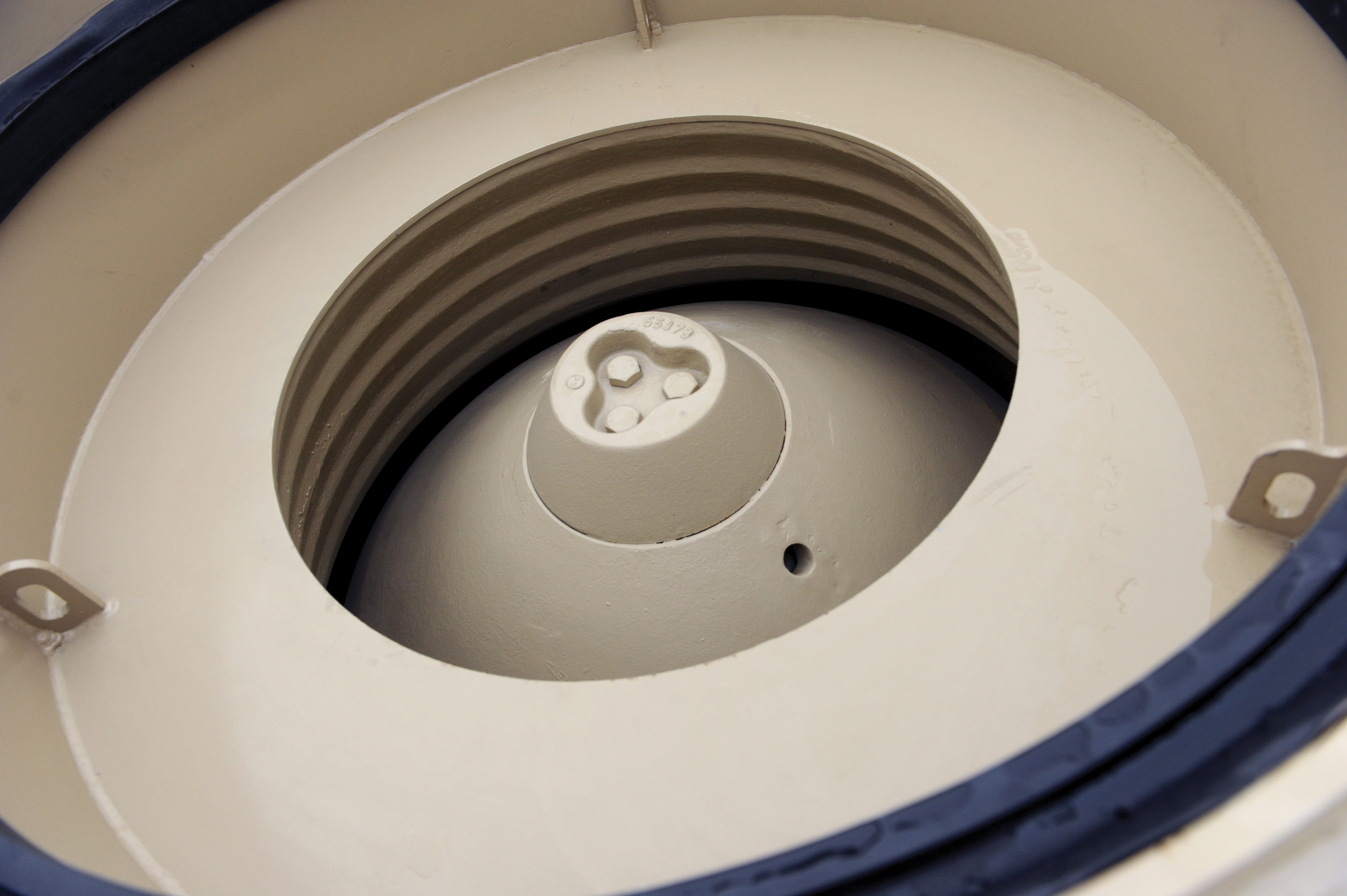
Ensuring efficient cone crusher operation can deliver major economies of scale for quarrying facilities
There are a number of ways in which cone crusher throughput can be optimised.One of the key issues is in keeping the system choke fed during operation, as this maximises the effectiveness of rock-on-rock crushing, extends the wear life of manganese components and ensures a quality product shape. A lack of feed causes inconstant loading, which affects the long-term life of internal components. Too many fines will limit the room for the rock to expand and can result in high crushing forces, causing premature wear and damage components. In addition, if the crusher is not choke fed this increases recirculating load, impacting on screens or other crushers downstream of the circuit, as well as reducing crusher efficiency and overall throughput.
