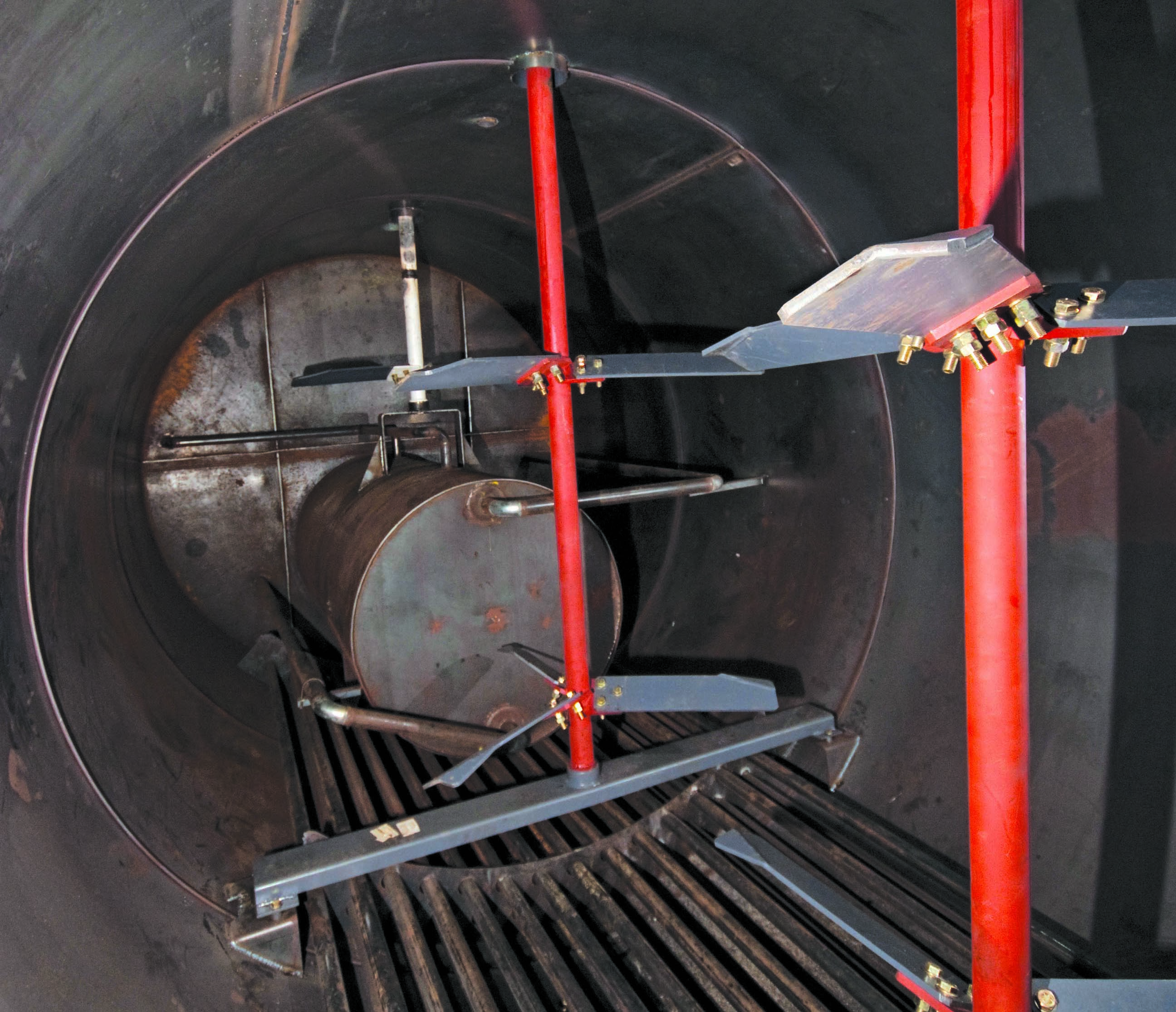
These can be used to boost output and material quality, while also delivering new grades of mixes. At the same time, plant upgrades can reduce the environmental profile of a plant, while improving its safety features for the operator.
Using new technology on an existing plant, Marini says that it is possible to meet demands for higher use of RAP in mixes; plant upgrades can also meet industry needs for low temperature mixes,
foamed bitumen, modified bitumen, additives such as fibres and other new developments.
