An eye-catching state-of-the-art asphalt plant is making a big impact in South East Asia, while other new and proven asphalt plant technology remains in demand in Europe and other continents. Guy Woodford reports Marini China has ventured out of its traditional Chinese market to deliver to a Singaporean customer what is claimed to be Asia’s largest asphalt plant. An impressive 45m tall and capable of producing 360tonnes/hour, the plant model was in response to Ley Choon Group’s request for a new plant ahead
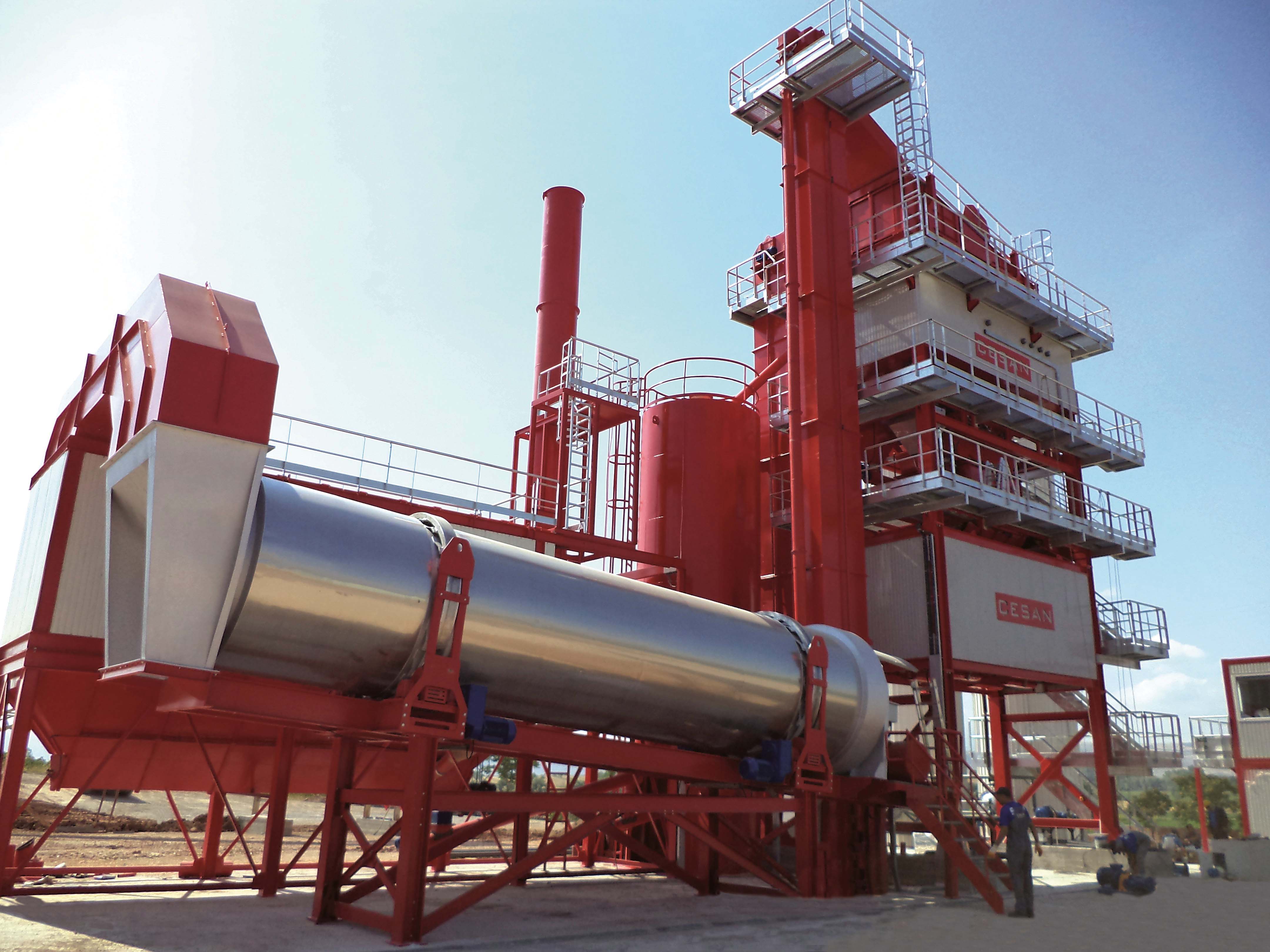
Çesan has recently sold its mobile yet still high quantity per hour bauma 2013-launched King Batch 280 plant to Turkish firm Tokat Kemer Insaat
An eye-catching state-of-the-art asphalt plant is making a big impact in South East Asia, while other new and proven asphalt plant technology remains in demand in Europe and other continents. Guy Woodford reports
273 Marini China has ventured out of its traditional Chinese market to deliver to a Singaporean customer what is claimed to be Asia’s largest asphalt plant. An impressive 45m tall and capable of producing 360tonnes/hour, the plant model was in response to Ley Choon Group’s request for a new plant ahead of its time that didn’t compromise on technology. Following an in-depth analysis of existing technical solutions, Ley Choon is said to have submitted a complex set of specifications to Marini, incorporating all of its requirements.
