Asphalt plants were recently delivered for use in the biggest road construction project in Latin America. Meanwhile, a US navy base has just received a plant Guy Woodford reports Spanning around 1,000km, the Ruta del Sol highway in Colombia is the largest road build works currently taking place in Latin America. Brazilian company Odebrecht, part of the Ruta del Sol Concessionaire group working on sector 2 of the highway stretching 528km from Puerto Salgar to San Roque, connecting the capital Bogota to the
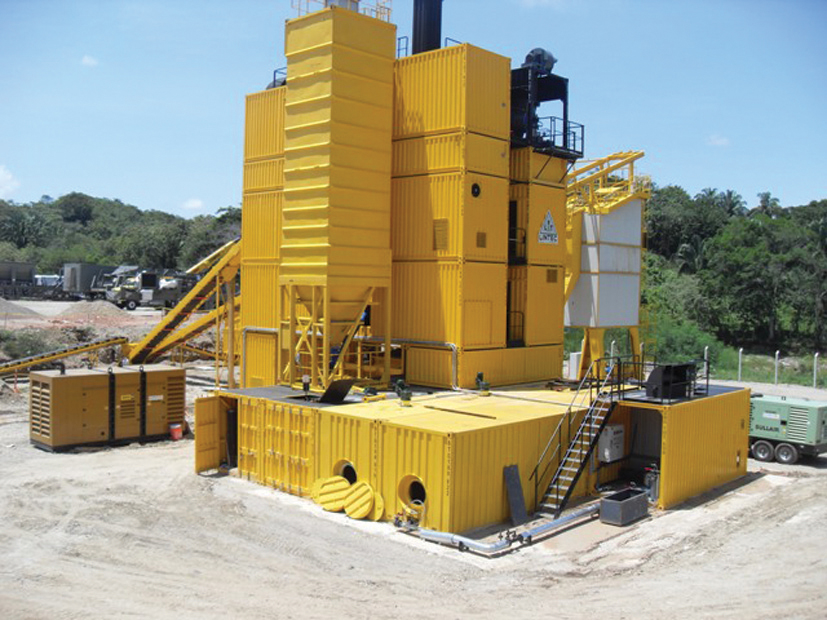
The CSD 1500, CSD 2500 (pictured) and CSD 3000 asphalt mixing plants from Lintec are being used during the Ruta del Sol highway construction project in Colombia
Asphalt plants were recently delivered for use in the biggest road construction project in Latin America. Meanwhile, a US navy base has just received a plant Guy Woodford reports
Spanning around 1,000km, the Ruta del Sol highway in Colombia is the largest road build works currently taking place in Latin America.
The CSD 1500 with 120tonnes per hour capacity; the CSD 2500 with 160tonnes per hour capacity; and the CSD 3000 240tonnes per hour capacity plants are fully equipped with bitumen and diesel tanks, foreign filler silos, hot storage silos and bitumen modification units. Types CSD 2500 and CSD 3000 also have fitted recycling systems. The modular construction of all three plants makes them easy and quick to erect and take apart.
Last month, the Ruta del Sol Concessionaire completed the first 10km of Ruta del Sol highway sector 2, between the municipality of Puerto Salgar and the district of Puerto Araujo.
An event to mark the initial sector 2 works, held at Puerto Salgar, included the presence of the Colombian Minister of Transportation, Germán Cardona Gutiérrez.
“This is the fifth time that I have visited the project and you can clearly see the intense pace of the operations,” said Gutiérrez.
“The construction work has already generated 10,000 direct and indirect job opportunities,” said Eder Paolo Ferracuti, president of the Ruta del Sol Concessionaire, who also attended the Puerto Salgar event.
Lintec recently launched a specially designed and fully containerised CDD 1200 GA Gussasphalt plant for the European market.
Capable of producing 20tonnes of Gussasphalt per hour (optional up to 20tonnes/hour), the plant was sold to the French company SMAC (belonging to the
The plant has a hot bin with one chamber and can take 15tonnes of material, while the recuperated filler silo is 11tonnes.
