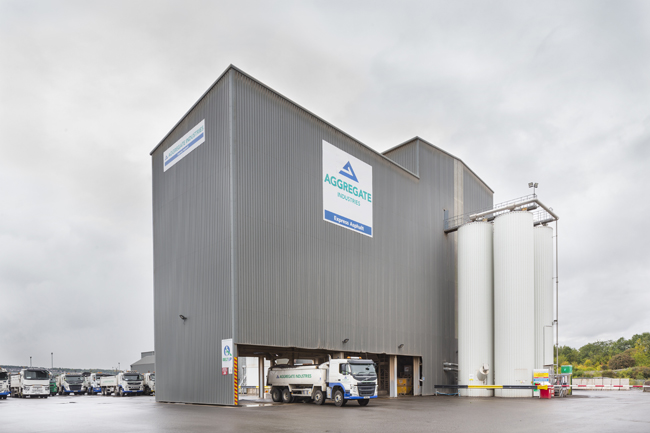
Delivering on both fronts is no small task, but the firm has achieved that at its facility in Sheffield in the UK. RAP utilisation is high and meets the company’s sustainability goals. Production has been good, too; nearly 2 million tonnes of asphalt have been created since the Sheffield plant was commissioned in 2013. Stott credits many sources: operators; other staff; suppliers; and the plant itself – an
He said that a key feature is the plant’s operating system, the Ammann as1 Control System. The supplier also trained the production staff when the plant was installed so as to help optimise operations, with 24-hour emergency support available, which can be crucial when making changes and identifying problems according to Stott. The system also includes modules, additional software options that help plants deliver more value for certain applications.
The EcoView module helps to minimise energy waste, with the display showing operators and adjustments that need to be made. “EcoView allows for real-time reporting and monitoring of energy consumption and raw material use,” Stott said. “This gives operators the data they need to make decisions around throughput and material control to maximise savings and efficiencies.”
EcoView also determines the values of emitted carbon dioxide and calculates energy costs that result when adjustments are made and operations become more efficient.
“It is designed to ensure that RAP addition, and binder saving, are always maximised,” Stott said. “This gives operators the confidence to keep throughput high while maintaining quality as the overarching priority.”
“Having real-time information keeps the operators one step ahead at all times,” he said. “It allows them to keep throughput high while maximising RAP addition without compromising quality. This, in turn, ensures that efficiency is excellent and therefore profitability is maximised.”
The as1 Control System, including EcoView and RAD modules, collects data at all stages of the manufacturing process. Some information is relayed to operators in real time so they can adjust to maximise fuel usage and achieve other efficiencies.
In addition, data is stored and processed to provide insight into plant operations, Stott said. “All levels of personnel at the facility gain something from the reports. The operators can monitor their own performance. Management can get details regarding usage and efficiency. All of the details from the suite of reports are used to drive improvements and plant efficiency.”
Aggregate Industries uses the reports on a daily, weekly and monthly basis, he said. “The biggest win we have identified from the reports is the detailed information surrounding RAP addition,” Stott said. “The RAP usage report allows us to identify every missed opportunity to improve the cost-savings the addition of RAP gives us. It also drives improvements for how we control RAP.”