Warm mix asphalt can save energy and the environment, cutting emissions of carbon dioxide and other harmful gases, but are environmental arguments enough for clients and contractors? Kristina Smith asks Though popular in the United States, warm mix asphalt is still a technology waiting to happen in the rest of the world. Chemical companies who imagined a meteoric rise in sales are still waiting for the right economic conditions to allow warm mix to start taking serious market share from hot mix. “In Europe
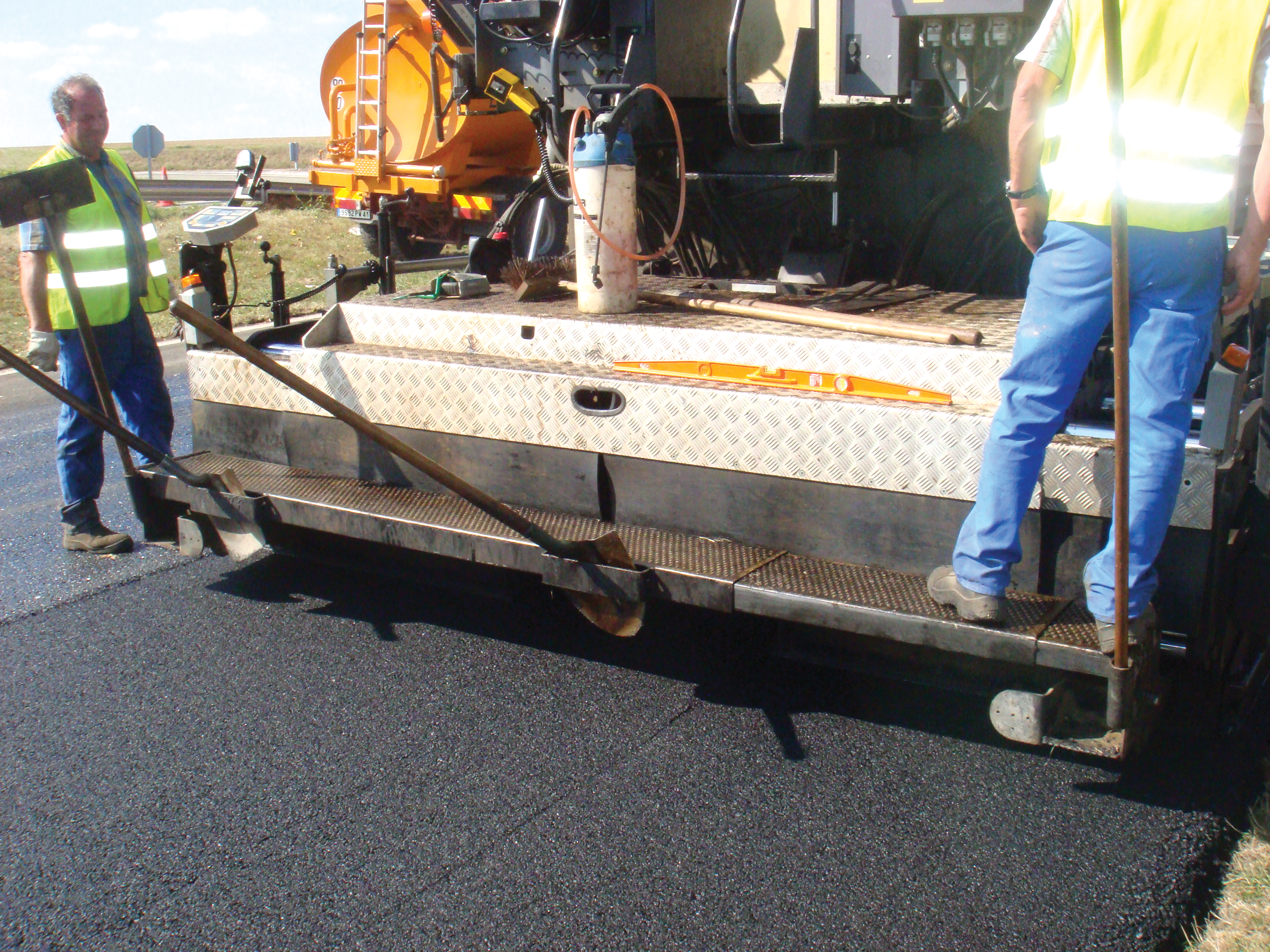
Total put its new ready-to-use binder Azalt EC02 through its paces on France's RD957 near Blois
Warm mix asphalt can save energy and the environment, cutting emissions of carbon dioxide and other harmful gases, but are environmental arguments enough for clients and contractors? Kristina Smith asks
Though popular in the United States, warm mix asphalt is still a technology waiting to happen in the rest of the world. Chemical companies who imagined a meteoric rise in sales are still waiting for the right economic conditions to allow warm mix to start taking serious market share from hot mix.“In Europe we thought that environmental benefits would have been a key factor,” said Claude Giorgi, technical marketing and services manager – Asphalt Innovations, for
However, as fuel costs rise, the energy savings which warm mix can offer become more and more relevant. Many organisations have been carrying out research to quantify warm mix asphalt’s environmental and energy saving credentials, some of which was published at the 2012 Eurasphalt & Eurobitume Congress in Istanbul this summer. World Highways went back to the authors to ask about their findings – and what impact they might have in this tricky economic environment.
