Hyper-mobility is constantly demanded by customers who favour continuous plants, especially in France. However, compromises must always be sought in the high output equipment range, says Ermont (part of the FAYAT Group), and major progress has been made in the parallel flow field with the 500tonne/hr and 600tonne/hr TSM plants, whereas the Rétroflux type of the counterflow plants have lagged somewhat behind. This gap has now been closed with the development of the hyper-mobile RF 400, capable of producing 4
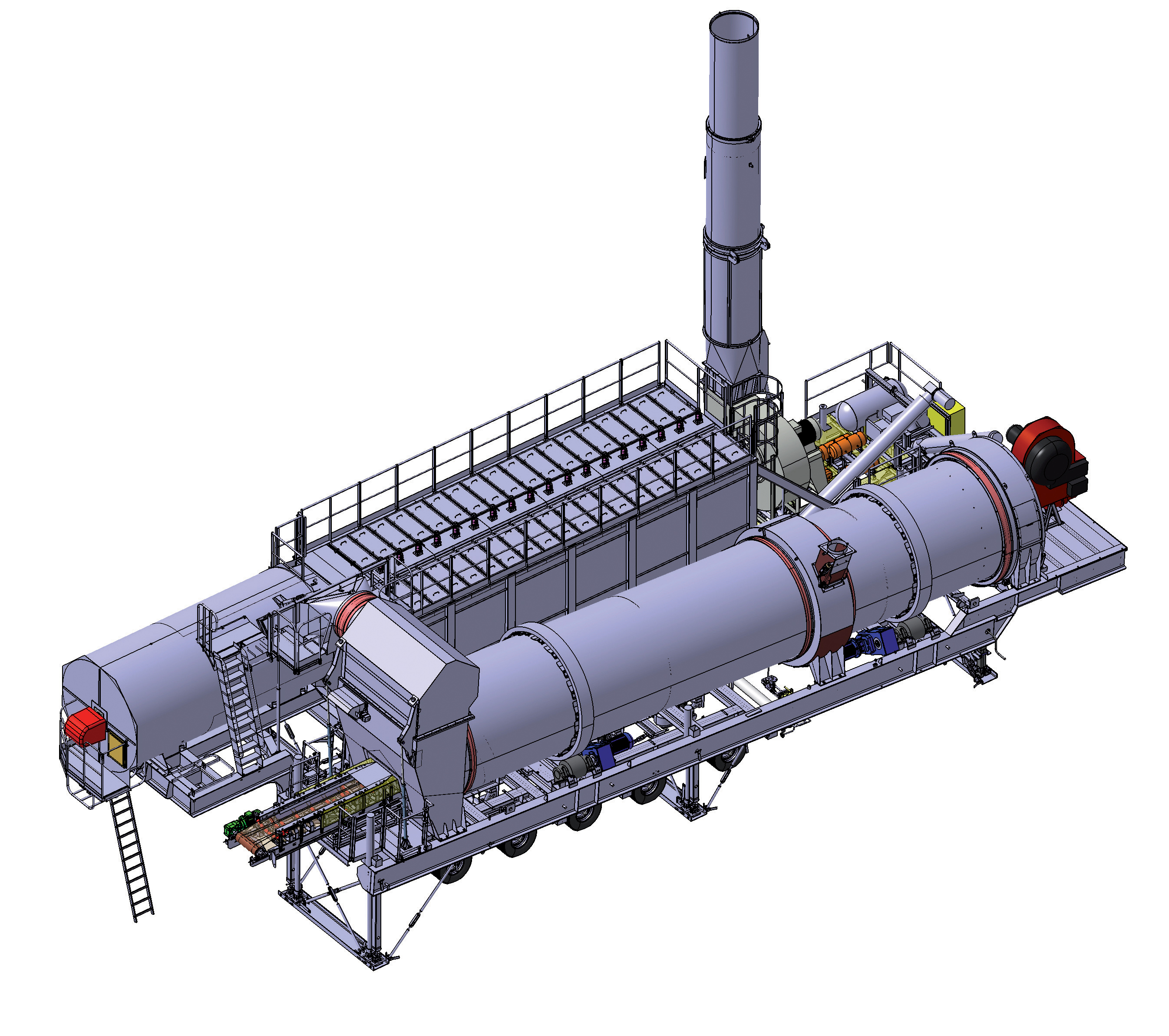
Ermont's hyper-mobile RF400 Rétroflux-type asphalt plant
Hyper-mobility is constantly demanded by customers who favour continuous plants, especially in France.
