature of 180°C inside each tank, the firm says it would take 40 days for the tank temperature to drop to 60°C. According to E-MAK, the bitumen temperature with a conventional storage system would drop to 60°C within just 20 days.
The storage system also offers safety benefits as the tanks are shielded externally, so there is no chance of site personnel suffering burns. Because there are several tanks in each system users and can also store different bitumen grades separately, while agitators can also be fitted to tanks for PMB storage.
While the Bi SAS 300 system can be described as a logical development for lowering asphalt plant heating bills, then E-MAK’s other concept for bitumen storage is radical and all the more so as this is not being patented, allowing it to be implemented globally.
The idea is that bitumen storage costs can be reduced in very large tanks by reducing the amount of insulation. A conventional large bitumen installation will feature insulation all the way up the sides. However, for the E-MAK concept insulation is only required for a height of 2m from the bottom of the tank.
The heating coil is mounted centrally, raising the temperature of the bitumen in the centre of the tank to the required 120°C. But this heat energy only needs to be supplied centrally as the bitumen itself is a good heat insulator. This design allows the heat to rise so that the material can flow, however the heat distribution drops towards the external surface of the tank. And due to the insulation properties of the bitumen itself, there is no need for additional insulation for the walls of the tank.
The combination of the centrally mounted heated coil and the low thermal conductivity of the bitumen mean that comparatively low power demands are required to ensure that the material will flow from the tank when required. Overall, E-MAK believes this design could save in both tank construction costs and heating costs.