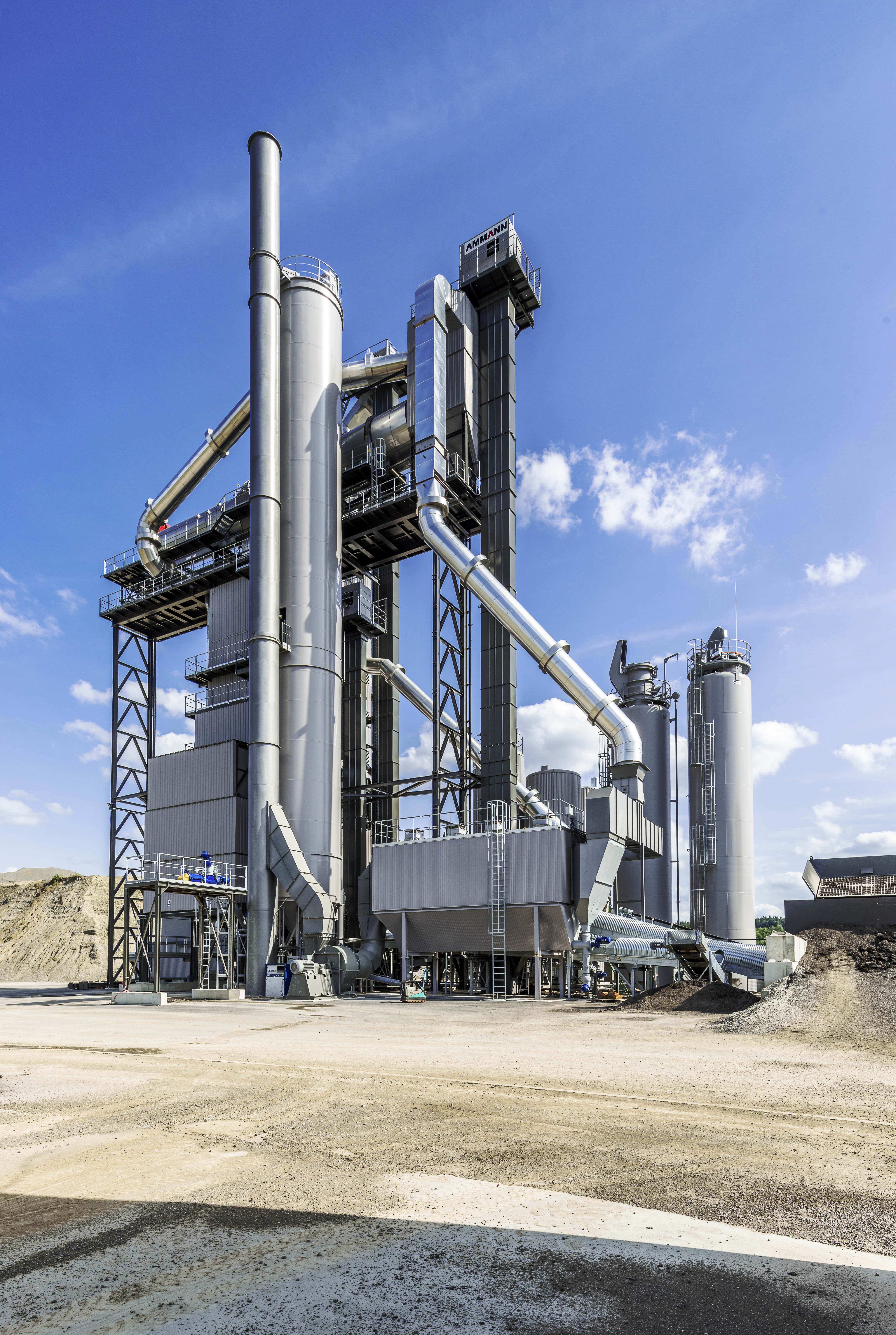
The asphalt plant market has been a focus for a series of technical developments in recent years. Warm asphalt solutions and new technology for the use of recycled asphalt have been high on the R&D priority list for manufacturers of both continuous and batching type plants.
However, new developing technology is not the only driver for commercial advantage in the sector and increasing competition between leading players could be a key point to watch for the coming year. The US has long been a strong market for continuous type plants but Swiss firm
It is not clear if other European major suppliers of batching plants will adopt a similar strategy and try to take advantage of increased interest in batching plants by North American contractors. The
But while Europe is primarily perceived as a market for batching plants, Astec has had a sales presence across Europe for many years and has supplied a number of units. And Fayat’s Ermont facility in France also builds an extensive line of continuous plants.
While North American firms have preferred US plants for many years, Ammann has now supplied its first plant into this market. A Universal ABP HRT (High Recycling Technology) Asphalt-Mixing Plant has been installed in Columbus, Ohio and began producing mix in early December 2017. According to Ammann, the ABP HRT plant is aimed at asphalt manufacturers wanting to incorporate large percentages of RAP into mixes, without sacrificing production capacity and quality. The HRT is a two-in-one plant featuring both warm and cold recycling systems that can be used simultaneously.
Amman offers two warm recycling systems. One is the conventional concurrent flow dryer for RAP additions of up to 60%. The second is Ammann’s latest development in warm recycling, the RAH100, which can use 100% RAP, depending on the quality of the feed material.
US plant firms are not waiting around however and are also making significant technical developments.
