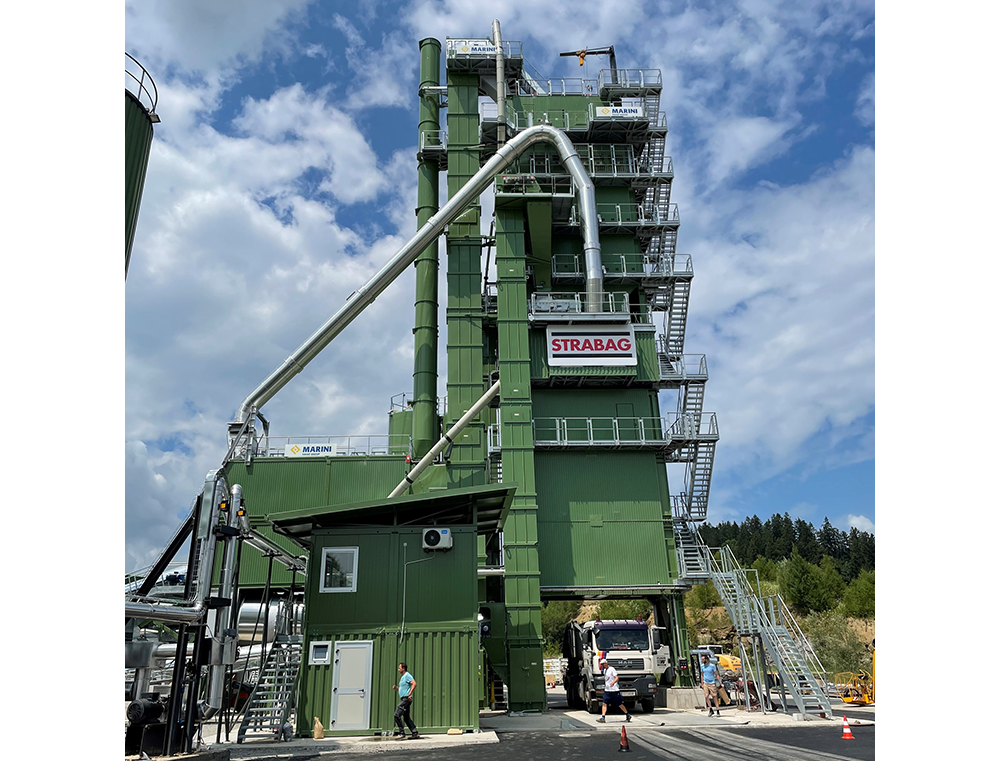
The firm replaced the plant at its site in Haselbach in Austria with a new one better able to optimise the needs of the construction site. The Austrian company wanted a state-of-the-art plant able to produce a large output of high-quality asphalt while complying with the technical specifications of Austrian contracting authorities. The company also needed the plant to be able to use RAP and to change the production of the different recipes quickly, from limestone to basaltic materials.
The Marini Class Tower features a six-selection screen with a 45m2 screening surface and a deviator under the screen to divide the dried and checked materials into two rows of under-screen hoppers. In this way, Strabag can store up to 80tonnes of limestone material and 80tonnes of basalt material in insulated hoppers to minimise heat losses. As a result, the operator can change the production recipe and meet the needs of several paving sites.
A key feature of the plant is the automatic drying process control. The drying/filter processes model retroactively controls the output temperature of the material at the exit of the dryer drum and the temperature of the fumes entering in the bag filter. The software adjusts burner power and drum rotation speed based on the production rate and humidity of the materials in the dryer. In this way, the plant is able to stabilise the temperature of the material leaving the dryer. The function helps to manage the cold RAP in the mixer, because the software helps to stabilise the temperature at the mixer outlet and the temperature of the fumes entering the filter. This improvement prevents excessively high or low temperatures of fumes in the filter, avoiding clogging. It also optimises fuel consumption while making the thermal exchange more efficient, especially with high RAP percentages.
Another software development is the dynamic management of RAP, which was demanding in terms of preliminary studies and onsite calibrations. The software allows the operators of the plants to check the maximum amount of RAP that can be used based on the asphalt they have to produce and to the RAP available onsite, in order to stay within the particle size curve. The formula can also be adapted to suit the operating condition, of key importance for this application where only the cold RAP line is used in the mixer.
In addition, this software changes the quantity of bitumen, filler, and aggregates inside the under-screen hoppers, based on the amount of RAP used, in order to ensure the maximum finished product quality. This allows operators to manage the finished product temperature by changing the RAP percentage based on the aggregate temperature.
The function allows the operator to increase or decrease the quantity of RAP to ensure the correct temperature of the finished product, adjusting in real time all the other components, suiting high or low ambient temperatures. For this jobsite, Strabag has chosen the RAP technology with the RAP line into the mixer. The aim is to prioritise aggregate control to optimise the grading envelope during any operating stage.
The client was keen to optimise maintenance and reduce energy consumption, as well as asking for large aggregate cold feeders with a galvanised steel structure to reduce corrosion from the contact between the wet material and the sheet plates. Most of the hoppers have a bolted anti-wear lining. However, the sand hoppers have a Hypalon inside coating to prevent cold feeder blockages.
The dryer drum has a 16.8MW natural gas-burner fitted with an oversize silencer to reduce its noise. The bag filter has a large filtering surface to reduce wear and dust emissions, as well as an inverter-operated exhauster to minimise the energy consumption and fan noise.
Strabag also asked to add liquid and solid metering systems to the plant. Today, rejuvenators must be supplied accurately to handle high RAP percentages. The same applies to binding agents if aggregates and bitumen are poorly compatible. Even fibre additives (or in bags) must be supplied accurately to produce porous asphalt and Splittmastix. The control cabin with the Cybertronic 500 software help control the functions, ensure metering accuracy, and optimise the burner’s consumption and connection with the Group’s centralised software.