Other components include a quick mixer (1,000kg); an integrated bucket (1,000kg); an aggregate weigher (800kg); and a filler weigher with four inlets (200kg).
“Apart from this special solution Lintec is well known for fully containerised asphalt and concrete mixing plants. The Lintec product range covers asphalt mixing plants with a capacity from 80–400tonnes and concrete mixing plants with a capacity from 60–40m³/hour,” said Lintec.
The Gussasphalt Plant was developed together with Lintec’s partner company Linnhoff & Henne.
The new plant ensures, according to Fayat, optimum energy management when mixing aggregates, while also maintaining the ability to recycle materials according to typology.
The feed is conventional into the dryer tube for virgin materials – and into the continuous mixer, or both, for recycled materials.
Bitumen is introduced into the Retroflux or Recyclean dryer tube, or into the mixer, far away from the flame.
The benefits of this system are said to include zero emissions and no waste.
Fayat said that bitumen does not age prematurely because it is added to virgin aggregates + RAP at an ideally controlled temperature.
TThe COMPACT has two introduction/mixing sequences, one in the dryer and a second called pre-mixing (virgin and recycled aggregates). The second features 60 seconds of mixing with the addition of bitumen and other products in a 3.5metre long mixer.
Fayat has also incorporated a low mixer behind the dryer in order to have a direct feed into the mixer, eliminating the risk of time lag and guaranteeing correct bitumen dosage.
Supplied either as 100% new investment or as a retrofit on an existing plant, the versatile nature of the COMPACT system and projected savings in terms of maintenance costs are seen by Fayat as major justification arguments for contractors wishing to own a modern production tool for new material, while keeping ecological and environmental footprints to a minimum.
Last month, US-based
The plants produce 100 to 425tonnes per hour at what is claimed to be a very low cost per tonne. ADM have said that the plants boast the longest aggregate drying and mixing times in the industry, and are capable of processing high percentages of RAP.
Using counter-flow technology, the EX Series has separate drying and mixing zones to achieve the maximum level of heat transfer and fuel efficiency. Furthermore, this system is said to virtually eliminate unsafe hydrocarbon emissions, which are cited by the ADM as a common problem with other drum mix plants. To make the plants even more environmentally friendly, ADM designed the system to re-introduce residual gases back to the drum’s combustion zone.
Also, the plants are available in portable or stationary versions. They meet all federal and state specifications and are said by ADM to consistently produce quality asphalt to help protect operators against out-of-spec damages.
The EX Series can be operated by just one plant operator and one loader operator. Additionally, the plants are described as being built with durability and low maintenance in mind, so on-site staff can handle most breakdown issues.
A wide range of components further customises each plant for particular client needs. Available individual components include cold feed bins, hot oil asphalt cement tanks (both horizontal and vertical), direct-fired horizontal cement tanks, portable and stationary bag houses, mineral filler systems, RAP systems, self-erect and stationary silos, weigh and drag conveyors, weigh batchers and fuel oil tanks.
In addition to the EX Series, ADM also has its MileMaker, RoadBuilder and SPL Series. Each ADM plant can be custom-designed to meet the requirements of individual sites.
Representatives of
counter-flow drum mix plant.
The super portable
The Nellis asphalt plant configuration includes a 77tonne self-erect silo, a Roto-Aire RA218 baghouse, four cold feed bins, a liquid AC tank and a custom-built control house.
“This is a training plant for all of the RED HORSE active duty and reserve units, so we needed a larger control house to accommodate class sizes,” said Sergeant Dennis Hagglund, asphalt plant subject matter expert and equipment operator for the 820th RED HORSE squadron.
An emerging technology not found on the 820th’s old asphalt plant, the new E225P is equipped with a Terex warm mix asphalt system. “We want to make sure we keep up with the latest technology available,” added Hagglund, “and warm mix is the wave of the future.”