Dirty air and dust created by the aggregate drying process are directed from the dryer into the baghouse, which features an oversized precleaner air entry. The bags act as filters, collecting dust as the air moves through the baghouse. This prevents the dust from being expelled into the atmosphere, while the clean, filtered air is forced out by an exhaust fan.
The 397gramme capacity, 204°C-rated Nomex bags are housed in 3mm thick galvanised steel cages to prevent them from collapsing. Internal grids installed above the hopper serve as a bag catcher. Airtight, lift-off doors on the roof allow for easy bag removal. An optional primary knockout box features a baffle plate incorporated into the housing, decreasing air velocities and preventing premature bag wear.
In addition, maintenance personnel are said to be able to quickly and easily access the screw conveyors to clean out the excess dust by removing the airtight hopper access plates.
Safety features include a caged roof-access ladder, top perimeter tubular guardrail and solid-steel toe-stop kickplate. The relocatable baghouses feature a heavy-duty I-beam structural frame with high-temperature fibreglass blanket insulation and a thin aluminum insulation jacket.
Astec Industries is working on various new developments, including its novel Silobot inspection system for asphalt plant silos as well as batching plants. The second generation Silobot prototype is undergoing field testing at the moment and includes a number of upgrades over the original design. The units will be offered as a service through Astec’s parts department but the development work is not yet at that stage where the company can say it will be commercially available to all of its customers.
The firm has developed its latest generation foamed bitumen system. Mike Varner, chief engineer at Astec Inc said, “We listened to the customers. They said if the water pressure is increased, they see a greater effect of bitumen foaming.”
He continued, “We used all the components from the original system so we have frontwards compatibility. We did redesign it to reduce the footprint and we increased the water pressure by a factor of 10 but we used the same pumps. We wanted to do so to control the pressure in a specific range. Having fewer nozzles allows the increase in pressure.”
Varner said that not only is the new system more compact, it is also around 75% lighter, making it easier to transport from one facility to another.
Meanwhile Benninghoven claims that its innovative asphalt transfer system boosts the capabilities of the firm’s ECO mixing plant range. The newly developed alternating chute unit is fitted to the firm’s ECO asphalt plant and is said to be a key development for the sector, with a patent pending.
The ECO asphalt plant is offered with output ranging from 100-320tonnes/hour and is said to combine the latest Benninghoven technology and quality. Designed for mobility, the plants fit inside standard shipping containers sizes, maximising mobility and versatility. The firm says that the ECO units can be operated as stationary plants, but can also handle fast location changes without problems.
Because all main components are designed in standard container dimensions, they can be easily transported by road, sea or rail. The plants are also said to be cost-efficient and effective, while offering optimum mix quality.
Weighing and mixing is said to be efficient and a key development is its new alternating chute container. The firm relies on loading skip technology as a link between mixer and loading silo, with the skip volume corresponding to the volume of the mixer. The mixer drains the asphalt vertically downwards into the skip, which then positions itself vertically above the targeted loading silo pocket and drains the stored mixed goods vertically downwards. This is a proven technology for excluding segregations in the mixed goods.
But for the new ECO asphalt mixing plant range, Benninghoven has developed a new cost-efficient alternative to the skip track. The alternating chute unit features a purely mechanical structure which is not subject to malfunctions. The design means that no sensor system, motors or brakes are required, while reliability is ensured. The system is said to offer fast and load-free positioning for silo selection. Separation effects in the end product are minimised through cross mixing in the material transfer, while the proven geometry of the Benninghoven loading mixed materials storage silos ensures mass flow instead of core flow, further preventing segregation in the mix.
The firm claims efficient mixing due to the design of the mixer with its optimum fill level and large dimensions. The larger plants in the ECO range include cold and hot recycling feed, bag feed, foam bitumen, granulate feed, fibrous material feed and adhesive feed. Other important features include a key transfer system for increased safety, a large service opening on the mixer cabinet, purge air cleaning on the infrared temperature sensor and oil lubrication and filtering for the compressor. The system also offers the choice of plug-in cables and permanent cable connections, while the plant features the latest version of the firm’s sophisticated BLS 3000 control package.
From Marini-Ermont comes the innovative TRX100 asphalt plant, which utilises a patented low temperature technology that allows it to use feed material containing up to 100% recycled asphalt pavement (RAP). The plant has been developed in partnership with Eurovia’s Technical and Research Division in a bid to increase the use of RAP for road building.
The patented TRX 100% technology, based on the drying of asphalt aggregates at low temperature, is said to reuse and preserve the binder in the asphalt. This is achieved through longer mix times, together with an innovative heating system. According to the firm, the TRX 100 is the most efficient mobile recycling solution on the market.
The plant forms part of Eurovia’s project to construct roads made entirely from recycled materials. The aim is to significantly reduce the use of raw materials and greenhouse gas and polluting emissions while delivering mechanical performance identical to that of new materials, sustainably and at competitive prices. The project is supported by the French Environment and Energy Management Agency (ADEME). The project started in April 2017 and the programme covers study, design and prototyping phases and a demonstration plant, real on-site testing as well as a validation phase. Studies and tests on materials produced will be run in parallel to check their performance.
The demonstration will be on a road stretch with high traffic loads and will deliver road foundations with a recycling rate close to 100%.
Once the economic model of the “100% recycled” solution has been validated, the plant is expected to be duplicated in France and abroad on major road maintenance sites, which are its primary targets. This infrastructure offers high volumes of material with features suitable for complete reuse in major maintenance operations.