It is no coincidence that three out of the four papers originate in France. There, it is the contracting industry which is taking a strong lead in bringing warm mix to the market.
In 2009, members of the French road contractors’ association
“There is a real commitment from the contractors to get the message out to clients that they should use warm mix,” said Sylvie Zucco, product engineer at
Total
“One of our main objectives is to do research in order to develop new binders which decrease the impact on the environment,” said Laurence Lapalu, research engineer in the bitumen department at Total’s Research Centre in Solaize, France.Last year, Total launched a ready-to-use binder for warm mix, called Azalt ECO2. The idea behind the product is that it goes into the mix plant just like a standard binder; no modifications or additions to the plant are required, just lower burner temperatures. And switching between hot mix and warm mix on the same day is a simple operation.
Lapalu’s research paper ‘Warm asphalt mixes made with a ‘ready to use’ bitumen: an experimental field trial’ describes a 2009 trial comparing Azalt ECO2 to a standard hot mix on a 1km stretch of the RD957 near Blois in France. As well as measuring and documenting the performance of the warm mix, it was important for Lapalu and her colleagues from Total and IFFSTAR to record emissions too.
“When you speak with a customer, they have two questions,” said Lapalu. “The first one is ‘Is the performance equivalent?’. And the second one is ‘What is the decrease in consumption and emissions for warm mix? Can you prove that there is a decrease in emissions at the plant?’”
Using IFSTTAR’s measurements, Lapalu was able to prove that there was a decrease in emissions across at the mixing plant and during application, and in parallel with that, a 35% reduction in the energy used at the plant. After two years in use, the mechanical performance of the warm mix section was also comparable to that of the hot mix section.
Zucco said that warm mix is starting to appear on clients’ tenders. And she highlighted the growing use of eco-comparison tool SEVE, developed by USIRF, which allows contractors and clients to calculate and compare factors such as energy use, global warming emissions, aggregate use and content of reclaimed asphalt pavement (RAP) for different mixes.
“We have noticed that environmental criteria are becoming more and more important at tender stage in the selection of a solution,” said Zucco.
Total started production of Azalt ECO2 at one of its five refineries in Donges in Brittany in June 2011. In April this year, it started up production at its Feyzin refinery in the South of France too.
“The French market is not as strong as we expected, but there are positive signs from USIRF for instance, and so, we really believe that the market will grow progressively,” said Zucco. “And we are also starting to receive enquiries from other European countries.”
CECA Arkema
Five years ago, much of Juan Gonzales’ role as a research and development engineer in warm asphalts for“In the beginning, it was difficult to convince people it actually worked,” said Gonzales. “Once we passed that phase, we are in the position where the road industry is ready to do it, but there is no incentive.”
However, contractors and clients are starting to ask about carbon and energy savings, said Gonzales. His paper, ‘Environmental aspects of warm mix asphalts produced with chemical additives’, was produced with Poul Henning Jensen of Pankas in Denmark.
Their work involved making detailed measurements of fuel consumption and emissions on two very different applications on live sites, one in France and the other in Denmark. In each case, warm mix and hot mix versions of the asphalt mix were made at the same plants with the gas consumption directly measured.
In France, the researchers looked at warm mix used for the top layer, 3-4cm thick, of a road, called Beton Bitumineux Très Mince (BBTM). By adding 0.4% of Cecabase RT into the polymer modified bitumen binder, the production temperature was lowered from 170°C for hot mix to 130°C, equating to a 31% fall in temperature.