One of the most significant examples of Marini's successful upgrades is for a MAP 260 plant belonging to the Adige Bitumen Group in Friola, Vicenza. Originally installed in 1997 on the site of Friola di Pozzoleone, this plant has been progressively modified and modernised to face new market needs. In 2004 the screen surface was increased from 783m2 to 1096m2 to upgrade the filtering process, boosting fines recovery and improving temperature control at the filter entrance.
In 2007 the cold feeders were increased from seven to 10, to meet the increasing requirements of the authorities and customers and to allow a greater versatility for the use of new asphalt mixes developed over the years.
The Adige Bitumen Group then found it had to install a special production unit to manage RAP arriving from various road sites. So alongside the Friola production site, a plant at Sarcedo, Vicenza, was set up to treat the RAP and the material is deposited on a special asphalt platform before being treated in the adjacent 2010 plant. This has a waterproof surface, so water is collected and fed into a plant for de-sanding, degreasing and discharge.
The piles of RAP are covered for protection and to limit moisture content, improve the quality of the material and ensure consistent energy savings during the work cycle. The Sarcedo plant not only recovers waste but is designed to operate with aggregates (recycled and non-recycled) and has a quarry licence, which runs until 2023.
To recover and reuse the RAP, a line for cold RAP feed was installed at the beginning of 2016. The RAP is treated and selected, then weighed and fed directly into the mixer. Through contact with the virgin aggregates, which are heated up to a high temperature, the heat exchange is sufficient to dry out the RAP. This equal temperature distribution throughout the various materials guarantees, once the bitumen has been added, the production of high-quality, asphalt mixes.
Additionally, in 2016 the latest version of Cybertronic 500 software was installed for more accurate formula selection. This new software means that the Marini MAP 260 plant is more precise than units built at the same time and can now deliver mixes of the same quality as the latest generation plants. The software also allows the upgraded plant to use the latest additives, with accurate metering through a gravimetric system directly into the bitumen supply. And too boost versatility, two separate metering lines have been installed.
According to Ciber, polymers and crumbed rubber can be used to address the problems with bitumen grades but may themselves cause issues within a plant. Specific knowledge about material grades and the effects of different additives are crucial to ensuring a quality mix is produced that meets the desired specification.
Bitumen is a by-product of petroleum production and gives the asphalt the necessary flexibility as well as its impermeability. But some of the properties, such as its elastic behaviour, viscosity and softening point, may be insufficient to cope with traffic volumes or the local climate. To ensure the asphalt surface meets the requirements of an application, additives may be used while also allowing better permeability for drainage purposes, or improved skid resistance for instance.
Modified asphalt tends to be more viscous, with the additives often being mixed in with the binder by the provider. Using polymers can provide better performance for adherence than crumbed rubber according to Ciber, while this can be determined by a phase separation test. Where the phase separation is over 5%, Ciber says that it is important to agitate the material in the tank at speeds of over 100rpm. For lower phase separation levels however, a pumped recirculation system can be sufficient to ensure that the product remains homogenous.
Marcelo Zubaran, product and application engineer at Ciber Equipamentos Rodoviários commented, "In general terms, crumbed rubber asphalt requires stirrers and the polymer requires recirculation only.” He added that stirrers can be used for all binders however as they boost shearing in the mix inside the tank. In addition, stirrers and recirculators aid in the homogenisation of asphalt temperature inside the tank and speed up the heating of the binder, reducing fuel consumption for heating.
To deliver the optimum mix quality, it is important that the binder is heated with other aggregates according to the viscosity. Variations in asphalt temperature for the mix can damage the adhesiveness of the binder with the aggregates or boost asphalt ageing.
The mix between the modified asphalt and the aggregates should be carried out in a mixer delivering a high shearing rate. The mix time should be adjusted so that the most viscous binder can disperse and cover the aggregates. Certain mixes also require a dry mixing stage.
Meanwhile for plant maintenance, it is important to constantly verify the conditions of the asphalt filter of the tank in application with modified asphalt. Another system that requires monitoring in those applications is the system for asphalt binder spreading. If the asphalt viscosity is too high, it may be recommended to remove the injector nozzles to avoid obstruction in the nozzles.
The asphalt plant should also allow the production of different asphalt mixes and have the capability to be tuned to meet the parameters of the materials and product specification required.