With new roads to be built and existing ones to be maintained, one company is predicting a big increase in asphalt production Asphalt plant manufacturer Ammann says that four factors in particular will shape the future of the asphalt industry. The company, which has sold its first JustBlack asphalt mixing plant to Costa Rica through its Spanish distribution partner, EMSA, says that many more roads have yet to be built in the world. "Building the global road network will provide work for many generations to
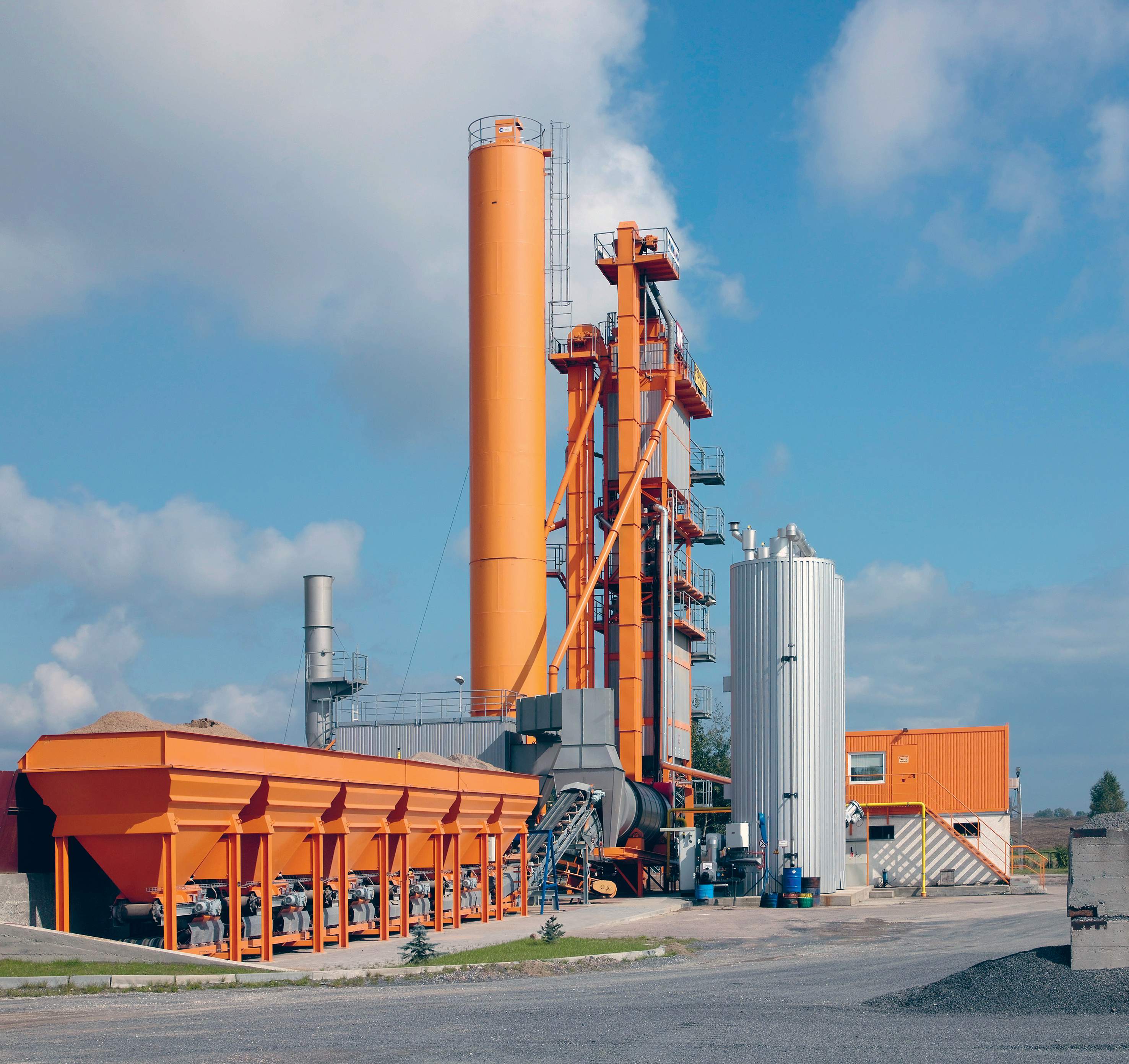
Ammann Group's "innovation": the Uniglobe 2 asphalt mixing plant
With new roads to be built and existing ones to be maintained, one company is predicting a big increase in asphalt production
Asphalt plant manufacturer"Building the global road network will provide work for many generations to come. Today's global roadmap shows two large and extensively developed road networks, those in the USA and 'old' Europe, each about 7 million kilometres in length.