The new Marini 360tonnes/hour plant is capable of using three recycling techniques: recycling by materials introduction into the recycling ring of the dryer (a 35% recycling rate); by adding recycled materials directly into the mixer (25% recycling rate). By choosing a five-tonne mixer, oversized, a high production output of RAP can be maintained, including for formulas that incorporate reclaimed materials. Finally, recycling can be carried out in a double dryer drum, offering a RAP recycling rate of at least 60%.
A particularly appealing feature of this plant is said to be the possibility of combining recycling technologies in the dryer drum and recycling ring, in order to reach recycling rates of up to 80%.
The Marini AQUABlack foamed bitumen system has been supplied with the new 360tonnes/hour plant for the first time in Asia. Water is injected at very high pressure into a spray injector – known as the Foaming Gun. In this way the plant can produce Warm Mix Asphalt (120-130°C) in order to reduce the emissions and to be environmental-friendly.
The new plant for Ley Choon has 1,000tonnes of storage space in ten compartments. This novel design is said to make it possible for the hi-tech plant to swiftly supply all of the maintenance projects across Singapore; capitalise on short periods for applying asphalt between rain spells; and provide a whole range of necessary formulas.
After two months in operation, the plant has produced over 100,000tonnes of asphalt, with an average recycling rate of 45%.
With its high level technical team, Ley Choon wants to become a reference point for South East Asia and, thanks to the new Marini plant, appears to have taken a step forward towards the future.
1177 Lintec says its containerised asphalt mixing plants are selling well around the world due to what the German firm claims are their unbeatable transportation costs, short assembly times, competitive operation costs and lifetime mobility.
Among the latest installations have been a CSD 1510 with a capacity of 120tonnes/hour and integrated hot storage silo in Ecuador; a CSD 3000 with a capacity of 240tonnes/hour and external hot storage silo in Brazil; and a CSM 2500 with a capacity of 160tonnes/hour and external hot storage silo in Serbia.
The CSD series plants feature Lintec patented double screen drum technology combining the drying and screening process in one containerised unit. CSM series plants with conventional screening machine have a hot elevator to the screening unit.
Family-owned company CTB (Celu Tiltu Buvnieks) based in Latvia’s third largest city, Liepaja, are said to be continuing to benefit from investing in167 Benninghoven’s RA-150 RAP drum plant.
The firm had been successfully operating a Benninghoven TBA 3000 asphalt mixing plant since 2005. But when, in 2011, the market situation in Latvia became extremely difficult and asphalt quantity and prices hit a record low, CTB boss Gatis Zvirbulis saw it as the right time to make an investment to boost his company’s future competitiveness.
After ordering the RA-150 plant from Benninghoven in spring 2012, by the end of June that year Zvirbulis was overseeing its installation at CTB HQ. Production with around 150tonnes/hour of RAP content began in August 2012 after what was said to be a quite complicated installation, as CTB’s existing TBA 3000 asphalt plant was very busy and still had to produce all of the time. The Benninghoven engineers also had to work under pressure as Zvirbulis was keen to start with RAP as soon as possible to meet CTB’s ongoing project commitments.
Since its successful installation and to ensure optimum recycling quality, the RA-150 has been joined at CTB in Liepaja by a hired mobile Benninghoven Granulator System supplied by Siauliu Plentas of Lithuania. Producing excellent raw feed material for the RA-150 plant is said to be crucial to CTB’s successful use of its cutting-edge Benninghoven RAP drum plant.
Çesan recently sold one of its new King Batch 280 plants to fellow Turkish firm Tokat Kemer Insaat.
Launched at bauma 2013 in Munich, Germany the 280tonnes/hour plant has been designed for customers facing problems with a lack of infrastructure. Its compact form allows it to be transported anywhere in the world in as few as eight containers, greatly reducing transport costs. Çesan has also designed a mechanical base for the plant, allowing it to be constructed on any surface.
