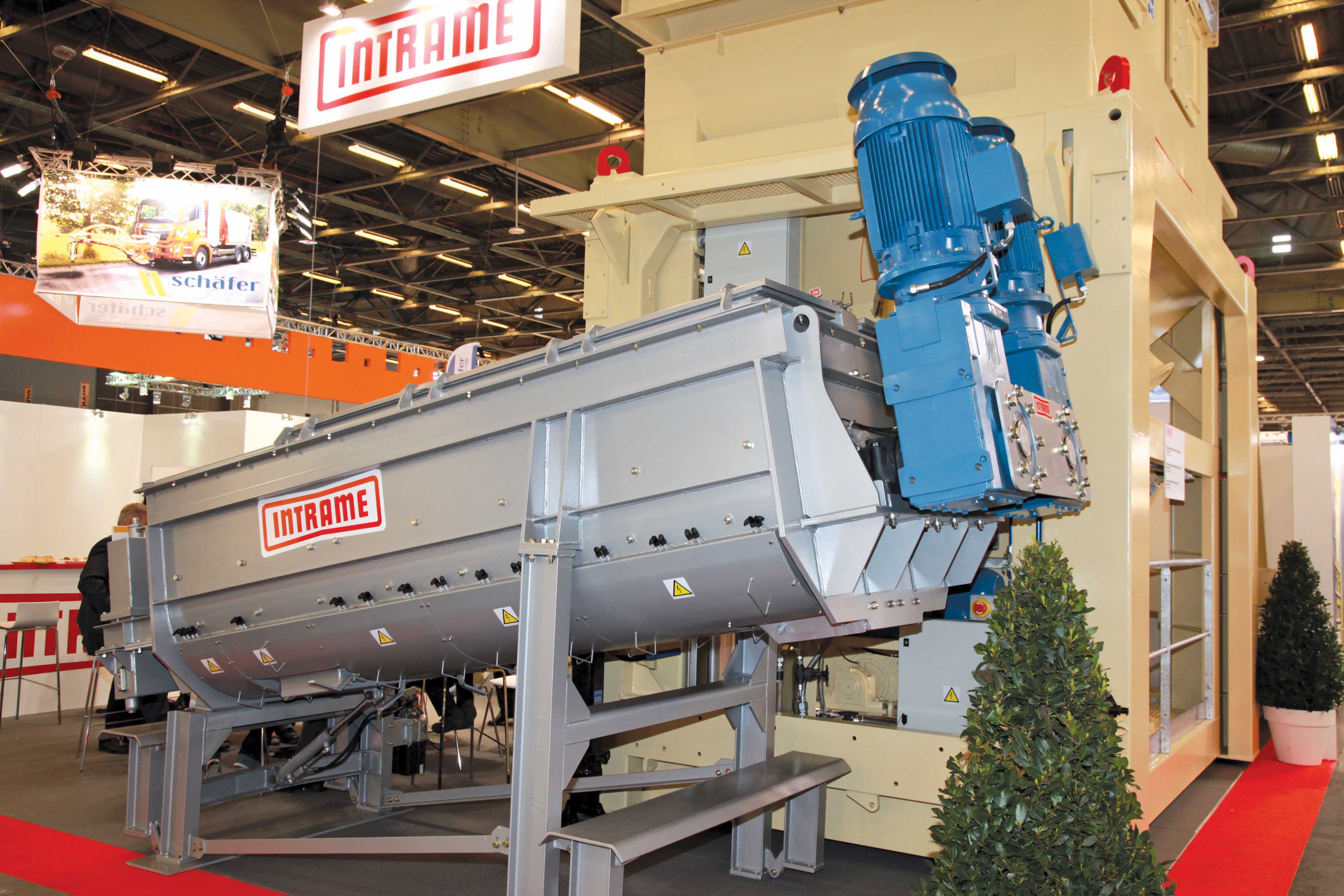
Increasing asphalt plant sophistication will boost the capabilities for the use of recycled materials - Mike Woof writes
Major innovation is being seen in the asphalt plant sector with many of the major manufacturers developing sophisticated new plants. The increased use of recycled materials and reduced fumes emissions are all important issues for the segment. In the US for example, the potential for recycled asphalt has been well identified. It is now one of the most frequently recycled industrial materials.
The plant manufacturers in the US and Europe have been quick to capitalise on this demand although some regulatory bodies have been somewhat slower to respond. In China too there is interest in both recycling asphalt and introducing plants with fewer emissions. The Chinese authorities have already taken steps to boost the use of RAP and with dealing with airborne pollution having been placed high up the political priority list, plants with reduced fume emissions will soon find a ready market in the country.
New developments have been made resulting in asphalt plants that can handle increased quantities of RAP, have lower emissions and can cope with varying specifications, including using PMBs. Manufacturers have also made these plants more versatile, with equipment that is highly mobile and can be commissioned on-site in a very short time.
However other firms have also developed new technologies, including
Asphalt Drum Mixers says that its EX Series asphalt plants feature single-drum, counterflow technology. The firm says that the plants combine high efficiency with a compact design and are aimed at contractors with low - medium production needs.
The EX Series asphalt plants produce 100-425tonnes/hour at a very low cost/tonne. They boast the longest aggregate drying and mixing times in the industry, and are capable of processing high percentages of RAP.
Using counterflow technology, the EX Series has separate drying and mixing zones to achieve the maximum level of heat transfer and fuel efficiency. Furthermore, this system virtually eliminates unsafe hydrocarbon emissions, which are a common problem with other drum mix plants. To make the plants even more environmentally friendly, ADM designed the system to reintroduce residual gases back to the drum’s combustion zone.
These plants are available in portable or stationary versions and are said to meet all US Federal and state specifications. The EX Series can be operated by just one plant operator and one loader operator. A wide range of components is available to customise each plant for particular customer needs. Available individual components include cold feed bins, hot oil asphalt cement tanks (both horizontal and vertical), direct-fired horizontal cement tanks, portable and stationary bag houses, mineral filler systems, RAP systems, self-erect and stationary silos, weigh and drag conveyors, weigh batchers and fuel oil tanks.
The plant also features a dryer, which has been developed so as to allow the use of RAP in the mix. The extended dryer design allows the system to use up to 50% RAP in a mix design, as long as the RAP meets quality targets.
The firm has also introduced a new control cabin for its Flow-Mix 140, with one unit being delivered in France as well. This cabin includes the novel ASFLOW 10 control system, which benefits from Ethernet IP communications.