"But to achieve global economic equilibrium, seven road networks of this sort, each with a length of 7 million kilometres, will be needed. In the years to come, the regions of China, India, South America, Africa, Asia and the Pacific will substantially expand and in some cases multiply their road networks," says Ammann Group, which obtained the first patent for asphalt mixing plants in 1908, and which is now introducing new models.
It also claims that the current global asphalt production of 1.4 billion tonnes/year will more than double in the coming years, brought about to some degree by a shift in asphalt production for road maintenance.
Increased requirements for environment-compatible production of asphalt mix call for new technologies, and "the industry is currently focusing on reducing the carbon footprint (the CO2 emissions) of an asphalt mixing plant.
"Further reductions in harmful substances, especially NOx and VOC, will be necessary in order to meet future standards."
The final point Ammann makes is that 100% recycled asphalt will become the global standard with road maintenance being closely linked to such recycling.
Meanwhile, the JustBlack plant in Costa Rica, ordered by
Until now, Costa Rica had always been a market for continuous asphalt mixing plants. It is described as an efficient start-up or basic asphalt mixing plant in the 80 to 240tonnes/hr category.
The company is also introducing the Uniglobe 2, which is capable of producing 120-320tonnes/hr. Mixer variations are 2tonnes, 3tonnes and 4tonnes, while hot aggregate silos are 30tonnes, 56tonnes, 80tonnes and 120tonnes, as single and double lane models.
The new SB-150 asphalt plant from SIM-Ammann rounds off the SpeedyBatch series, and is said to be small in comparison to other models, but as "big" as its older brothers with regard to technology and versatility, says SIM-Ammann.
The SB 150, which can produce up to 150tonnes/hr of asphalt at 3% humidity, consists of elements with a maximum width of 2.5m to provide greater versatility for transport by road or sea. Concrete foundations are not required: a compacted level surface as needed for previous models is sufficient.
Low-cost portability
The super-portable
"Building on producer feedback, we designed each self-contained load for quick set-up and tear-down," says David Emerson, director of engineering and product management.
At the heart of the design lies a new counter-flow drum mixer that Terex says blends the technologies of more than 100 years of asphalt production experience from the former CMI and Cedarapids brands.
The drum's new flight arrangement offers more efficient aggregate heating and asphalt mixing and is capable of making a wide variety of mix designs, including Stone Matrix Asphalts and Superpave, says Terex.
The drum is pitched at operating angle on its triple-axle chassis and has all ductwork pre-installed, significantly reducing set-up and teardown times. A powerful SJ-360 Hauck burner delivers 75 million BTUs of energy for aggregate heating, while its patented adjustable slinger increases/decreases drum length to tailor drying and mixing time to the producer's needs.
The base plant includes the necessary electronic connections to accept recycled asphalt (RAP), and its counter-flow technology enables the E225P drum "to run higher percentages of RAP than parallel flow designs, while still meeting tough environmental regulations." With its near 2m diameter and 12.3m length, the self-contained drum can be quickly moved with standard permits.
Terex says the plant's field-proven Roto-Aire RA218 baghouse has ample capacity to match drum mixer production, and integral to the baghouse, the fines return auger hydraulically pivots into position to interconnect the baghouse to the drum, resulting in no 'loose loads.'
A self-contained 45tonne self-erect and self-weighing silo is standard in the base plant configuration, and plant operation and asphalt mix designs are managed by the Terex Impulse X control system (it is capable of making any mix design for which the plant is configured).
"The E225P has only 20 plug-and-play cable connections, which is significantly less than traditional portable plants," says Emerson. The plant is set-up without the aid of a crane.
Roadbuilder Series
In the past two years, ADM has introduced more than 35 plants into the African market.
"The parallel flow system maximises heat transfer through the mix by utilising ADM's proven flight design to move the moisture-laden aggregate in a rotating veiled pattern away from the burner," says the company. A fuel-efficient Hauck StarJet burner produces the dryer flame, which efficiently dries and heats the material.
"Plant controls are sophisticated in their abilities, yet simple in operation. The plants can be operated by just one plant operator and one loader operator. Additionally, all plant components are standardised to ease maintenance and lessen downtime."
Both stationary and portable options are available. Portable plants can be easily installed for quick start-up, allowing a contractor to begin production within a few days. Options such as self-erecting silos require only one person and less than 15 minutes of set-up time. Other options include baghouse or wetwash systems, multiple cold feed bin systems and liquid asphalt cement tanks among others. ·