The King Batch 280’s composition in easy-to-move modules and the possibility to avoid using concrete foundation gives users, claims Çesan, the possibility of producing big quantities of asphalt not normally associated with a single mobile plant. A further advantage of the plant’s compact design is the ease of maintenance access.
Çesan has expanded its sales activities in Europe by opening a new company office and expanding its sales and after-sales network on the continent. The company plans to showcase its King Batch 280 plant at the Samoter-Asphaltica co-located shows in Verona, Italy from 8-11 May 2014.
The new Marini 360tonnes/hour plant is capable of using three recycling techniques: recycling by materials introduction into the recycling ring of the dryer (a 35% recycling rate); by adding recycled materials directly into the mixer (25% recycling rate). By choosing a five-tonne mixer, oversized, a high production output of RAP can be maintained, including for formulas that incorporate reclaimed materials. Finally, recycling can be carried out in a double dryer drum, offering a RAP recycling rate of at least 60%.
A particularly appealing feature of this plant is said to be the possibility of combining recycling technologies in the dryer drum and recycling ring, in order to reach recycling rates of up to 80%.
The Marini AQUABlack foamed bitumen system has been supplied with the new 360tonnes/hour plant for the first time in Asia. Water is injected at very high pressure into a spray injector – known as the Foaming Gun. In this way the plant can produce Warm Mix Asphalt (120-130°C) in order to reduce the emissions and to be environmental-friendly.
The new plant for Ley Choon has 1,000tonnes of storage space in ten compartments. This novel design is said to make it possible for the hi-tech plant to swiftly supply all of the maintenance projects across Singapore; capitalise on short periods for applying asphalt between rain spells; and provide a whole range of necessary formulas.
After two months in operation, the plant has produced over 100,000tonnes of asphalt, with an average recycling rate of 45%.
With its high level technical team, Ley Choon wants to become a reference point for South East Asia and, thanks to the new Marini plant, appears to have taken a step forward towards the future.
Among the latest installations have been a CSD 1510 with a capacity of 120tonnes/hour and integrated hot storage silo in Ecuador; a CSD 3000 with a capacity of 240tonnes/hour and external hot storage silo in Brazil; and a CSM 2500 with a capacity of 160tonnes/hour and external hot storage silo in Serbia.
The CSD series plants feature Lintec patented double screen drum technology combining the drying and screening process in one containerised unit. CSM series plants with conventional screening machine have a hot elevator to the screening unit.
Family-owned company CTB (Celu Tiltu Buvnieks) based in Latvia’s third largest city, Liepaja, are said to be continuing to benefit from investing in
The firm had been successfully operating a Benninghoven TBA 3000 asphalt mixing plant since 2005. But when, in 2011, the market situation in Latvia became extremely difficult and asphalt quantity and prices hit a record low, CTB boss Gatis Zvirbulis saw it as the right time to make an investment to boost his company’s future competitiveness.
After ordering the RA-150 plant from Benninghoven in spring 2012, by the end of June that year Zvirbulis was overseeing its installation at CTB HQ. Production with around 150tonnes/hour of RAP content began in August 2012 after what was said to be a quite complicated installation, as CTB’s existing TBA 3000 asphalt plant was very busy and still had to produce all of the time. The Benninghoven engineers also had to work under pressure as Zvirbulis was keen to start with RAP as soon as possible to meet CTB’s ongoing project commitments.
Since its successful installation and to ensure optimum recycling quality, the RA-150 has been joined at CTB in Liepaja by a hired mobile Benninghoven Granulator System supplied by Siauliu Plentas of Lithuania. Producing excellent raw feed material for the RA-150 plant is said to be crucial to CTB’s successful use of its cutting-edge Benninghoven RAP drum plant.
Çesan recently sold one of its new King Batch 280 plants to fellow Turkish firm Tokat Kemer Insaat.
Launched at bauma 2013 in Munich, Germany the 280tonnes/hour plant has been designed for customers facing problems with a lack of infrastructure. Its compact form allows it to be transported anywhere in the world in as few as eight containers, greatly reducing transport costs. Çesan has also designed a mechanical base for the plant, allowing it to be constructed on any surface.
The King Batch 280’s composition in easy-to-move modules and the possibility to avoid using concrete foundation gives users, claims Çesan, the possibility of producing big quantities of asphalt not normally associated with a single mobile plant. A further advantage of the plant’s compact design is the ease of maintenance access.
Çesan has expanded its sales activities in Europe by opening a new company office and expanding its sales and after-sales network on the continent. The company plans to showcase its King Batch 280 plant at the Samoter-Asphaltica co-located shows in Verona, Italy from 8-11 May 2014.