Timely oil changes are vital as the oil provides both lubrication and cooling. Allowing the crusher to run with contaminated oil could decrease bearing and gear life. Oil filters should be checked and changed at the proper intervals.
The source of contaminants should be found and where oil leaks out, contaminants such as dust particles and water can get in. Inspect hydraulic systems and tag leaks for corrective action at the next maintenance cycle. Completely drain and thoroughly clean out the inside of the oil tank to eliminate contaminants before refilling. The type and condition of the lubrication oil is critical to successful operation of a cone crusher as the wrong specification can significantly reduce life. A crusher is designed to work with the lube oil in the range of 10°-51°C. The maximum oil temperature is controlled by a sensor switch at the reservoir return line and if the crusher is used regularly in extremes of heat or cold and it is hard to maintain crusher oil in the correct operating range, it may be necessary to switch to synthetic oil. When changing the outer sleeve bearing, inspect the main frame bore for nicks, burrs, scoring or other damage and attempt to remove imperfections with a file or emery cloth. Use a micrometer to measure the bore at the top, bottom and centre and at each position, check the dimension at two places 90° apart.
The average of all six measurements must fall within an acceptable range. If high spots cannot be filed down to an acceptable range the bore will need to be re-machined into tolerance. Check the bore carefully after re-machining for burrs, particularly at the keyways and grooves. A main frame bore that is worn outside the tolerance limits will need to have the worn spots welded and the complete bore re-machined to tolerance.
If electrical changes are made, or programs are altered in automated systems, verify that alarms and interlocks function properly.
It is cheaper to replace switches or timers that appear damaged or are in poor condition than risk the cost of a major overhaul.
Record vital machine information such as motor amps, oil temperature and oil pressure in a variety of operating conditions, which will identify trends and will also help to detect problems before they cause costly damage or downtime.
High performance cone crushing
The Trac10 system continuously monitors operations with sensors monitoring crusher lube, hydraulic and electrical systems, making adjustments and providing early advanced warning alarms when required. Performance records and trending data provide troubleshooting tools, which can be used for predictive maintenance.
In addition the machine features the firm’s innovative anti-spin system, which is mounted on top of the machine to ease service access. This patent-pending system prevents head-spin and boosts the wear life of the manganese components. Depending on the materials and sizing requirements the crusher can produce from 125-400tonnes/hour even in hard abrasive conditions. The clearing circuit ensures that materials that cannot be crushed, such as waste steel, avoid entering the machine and causing any potential damage. Pressure lubrication ensures reliability while large, patent-pending bearings are said to deliver both a static and dynamic lift. This is said to deliver increased lift to carry the crushing forces. The bearings also feature a washer and ramp design that replaces the conventional use of a socket, socket liner, and head ball. Additionally, the T300 is nitrogen-free and has a patented release system that eliminates the need for maintenance-intensive hydraulic accumulators.
Other important features include the patent-pending concave (bowl liner) retention system with its specially-designed and positioned lip ring that provides retention without the use of hammers and other hand tools.
The design of the T300 is also said to minimise downtime and reduce spare parts inventory costs as it allows the use of a single bowl for all liners over its range of operation, with the added benefits of increasing versatility and efficiency in any aggregate application, according to the firm.