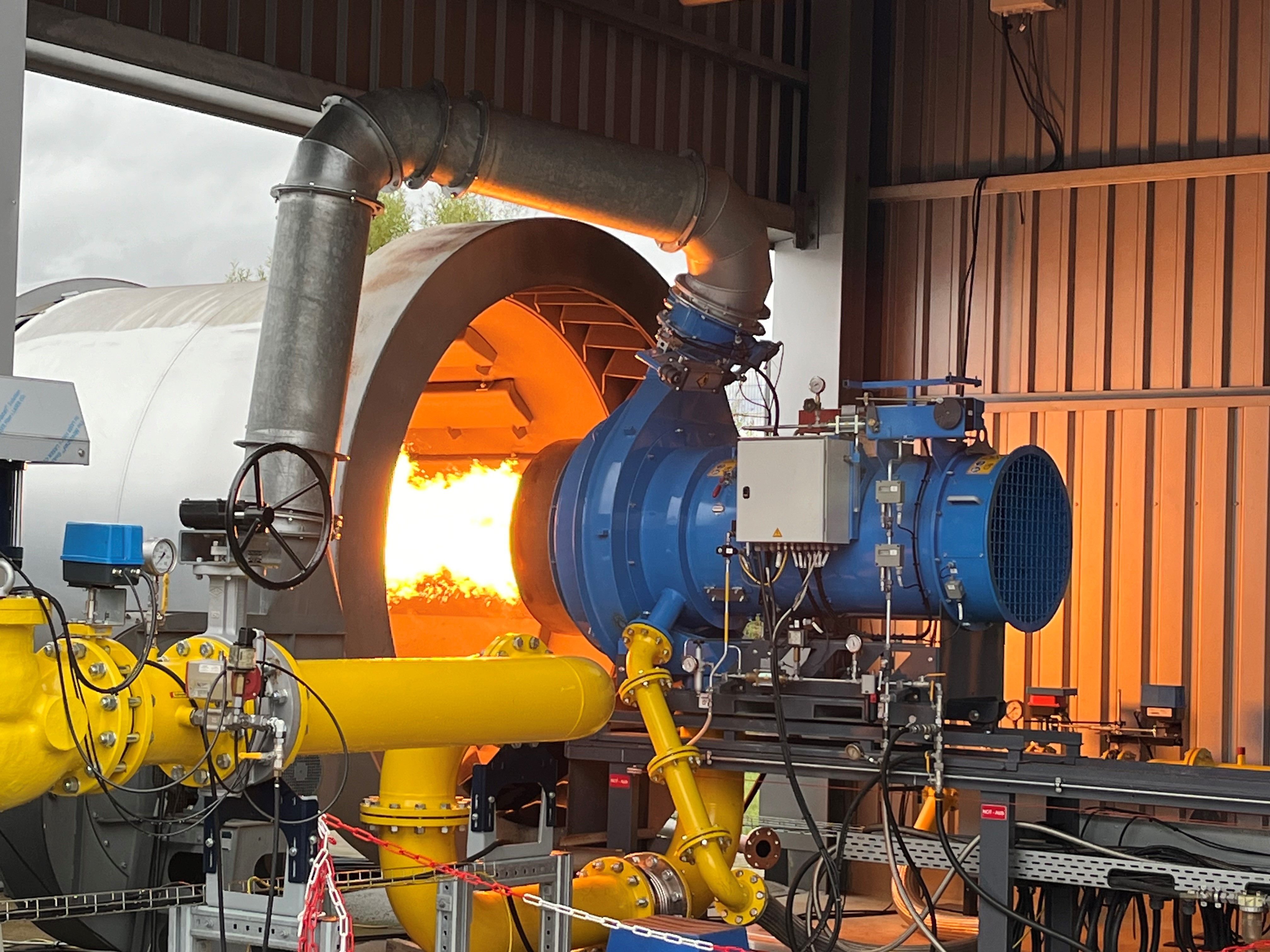
Hydrogen is the most plentiful element in the universe and offers huge potential as a clean fuel as emissions from burning it are of water vapour for the most part. However, producing hydrogen is energy intensive and industrial scale operations will require major investments in sustainable energy to become cost-efficient. All the same, many industries including the construction sector are now looking ahead to a time when hydrogen can play a key role in powering the world, while also helping reduce climate change.
Benninghoven, part of the Wirtgen Group, has used its innovative new hydrogen burner system to produce asphalt for construction work at a facility in Norway. This represents a major step forward for the construction industry in addressing net zero targets and reducing the effects of climate change. Jean-Luc Didier is head of sales at Benninghoven and said, “We really believe hydrogen will be the fuel of the future.”
It is worth noting that Benninghoven’s two biggest rivals in the asphalt plant market in Europe, Ammann and Marini, have parallel development programmes for hydrogen burners. While Benninghoven may have been first to provide asphalt produced by a plant using hydrogen as fuel for a construction project, Ammann and Marini are close with their hydrogen burner solutions for the construction market.