However, compromises must always be sought in the high output equipment range, says211 Ermont (part of the FAYAT Group), and major progress has been made in the parallel flow field with the 500tonne/hr and 600tonne/hr TSM plants, whereas the Rétroflux type of the counterflow plants have lagged somewhat behind. This gap has now been closed with the development of the hyper-mobile RF 400, capable of producing 400tonne/hr, said to be the first hyper-mobile plant of its type.
The plant incorporates the latest technological advances that allow for the high-rate production of recycled materials, warm and half-warm mix asphalts and the addition of new types of binders.
The plant is exclusively equipped with hydraulic systems (supports, filter stack, connector ducts) for quick and secure installations, and it has integrated walkways with folding handrails, telescopic filter stack, integrated filter connector ducts and foundation battens for each unit.
Integrated electrical wiring can be stored in the control cabin or in a dedicated, vandal-proof enclosure during transport mode, and there are quick interconnections between units.
A specially adapted high-rate 50% recycling solution with radiation shielding vanes made from heat-resisting stainless steel, is accompanied by a volute cold air dilution flap, additional burner on the inlet of the filter for preventing unwanted condensation.
The plant is also specially designed for the production of new materials at low energy consumption with an injector pipe for new binders including foam bitumen, controlled removal of low-temperature gases, anti-condensation system and a Retrobatch-type retention system equipped with an electric heater.
The RF 400 separates into TUV-approved transportable units.
"This versatile plant thus benefits from all of the latest technological and environmental developments that can be incorporated into a third-generation plant. It can also be combined with a TSR high-rate recycling drum for the production of recycled hot mixes at a recycling rate of 70%," says Ermont.
The plant is suitable for big work sites including motorways where a quick installation is demanded. High outputs are necessary for such sites, which require minimum interventions so as not to interrupt circulation. ·
However, compromises must always be sought in the high output equipment range, says
The plant incorporates the latest technological advances that allow for the high-rate production of recycled materials, warm and half-warm mix asphalts and the addition of new types of binders.
The plant is exclusively equipped with hydraulic systems (supports, filter stack, connector ducts) for quick and secure installations, and it has integrated walkways with folding handrails, telescopic filter stack, integrated filter connector ducts and foundation battens for each unit.
Integrated electrical wiring can be stored in the control cabin or in a dedicated, vandal-proof enclosure during transport mode, and there are quick interconnections between units.
A specially adapted high-rate 50% recycling solution with radiation shielding vanes made from heat-resisting stainless steel, is accompanied by a volute cold air dilution flap, additional burner on the inlet of the filter for preventing unwanted condensation.
The plant is also specially designed for the production of new materials at low energy consumption with an injector pipe for new binders including foam bitumen, controlled removal of low-temperature gases, anti-condensation system and a Retrobatch-type retention system equipped with an electric heater.
The RF 400 separates into TUV-approved transportable units.
"This versatile plant thus benefits from all of the latest technological and environmental developments that can be incorporated into a third-generation plant. It can also be combined with a TSR high-rate recycling drum for the production of recycled hot mixes at a recycling rate of 70%," says Ermont.
The plant is suitable for big work sites including motorways where a quick installation is demanded. High outputs are necessary for such sites, which require minimum interventions so as not to interrupt circulation. ·