In Denmark, 0.35% of Cecabase RT was added to the polymer modified bitumen for Stone Mastic Asphalt (SMA), a commonly used product in that country. A reduction of temperature from 172°C for the hot mix version to 135°C for the warm mix resulted in energy savings of 23%.
Gonzales also carried out an indicative life cycle assessment for the additive, to work out whether the environmental benefits of producing warm mix asphalt were wiped out by the environmental damage caused by manufacturing the chemicals. The conclusion was that the warm mix asphalts still reduced carbon emissions overall.
Despite the growing interest in carbon and energy savings, it is the economical argument which is important right now for contractors, said Gonzales. Energy savings depend on fuel costs and the climate in which asphalt mixes are produced.
“In many places we are close to the balance between energy savings and the cost of the additive,” said Gonzales. “If the fuel gets a bit more expensive, we are close.”
LAVOC, EPFL, Switzerland
Warm mix is still in its early stages in Switzerland. However the Swiss government has signalled its support for the technology with a research budget of €1.5 million (US$1.6m) over three years for warm mix (PLANET Project).Along with recycling and low noise pavements, warm mix asphalt is a key focus for the Federal Road Administration, said Dr Nicolas Bueche of research institute Laboratoire des voies de circulation (LAVOC) in the Ecole Polytechnique Fédérale de Lausanne (EPFL). Bueche’s research into warm mix includes a project to work out which parts of the process could have the most impact on energy used, and therefore how to optimise energy savings.
“A life cycle inventory shows that with asphalt mixtures, 30-50% of emissions are linked to production in the plant,” said Bueche. So he created a model, calibrated it using actual measurements and used it to identify the key parameters.
“What is really important is the aggregate and sand you use, whether it is wet or not,” said Bueche. “Using warm mix asphalt but wet sand, is a waste of energy.” Bueche showed that by using sand with 1% water content, you could save 14% of energy compared to a reference of sand with 5% water content.
The findings recorded in, ‘Energy in warm mix asphalts’, co-authored with LAVOC director Prof. Andé-Gilles Dumont have been used to help create a model which assists in choosing the best asphalt mix, taking into consideration many factors including energy consumption, emissions, mechanical performance, production complexity and recycling potential.
Uptake of warm mix asphalt in Switzerland is hampered by the structure of the industry, said Bueche. Road contracts are split into small packages, and there are many small mix plants each supplying many different mixes.
“Many plant owners would like to produce warm mix, but that would involve an initial investment and they do not always have the money,” said Bueche. "It is an investment that comprises a risky part right now"
MeadWestvaco Europe
For MeadWestvaco in Europe the important task at the moment is to promote the technical benefits of warm mix asphalt, said Claude Giorgi, technical marketing and services manager, asphalt innovations. One of the major considerations is the fact that it is workable at lower temperatures compared to warm mix, which means it can be used at lower temperatures, extending the paving season.“Until there are taxes on carbon dioxide, we have to focus on the technical benefits,” said Giorgi, “Things that will enable you to make more money, save money or work in conditions where you were not able to work previously.”
One of MeadWestvaco’s most significant projects, since it started promoting warm mix in Europe in 2006, was the A35 around the city of Strasbourg in France. Here contractor
Using Evotherm DAT technology, which involves injecting an aqueous solution of Evotherm H5 additive into the bitumen line, the mix for the A35 contained 10% RAP. With a mix temperature of 115-120°C, the researchers calculated that fuel savings of 34.5% were achieved with the
Giorgi’s paper, ‘Laboratory and field performances of a warm mix asphalt on highway A35 in France’, was written with colleagues from MeadWestvaco and Eurovia.
For warm mix to take off in Europe, there needs to be a combination of political will and economic benefit. The technology’s success in the US, where ‘warm mix’ often involves much lesser decreases in temperature than in Europe, comes not from environmental benefits but from a system where contractors are paid a bonus for achieving better compaction.
The researchers World Highways spoke to all highlighted the issues of recycled content: warm mix can take a higher content of RAP than hot mix whilst achieving the same performance. MeadWestvaco in the States has demonstrated that a hot mix containing 20% RAP has equivalent properties to an Evotherm mix with 35% RAP.
If RAP is taken into consideration, warm mix can offer savings right away, says Gonzales. Total’s Zucco agreed: “We see that the combination of warm mix and recycling allows you to gain in all areas,” she said. “The future is a combination of these technologies.”