The need to reduce carbon emissions from industry is clear. Didier explained that many customers are waiting to see the outcome of coming regulations with regard to reducing CO2 emissions from asphalt plants. The cost of purchasing a plant is high, so this reluctance to invest now is understandable. However, Didier pointed out that with over 1,800 asphalt plants in Europe, waiting may not be the best option. Benninghoven’s managing director, Heinrich Steins, said that there is overcapacity for asphalt production in the European market and that some of the smaller and older plants will close. But Steins and Didier agree that around 1,400-1,500 will remain by 2030. These will have to be replaced or upgraded with new low emission technologies. And with just three major asphalt plant manufacturers able to supply hydrogen burners in volume (and some smaller manufacturers perhaps developing their own burners), any customers waiting too long to place orders would be taking risks.
Many of the existing asphalt plants that will remain use recent technology and could easily be retrofitted with new burners and other systems to reduce smoke emissions. Didier said, “About half of our turnover today comes from retrofits. We have lots of solutions to upgrade mix plants.”
Addressing CO2 emissions from asphalt plants is crucial. According to Benninghoven’s figures, around 45% of the CO2 emissions for an asphalt road construction project are produced at the asphalt plant, with the burner itself accounting for the lion’s share at 41% of emissions.
Steven McNally is head of research and development at Benninghoven and said, “The biggest potential for saving CO2 as the asphalt plant is the choice of fuel. Hydrogen could be the solution.”
At the moment, plants in Germany for example are able to use fuel oil or lignite dust in burners but that will have to cease by 2028. While the use of natural gas or LPG will be able to continue for a period, this will also be phased out in time.
Benninghoven is well aware that zero carbon emissions will come and also that fuel versatility will be crucial. McNally said, “To be as flexible as we can for the future we have developed our variable burner technology.”
This allows up to four different fuel types to be used at the same time. And a key point is that the fuel mix for the burner can be switched at any time without having to shut down the plant.
McNally commented that while fossil fuels are comparatively cheap at present, this price will rise over time. He said, “Hydrogen is expensive now but the price will decrease in the future.”
Of note too is that in Switzerland, industries are already being taxed for their CO2 emissions at €100/tonne of CO2, charges that will only increase in the future. And similar taxes are likely to be rolled out elsewhere in Europe in coming years, followed by other parts of the world in due course. There will come a point when the cost of hydrogen will fall sufficiently against the CO2 taxes for it to be commercially viable as a fuel.
As Didier pointed out, waiting for the point in time when hydrogen is cheap could be a costly error. With just three manufacturers able to offer hydrogen burners, waiting lists could be very long indeed.
In addition, a further 30% of CO2 emissions for road construction comes from production of the bitumen needed for the asphalt. By using an asphalt featuring up to 60% RAP in the mix, the emissions from bitumen production can be lowered to 15%. Didier commented, “We have lots of solutions for RAP from 25%-100%.” And it is worth noting too that all of Benninghoven’s major competitors in the asphalt plant segment also have numerous solutions for using RAP in the feed.
Utilising warm asphalt instead of hotmix offers further benefits. Didier said, “If you reduce the temperature by 30°C you can save 18kWh of energy/day, about 1,800litres/day of fuel savings.” And he added that saving such a substantial quantity of fuel will also lower CO2 emissions significantly.
Didier continued, “If you stay under 130°C you have low CO2 emissions.” At the same time, the lower temperature will cut emissions from the bitumen by 87.5%, reducing the smell from the plant, an important factor for facilities located close to urban areas. This is an important factor for countries or regions with strict regulations covering emissions from asphalt plants such as Switzerland and Northern Italy. It is worth noting that such strict emissions requirements will become more widespread in Europe and will also be likely in US states such as California, with the rest of the world to follow in due course.
Introducing this low carbon technology requires a change in mindset, not to mention a significant financial investment. But there is no other option and making a move now could save costs significantly in the medium-long term. Most countries have already subscribed to science-based targets on reducing CO2. If governments were to adopt a carrot and stick approach, offering subsidies for construction firms utilising low carbon technologies and taxation for carbon emissions, take-up would be faster.
Right now, green hydrogen from sustainable sources is not available in the large quantities required to meet industry needs. That will change. The infrastructure has to be built. There are commercial producers of hydrogen expanding operations in Europe as well as in North Africa. Morocco is already building large solar arrays and has plans to install electrolysis plants for hydrogen production, with Algeria looking to follow suit for example. This rather begs the question though as to why Saudi Arabia is not using its massive financial strength to make its vast desert expanses bloom, with solar arrays.
Numerous engine makers such as Cummins and Deutz or off-highway machine manufacturers, Hyundai, JCB, Komatsu, Liebherr and Volvo CE to name but a few, are also investigating the potential for hydrogen as a fuel. That so many leading manufacturers have seen the need to dedicate the time and investment required to develop this technology makes it clear just how important it is for the construction industry to deliver low carbon solutions.
Similar moves towards a low carbon future are also being made in parallel in the cement/concrete sector, most notably from Cemex, Heidelberg Cement and LafargeHolcim.
And it is encouraging that major players in the construction industry are investing for the future and helping ensure that human life on this planet will have a future.