Said by TR to be simple to operate, the Terex warm mix asphalt system features single-point mixing of water and asphalt cement inside its patented expansion chamber. The chamber is mounted in line on the plant’s existing liquid AC supply line and allows plant operators to reverse the system to clean oil from the pipe. The expansion process allows the “foamed” binder to more readily coat the aggregate at lower mixing temperatures than when produced as traditional hot mix asphalt. TR has claimed that it is one of the market’s most efficient and cost-effective methods for lowering asphalt production temperatures by up to 32°C.
Minus the liquid AC, the RED HORSE squadron has everything it needs on site to make asphalt mix. Nellis Air Force Base has its own quarry, and the squad’s demolition team designs and conducts the blasts. The unit crushes and sizes the virgin aggregate for making asphalt, and its own engineers develop the mix designs for specific projects. The new Terex plant will make mix for base infrastructure projects in addition to being the training hub for the RED HORSE squadron.
This summer, the plant will make mix for a 3.2km road upgrade project along the perimeter of Nellis Air Force Base. In addition to the unit’s asphalt crew, it has the paving crew and equipment to complete these upgrades on its own.
A second E225P asphalt plant has been shipped to the Air Force base in Guam, a sister unit to the one at Nellis.
At last month’s INTERMAT construction show in Paris, Astec brought along a detailed model of a complete mobile asphalt plant to explain its key features to potential customers.
The plant incorporates double-barrel technology. A continuous process delivers virgin aggregates or 50% recycled material into the inner drum where it is dried. The aggregate then drops out to the outer drum, where bitumen is injected. Advantages include guaranteed mixing times and being able to heat the material within a single system.
The plant’s warm mix system uses foam rather than additives. Astec said that foaming provides an enhanced coating as well as only involving a one-time cost.
Meanwhile, Northern Ireland-based
“We’ve got two really good leads on the provision of our services and equipment,” said ABS technical engineer Martin Gandy.
Gandy has claimed that the Vulcan Burner has “unparalleled” fuel efficiency as well as “ultra-low” emissions and noise levels.
The asphalt servicing and spare parts firm has fitted one of its Vulcan Burners at Cemex Shap, in Cumbria, North West England.
ABS said Cemex has noted that fuel usage has reduced, emissions have lowered and overall plant performance has increased substantially.
“We’ll definitely come back to INTERMAT,” said Jodie Lewis, sales and market development manager for ABS. “It has given us a more visible presence in the European market. The networking has been invaluable.”
The Turkish Company Cesan has said that it will soon launch a new asphalt plant with features, based on customer demand.
Benninghoven launches Master Mix 1000 compact mobile asphalt plant
The new plant is said by the German manufacturer to be designed with smaller asphalt operations in mind. With the entire asphalt plant constructed on one chassis, customers are told that they can expect to be producing asphalt within a day of delivery.
“Flexibility and transportability were the key design criteria,” said company spokesman Bernd
Capable of manufacturing up to 320t/h, the plant does need to be established on concrete ground, and is said to be easily transportable and quick to assemble. It uses parts from leading companies such as
RATech can be combined with a conventional asphalt plant to use recycled asphalt pavement (RAP) in the production of new materials.
Offering a throughput of 160200t/h, the machine can be integrated with an asphalt plant to use different quantities of RAP.
For a base course material, the RATech inclusive plant will supply 100% of the material using RAP mixed in with bitumen and chemicals providing anti-ageing properties.
An amount of fresh asphalt from the asphalt plant is used to produce a binder course, which is then mixed with the product from the RATech. For a wearing course, a larger amount of the fresh asphalt from the integrated plant is used. Furthermore, recycled asphalt concrete is added to the mixture with a weighing unit.
Scraper type conveyors inside the RATech convey the material from the top to the bottom of the plant while, simultaneously, preventing any sticking. Indirect heating to temperatures of 200-400°C ensures that the material is kept at the correct temperature.